(一)行业产能产量情况
“十三五期间”,受惠于内需市场持续发展壮大,玻璃纤维纱产能及产量均保持稳定增长。截止到2020年年底,国内大陆地区玻璃纤维纱总产能约为580万吨。2020年玻璃纤维纱总产量为541万吨,同比增长2.64%。

(二)内需与外贸市场情况
内需市场方面,一是在增强复合材料市场方面,随着环保规范管理要求日趋严格,复合材料制品行业加速实施产业结构调整,一大批小散乱企业被迫实施关停并转,规模以上企业生产经营和市场竞争环境得到持续优化,从而带动玻璃纤维应用需求升级;二是在产业用纺织品方面,电气绝缘、建筑保温、环保、装饰装修等相关产业个性化需求规模持续快速增长,带动各类工业用玻璃纤维制品差异化、规模化快速发展。
外需市场方面,为避免过度依赖外需市场所造成的不利影响,玻纤行业在“十三五”期间提出了主动降低产品出口比例,同时实施产能全球布局的发展思路。2020年我国玻璃纤维及制品出口约为133万吨,行业出口比例已经由“十二五”末的38.7%降至24.6%。与此同时,我国玻璃纤维企业海外产能在“十三五”期间增加29.3万吨,由“十二五”末的13.5万吨增长到42.8万吨,有力支撑了我国玻璃纤维产业的全球化发展。
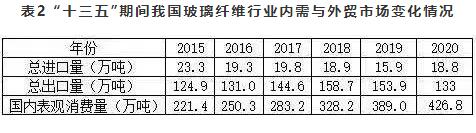
(三)技术与装备创新情况
“十三五”期间,玻璃纤维及制品生产技术与装备不断提升。
池窑企业通过优化工厂总体布局、改造应用更加智能化的生产和物流装备、创新工艺流程、搭建智能工厂大数据管理平台并进行模拟仿真,实现实时数据库平台与过程控制、生产管理系统互通集成、制造执行系统(MES)与企业资源计划管理系统(ERP)集成等,不断提升智能制造水平。粗纱池窑生产线熔化率最高可达3.6t/d.m2,人均玻璃纤维纱年产量最高可达400吨;细纱池窑生产线熔化率最高可达2.2t/d.m2,人均玻璃纤维纱年产量最高可达180吨。企业生产效率、能源利用率实现较大幅度提升,运营成本、产品不良率以及产品研制周期进一步降低和缩短。
坩埚拉丝生产企业通过实施分拉、大卷装、大漏板、双层作业线,以及原料球、浸润剂及窑炉温度智能化集中控制系统等工艺改造,降低工人劳动强度,提升企业生产效率。
制品深加工企业则通过积极寻求更高效的织造技术与设备、更先进的后处理工艺与装备,实现产品质量与附加值水平的进一步提升。
(四)应用研究与产品开发情况
“十三五”期间,电子细纱及电子布产品系列化研发与生产实现较大突破。7微米、5微米等玻璃纤维细纱陆续实现大批量池窑化生产,7628标布产能规模迅速扩大,各类薄布、超薄布国产化水平不断提升,满足了下游电子通讯行业转型升级的需求变化。
“十三五”期间,各类热塑性玻璃纤维及制品也得到快速发展,产品种类和产能规模都得到迅速提升,但在浸润剂研发环节,与国外先进企业相比仍有差距。
“十三五”期间,高模量、高强度、低介电、高硅氧、耐碱、耐腐蚀、异形截面、本体彩色玻璃纤维及玄武岩纤维等各类高性能玻璃纤维均得到进一步发展,部分高性能玻璃纤维实现了池窑化生产,未来市场潜力巨大。
(五)节能减排情况
“十三五”期间,玻璃纤维生产企业通过改进原料配方、提升熔化效率、提高综合成品率等措施,不断降低产品综合能耗。其中,池窑粗纱产品综合能耗先进值由“十二五”末的0.55吨标煤/吨纱降低至0.35吨标煤/吨纱,池窑细纱(7至9微米)产品综合能耗先进值由“十二五”末的0.75吨标煤/吨纱降低至0.45吨标煤/吨纱,坩埚纱产品综合能耗先进值由“十二五”末的0.37吨标煤/吨纱降低至0.30吨标煤/吨纱,无碱球及中碱球产品综合能耗分别达到0.35吨标煤/吨球和0.25吨标煤/吨球。
“十三五”期间,随着国家环保政策趋严及各地环保标准要求提升,玻璃纤维行业在生产线环保设施方面持续加大投入。在废气方面,企业配备了除尘脱硫脱硝等环保设施,先进企业颗粒物、二氧化硫、氮氧化物排放浓度分别稳定控制在10mg/m3、50mg/m3、100mg/m3以内;在固体废弃物方面,企业通过对废丝进行原地分类预处理,实现各类废丝回收再利用。
(六)存在的主要问题及原因
(1)行业中低端落后产能仍然存在且持续发展;
(2)企业创新发展意识和能力水平不足,行业供给侧结构性改革任务较重;
(3)产业链供应链协同创新意识较差,行业需求侧管理能力亟待提升;
(4)企业生产及物流自动化、智能化水平有待进一步提升;
(5)行业绿色发展任重而道远,碳减排工作亟待开展;
随着中国经济持续发展,中国企业正在逐步从各领域各行业的参与者、追赶者,变成现有及潜在领域的引领者、拓荒者。而新冠肺炎疫情的爆发和防控,不仅对全球经济造成影响,也深深地影响到了全球政治、社会、文化的各个方面,并对人类的生产生活方式产生巨大影响。人类社会的发展进步,为玻璃纤维行业发展提出了很多新的发展要求和新的应用需求。(未完待续)
中国玻璃纤维工业协会