初步的IACMI/ORNL研究,评估了采用热塑性聚合物3D打印模压成型SMC用模具的可行性。
为了能够在不影响关键性能的前提下,以更低的成本将零部件更快地推向市场,OEMs及复合材料供应链的成员们正在不断寻求新的方法。随着模拟工具的日益精确以及材料成型速度的日益加快,最终限制新产品上市速度的重要一步,就是部件成型所需的高成本、长交货期的金属模具的制造过程。为了缩短这一步骤,人们将更多的注意力集中到了增材制造技术上,希望通过对聚合物和金属的3D打印来制造可行的模具,以化解这一关键步骤带来的瓶颈。
采用传统的“减材”制造方法,如研磨、切割、钻削和电火花加工等,制造一副用于模压或注射成型的P20钢大型汽车模具,可能需要24 周的时间,相比之下,增材制造能将模具的制造周期从几个月缩短到几周甚至几天,同时还能降低成本和重量,重量的减轻则有助于减少模具制造带来的碳足迹。
作为美国能源部(简称DOE)先进复合材料制造创新研究所(简称IACMI)支持的一个大型研究项目的一部分,美国能源部橡树岭国家实验室(简称ORNL)所属的制造示范工厂(简称MDF)开展了一项初步研究——用热塑性复合材料3D打印用于模压成型片状模塑料(SMC)的模具,如图1所示。
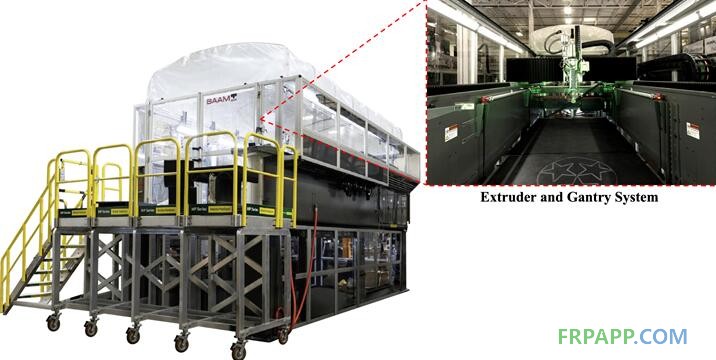
图1 由ORNL和IACMI 联合开展的一项研究,尝试采用耐高温的碳纤增强热塑性塑料,在大型增材制造系统上3D打印出用于产品开发的SMC模压成型模具。虽然还有更多的工作要做,但这项研究表明,此概念是可行的,它为那些准备开发新的复合材料部件的制造商提供了除依靠模拟或者花费大量的时间和成本制造硬模具之外的第三种方案(图片来自ORNL)
工程项目范围
该项目是作为一个更大的、多年期的IACMI项目的一部分而开始的,参与IACMI项目的成员包括一家欧洲的汽车制造商,以及代表汽车复合材料供应链的IACMI组织的成员。
“我们这个项目的OEM合作伙伴想要了解有关SMC的知识,所以我们设计了一系列的试验来探索什么是可行的,同时保持开放的心态。”位于田纳西大学诺克斯维尔分校的、由ORNL主管的IACMI的所长兼首席技术官Uday Vaidya回忆说,“我们的研究需要解决的一个问题是,看看能否3D打印出用于成型SMC的复合材料模具。”
“从一开始我们就知道,我们制造的模具不够耐用,无法用于商业生产。”ORNL的复合材料创新集团制造科学部研发专职科学家Ahmed Arabi Hassen补充道,“但是,快速、低成本地制造原型模具的前景,为我们提供了一个探索未知的机遇,因为这能够为制造商提供一种新的方法,以取代单纯依靠模拟或者耗费时间和成本来制造硬模具的方法。”
研究人员们首先定义了用于成型SMC的模压模具对性能的要求,包括能够耐受130~150℃的模温以及13.8 MPa的成型压力。
从修边模具到耐高温、耐高压的热压罐模具,ORNL的团队曾经对3D打印聚合物和金属的模具作过研究。该项目则是ORNL第一次尝试采用3D打印的方法来制造一种用于模压成型SMC的聚合物模具,这可能也是在全球开展的第一个这样的研究工作。ORNL的MDF采用的大型增材制造(BAAM)打印机由美国辛辛那提公司和ORNL共同开发,这台挤出(熔丝制造类型)打印机装有大型喷嘴(直径10.16 mm),沉积速度45kg/h,能采用粒料形式的聚合物原料打印出长6m、宽2.5m以及高1.8m的部件。BAAM打印机能够快速打印出大型部件的代价是打印的分辨率低,同时会产生凹凸不平的表面,因此需要后续加工。为了确保在打印及清理完毕后获得正确的尺寸,打印的模具路径会略有增大。
“因为我们之前已经探索过所有容易实现的目标, 比如3D打印铺层模具和热压罐模具,所以我们已经筛选出了可以在BAAM机器上打印的各种热塑性塑料。”Hassen继续说道,“我们已经确定了3种耐高温的碳纤维增强材料,它们具有成型SMC所需的热性能和力学性能。”
这3种材料包括两种无定形热塑性塑料,即碳纤增强聚苯砜(CF/PPSU)和碳纤增强聚醚砜(CF/PES或CF/PESU),以及一种半结晶材料,即碳纤增强聚苯硫醚(CF/PPS)。鉴于通常在BAAM机器上打印的部件尺寸很大,研究人员们选用了碳纤维而不是玻璃纤维增强的聚合物来为模具提供必要的刚度和强度以及实现减重。此前,MDF团队已经为每种聚合物确定了碳纤增强材料的使用比例,比如,可以在半结晶PPS中添加40%~60%重量百分比(FWF)的碳纤维,50%被认为是最佳比例。“我们发现,当碳纤含量低于50%时,性能还有待提高,但高于60%却出现了干纤维束。”Hassen补充道。
由于PES和PPSU是无定形的,它们的粘度在润湿或成型温度下会更高,因此很难拥有高重量百分比的纤维,通常拥有的比重是20%~35%,其中25%被认为是最佳比例。“虽然我们可以在PPS中添加更高比例的纤维,以获得更高的力学性能,但是在打印某些形状时,这种材料更容易变形和开裂,因为模具温度和压力会上下循环变动。”Hassen表示。
概念验证: 饰板
研究人员们首先采用碳纤增强PPS打印了一副正方形的饰板模具(如图2所示),其最终的外形尺寸是355.6mm×355.6mm×3.2mm,要求该模具要能够承受1.03MPa的成型压力和130~150℃的成型温度。为了便于打印,他们改变了模具中凸起部分的角度(90°)并垂直打印了最长的一面(在Z轴上)。此外,为了防止冷却过程中热的热塑性塑料在凸起区域坍塌,他们添加了可移动的45°倒角支撑,随即会在打印完成后用机加工方式将其去掉。模具的芯模和型腔侧面在BAAM机器中被并行打印出来,整合到打印中的其他特征还包括插槽,它被打印在阴模的背面,用来容纳顶出销(如图3所示)。鉴于打印后需要加工,以使成型表面获得可接受的光洁度,他们将尺寸加大了5.08mm。打印后,将模具内表面加工光滑,并在容纳4个顶出销的位置上进行钻孔,以将一个气动顶出销系统安装到模具中。
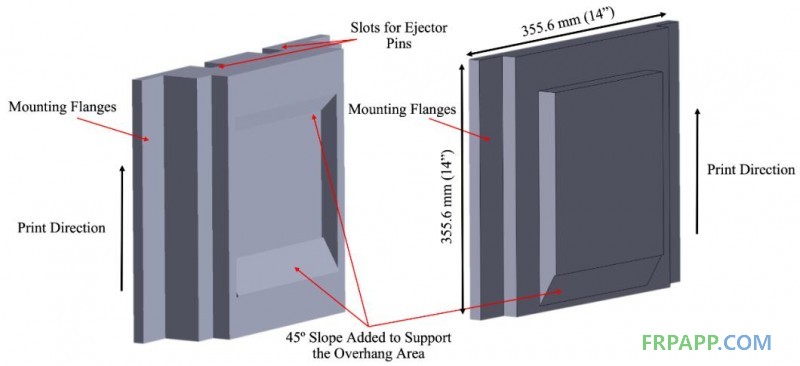
图2为饰板模具而设计的芯模和型腔,在BAAM 设备上采用碳纤增强PPS材料将其打印出来(图片来自ORNL)
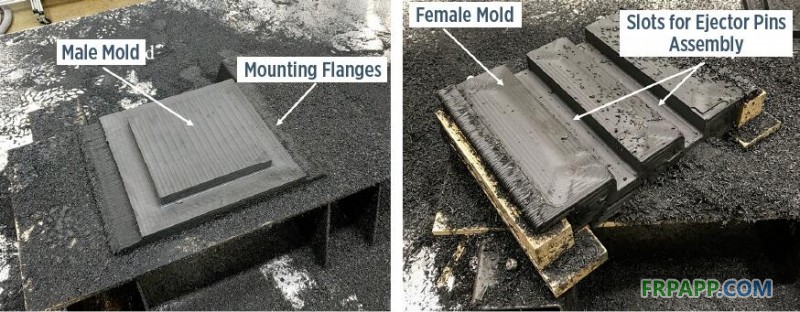
图3 打印且加工后的模具两个半模,包括用于容纳试验用的气动顶出销系统的插槽(图片来自ORNL)
接着,将模具安装到一台模压机中,利用压机模板(将其温度设置在190℃)对该模具间接或被动加热12小时,使其达到180℃的温度。如此长的加热时间是必要的,这是因为打印该模具采用的是一种热导率很低的热塑性塑料,虽然其中含有50% FWF的碳纤维(碳纤维本身的热导率很高)。研究人员们通过嵌入式传感器来监测成型表面的温度,他们发现,每次打开压机、取出部件然后放入新的SMC时,温度都会降低15~20℃,因此,有必要在打开压机、放入材料开始下一成型周期之前,先取出部件,然后闭合压机并等待模温的再次升高。
为了减少热损耗,防止模具表面温度降到150℃以下,他们在模具周围放置了额外的隔热材料,然后直接将SMC铺放到复合材料的模具表面,采用150℃的成型温度和10t的锁模力成型并固化,停留时间为5min.。他们总共生产了12个部件,整体效果良好,如图4所示。材料完全固化后,可以毫无问题地从CF/PPS模具表面(偶尔会向该表面喷脱模剂)脱离。此外,顶出销系统运行良好,成型过程中材料没有在顶出销的缝隙之间流动。
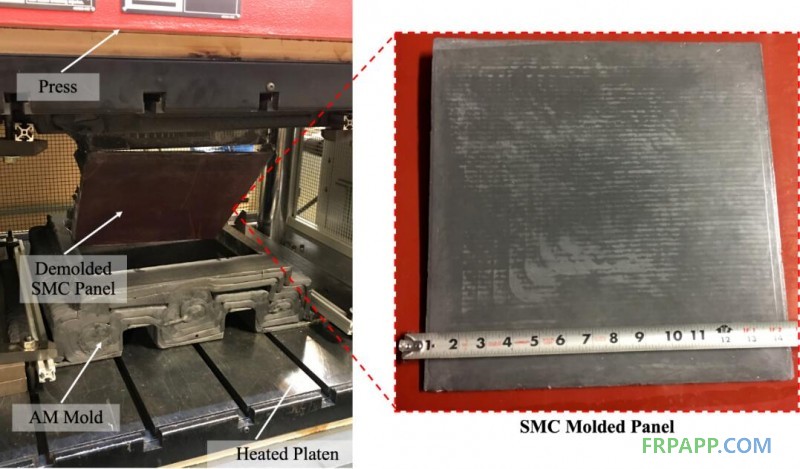
图4 采用CF/PPS饰板模具成功地成型出了SMC的饰板(图片来自ORNL)
座椅靠背示范件
接下来,研究人员们扩大了这项技术的应用范围,打印了一副更大、更复杂的汽车座椅靠背模具,尺寸是812.8mm×685.8mm×304.8mm。为了便于打印,这次他们再次改变了形状,同时在凸起区域增加了可移动的支撑结构,如图5所示。这次采用的打印材料是25% FWF CF/PPSU,芯模和型腔半模分开打印,每一半都在4h内打印完毕。和上次一样,打印后利用机加工来清理表面。由于该模具很浅,所以无需顶出销就能确保部件脱模。
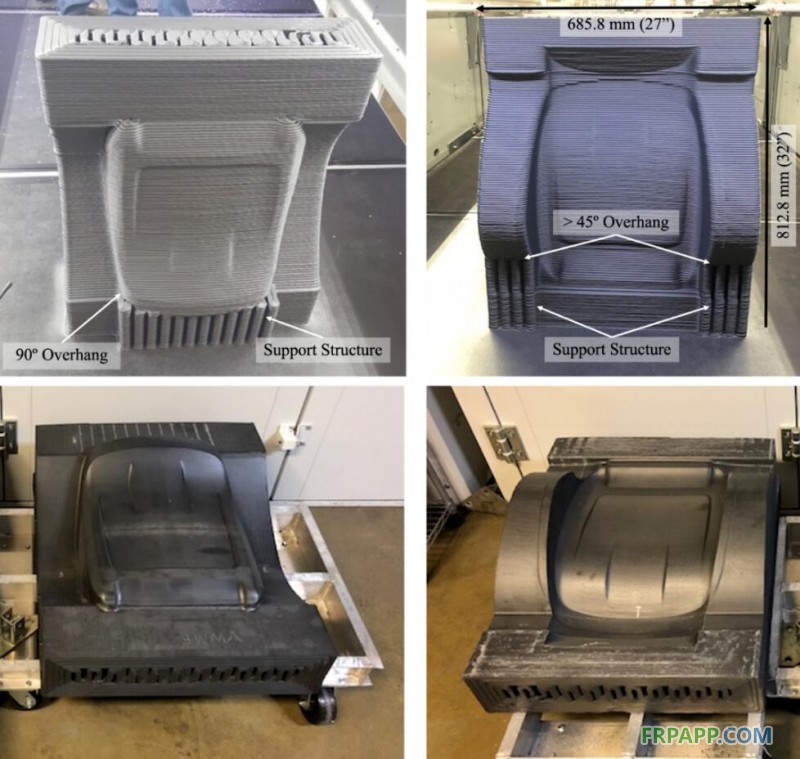
图5 采用CF/PPSU 材料打印的(上)及机加工后的(下)座椅靠背模具半模(图片来自ORNL)
和上次一样,他们将该模具安装到模压机上,利用压机模板(该模板同样保持190℃的温度)加热12h,如图6所示。由于这种打印材料的热导率更低(因为碳纤维的含量更低),所以模具表面只达到了105℃,这一温度太低而无法固化SMC。和上次一样,他们在模具周围放置了隔热材料以便更好地保温。然而,再次加热12小时后,整个成型表面的内部温度也只达到120~125℃。为确定此温度是否足以固化SMC,他们将一块坯料放入模具中,并施加30t的锁模力,结果发现,每一次开、合模后,模具的表面温度会降低10~15℃,表明它无法维持SMC正常固化所需的温度。为弥补温度的降低,研究人员们讨论了将温度提高10~15℃的方法,但是,由于加热模具需要的时间很长,所以他们认为这不切实际。因此,他们只成功地生产出了两个部件,一个部件完全固化,另一个部件存在固化不良的部分,如图7所示。
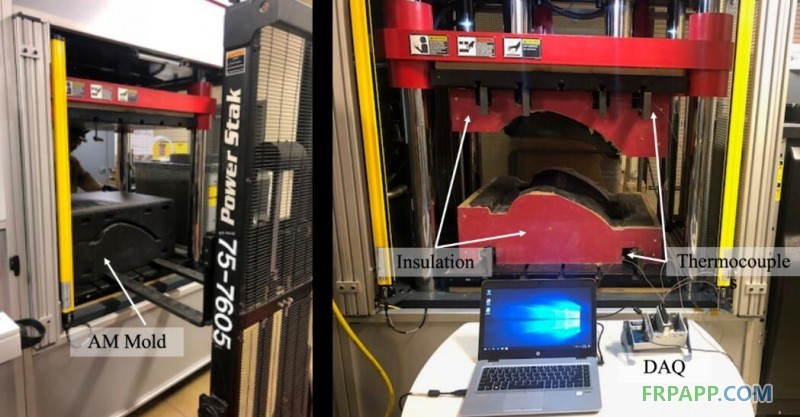
图6 安装在压机上准备用于生产部件的汽车座椅靠背模具半模(图片来自ORNL)
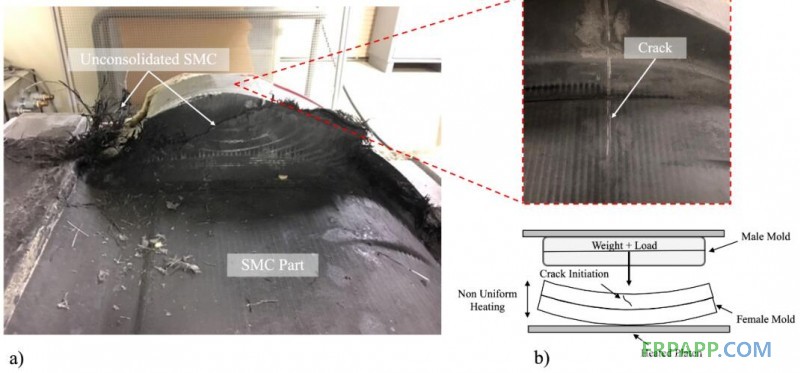
图7 对更大更复杂的汽车座椅靠背模具进行加热和保温都有难度,导致模具不均匀的加热和变形,从而在部件中表现出固化不良(a)和开裂(b)问题(图片来自ORNL)
问题管理及下一步措施
研究人员们审查了项目成果,并确定了未决问题。
好的一面是,模具在几天之内就能被打印、加工和安装好。虽然使用的材料成本要高得多,但依然比传统的金属模具省时省钱。此外,打印的模具能够承受成型SMC所需的温度和压力,而且加工后成型表面的光洁度足以生产出表面光洁的部件,虽然不能达到汽车的A级表面质量。
另一方面,模具低的热导率导致来自压机热模板的热传递非常缓慢而令人无法接受,而且每次压机打开时都会快速散热。此外,两副模具都拥有非均匀的结构(由打印方向和纤维排列所致)和非均匀的热剖面,这会导致PPS模具在延长的加热周期中出现翘曲和裂缝,以及SMC 部件的薄段在PPSU模具中固化不一致。
研究人员们得出结论,只是利用压机模板的热传导来被动加热模具的方法是低效的。所以,为了找到更快的模具加热方法,他们进行了头脑风暴:采用感应加热模具的方法所带来的模具改装成本和复杂性会超出这项短期研究的范围,而使用热导率更高的替代材料也是如此,因此,他们考虑将重点转移到开发更有效的主动加热方法上。他们提出并评估了几个方案,包括将电阻加热织物和电热丝集成到模具表面。
“虽然我们发现了一些技术问题并需要去解决,比如,采用某种形式的综合主动加热方法来达到并保持SMC的成型温度,但让我们高兴的是,我们对打印模压成型用模具的疯狂想法却奏效了。”Hassen说道,“自从该项目结束后,它已被证明是更多研究项目的核心。”