虽然电池周围的结构已经很强大,能为正常碰撞提供足够的保护,但在严重的撞车事故中,保护结构本身会发生变形并可能刺穿电池,使电池无法工作。
这种情况下,需要对电池进行额外的保护。
理想的做法是,以不牺牲设计或其他安全功能、不增加更多的重量或成本以及在汽车使用寿命期间不妨碍电池的维修或更换为前提。
为此,一个名为“电池碰撞保护”的新部件被开发出来,它可以在严重的碰撞事故中保护较大的12V电池——这是复合材料的一个正在成长的应用领域。
严格的测试变得更加严格
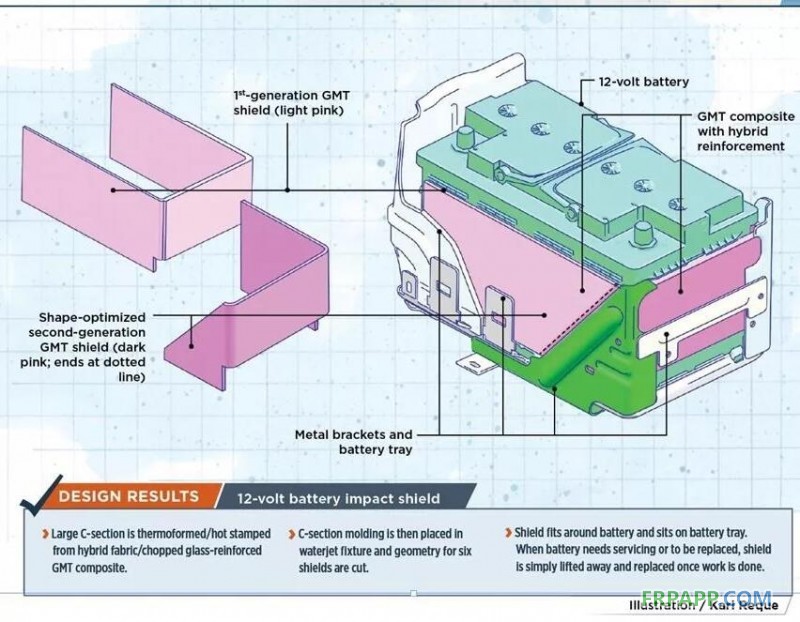
12V电池防碰撞保护的设计方案
本已非常严格的美国联邦机动车辆安全标准(简称“FMVSS”)208,现在要求汽车制造商在正面障碍物测试期间,在30°偏移位置进行测试。
该测试用的冲击器被设计成完全错过框架轨道,这样,就能在被推入发动机舱之前,使保险杠的一角受到重击。
此测试模拟的严重碰撞载荷,已促使通用汽车公司增强了电池盒,并开发了电池防碰撞护罩,它可将碰撞载荷分布在更大的面积上,以在汽车前端遭受撞击时,防止电池长时间被周围的部件刺穿而发生短路。
这为在电池停止工作之前,由车载诊断来检测碰撞并向第一响应者发出“离机”安全呼叫提供了足够的时间——当乘客失去知觉或被束缚而无法拨打电话时,这一功能可以拯救生命。
这些防护罩被设计安装在金属的电池盒上,以将最靠近发动机舱部件的电池部分包起来。
碰撞模拟表明,这些发动机舱部件最有可能在严重的碰撞中损坏电池。
使用中,控制模块和与蓄电池连接的其他部件悬挂在护罩上并固定到位,这样就不会出现NVH问题。
在维护或更换电池期间,只需简单地将护罩移开即可,之后再放回去。
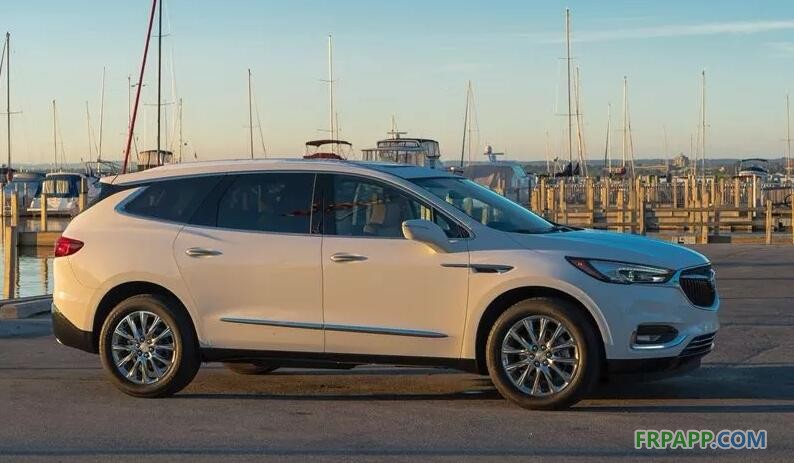
通用汽车公司正在开发新的、更强的电池盒和电池防碰撞护罩,以将碰撞载荷分布到更大的面积上(图片来自通用汽车公司)
研究2018 款Buick Enclave运动型多用途汽车(SUV)的团队在开发后期发现, 为保护汽车的12V电池而设计的钢护罩不能通过规定的碰撞测试。
在经过屏障和落料仓测试后进行的广泛的计算机辅助工程分析(CAE),促使工程师们为部件制定了具有挑战性的性能要求。
为防止成本高昂的生产启动被延迟,他们请来了通用汽车公司的先进材料与开发团队,以便快速找到一种替代技术。
碰撞测试过程
那是12月初,在假期前又安排了一次汽车碰撞测试,这对于SUV的认证非常必要,该车将在3个月之内被推出。
在对汽车作最后的碰撞测试之前,必须对新的防护罩设计、材料和模具等进行创建和验证。
通用汽车公司的工程师们审查了早期的碰撞试验结果,并计算了金属设计所经受的荷载和冲击力。
他们针对额外的负载情况,还评估了几个额外的CAE模型,输入后用于6Ʃ Pugh矩阵分析,以为材料评估制定关键指标。
新的候选方案需要符合或超越所有的联邦安全法规要求,包括阻燃要求(FMVSS 302),同时还要达到通用汽车公司的总体系统成本目标。
考虑到时间紧迫,研究人员筛选出了6种采用短玻纤增强的商用结构SMC级别,纤维在乙烯基酯树脂/不饱和聚酯树脂基体中的重量百分比是42%~49%,比重为1.5~1.9。
购买材料后,成型出一些牌匾,将其切割成标准的试样,然后测试材料。
考虑到30°偏离屏障测试的严重性,在仪表(Dynatup)冲击试验中表现出高冲击强度和抗穿刺性的材料被优先选用。
在冲击试验期间,冲击器以6.6m/s的速度下落,试验在-40°、23°和125°C下完成。
结构SMC级别中高的玻纤含量很难保持良好的润湿性。
当研究人员用显微镜检查破碎的样品时,他们发现,有明显的玻璃纤维从基体中脱离,但没有折断。
3Ʃ数据传播的特点是噪声大,不能提供所需的安全边际量。
由于没有时间重新规划,研究人员转向采用不同的技术——玻璃纤维毡热塑性复合材料(GMT)。