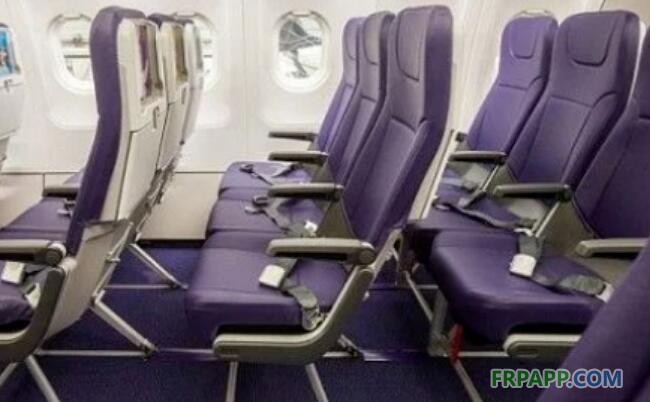
汽车、高铁、飞机上的座椅在设计时必须满足安全、舒适、功能完善、造型美观等多项要求,在满足座椅传统性能要求的基础上,尽可能地降低座椅的重量,这是轻量化发展对座椅提出的基本要求。
碳纤维复合材料座椅骨架的性能
从目前的情况上看,碳纤维复合材料是替代钢、铝等传统金属材料制作座椅骨架的最佳材料之一。碳纤维以“质量轻、强度大”而闻名于新材料界,其密度在1.7g/cm3左右,仅是钢材料的五分之一,但是抗拉强度却在1700MPa以上,不仅如此,碳纤维还对酸碱盐的等化学物质都有很好耐受能力,不用担心腐蚀、生锈的问题,抗冲击吸振能力也很强,因此,很适合用来替代金属材料来制作座椅骨架。据一家拥有多年航空碳纤维部件开发制造经验的公司,提供的数据可知,用碳纤维复合材料制作的座椅骨架比同尺寸的钢制骨架能减重50%以上,比铝合金骨架也能减重30%左右。
使用碳纤维复合材料制作座椅骨架主要要从静态强度、刚度、动态冲击和疲劳强度这几个方面是检验和衡量其安全性能。除此之外,由于座椅应用的空间环境具有特殊性,因此,座椅的制作材料是否具有阻燃性也是测试和评判的重要标准。因为事故死亡率中主因之一就是交通工具发生事故或者碰撞时,乘员因吸入了有毒有害气体致死,如果车内部件材料在遇明火后能做到阻燃低烟低毒,则将很大程度地提升了乘客的人身安全。
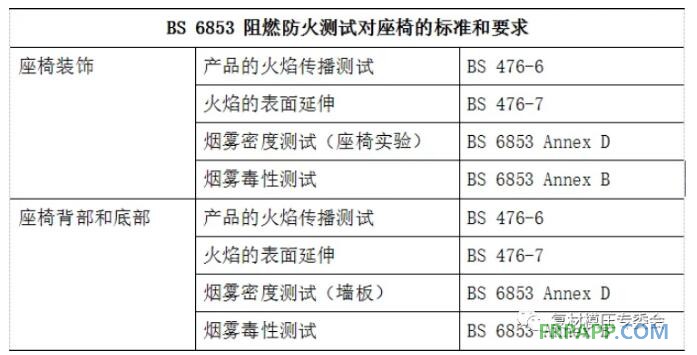
碳纤维复合材料座椅骨架的成型
应用于航空、汽车、高铁中的座椅需要规格一致、性能稳定的量化型制造技术。除了手糊袋压成型、真空导入等工艺外,用热压罐固化成型的方法正被积极尝试应用。
热压罐的工艺流程是将预浸料逐层铺贴于模具上,形成零件叠层,然后经热压罐加压加热固化成型。使用该材料时,在操作过程中不易出现纤维的滑动和弯曲现象,纤维方向的一致性和准直度可以得到较好的控制。由于使用半成品的预浸料,可以连续铺贴,提高了速度,因而取代了以往重复交替的纤维和树脂的逐层铺贴工序,使得生产效率大为提高。根据制品的不同,预浸料成型工艺的产量一般在几千到几万件之间,非常适合于座椅骨架这类批量化碳纤维产品的生产。
此外,在热压罐压力的作用下,产品可以实现较高的纤维含量而得到较高的力学性能,其产品的致密性更高,其强度性能也更好,用这种方法制作的座椅骨架更符合航空、汽车、高铁等特殊运行环境下的高要求。
从实验数据到市场应用情况看,使用碳纤维复合材料制作航空、汽车、高铁中的座椅骨架,不仅可以实现轻量化目标,节省能源消耗,更能有效提升座椅的安全性能,值得在更大的范围内进行推广使用。