泡沫铝三明治夹层复合材料的性能特点
相较于普通钢制或铝制控制臂,这种三明治复合材料具有更好的抗冲击和抗弯曲性能。泡沫铝的芯层使得其更适用于承受弯曲应力的部件,金属外壳提供了较好的抗冲击性。这种三明治复合材料让承受复杂载荷部件实现轻量化设计成为可能。
作为德国政府“多功能轻量化结构的技术融合”项目MERGE卓越集群(Federal Cluster of Excellence MERGE)中的A、B、C子项目,研究者们通过夹层的结构设计,成功开发了泡沫金属基的轻量化夹层材料。该部件的成功开发依赖于多种材料技术的融合。由于涉及包括金属、塑料、发泡材料在内的多种材料,材料性能的差异使得其间的连接较难实现。因此,各种材料的复合顺序以及各半成品间的连接技术成为该研究中的重大难点。
在MERGE卓越集群项目中,这种复合材料分别被用于制作车轮盘、车顶横梁以及控制臂(如下图1)。与普通的纤维增强复合材料相比,泡沫铝芯层的加入使得新材料具有更高的容损性和抗失效性能。特别是对于控制臂这样的承载部件,不会发生突然失效,且其损伤在表面可以轻易发现,便于及时更换。工艺方面,由于控制臂呈双弯曲的几何形状,因此,其在制造时不能像轮盘一样直接采用泡沫铝作为基材,而是需要嵌入金属嵌件,从而实现零件的功能。
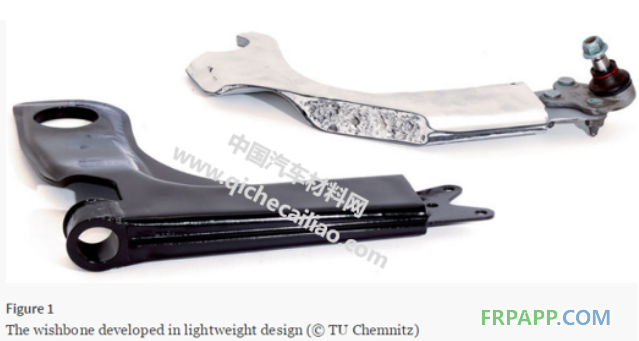
多材料复合层板的制造过程
研究者们先尝试采用多种纤维增强复合材料和薄铝板制作了一种独特的混合层压材料,如图2所示。纤维增强复合材料基体保证了足够的强度和刚性,减轻了部件重量,并提升了耐疲劳性能。而铝合金外壳则提供了优异的抗冲击性和延展性。
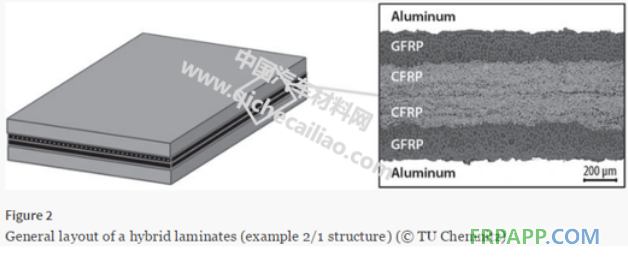
铝合金外壳可以保护纤维增强复合材料不吸收水分,隔离外界环境影响,提升耐腐蚀性。金属表层可实现切割、钻孔等机械加工。同时,金属表面也可以进行更好的涂装修饰。在纤维增强复合材料中,不仅有碳纤维增复合材料,还加入了玻纤增强复合材料层。一方面是为了避免碳纤维与铝合金直接接触发生电腐蚀,另一方面可减少由于不同杨氏模量和热膨胀系数的材料复合所产生的残余热应力。
研究人员先将铝合金覆盖层通过施压进行预成型,然后通过机械喷砂和火焰处理,增加其表面粗糙度,用以提升其与塑料复合材料的结合强度。随后将干燥后的纤维基半成品与铝合金壳体一起放入模具中加热、加压、成型。加热使得纤维基复合材料表面熔融,加压,与铝合金壳体充分结合,再冷却定型。
泡沫铝芯层材料
由于具有泡孔结构,金属泡沫材料具有低密度、高强度、良好的吸能性以及良好的阻尼性能,是较为理想的轻量化材料。泡沫铝的工艺难点在于发泡过程的控制,特别是用作结构复杂的部件时,既需要成型复杂结构,还需要保证足够的强度。与发泡塑料相比,泡沫铝具有高刚性、高强度以及高稳定性,更适合作为高承载结构件的芯材。
泡沫铝具有网状的泡沫结构,适用于覆盖层的压缩成型。表面的闭合泡孔结构适用于覆盖层的压缩成型。通过材料体积和泡沫设计密度计算出基体材料的质量,然后放入模具成型。
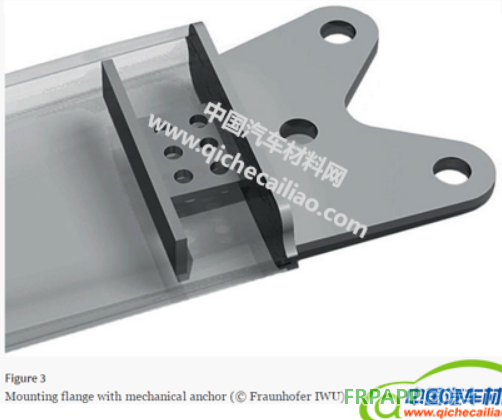
同时,由于铝具有较高的热膨胀系数,在设计时需要通过缩放泡沫模具以避免泡沫材料冷却期间铝壳体的收缩。
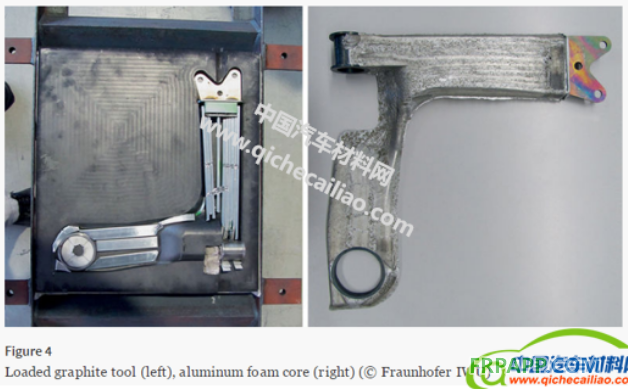
在脱模过程中需要考虑模具对泡沫组织的破坏,且需要防止手工操作过程中泡沫结构的塌陷。因此,需要尽可能地缩短脱模时间。总体而言,发泡过程需要确认温度、预热和起泡时间、冷却脱模时间等参数。
三明治结构复合材料的设计
多材料混合的夹层结构复合材料可承受较高的压缩、剪切和扭转载荷,因此夹层结构的复合材料特别适合用作承受弯曲载荷的部件。控制臂的复合材料截面结构如下图所示。
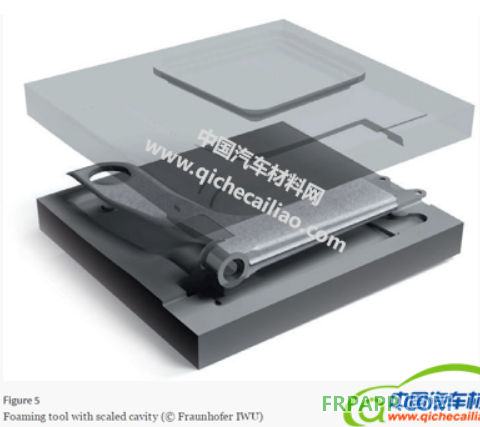
芯层采用泡沫铝,中间采用PA6/玻纤增强PA/碳纤增强PA组成的多层复合材料,外层采用金属铝。由于泡沫铝具有较高的热稳定性,且表面具有粗糙的闭合泡孔结构,因此其可以与热塑性PA直接复合。再通过加热,使得外层的PA融化,在压力作用下与铝外壳连接。
总结
控制臂的成功设计是多材料技术融合实现轻量化的典型案例。通过泡沫铝与多材料复合层板的结合,解决了结构复杂的、变厚度部件的轻量化设计。这一研究成果又丰富了底盘控制臂轻量化方案。