轻型RTM工艺介绍
传统的RTM工艺,由于是闭模工艺,具有减少挥发性有机物(VOC)排放、扩大可用原材料范围、降低用工、环境友善以及可得到两面光洁的产品等优点。但是在RTM工艺中,树脂的注入是在较高的压力和流速下进行的,因此我们要使模具的结构强度和刚度大到足够在注射压力下不破坏、不变形。通常采用带钢管支撑的夹芯复合材料,或用数控机床加工的铝模或钢模,这使制造费用增大,只有对产量足够大的产品,才能抵消模具费用。此外为了闭合模具,要使周边有足够的箝紧能力或使用闭合模具的压力系统。上述因素都限制了RTM工艺在大产品上的应用,否则模具会变得很重.而且投资也会很大。
轻型树脂传递模塑工艺(RTM-Light)又称为LRTM、ECO、Vacuum Molding或VARTM。是近年来发展迅速的低成本制造工艺,目前在船舰、汽车、工业和医用复合材料领域中应用已有超过RTM工艺的趋势。
LRTM工艺保留了RTM工艺的对模工艺,从而几乎保留了RTM工艺的所有的优点。但其上模为半刚性的玻璃钢模,厚度一般为6一
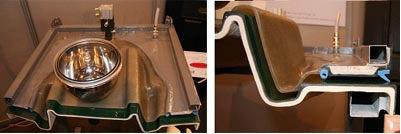
图 1,LRTM的主要设备包括树脂注入装置、模具、抽真空装置
LRTM和常规RTM比较
1、模具
模具是这两种工艺的最大差别,在RTM投资中,由于注射压力大,相当部分的成本花在模具和夹紧装置上。这样对于产量少的产品在价格上是不适合的。RTM工艺模具使用寿命可达5000件以上,生产效率高,适合年产2000件以上的产品。
LRTM的最大优势在于其模具生产成本的低廉性,费用大概只有常规RTM模具的一半,但模具使用寿命也低于RTM模具,适合年产1000件左右的产品。 LRTM工艺所生产的产品尺寸可以比传统RTM大,通常产品小到相当于一个蓝球帽,大到长
玻璃钢模具的缺点是模具表面的使用寿命短。为了得到优良的模具寿命和产品的重复性和尺寸精度,LRTM和RTM工艺的模具都必须有高质量和具有精确的截面。在复合材料模压工艺中,最终产品表面要求的成本可达到最终产品价格的60%。复合材料模具能达到汽车表面质量的使用次数为500次,然后要进行模具的表面处理。增加寿命的一个方法是使用可更换模具面(ex-changeablemold skins),如JHm Technologies公司的专利ZIP RTM技术,可用于RTM和LRTM工艺。通过使用可更换模具面来替代易损的模具表面,从而延长模具寿命和提高模具质量,模具使用寿命可达到8000一10000次。当同时使用几个可更换模具面时,由于可以在模具外的可更换模具面上直接上胶衣并加热,从而大大提高了生产效率。
2、注射压力、流量和设备
RTM工艺的注射压力一般在0.1一0.4MPa,而LRTM工艺的注射压力一般不超过0.1MPa,通常在0.03-0.07MPa。树脂注射速率随多种因素影响,如树脂粘度,部件尺寸,纤维类型和铺层结构等,通常的注射速率为1.3一
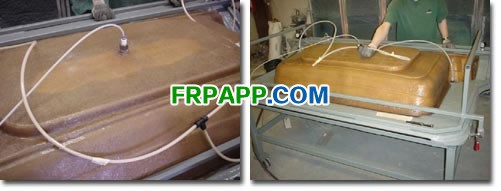
图 2 LRTM工艺的模具
为防止模具变形或冲开上模(尤其是在注射口位置),这就要求对压力有一个较为严格的控制。用于LRTM工艺的注射设备一般都带有压力反馈装置,对压力作闭环控制。也可以在RTM标准设备线上设计一个简单的气压控制系统和配合用的电子闭环系统,就可以在不导致模具变形和破坏的情况下,利用原生产设备得到最佳的生产率。
设备研究也在向低价化和多用途化发展,Plastech的SSB注射设备,采用专利的活塞改造精密计量泵,其催化剂最低配比可达0.5%,配合工业用MPG(Mould pressureguard),可由机器自行控制泵速,在12一15秒,可浸渍
3、生产效率和成本
由于注射压力较低,树脂的流速不能加速到最佳流速,LRTM工艺的生产速度比RTM工艺少一半,以每班8小时计,对于采用胶衣表面和非加热模工艺,RTM工艺每班可生产10一12模,LRTM工艺只能生产4一6模。对于一个34平方英尺需要加热固化的产品,RTM工艺,在使用水压机、加热模具、并有5个可更换模时,每班可生产40模。同样情况的LRTM工艺,可生产20模。但不需要用水压机,模具价格也低一半。
近年来通过模具设计和工艺控制的改进,两者生产速度已接近。如Xiraplas公司在采用LRTM工艺替代开模工艺后,车间变得井然有序,利用原有的50名工人,和3000平方米车间面积,使得产量增加了25%。据该公司声称和原开模工艺相比,生产效率提高了90%。
4、流道设计
一般RTM工艺的流道设计都从中心注入,从周边排出。但LRTM工艺通常从周边流入,从中心排出。我们知道,当树脂从树脂管道进入模腔后,与织物相遇,织物对树脂会产生一个阻力。阻力的大小和织物的渗透率、树脂的粘度以及树脂的流速有关,当织物和树脂选定的情况下,则和树脂的流速成正比。以一个面积为3平米、厚度为
流道设计随产品而异,如Spectrayte公司的
5、产品精度、结构及其它
RTM和LRTM产品的尺寸粘度和重复性都受模压用树脂、工艺控制和产品固化情况的影响。产品截面精度还受工艺中树脂流动速率和注射压力的影响。对于RTM工艺当模具按标准制造,不发生弯曲,合适的夹紧装置或用压机夹紧,则部件的尺寸精度重复性很好,厚度偏差不大于0.OlOmm。而LRTM工艺通常上模有一定的变形,但产品尺寸精度也可以达到士
RTM和LRTM工艺都可压制夹芯材料。芯材可采用轻木和泡沫。但RTM工艺有高的注射压力,限制了低密度泡沫材料的使用,泡沫最低密度不小于80千克/立方米,而LRTM和ZIP RTM工艺的压力较低,他所用的泡沫密度可小到37千克/立方米。但要指出的是在制造夹芯材料时,芯材的尺寸精确性要满足模具要求,以保证模压工艺和产品质量的重复性。
RTM和LRTM工艺也可以使用预制件和嵌件,当使用预制件时可得到高纤维体积含量的产品。LRTM工艺产品可以不上胶衣,只要一般的脱模蜡,产品就可脱模。但RTM产品如不用胶衣,脱模较为困难。
和开模工艺相比LRTM的投资还是相对较高,必须考虑产量对于配置模具必需的成本的合理性。此外,工艺的专业性强,日常维护任务重也影响一些手工铺层的复合材料制造商对LRTM的使用。
相对于RTM来说,LRTM拥有耗能低,对模具的刚性等指标要求不是太高等的优点,但是对树脂的黏度,树脂和增强材料的相容性,还有对树脂前锋的前进速度的要求很高。
LRTM工艺是一个专业性较强的工艺,操作人员必须经过适当的培训。如果没有合理的纤维铺层、好的气密性和精确的模具安装,没有一致的树脂流道控制,产品就会出现杂乱的干斑,径向气泡,以及树脂富集等问题。下面对相关问题作简要解说:
轻型RTM工艺中要注意的问题
LRTM工艺是一个专业性较强的工艺,操作人员必须经过适当的培训。如果没有合理的纤维铺层、好的气密性和精确的模具安装,没有一致的树脂流道控制,产品就会出现杂乱的干斑,径向气泡,以及树脂富集等问题。下面对相关问题作简要解说。
1、密封性
RTM一Ligh工艺对细节性问题要求较高,特别是模具的密封性问题。周边夹紧用的真空槽的真空度越低越好。内腔的真空度一般控制在
在模塑的过程中,除了要注意模具真空密封胶的密封性,还要注意到模具的装配、密封圈和管子的连接、以及模具的裂口等造成的泄漏。事实上,任何密封口或者是树脂入口处的接头,包括真空区的出口都应该严格的检查。一个更为隐蔽的漏气原因是,在模具面板的表面有裂纹,这些原因通常不被发现。这种问题的解决方法是,在模具内部未达到真空以前,用催化剂调制过的树脂涂抹在模具的外表面,这是一种很有效的方法。
此外密封面要保持清洁,尽量不用溶剂清洗。脱模剂最好选择免清洗的半永久性脱模剂。
2、上下模的精密配合
上下模的精密配合有助于模内空腔的压力平衡,使树脂渗透均匀,有助于产品质量的提高。由于上模是半刚性模,每次合模必须仔细校正。
如果在产品同一位置连续地出现白斑,这可能是因为模具闭合的不准确,造成内腔的不准确性,这直接导致了内腔厚度的不均匀。在这种情况下,假设玻璃纤维的铺层是均匀的,注射过程中树脂的流动会具有选择性,它会选择厚度(间隙)比较大的地方,所以在内腔比较薄的区域就会导致白斑的出现。
较差的模具定位是造成模具配合不好的重要原因。当模具的边销安装好之后,模具的X轴和Y轴就自然而然地确定下来了。如果边销的定位不当,就会造成不可预测的错误和改变注射的特性。
3、合理的铺层和原材料选择
由于成型压力低LRTM工艺对织物的铺层要求更为严格,不合理的铺层,尤其是搭接头的处理,会严重影响树脂流道的一致性,从而造成产品的树脂富集或缺胶(干斑)现象等。
在铺层时可籍助喷胶固定织物,使铺层更为平整。但喷胶必须和所用树脂相溶性好,过多的喷胶对产品最终性能还是有一定影响。
不同的织物和毡对工艺有很大的影响,要尽量使用渗透率好的增强材料,现在的O.c.闭模毡或“Hi一Flow”复合毡的树脂流速可比通常的短切毡快一倍。应根据产品要求的不同选择合适的树脂体系。尽量使用低粘度、低收缩率的树脂。其标准和真空树脂扩散工艺的要求相当。
4、表面裂纹
产品表面的裂纹,会经常在角边区域观察到。这是一个在树脂富集区常见的问题。这也可以追溯到模具的制造上去。如果两个半模不能很好地彼此配合,就会产生一个超过预期厚度的余量。为解决这个问题,除了可修正半模之外,还可以在这些较厚的地方通过增加额外的玻璃纤维来弥补厚度,以防止产品的裂纹。
在大面积的平面区,会发现由于产品过厚而产生的模具上的裂纹。这是由于操作者任意加大树脂的注射速度造成的。注射的速度过快,就会使得模具的内腔膨胀,如果注射过程在一个很短的时间内完成的话,那么腔体就没有时间来恢复,所以过多的树脂就会导致模具的裂纹。在极端的情况下,会产生不可修复的模具表面的裂纹。
5、树脂的溢出
为了接收在模塑结束之前排出的树脂,许多制造者感到有必要用一个较大的树脂收集器。这是他们不能精确控制模塑填充的结果。如果树脂充填过程进行得太快,就难以正确判断什么时间停止注射。因为如果当你看到树脂到达树脂收集器后再停止注射,那么接着你会看到过多的树脂会因为过度膨胀的模具恢复到原来的尺寸而流进树脂收集器。为了克服这种可能,你只能更换一个较大的树脂收集器来防止树脂的溢出。
解决这个问题的简单方法是,预先计算要用多少树脂。但是在模塑大件制品时,很难准确地知道要用多少的树脂。另外的方法是通过精确的气压控制来为操作者提供信息,以避免操作者的盲目判断。腔内的气压读数,为操作带来了更为准确的模具填充信息,避免了较大树脂接收器的需要。这样的一个系统,保证每次注射过程后有10到100毫升的余量已足够,这使得树脂的浪费达到最低,保证了利润的增加。
轻型RTM的应用领域
目前常见的应用领域,有航空航天、军事、交通、建筑、船舶和能源等不一而足。例如:航空航天领域的舱门、风扇叶片、机头雷达罩、飞机引擎罩等:军事领域的鱼雷壳体、油箱、发射管等;交通领域的轻轨车门、公共汽车侧面板、汽车底盘、保险杠、卡车顶部挡板等;建筑领域的路灯的管状灯杆、风能发电机机罩、装饰用门、椅子和桌子、头盔等;船舶领域的小型划艇船体、上层甲板等