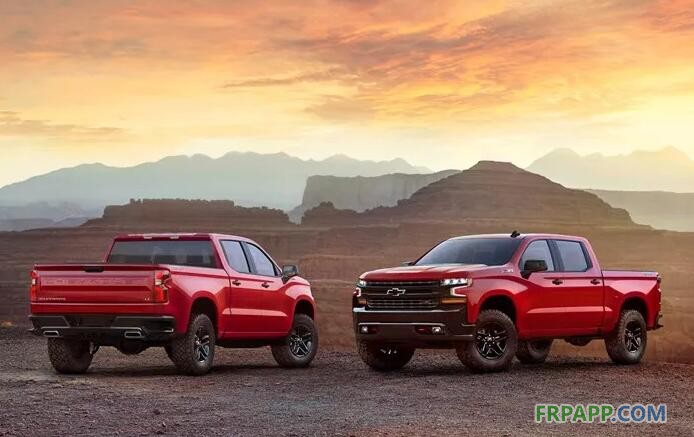
在钢制保险杠后部左前和右前这样一个隐蔽但极为重要的位置,通用2019 雪佛兰Silverado皮卡为复合材料带来了新的结构应用机遇。由热塑性复合材料/金属混合材料制成的支架不仅质量更轻,还在有限的包容空间中实现了等效的或更好的模态、应力、疲劳和碰撞测试性能,减少了腐蚀和保修风险,为整合关键部件提供了更大的自由度(图片来自通用汽车公司)
作为一名OEM设计工程师,开展全尺寸皮卡项目研究并非一件易事:一方面,要确保车辆尽可能安全、功能丰富且燃油效率高;另一方面,用户,尤其是建筑和农业领域的用户,每天的用车频率非常高,对什么是耐用材料、什么是非耐用材料有一定的见解,他们了解并信得过钢材。但对复合材料呢?也许,他们了解和信任的程度并不高。
当通用汽车公司全尺寸皮卡的首席设计发布工程师Chris Heo与其团队开始开发最新一代的雪佛兰Silverado皮卡时,他们讨论了哪些部件可以用复合材料取代金属从而减轻车辆质量。
就2019 车型而言,已经决定要保留带有防撞条的保险杠风格,即在车辆的前后采用由冲压钢制成的保险杠,它的A侧表面采用镀铬装饰或者与车身漆色保持一致。基于其形状造型,再加上钢制外壳较重的质量,该保险杠通常需要一个或多个钢制加强支架,用于将保险杠与车架连接起来,满足通用汽车公司对保险杠的耐久性、车辆的损伤性、碰撞性能和包容空间等方面的要求。在此情况下,保险杠的左、右角会含有一对支架,但该团队的成员们想要知道的是,可否将这些又重又复杂的多个冲压件改造成更轻质的部件,同时又不影响性能和耐久性呢?
“我们讨论了保留保险杠的金属外壳、但将隐藏的部件转变成采用轻质材料的方法。”Heo回忆说,“我们知道这具有挑战性,因为需要用坚固的支架来支撑保险杠这样的重物, 而且保险杠和支架的耐久性必须与车辆的使用寿命保持一致。此外,在满足严格的、难以通过的偏置防撞试验要求方面,这些支架起着关键作用。”
第一个尝试
面对挑战,通用团队开展了研究,并很快让车辆指定的保险杠供应商——美国Flex-N-Gate公司(以下简称FNG)参与进来。最初,由于车辆外部造型尚处在最终敲定阶段,因此该联合团队花了一年的时间,研究了行业选项并讨论了可行的方法。
“我们在等待合适的时机,因为取决于最终的造型,我们的设计和方法都有可能发生变化。”Heo解释道。
“我们知道,另有一家公司已在其用于货车的一个保险杠上使用了复合材料制成的非常小的支架,虽然这是一个非结构性的支架,却为我们提供了参考。”FNG工程团队塑料/金属研发经理Steve Perucca补充道。在将乘用车上的金属结构部件转变成热塑性复合材料部件方面,FNG 已积累了丰富的经验,这为该团队树立了信心。
设计考虑因素
随着皮卡外观设计的确定,该联合团队开始了支架的设计工作。基准支架由高强低合金钢冲压而成,与碳钢相比,这种高强低合金钢拥有更高的机械性能和更好的耐腐蚀性。这些支架拥有3mm的公称厚度,每个重4.362kg。相比之下,如果采用复合材料的支架,设计时就要考虑多个因素:
首先,需要将复合材料的支架安装在大致相同的空间内,且被限制在保险杠的后面,因此,需要一种强度足够的材料,以确保部件厚度不会增加太多。
其次,为了达到设计所需的造型效果,前保险杠通常要包裹住车辆的前角。但是,由于前保险杠是被坚硬的钢支架固定在车架上,因此在高速碰撞事故中,可能会被挤压到车轮中,从而对车轮定位带来负向影响并锁定转向。为了尽可能长时间地保护受碰撞一侧的车轮,可取的方法是,使保险杠支架在撞击过程中脱落。但另一方面,为了避免保修问题,保险杠需要在车辆正常使用期间保持连接状态。显然,该团队必须考虑如何平衡好这些相互竞争的要求。
该团队想要解决的另一个问题是,由于钢的成形性限制,不能将基准支架成形为可以固定车辆雾灯的形状,这就需要增加一对较重的金属支架。如果可能,该团队希望将雾灯支撑架整合到复合材料的支架上。
另外,避开线束夹点也很重要。线束夹点会穿过支架来固定线束,防止可能导致前照灯和风扇等重要部件发生短路的电线擦伤和断裂问题。为此,可以在金属支架上开一个孔,以使电线穿过,但这会带来额外的冲孔操作步骤,再加上设计自由度的限制,还会增加模具成本。而用复合材料支架来解决这一问题却是可取的。当然,还有一点也很重要,就是要避免因使用复合材料的车架而不得不改变车辆的装配工序。而且,就像汽车应用中经常要求的那样,与金属的基准支架相比,复合材料的支架最好能够更轻质、更便宜。最后一个问题是,目前可用的CAE模型是否能准确地预测不连续纤维增强热塑性塑料的高周疲劳/耐久性。
混合材料方法
该团队首先要决定选用什么材料,也就是说,要使用FNG已经用过的并已得到通用汽车公司许可的材料。为此,他们选用了韩国乐天化学公司的一种黑色长玻纤增强聚丙烯(LFT-PP),名为Supran PP1340 GMW15890P,其纤维重量百分比为40%。由于支架不会暴露在阳光下,且距离发动机的热量足够远,因此,这种强韧的烯烃聚合物能提供足够的耐热性。由于熔体流动指数为40,因此,这种高流动注射级别的材料还确保了在不增加额外浇口的情况下,完美地填充复杂的形状。如果增加额外的浇口,会形成比周围材料弱的熔接线,这在结构部件中是绝对不允许的,特别是那些必须通过碰撞测试的部件。
为了平衡好长期耐久性与高碰撞性能这两个彼此竞争的要求,该团队采用了一种混合材料的方法。他们将支架分为两部分:连接保险杠与车架的部分仍然采用高强低合金钢,但外面的部分转变成采用复合材料。这种方法为部件整合提供了较大的设计自由度,减轻了部件质量并能够将雾灯整合进来。但是,针对复合材料部分的设计,应确保其在高速侧面碰撞中能够脱落,以使车轮的定向尽可能长时间地保持纵向,这对于保持转向力极为有利。
为了满足通用汽车公司的所有要求,该团队在支架的复合材料部分添加了一些金属嵌件,再加上3个轴套,则为在装配过程中进行调整提供了便利。设计师发现,这种材料可以毫无问题地允许支架的腿(CAE设计中棕色的弯曲端部)伸展开来以包裹住雾灯,这样,就无需在此处使用额外的支架。
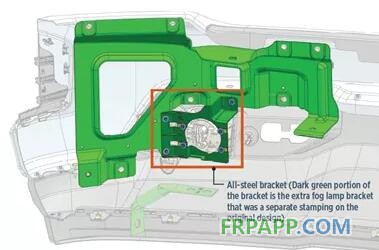
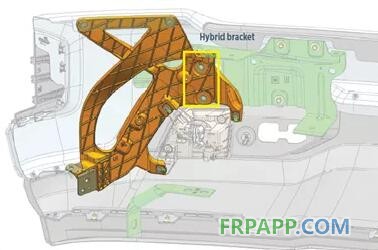
设计混合材料的结构保险杠支架之前(上图)和之后(下图)。采用一种独特方法,即三螺栓/双面的机械紧固系统(黄色轮廓线),即将混合材料支架的复合材料部分(棕色)与钢部分(绿色)连接起来,同时还减小了应力。沿支架的前表面使用了两个螺栓,第三个螺栓则用在其上方。轴套上的限制器可防止组装过紧。相比之下,如果采用结构粘合剂进行粘接,会增加时间、机器人、固化架和车辆的装配成本(图片来自通用汽车公司)
随着项目的向前推进,该团队生产并测试了实体部件。他们高兴地发现,他们的CAE模型相当准确。“就耐久性和高重力负载而言,我们试图预测高周疲劳,因此一开始我们就想知道,我们能否在碰撞模拟中正确模拟这个部件。”Heo介绍说,“令人惊讶的是,在振动试验甚至在碰撞试验中,预测结果与实测结果高度一致。”
最终,该团队在不到6个月的时间里完成了支架设计。它的尺寸大约是41cm×46cm,公称壁厚3mm,带有肋,因而提供了较高的力学性能。
模具由加拿大Integrity Tool & Mold公司制造,这是一副排气良好、拥有两个型腔的2+2叠模,两个直接注射点(冷流道)采用顺序阀浇口,每次循环可以生产出4个部件,循环周期60s,因而满足了Silverado 平台的高产量需求。该部件的成型商是FNG的Ventra Evart 部门。
重大成果
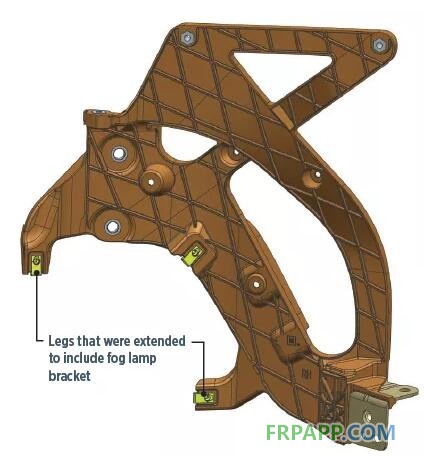
最终经拓扑优化的复合材料支架设计整合了众多的部件,包括之前单独的雾灯支架,以及用于提高力学性能同时确保公称壁厚不超过3mm的结构肋。在容易出现明显疲劳或者承载路径上必须得到加强以确保拥有适当碰撞性能的区域,使用了几个金属嵌件,以帮助提高性能(图片来自通用汽车公司)
由混合材料方法制成的结构保险杠支架令通用汽车公司在首次商业化应用中就获得了很多好处:
首先,该支架在模态、应力、疲劳和碰撞测试方面都达到了等效或更优的性能。
第二,复合材料的设计自由度允许在一个相对较小的包容空间里实现更有冲击力的造型。
第三,与基准支架相比,一对混合材料的支架使每辆车减轻了2.5kg的质量。同时,归功于质量分解效应,更轻的保险杠转角还使得保险杠安装支架和其他部件的尺寸更小,从而使前保险杠系统的总质量要比2016车型的减轻了7.3 kg。
此外,由于复合材料的支架不会生锈,还降低了腐蚀风险和保修成本。质量的减轻有助于提高燃油经济性,或者可以在不超过法定道路载荷限制的情况下运载更重的载荷。
如果按部件计价,由于增加了注射模具的成本,这种混合材料的支架似乎并不划算。但如果按系统成本计算,由于能够精简额外的组件,因而更具成本效益,虽然实际节省的成本很难量化。
目前,该支架实现量产已有3年多的时间,没有出现过任何问题。针对下一代的Silverado车型,Heo的团队计划继续在前保险杠上采用混合材料的支架,但他已要求团队开始考虑如何将这种混合材料的方法用在后保险杠支架上。这很复杂,因为后保险杠的转弯处有助步功能,以使人们能够更轻松、更安全地爬进/爬出皮卡车厢。此外,在钢制外壳的后面还容纳了较多的部件(如后备警报传感器),因而包容空间更小。
“我们将继续使用智能工程方法来研究问题,弄清楚产品如何得到应用,它们的功能需求是什么,然后挑战极限。”Heo最后总结道。