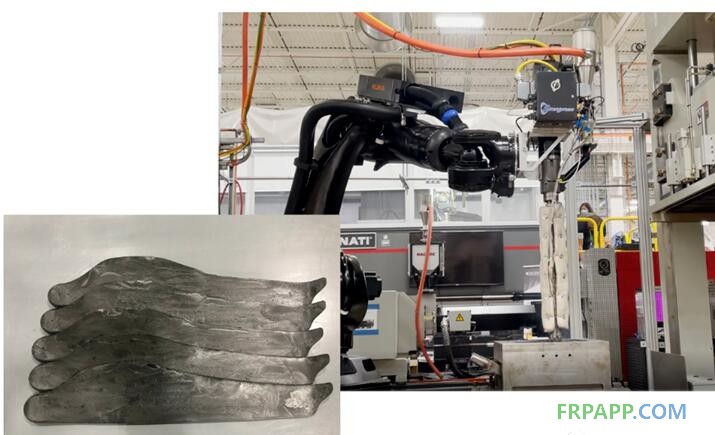
大型复合材料部件的3D打印+模压成型:为实现高性能的大型3D打印复合材料部件的大批量生产,美国橡树岭国家实验室开发了一种名为AMCM的系统,该系统组合了机器人、基于挤出的3D打印机和模压成型设备。第一个试验案例是此图所示的螺旋桨叶片,最终的应用目标是能够生产汽车电池盒及其他高产量的复杂形状的产品
在美国橡树岭国家实验室(ORNL)11万平方英尺的生产示范工厂(MDF)中,安装了一个美国能源部(DOE)的用户设施,专门用于在制造、机器人和模拟(包括复合材料)等众多领域开展早期的研发工作。
其中的一项创新是ORNL与辛辛那提公司(美国俄亥俄州Harrison)合作开发并商业化的大型增材制造(BAAM)大幅面3D打印机。一直以来,大型增材制造主要被用于制造基础设施、航空和汽车等领域所需的模具,以及机床机座、船舶结构等最终用途的部件。
传统上,大幅面增材制造的一个限制因素是,3D打印容易生产出表面粗糙不规则及孔隙率较高的部件,因而阻碍了增材制造在许多高性能最终用途部件生产中的应用。为了降低孔隙率,商业上已通过增加二次加工步骤如模压成型的方式作过多次努力。在过去的两年里,一个 ORNL的团队一直致力于开发自己的可扩展两步法工艺,以期消除大批量生产的大幅面终端用途部件中的孔隙,同时确保每个部件的生产周期不超过2.5分钟。
为高产量的大型3D打印部件开发生产单元
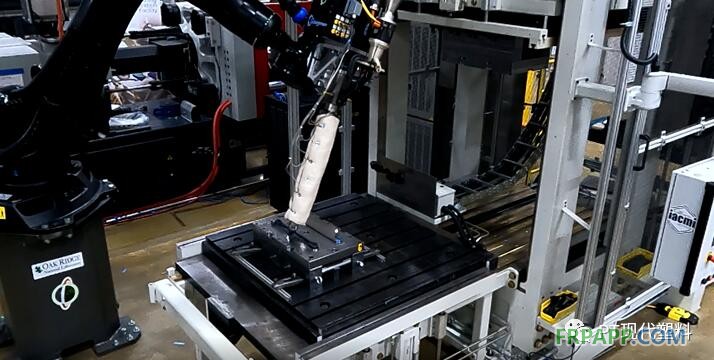
ORNL开发的工艺名为AMCM(增材制造+模压成型),它将一台采用机器人的挤出打印机与随后的模压成型步骤集于一体。
AMCM 工艺的开发已有两年多,该团队最初采用MDF现有的大幅面BAAM打印机和模压机初步证明了该工艺组合的优势,如最终部件拥有较低的孔隙率。但是,打印机和模压机彼此并不挨着,虽然两机之间距离不算远,但在模压成型前必须在带式炉上增加一个再加热的步骤,以使预成型件重新软化,达到模压成型所需的玻璃化转变温度(Tg)。然而,每个部件多预热5~6分钟,就会显著增加总的循环时间,使得每个部件总的生产节拍达到8~9分钟。
因此,他们发现,需要一个能将增材制造与模压成型组合成一个系统的专用的生产单元,以此来证明这项技术可以用于大批量的生产环境。
为了缩短这项技术的生产循环时间,ORNL提出了目前的AMCM生产单元这一概念,它于2021年11月被安装完成。该生产单元包括安装于六轴KUKA机器人手臂上的挤出打印头、一台500吨模压机和一个材料干燥系统,打印机每小时可以沉积多达150磅的材料。
ORNL于2021年秋季建成的实验室规模的AMCM单元组合了机器人、基于挤出的3D打印机和一台模压机,用于测试该系统的性能极限(图片来自ORNL)
在AMCM单元中生产部件时,首先直接在模具上挤出部件形状,从而获得一个三维订制的预成型件。该预成型件通过传送带直接进入压机,即刻成型。在材料的熔化温度或稍高于熔化温度的条件下挤出材料,AMCM 单元的设计允许预成型件在材料温度降至其玻璃化转变温度以下之前到达压机进行模压成型。
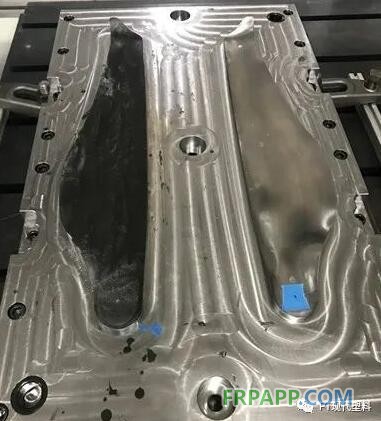
在模具中打印:为了缩短循环时间,AMCM 系统直接在模具中打印,打印好的预成型件将通过传送带进入压机(图片来自ORNL)
该团队利用AMCM单元演示生产了一个20%碳纤维增强ABS的简单平板,完成打印、压制和干燥过程的总循环时间是2.5分钟。此外,AMCM单元还演示生产了其他的平面部件,如无人机螺旋桨。
该团队希望安装在机器人手臂上的打印机可以打印尺寸相对较大或形状复杂的部件,而目前实验室规模的系统仅限于在500吨的压机上安装41英寸×48英寸的模具,而且,目前使用的模具是不加热的,但如果要打印更大的部件,可能需要加热模具,以确保3D打印的预成型件不会过快地冷却下来,以及在打印及转移到压机中的过程中温度能够保持在玻璃化转变温度以上。需要注意的是,使用加热的模具时,目前的参数如挤出温度会发生变化,在这种情况下,不必担心材料会很快冷却下来。
该单元的最初演示集中在生产单一材料的平面部件,以测试该系统的速度和性能,但该团队的最终目标是能够打印更复杂的非平面形状和多材质的部件,可以使用包括玻璃纤维增强ABS和玻璃纤维增强尼龙之类的材料。
这种方法的优势是,与传统的注射成型或挤压成型(ECM)工艺相比,可以制造出孔隙率低于1.5%的部件。该团队还在整合3D打印的纤维控制,以使纤维顺着打印珠的方向排列,从而获得模压成型的低孔隙率。
据说,该加工过程高度受控,基本上消除了所有的孔隙,实现了聚焦纤维的取向和排列。
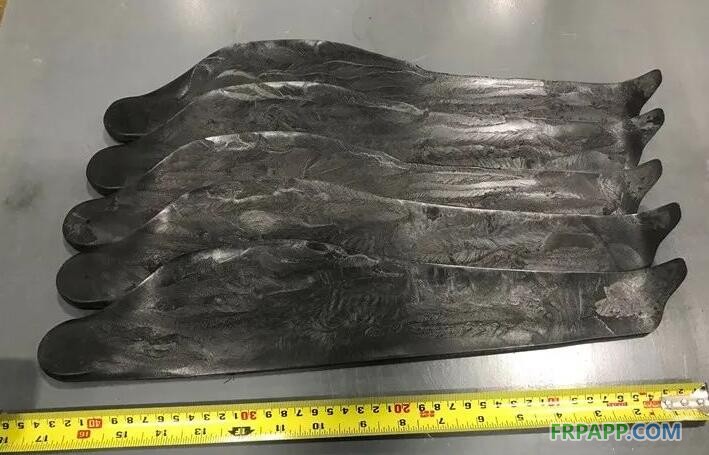
第一个测试案例:无人机螺旋桨叶片。ORNL希望其AMCM 单元能够大批量地生产商业化的部件,可能是大型部件。作为第一个测试案例,技术人员们制造了一系列用于无人机的碳纤维增强热塑性螺旋桨叶片(图片来自ORNL)
虽然现在安装在MDF的AMCM单元是一个实验室规模的系统,但据说它易于扩展成生产规模的设施,并可实现数字化、数字化设计和自动化。
该团队希望可以采用这项工艺大批量地生产汽车和城市空中交通等领域所需的下一代复合材料部件,如电池盒或座椅靠背,以及无人机螺旋桨等。完全优化后,预计该系统每小时能生产120个部件。
更多的3D打印
AMCM 工艺是MDF的主要创新之一,但不是MDF正在开发的唯一的复合材料3D打印创新。总体而言,3D打印始终是ORNL关注的一大核心领域,包括正在进行的采用其BAAM打印机实现的多材料打印、采用泡沫的打印、采用生物基再生纤维或天然纤维的打印以及将电线打印到3D打印部件的中心等。
在MDF,还安装了第一个实验室版本的反应增材制造(RAM)打印机。这是一台大幅面的热固性复合材料3D打印机,它由ORNL与美国田纳西州诺克斯维尔的Magnum Venus Products公司(简称MVP)合作开发,并采用美国Polynt公司的树脂进行打印,目前正在 MVP 附近的诺克斯维尔工厂中以商业化的形式进行开发和销售。
在MDF,ORNL继续优化材料的流动性能,采用RAM系统构建示范部件。利用RAM打印机开展的其他研究包括与MVP合作的一个项目,即将RAM打印系统与一台MVP的实验室规模的纤维缠绕机整合在一起,并安装在MDF。该项目还涉及使用RAM打印机打印示范件,然后在固化的3D打印部件周围缠绕纤维,以此通过添加材料来加强部件。ORNL还在与波音公司合作一个项目,即采用RAM 系统3D打印模具。
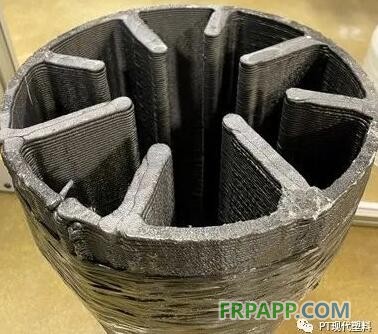
利用Magnum Venus Products公司的设备,ORNL 的研究人员们探索将纤维缠绕(提供抗压强度)整合到3D打印(获得复杂的形状)的部件上
与美国Orbital Composites公司合作,ORNL还在寻求优化多材料的机器人3D打印技术。研究人员们正在努力使该系统(能够打印热塑性或热固性的长丝)能够在非平面表面的顶部进行更准确的打印,以及将连续纤维打印到热塑性不连续纤维部件的顶部。为此,ORNL正在开展材料原料的研究,而Orbital旨在完善机器和配套的软件。正在开发的应用包括无人机部件、模具、汽车和风力发电机部件。
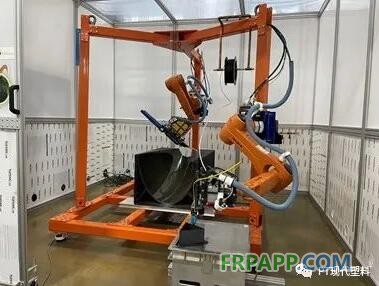
Orbital Composites公司与ORNL合作开发新的热固性和热塑性材料,用于其机器人3D打印系统,几台测试机器已安装在MDF
持续的复合材料创新: CMC、生物材料和更多
采用和不采用3D打印,MDF目前正活跃于众多的复合材料领域,包括用于极端环境如空间再入结构和核反应堆的碳-碳材料。比如,Orbital Composites公司正在ORNL的MDF尝试3D打印碳-碳材料的火箭喷管。ORNL还在研究碳-碳材料的模具,其优点是具有接近零的热膨胀系数。与项目合作伙伴美国桑迪亚国家实验室的另一项合作, 致力于将碳-碳和陶瓷基复合材料(CMC)用于国防和航空航天领域。
由ORNL的高级研发科学家Soydan Ozcan博士领导的生物基材料的开发也是一个重点,尤其是用于3D打印的生物原料。ORNL与缅因大学先进结构和复合材料中心紧密合作,开发纤维素纳米纤维(CNF),以及利用各种生产工艺来应用这些材料。在与缅因大学合作的一个试验项目中,他们在缅因大学的一台构建面积60英尺×22英尺的LFAM打印机上,采用CNF材料制成了两副模具,用于生产100英尺长的7片海上风机叶片。在此项目中,ORNL完成了材料和设备的开发。
另一个专注于可持续性的团队正在研究实验室规模的回收方法,用于回收包括风机叶片在内的复合材料部件。在此使用的系统是利用一台粉碎机和水刀切割机来探索加工/粉碎报废部件的新方法。回收再利用的案例也会得到评估,比如,将回收切碎的材料混入3D 打印的粒料中,然后送回BAAM打印机中进行打印。
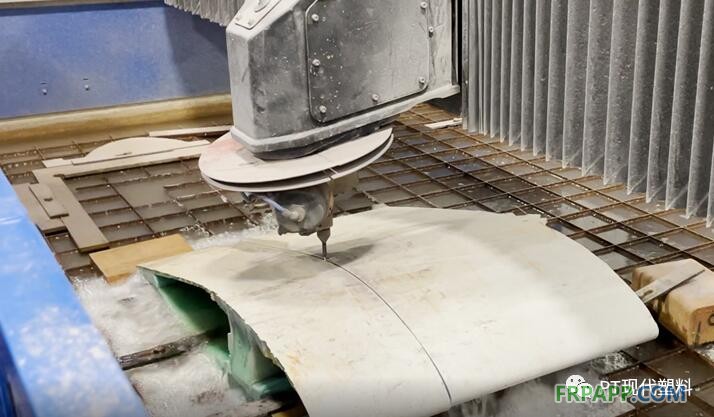
专注于可持续性:ORNL为回收报废部件而开发的解决方案包括用水刀切割风机叶片(图示),粉碎后通过3D打印或其他工艺进行再利用
距离MDF 30分钟的车程,美国能源部设立在ORNL的碳纤维技术设施(CFTF)运行着一条全范围的碳纤维生产线,使技术人员们能够试验并优化碳纤维生产的各个方面以及从生产线上下来的碳纤维的性能。一台BAAM打印机和拉挤系统能够立即采用新制成的纤维制造部件。正在开展的研究还包括采用煤制造低成本、高质量的碳纤维,以及在生产过程中采用一种方法来处理碳纤维,使它具有天然的抗雷击性,从而不需要为飞机或风力发电机部件提供额外的雷击保护。