为满足日益严格的排放法规及客户对延长电动车续航里程的要求,全球汽车行业正在加紧推进实现减重目标。
通过选出一种量产的钢悬架部件来对其进行重新设计,以将其作为一种可制造的复合材料轻量化部件,福特汽车公司启动了开发周期。
所选出的部件呈现出了“最小刚度与最大刚度”、“屈曲指标与强度指标”等彼此矛盾的要求。
对这一特殊的非弹簧支撑部件的减重,可提升弹簧和阻尼器的相对有效性,从而改善乘员的舒适性和驾驶员的操作性。
这一新开发的复合材料部件已证明适用于高性能的C级汽车。
这一成功的故事,是由Innovate UK部分资助的一个为期两年的项目以及由包括福特汽车公司、Gestamp、WMG、华威大学和GRM Consulting公司在内的一群组织实施的结果。
该项目的名称为“复合材料轻量化汽车悬架系统(简称‘CLASS’)”。
复合材料技术已不可阻挡地从学术研究和航空工业进入到了主流汽车工程实践之中,以抵消电动汽车和自动驾驶汽车固有重量的增加。
对于主流汽车行业整体而言,复合材料性能的复杂性仍然是有待克服的挑战性问题。
虽然大量的研究一直致力于从工业和学术两个层面上去理解复合材料,但对复合材料的性能进行预测的艺术尚处于初级阶段。
在为赛车的碳纤维结构开发预测工具方面,GRM Consulting公司拥有几十年的经验积累。通过避开传统的方法,以及减少所需的力学测试的数量,该公司对此项目作出了重大贡献。
利用VR&D Genesis有限元分析和设计优化软件,GRM Consulting公司采取了一种基于优化的方法来降低成本,缩短工程时间,同时又不影响性能。
对于满足强度、刚度和屈曲载荷要求的无穷多种纤维取向的组合,需要了解机构的失效点。为此,WMG、华威大学运用他们对材料行为的广泛理解以及最先进的制造单元,令汽车底盘制造的全球领先者Gestamp公司在设计部件以满足必要的功能性要求方面发挥了重要作用。
在该项目两年的开发过程中,这种复合材料部件的设计,从单一材料部件发展到了多种材料的设计,从而给制造和优化团队带来了挑战。
从书中了解的初步信息表明,复合材料轻量化转向节的构思,可由单一一种材料即片状模塑料(SMC)实现。
然而,长期的工程时间表最终导致设计工程团队转向采用多种材料系统:预浸料层赋予了其所在之处所需的平面力学性能,SMC 的包覆成型则允许实现复杂的几何细节和面外刚度。
这种单轴和双轴预浸料结合SMC的方法,意味着这种复合材料部件能够达到力学强度、刚度和屈曲目标。
其他的设计挑战表明,在不影响制造而保持此设计概要的同时,必须引入更多的创新。
在做了广泛的仿真和试验工作后,设计即被完成。这使设计得到了优化和细化,满足了OEM的耐久性和NVH目标。
该项目最终实现的减重效果是,在具有同等功能的情况下,最低减重达30%,最高减重达50%。
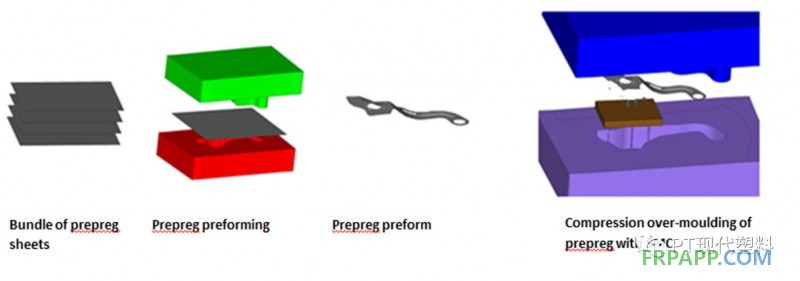