1 车用复合材料的应用
1.1 汽车轻量化
汽车轻量化是指在保持汽车原有的安全性、舒适性、可靠性等目标符合设计要求的前提下,且汽车本身成本符合设计预期目标,尽可能地降低汽车的整备质量,从而提高汽车节能减排、降低燃油消耗等性能指标。
材料轻量化技术是指通过采用新型轻质材料,在保证实现原有功能及性能目标的前提下来实现降低重量的技术措施。
在轻量化趋势的影响下,各种新型材料,如轻质金属材料(铝合金、镁合金)、轻质非金属材料(低密度、薄壁化)以及先进复合材料将越来越多的应用于汽车的轻量化设计中,在整车的材料组成中比例也将随之提高。
1.2 汽车用先进复合材料
高分子复合材料按性能高低,可分为通用复合材料和高性能(先进)复合材料。高性能高分子复合材料是采用新技术、新工艺或新设备研制的具有优异性能或特殊功能的复合材料。国际上一般是指以碳纤维、芳香族聚酰胺合成纤维(芳纶纤维)、硼纤维等纤维和晶须等高性能增强体与耐高温的高聚物等基体构成的复合材料,具有高的比强度和比模量、各向异性和可设计性、良好的抗疲劳特性、易于整体成形,还可具有吸波、透波、导电、半导、发热、耐热、记忆、阻尼、摩擦、吸声等功能[2]。
复合材料是各向异性的非均质材料,具有如下特点:
(1)比重小,质量轻。密度比钢、铝、镁等金属材料都低,以碳纤维复合材料举例,其密度约为1.7g/cm3,而金属材料中钢的密度为7.85g/cm3、铝的密度为2.75g/cm3;
(2)比强度和比模量高。比强度可达钢的14 倍,是铝的10 倍,而比模量则超过钢和铝的3 倍;
(3)可靠性佳,层压的复合材料对疲劳裂纹扩张有“止扩”作用,这是因为当裂纹由表面向内层扩展时,到达某一纤维取向不同的层面时,会使得裂纹扩展的断裂能在该层面内发散,这种特性使得FRP 的疲劳强度大为提高。研究表明,钢和铝的疲劳强度是静力强度的50%,而复合材料可达90%。;
(4)耐磨性好,通过掺入少量的短切碳纤维可大大地提高它的耐磨性,如聚丙烯为其本身的2.5 倍;聚酰胺为其本身的1.2 倍;
(5)化学稳定性优良。可长期在强酸、强碱等环境下使用;
(6)耐高温。纤维增强复合材料中,除玻璃纤维软化点较低(700~900℃)外,其他纤维的熔点(或软化点)一般都在2 000℃以上;
(7)设计自由度高。可根据构建的设计目标通过增强材料的分布、层数及纤维种类和树脂含量实现自由设计。
车用复合材料因其具有质量轻、比强度与比模量高、刚度好,可靠性佳、耐磨性好、化学稳定性优良、设计自由度高等特点,更有利于在汽车零部件上推广应用。
1.3 车用复合材料的应用
车用复合材料随着汽车轻量化的推进和新能源汽车的迅猛发展得到了广泛的应用。
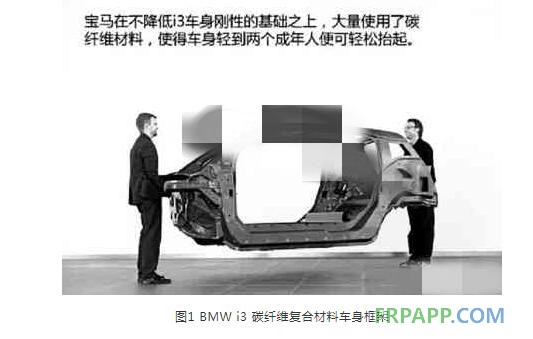
复合材料应用于汽车行业最早开始于1953 年,车用复合材料起初被应用在少数的汽车发烧友和商用车辆上使用,汽车发烧友将其用于改装和装饰零件使用;在商用车领域主要在重卡车上使用。
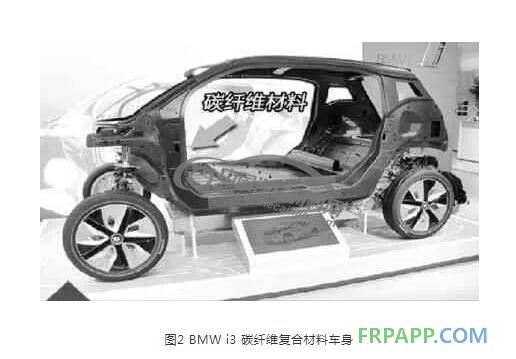
自2013 年宝马推出两款大量使用碳纤维复合材料的电动汽车i3 与i8,随着i3 与i8 的量产,开启了碳纤维复合材料在汽车上应用的风暴,各大汽车厂商纷纷开始复合材料的研发。
目前车用复合材料在汽车上的应用主要以碳纤维复合材料(CFRP)、玻璃纤维增强复合材料(GFRP)、金属基复合材料(MMC)等为主。
中国品牌主机厂对复合材料的探索主要集中应用在车身、内外饰、底盘传动、动力总成等系统。典型的系统零部件如下:
内外饰系统:保险杠面罩、后视镜壳体、扰流板、中网格栅、门内板、仪表板等;
车身系统:上车体,顶盖和顶盖横梁、后地板、车门外板等;
发动机系统中的进气歧管、发动机缸盖罩、发动机档杆、发动机装饰罩盖等;
传动系统中的传动轴、制动踏板、离合器片等;
底盘系统中的悬置、摆臂、框架、板簧等。
2 车用复合材料的开发关键
2.1 汽车用复合材料的探索
随着汽车在国内的销量和保有量不断增加以及燃油及能源消耗的不断上升,国家鼓励和支持发展新能源汽车并提供新能源汽车专用补贴。大力发展新能源汽车,续航里程是消费者考虑是否购车的关键因素之一,在电池能量密度恒定的前提下汽车持续减重可以提升续航里程,而车用复合材料可以替代汽车传统采用的金属材料以降低汽车整备质量实现减重。各大整车生产制造商也纷纷开始加大研发投入,探索汽车用复合材料在汽车各系统中的应用并开始寻找适合汽车应用的专用复合材料。经过调研和探索发现如果直接按照金属材料的设计目标将传统的钣金替换为复合材料是很难实现,而且基于传统的制造工序也存在许多问题,尤其批量生产制造方面,复合材料的应用还是有局限的,其中包括汽车专用的复合材料研发、与整车传统制造工序的结合、复合材料的维修以及和金属材料的连接和复合材料的回收等问题。
整车企业对车用复合材料的探索,是从市场调研阶段、深入学习阶段、实践消化阶段到深化实践阶段和创新应用阶段不断发展的。
2.2 车用复合材料的开发关键
起初整车企业研发人员大多采用“等代替换”的原则来开发设计复合材料零部件,即采用传统钢制部件的结构形式和性能要求作为设计目标和要求。这是因为整车企业的研发人员大多对复合材料性能和知识没有全面的了解,同时目前的设计手册和设计案例也都是以金属材料为主而制定的。复合材料主要由基体材料和增强材料两部分组成,其基体材料及增强材料的特性决定了复合材料的特性。复合材料与金属材料具有不同的自身属性,复合材料为各向异性;金属材料为各向同性。复合材料和金属材料的失效模式不同,复合材料失效模式复杂多变,属于渐进式韧性破裂失效,而金属材料的失效模式为塑性变形导致的屈服断裂失效。
汽车用复合材料的开发需要在正向设计的基础上结合材料、结构、制造工艺、成本等方面进行综合设计。仅依照结构的设计和忽视材料的设计都不能使复合材料达到最优化的设计。同时目前也面临着复合材料特性参数不足,汽车专用复合材料缺乏,复合材成本较高和复合材料零部件维修及保养等问题。
综合所述车用复合材料的开发应在具有汽车专用复合特性数据库的前提下从选材、制造、喷涂、维修和与金属材料的连接以及回收等方面进行综合考虑。汽车用复合材料的相关标准也应逐步完善和制定。
2.3 车用复合材料的开发建议
按照《节能与新能源汽车技术路线图》有关轻量化技术路线的发展目标指出,预计2026 年至2030 年实现整车比2015 年减重35%,重点发展镁合金和碳纤维复合材料技术,实现碳纤维复合材料混合车身及碳纤维零部件的大范围应用,单车用镁合金达到45kg,碳纤维使用量占车重5%。
整车企业研发设计人员和材料工程师大都对复合材料没有深入了解,目前正进入探索和实践阶段,经过近几年的市场调研及探索,初步具备了复合材料的设计开发团队。然而复合材料生产企业往往对于汽车主机厂的开发流程、质量体系、供应商管理、供应链物流、材料认可及实验认证均不熟悉。从而形成了主机厂找不到需要的复合材料供应商,复合材料企业也无法完全满足主机厂要求这一现象发生。特别是复合材料供应商到复合材料零部件供应商的身份进阶和转型需要加快,主机厂往往采购的是复合材料零部件而不是复合材料纤维。
所以建议整车企业逐步深入对复合材料进行研究,并建立研发项目团队和人才梯队以满足对复合材料的设计要求;同时复合材料企业目前也要深入到主机厂进行沟通交流,逐步完善相关要求以满足整车企业,以实现共同开发及同步开发的要求。
整车企业作为终端载体,需要对整体产业链负责,鉴于目前复合材料材料性能参数数据不完整,复合材料及零部件试验检测方法不完善,复合材料结构设计规则不统一等多方面应建立相应的体系和流程。
复合材料企业应推进复合材料的成本优化,并可实现由材料至零部件这一过程,按照主机厂要求建立健全质量体系,以满足整车企业要求,并深入主机厂开展复合材料的交流以推动其在汽车的应用。
3 结束语
车用复合材料在整车上应用范围不断扩展,伴随着复合材料厂商对汽车专用复合材料加大了研发投入,汽车专用的复合材料促使了复合材料在汽车上使用范围和使用量均双双上涨。对车用复合材料零部件的开发需要团队协作,通过顶层的正向设计结合材料、结构、制造工艺、成本等方面进行综合设计。复合材料厂商应更早的进阶成为复合材料零部件制造商这一身份转变,在复合材料零件的研发阶段介入主机厂的研发团队为车用复合材料零部件的开发提供技术支持和工艺试制。通过主机厂与复合材料厂商的共同推进,将更快的加速汽车用复合材料产业化的发展。