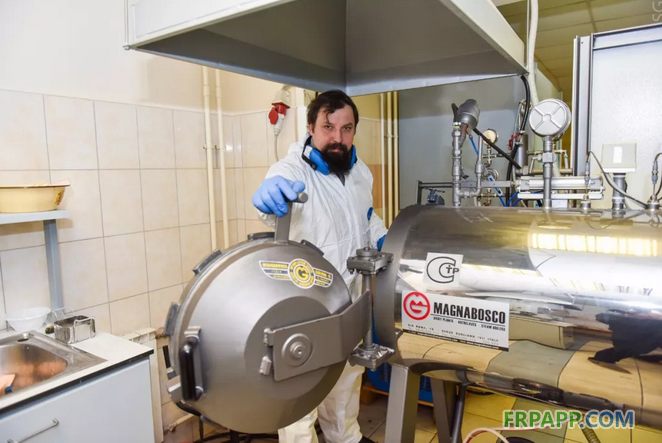
“这支由Sergey Kaloshkin教授领衔的科学家团队,通过测量内部压力值,对航空部件、油气管道、船舶壳体及其他工业/交通行业的复合材料部件进行内部损伤评估。”Nust MISIS院长Alevtina Chernikova表示说。
事实上,在制造过程完毕之后,不管是碳纤维复合材料、玻璃纤维复合材料还是其他混合纤维复合材料,其内部都不会产生这种水平的压力。然而,一旦在部件服役过程中,因为外部环境、天气等因素的影响承受了载荷,其内部必然会产生和积累一定的压力,导致材料本身的损伤,降低部件的承压能力。这些变化会损害运营的安全,必须及时发现并得到有效遏制。
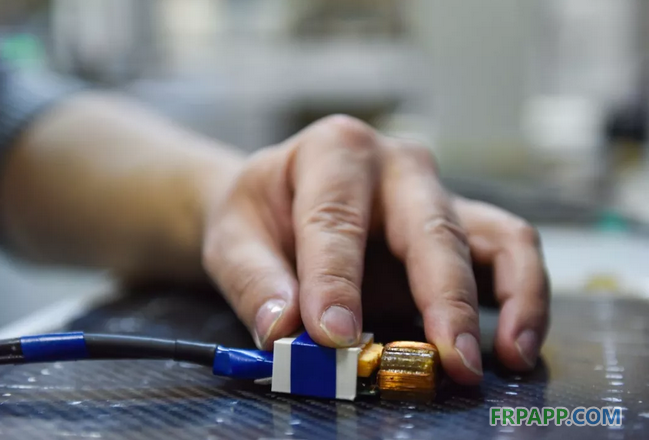
检测复合材料结构内部压力的方法有很多种,但有的操作不便、有的无法保证准确性。例如,传统的非接触检测法(包括超声检测法、声波探伤检测法、错位散斑干涉法)能够帮助我们检测到已经产生的损伤,但并不能对材料承受的压力和压力在结构中的分布状况提供有效的情报信息。而想要掌握压力分布和数值状况,只能使用贴纸、薄膜等类型的传感装置进行接触式的检测。总而言之,在损伤产生之前对压力进行非接触式的检测,在目前看来基本是不可能的事情。
新方法的关键在于,利用无定型软磁电路评估复合材料内部的压力状态。在生产过程中,微电线被放置于碳纤维片层之间,形成一道压敏网格。
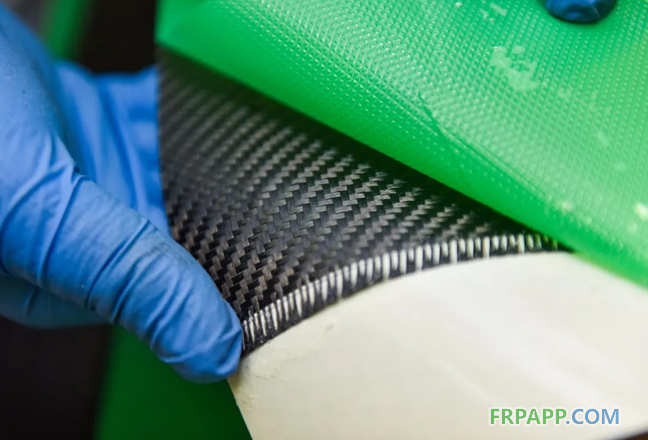
微电线周围的压力状况会影响复合材料内部对外部磁场的感应。这些检测数据可以通过无接触的方式,传输到同样在生产过程中埋入材料内部的传感装置。更令人称道的是,新方法只需要使用一枚传感器,就能实现其他类似方法使用多个传感器的效果。简而言之,这种新方法操作起来非常简便,快捷,同时使得修复过程更为简单、预测结果更加准确,大大降低了检测成本,而且全过程无接触。
目前,科学家们已经找到了在不损害复合材料内部性能的前提下,埋入软磁电线的方法。同时,他们还设计并掌握了多种不同的测量模式。
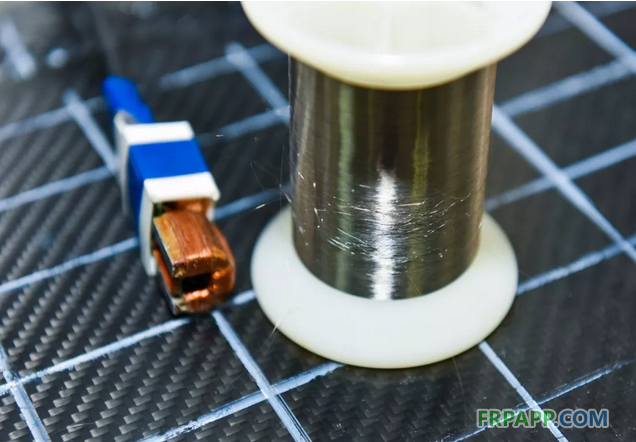
多位来自航天航空业的代表、以及复合材料行业的研发工作者对这种新方法给予了高度评价。目前,研究人员只需要走出实验室,找到一处真实场景,进行实测。
“虽然这只是万里长征的第一步,但是我们已经可以预见到它真实存在的市场前景。另外,我们埋入材料内部的微电网还能排除玻璃纤维内部产生的静电。这种微电网完全可以取代目前使用的金属网。”