拉挤是指玻璃纤维等增强材料在外力牵引下,经过浸胶、挤压成型、加热固化、定长切割等一系列工序,连续生产复合材料线型制品的一种方法。增强材料从纱架引出后,经过排纱器进入浸胶槽,浸透树脂胶液后,进入预成型模,将多余树脂和气泡排出,最后进入成型模凝胶、固化。固化后的制品由牵引机连续不断地从模具拔出,由切断机定长切断。它区别于其他成型工艺的地方是需要外力牵引和挤压模塑,故称拉挤成型工艺。

拉挤成型工艺流程如下:
增强材料(纤维及毡材等)排布→浸胶→预成型→挤压模塑及固化→牵引→切割→制品
在拉挤工艺中有六个关键因素:①增强材料传送系统,如纱架、过纱装置、毡架以及输送装置;②树脂浸渍系统;③预成型系统;④模具;⑤牵引装置;⑥切割装置。
纤维的引出方式有两种:内抽和外引。纤维从纱筒内壁抽出时,纱筒固定但纤维发生扭转,产生打捻;纤维从纱筒外壁引出时,可避免扭转现象,但应采用旋转芯轴,减少引出阻力,以及更好地控制纤维张力。
纤维和毡等增强材料的浸渍,在装有胶液的胶槽中进行,一般有三种形式:1. 压纱浸渍;2. 直槽浸渍;3. 滚筒浸渍。其中方法1和2最为常用。压纱浸渍方法简单易行,主要通过纱夹、纱孔、压纱杆等工具,将增强材料压入胶槽浸渍,其不足之处在于对增强材料存在一定的磨损,同时影响增强材料的定位和走向。随着拉挤产品结构的日益复杂,直槽浸渍法的应用越来越普遍,通过真空泵系统,实现胶液的不断回流,既保证了增强材料的良好浸渍,也能够使得纤维和毡的排列整齐、流畅,更易于实现预想的排布。
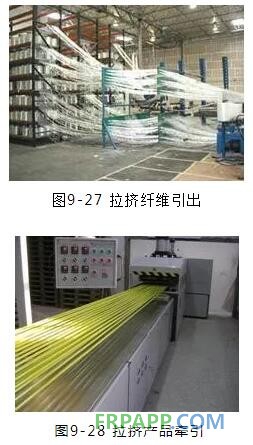

预浸好的增强材料穿过预成型装置,预成型是根据制品所要求的断面形状而配置的导向装置,具有以下作用:①增强材料的定位;②将增强材料按照产品形状预先有序排列;③排出多余的树脂和气泡,然后再进入模具,进行成型固化,从模具拉出。
一般而言,模具是在系统确定的条件下进行设计的。根据树脂固化放热曲线及物料与模具的摩擦性能,将模具分成三个不同的加热区,其温度由胶液体系的性能确定。模具是拉挤成型工艺中最关键的部分,典型模具的长度范围在0.6~1.2m之间。
模具出口与牵引装置之间的距离一般约3~5m,这个距离需确保复合材料制品可以完成固化过程,并逐渐冷却。牵引装置是一个履带型拉出器或两个往复运动夹持装置,可实现连续运动。通过牵引装置的牵引,将制品从拉挤模具中源源不断拉拔出来。
拉挤设备的末端,设置切割机,将拉挤制品按照要求定长切割。
通用拉挤成型设备
通用拉挤成型设备
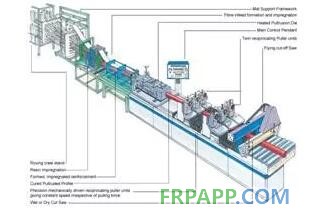
图9-30 典型拉挤设备
拉挤成型设备从五十年代发展至今,已逐步完善并定型,能够最大程度实现计算机智能控制,并伴随拉挤产品和工艺的发展呈现多元化趋势。
拉挤设备尽管型号众多,但每台设备均由以下基本部分构成:(1)增强材料架;(2)预成型导向装置;(3)胶液浸渍装置;(4)带加热控制的金属模具;(5)牵引装置;(6)切割装置。
拉挤设备中,内抽头玻璃纤维粗纱配置在纱架上,其他增强材料(如连续毡、表面毡等)通常按切线方向有序放置在多层搁架上,引出时应尽量遵循平行原则,避免行走时出现交叉、错乱。
从原料架上引出的增强材料经过纱板集束整形后,进入胶液浸渍装置。在直槽浸渍法中,胶液浸渍装置由以下几部分组成:托架、浸渍槽、接胶盘、胶液储存桶、循环泵。浸渍槽前后两面均放置导向板,导向板上按照需要设置纱孔和毡槽,以维持增强材料的有序排列。从纱孔和毡槽中漏出的胶液落到接胶盘中,再收集在储存桶,通过循环泵打到浸渍槽中使用。必要时,还可以设置循环水套管和控制树脂温度的加热器,以优化工艺。
浸渍过的增强材料在经过预成型后,进入模具。根据产品结构的不同,拉挤工艺的预成型体系形式多样而丰富,其主要目的在于,使增强材料按照预先设计的铺层结构,从发散状态自然、流畅地过渡到与产品截面相似,完成最终定位,顺利进入模腔。预成型的制作,多用摩擦阻力较小的塑料板,在其上打孔实现导向。结构复杂产品的纤维定位,也可以搭配定位管,将纤维直接引入模具入口。与纤维的预成型相比,毡材的导向则需要制作者具备更高超的技巧,将毡材从单一的平面状态转变为与模腔伏贴的立体形态,是一件充满挑战和技巧的工作。
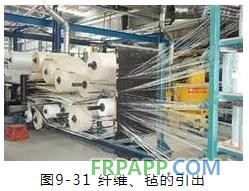
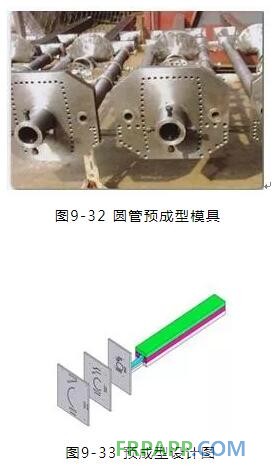
预成型可以通过框架和模具以及模具托台固定在一起,也可以根据增强材料的铺层结构,设置在浸渍区域的上方或下方。空心产品的预成型一般与芯棒托架设计为一体,便于调节同心度,同时节省了操作空间。
浸渍后的增强材料经过预成型后,将顺利进入加热的成型模具。模具通常采用电加热方式,分段加热,模具各区的温度可通过凝胶试验初步确定,并在生产过程中根据产品质量情况进行调整。在生产过程中,设置匹配的模具温度和牵引速度,控制合适的胶凝时间和固化程度,是保证制品质量的关键。生产大型中空制品时,由于芯棒较粗,传热速度较慢,材料在模腔中行进时,内外壁温度会存在较大偏差,从而影响产品固化,可以在芯棒内部安装加热器进行温度补偿,使产品内外受热均匀一致。
刚出模的产品固化度并不能达到理想状态,需要在持续运行中进一步后固化,并在到达牵引装置之前逐渐冷却。处于高速牵引状态中的型材,有时需要使用风机辅助冷却,以减少高温对牵引胶垫的磨损。
常用的牵引系统有两种:上、下履带式牵引系统和交替往复牵引系统。履带式牵引系统由上、下两个对置的不断转动的传动带组成,相对运动的上、下传动带紧紧夹住型材,并拖曳向前。这种牵引系统价格低廉,但通用性略差,对于复杂形状的产品,需要重新加工相应的夹持胶块,包覆在上、下履带上。
交替式往复牵系统克服了履带式的缺点,采用气压或者液压式设计,采用两对夹持胶块的循环往复运动,实现生产的连续。当一对胶块夹持住产品并向前运行时,另一对胶块松开产品,同时后退复位,等待下一次夹持。这种系统便于更换牵引夹具,操作方便,在产品种类较多的情况下,具有广泛的适用性。
位于拉挤机末端的是切割系统,通常采用金刚砂锯片,并配备冷却和润滑,切割时系统与牵引装置同步运动,并由一个定长切割开关控制。液压伺服驱动和程序控制的运用,已使得拉挤设备的自动化程度进一步提升。
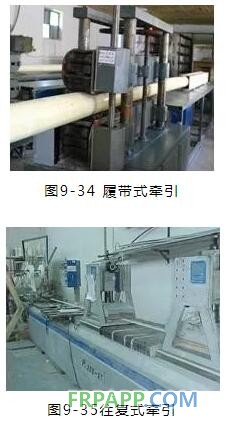
2. 新型拉挤工艺及设备
(1)预热工艺和设备
使用射频(RF)发射器对增强材料进行预热,是拉挤工艺发展的飞跃。这种变革利用射频能量预热与金属模具的热传导相结合,缩短了胶液固化时间,极大地提高了拉挤速度。RF发射器置于浸渍段和模具段之间,湿态的纤维束进入模具前,从发射器中穿过, 并在RF作用下产生瞬时分子磨擦热,降低胶液粘度,增强浸润性,并提供胶液反应所需的能量,在这种情况下,即使缩短模具长度,胶液同样可以凝胶、固化,减少了材料通过模具的时间,降低了牵引拉力。这一重大发明显著地提高了拉挤速度,在大型制品的生产上作用尤为显著。
(2)缠绕拉挤和编织拉挤
为提高拉挤制品的环向性能,在传统工艺中引入缠绕和编织技术元素,形成的拉绕工艺和编织拉挤工艺,使得拉挤制品的性能得到突破,综合性能更加优越。
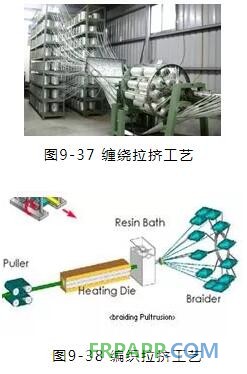
(3)拉挤与注射涂层工艺 一些有特殊要求的拉挤制品,表面需涂覆一层涂层,可设置一台小型注塑机,塑化的塑料液体盛放在一个槽中,从模具拉挤出的型材随即通过塑料液槽,这样就在型材表面涂上了一层涂层,实现外观、性能、耐腐等方面的更高要求。
(4)曲线拉挤设备 曲线拉挤原理是人为控制拉挤制品的固化和后固化过程,使其制品实现所设计的曲线形状。从而突破了传统拉挤只能制造恒截面、直线型产品的思维模式,可以满足变截面产品研发的需求。
3. 拉挤模具
在玻璃钢型材的拉挤成型过程中,模具是各种工艺参数作用的交汇点,是拉挤工艺的核心之一。与塑料挤出成型相比,拉挤成型与其有相似之处,但前者仅是一物理变化过程,后者还伴随着动态的化学反应。相比之下,拉挤模具的工况较前者要复杂得多,所以拉挤模具的设计和制造具有十分重要的意义,它不仅关系着拉挤工艺的成败,决定着拉挤制品的质量和产量,同时也影响拉挤模具的使用寿命。
从工艺角度来讲,拉挤模具一般由预成型模和成型模两部分组成。
(1)预成型模具 在拉挤成型过程中,增强材料浸渍树脂后(或被浸渍的同时),在进入成型模具前,必须经过由一组导纱元件组成的预成型模具,预成型模的作用是使浸渍后的增强材料进一步除去多余的树脂,排除气泡,逐步形成近似成型模腔形状和尺寸,然后进入模具。通过预成型,增强材料逐渐达到所要求的形状,并使增强材料在制品断面的分布符合设计要求。
(2)成型模具 成型模具横截面面积与产品横截面面积之比一般应大于10,以保证模具有足够的强度和刚度,加热后热量分布均匀和稳定。拉挤模具长度是根据成型过程中牵引速度和树脂凝胶固化速度决定,以保证制品拉出时达到脱模固化程度。
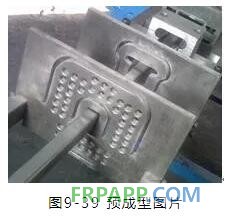
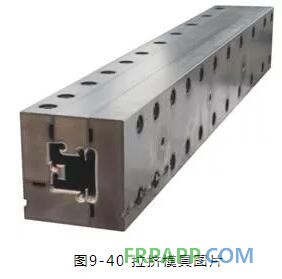
拉挤模具的模腔表面要求光洁、耐磨,以减少拉挤成型时的摩擦阻力,提高模具的使用寿命。模具材料的选择直接影响着拉挤模具的性能,模具材料要求具备以下性能:
1)较高的强度、耐腐蚀性、耐疲劳性和耐磨性;
2)较高的耐热性和较小的热变形性;
3)良好的切削性和表面抛光性能;
4)摩擦系数低,阻力小,尺寸稳定性好;
合金模具钢表面光滑致密,硬度高,易于脱模,清理模具时不易损坏,便于渗氮处理和型腔表面镀硬铬,所以拉挤模具一般选用合金模具钢。经过粗加工后再精加工,表面镀硬铬或者渗氮、渗碳处理,使模腔内表面的硬度达到50~70HRC(洛氏硬度),最后用抛光工具抛光,使型面达到很高的光洁度,表面粗糙度达到0.2um的水平,能够非常好地满足上述要求。这样不仅可减小摩擦系数,延长模具的使用期,而且也会改善对树脂的防粘特性。
经历几十年的发展,美国拉挤工业应用最广泛的模具钢主要是4140、P20和A2等少数几个牌号。国内拉挤模具制作中,使用较多的是40Cr、38CrMoAl、42CrMo、5CrNiMo等调质钢,使用效果较好,但与国外加工水平相比,还存在不小的差距。
表9-1列出上述三种美国用钢的化学成份及热处理后的HRC硬度,供我们进行拉挤模具设计和选材时参考。
表9-1 美国拉挤模具钢的化学成份
portant; overflow-wrap: break-word !important;">
portant; overflow-wrap: break-word !important;">
牌号 |
合金化学组成(%) |
热处理 |
|||||
C |
Si |
Mn |
V |
Cr |
Mo |
||
P20 |
0.35 |
0.50 |
0.80 |
- |
1.70 |
0.45 |
54 |
4140 |
0.40 |
0.25 |
0.90 |
- |
0.90 |
0.21 |
52 |
A2 |
1.00 |
- |
0.60 |
0.25 |
5.25 |
1.10 |
62 |
从整个拉挤工业来看,电镀拉挤模具仍占主导地位,非电镀模具仍处于发展阶段。我国拉挤厂家使用表面渗氮处理的拉挤模具,其氮化层厚度为0.2~0.3mm,HRC≥60。从有限的使用经历来看,腐蚀问题仍存在,摩擦阻力也略大于镀铬模具,还有一段较长的路要走。
(3)拉挤模具的设计
拉挤模具通常由若干个单独制造的模具组件装配而成。组件数及分型面的选择,取决于拉挤制品截面构造、模具加工工艺及使用要求。为保证模具分型面或合模缝所对应的拉挤制品外观质量好,不形成飞刺,在满足模具制造的前提下,尽量减少分型面,保证合缝严密。
玻璃纤维浸胶后进入成型模具时,纤维束是在成型机牵引作用下进入模具的。由于模具进口处纤维束十分松散,往往在入口处积聚缠绕,造成断纤。再者,模具在长时间使用过程中,由于积聚缠绕的影响,往往造成入口磨损严重,影响产品质量。为解决这一问题,在模具入口处周边应倒一椭圆截面圆角,同时入口采用锥形,角度在5~8°为宜,长度在50~100mm为宜,可大大减少断纤现象发生,提高了拉挤制品的质量。如下图所示:
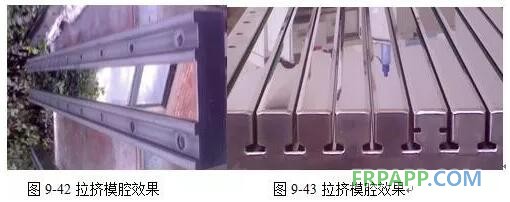
关注本公众号
微信号:cnfrtp
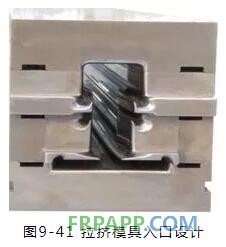
在设计模具时,模具长度的确定要考虑所用原材料和产品截面形状,目前国内模具长度一般设计为900mm—1200mm,模具型腔尺寸决定于制品的尺寸及所选用树脂的收缩率。一般情况下不饱和聚酯产品收缩率为2%—4%,环氧树脂0.5%—2%。对于中空制品,芯棒设计要特别注意,一般芯棒的有效长度为模具长度的2/3~3/4,而在拉挤工艺过程中要考虑到芯棒固定、调整的方便性,此外较大的芯棒还要考虑到配重及加热的问题,以保持水平方向的平衡和受热均匀。综合考虑,对于模具长度为900mm左右的模具,芯棒的长度可设计为 1500mm左右。
(4)拉挤模具的保养与维修
闲置模具通常情况下,需进行清理后,进行必要的防护,避免水、粉尘的腐蚀。芯棒闲置时应挂起,防止由重力引起的形变。
电镀拉挤模具使用一段时间后,可能会发生局部铬层掉落的现象,若面积不大,可通过打磨处理继续使用。打磨处理方法如下:首先选用600目的水砂纸打磨,待打磨到一定程度时,改用较细砂纸。打磨顺序如下:600目→ 800目→1000目→1200目→1500目。打磨过程中,必须不断用航空煤油冲洗模具,把砂纸磨下来的微粒冲掉,以免划伤模具。待水砂纸打磨到1500目以后,改用专用电动抛光机和羊毛抛光盘进行抛光。抛光开始时选用稍粗磨粒的抛光剂,同时羊毛盘选用稍硬一点的,抛2~3次。用煤油冲洗模具,把抛出的微粒冲洗干净,再换用一只稍软的羊毛抛光盘,抛光模具。在抛光过程中,抛光机向一个方向移动,不可停在一处不动,以免模具表面发热,烧坏模具。此过程进行2~3遍,抛光后的模具型腔十分光亮,达到镜面效果,可以继续使用,如下图所示。
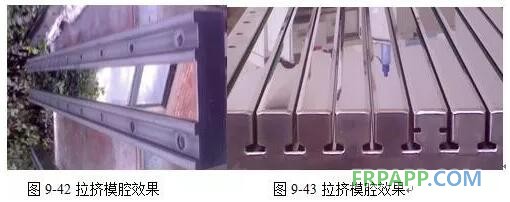
技术·产品·会展·宣传