底盘部件是复合材料应用的绝佳机会,因为其占据了车体重量的最大百分比,是承受动态载荷的结构部件。
Kordsa和Ford Otosan的目标是通过生产复合材料板簧来减少重量(与钢相比减轻重量75%),减少CO2排放并提高燃油效率和有效载荷。这还将减轻车辆的簧下重量,以减轻其他系统中的后续重量,并通过降低噪音、振动和声振粗糙度(NVH)来提高舒适性。
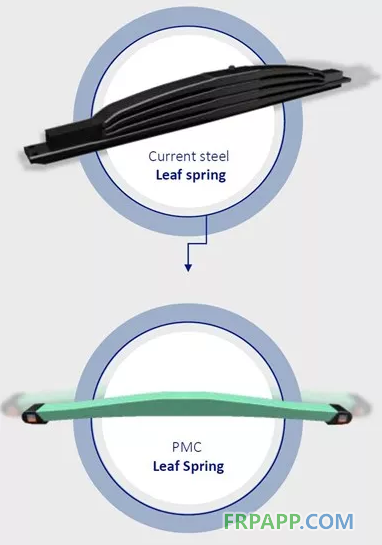
实现重型卡车板簧的性能目标极具挑战性。它必须承受13.4吨的轴重,并承受恶劣的服役环境,且具有至少100万公里的长期疲劳寿命。因此,这种厚的复合材料部件(最大110毫米)必须具有足够高的纤维体积和低空隙率,以及120-150°C之间的玻璃化转变温度(Tg)。生产率必须与重型卡车的生产率相符(每年最多10,000个零件),以使固化周期少于1小时,成本必须具有竞争力。
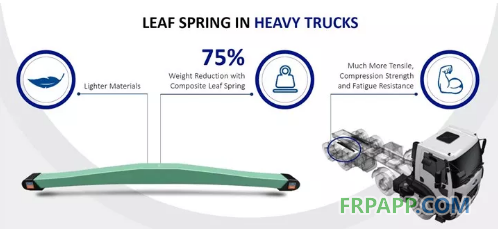
Kordsa和Ford Otosan之所以选择预浸料压模成型,是因为它能够通过改善纤维排列,减少变形和厚度变化来获得均匀的树脂分布和优化的刚度,并且该过程具有很高的可靠性和可重复性。Kordsa生产了各种单向碳纤维和玻璃纤维/环氧预浸料,并对每种材料进行了完整的材料表征,开发了福特Otsan所需的材料数据,以输入到计算机辅助工程(CAE)工具中。然后,它努力为原型重型卡复合材料板簧充分细化负载情况,并使用光纤布拉格光栅(FBG)传感器来验证载荷,探索工艺参数及疲劳特性。
最终的原型产品比钢材减轻了75%的重量,同时提高了拉伸强度、压缩强度和抗疲劳性。Kordsa将继续与福特Otosan和其他运输制造商一起努力,通过重量更轻的复合材料结构来减轻汽车、卡车、飞机和轮船的重量,从而在全球范围内减少CO2排放。