真空辅助树脂灌注成型工艺(VacuumAssisted Resin Infusion Molding)简称VARIM工艺,是在RTM(Resin Transfer Molding)工艺基础上发展起来的一种高性能、低成本的复合材料成型工艺。自80年代末开发出来,VARIM工艺作为一种新型的液体模塑成型技术(Liquid Composite Molding,简称LCM),得到了航空航天、国防工程、船舶工业、能源工业、基础结构工程等应用领域的广泛重视,并被美国实施的低成本复合材料计划(Composite AffordabilityInitiative,简称CAI)作为一项关键低成本制造技术进行研究和应用。
如图1所示,VARIM工艺的基本原理是在真空负压条件下,利用树脂的流动和渗透实现对密闭模腔内的纤维织物增强材料的浸渍,然后固化成型。
VARIM工艺的基本流程包括:
(a) 准备阶段。包括单面刚性模具的设计和加工、模具表面的清理和涂覆脱模剂、增强材料(纤维织物、预成型件、芯材等)和真空辅助介质(脱模介质、高渗透导流介质、导气介质等)的准备等。
(b) 铺层阶段。在单面刚性模具上依次铺设增强材料、脱模布、剥离层介质、高渗透导流介质、树脂灌注管道、真空导气管道等。
(c) 密封阶段。用密封胶带将增强材料及真空辅助介质密封在弹性真空袋膜内,并抽真空,保证密闭模腔达到预定的真空度。
(d) 灌注阶段。在真空负压下,将树脂胶液通过树脂灌注管道导入到密闭模腔内,并充分浸渍增强材料。
(e) 固化阶段。继续维持较高的真空度,在室温或加热条件下液体树脂发生固化交联反应,得到产品预成型坯。
(f) 后处理阶段。包括清理真空袋膜、导流介质、剥离层介质、脱模布等真空辅助介质和脱模修整等,最终得到制品。
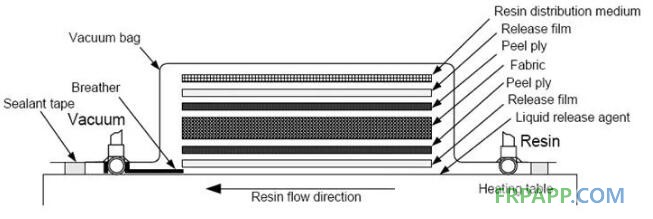
图1 真空辅助模塑成型(VARIM)工艺示意图
和传统的开模成型工艺以及RTM工艺相比,VARIM工艺具有以下优点:
(1)模具成本低。与RTM工艺需要阴、阳双面刚性对模相比,VARIM工艺只需要单面刚性模具;与模压工艺需要承受高温高压的成型模具相比,模具的制造成本较低,适用于设计开发不同结构复杂外形的大型模具。
(2)制品外形可控,尺寸精确。VARIM工艺对制品尺寸和形状的限制较少,可以用于航空航天、国防工程、船舶工业、能源工业、基础结构工程等领域中大厚度、大尺寸结构制件的成型,如火箭外壳、风电叶片、汽车壳体等。
(3)制品力学性能好,重复性高。与手糊构件相比,VARIM工艺成型制品的力学机械性能可以提高1.5倍以上,并且制品的纤维含量高、孔隙率低、结构缺陷少、表面均匀光滑、构件之间一致性高,因此VARIM工艺成型制品的质量稳定,具有很好的可重复性。
(4)环保性好。相比与开模成型时,苯乙烯、丙酮等挥发性有机化合物(VOCs)的挥发量高达35~45 %,了解更多工艺资料登录复材应用技术网,VARIM工艺作为一种闭模成型技术,在树脂灌注和固化过程中,易挥发物和有毒空气污染物均被局限于真空袋膜中,因此几乎不对环境造成污染,是VARIM工艺最突出的一个优点。
(5)生产效率高。处于真空负压下的树脂能够沿着树脂灌注管道迅速导入到密闭模腔内,并在凝胶前充分快速渗透和浸渍增强材料,可整体成型大型复杂几何形状的夹芯和加筋结构件,与开模工艺相比,VARIM工艺可节约劳动力50 %以上。
VARIM工艺的主要原材料
1.1.树脂
适用于VARIM工艺的树脂包括环氧树脂、乙烯基树脂、不饱和聚酯树脂、酚醛树脂等低粘度树脂。VARIM工艺对树脂的要求一般有以下几点:
(a)树脂体系粘度低。一般要求树脂体系粘度在100~800 mPa·s,最佳粘度范围为100~300 mPa·s,从而使树脂在真空负压力作用下能够完全浸渍增强材料。如果树脂粘度过高,充模流动速度慢,并且对纤维织物的浸渍效果也不理想;如果树脂粘度过低,树脂流动速度太快,容易形成干斑等缺陷。
(b)凝胶时间适宜。不同的工艺对凝胶时间有不同的要求,因此凝胶时间应可变易控,具有合适的操作周期,是VARIM工艺专用树脂体系的一项重要指标。一般对于大型制件成型而言,要求树脂体系的低粘度平台时间(即工艺操作窗口)不少于30 min,了解更多工艺资料登录复材应用技术网,以避免树脂在灌注过程就发生剧烈的凝胶反应和固化交联反应。
(c)固化放热峰值适中。高放热峰会降低模具的使用寿命、可能对制品中的芯材、加强筋等部件产生影响。同时,高的放热峰可能引起部件的裂纹,影响制品性能。
(d)其它物理化学性能,包括良好的力学机械性能,以满足工程应用的高要求,抗热氧老化性、耐化学腐蚀性、阻燃性、无毒、成本低等。
1.2.增强材料
增强材料一般包括E玻纤、碳纤维、Kevlar纤维、Spectra纤维以及E玻纤与其它几种纤维的混杂形式。增强材料的可以是短切纤维或纤维织物,但通常采用织物,如无捻粗纱织物、加捻织物、双向缝合织物等,其中新型的针织材料和平纹单向纤维是较理想的选择。
1.3.真空袋膜
耐高温尼龙膜和聚丙烯膜是最常用的真空袋膜,主要利用它们的延展性、柔韧性和抗穿刺性能;同时要求材料具有较高的耐热温度(具体需考虑树脂性能)和优异的阻隔气密性。
1.4.密封胶粘带
密封胶粘带是一种以丁基橡胶为基胶,添加耐温的补强剂和增粘剂等助剂的真空袋膜密封剂,要求材料具有高弹性、表面粘接性以及耐温性等性能,保证在制品成型周期内具有优异的密封性能。
1.5.高渗透介质
高渗透介质的作用是保证树脂在真空灌注过程中能够迅速渗透和流动,大幅度提高充模流动速度,通常可采用尼龙网和机织纤维。
1.6.剥离层介质
剥离层介质的作用是将制品和高渗透介质或真空袋膜分隔开,避免真空辅助介质粘附在制品上。一般选用低孔隙率、低渗透率的薄膜材料作为剥离层介质,如PE、PP多孔膜等。
1.7.轻质芯材
一般芯材都在可选范围内,如轻质木材、PVC、PEI、PMI、SAN、PS泡沫和其它线性微孔封闭型塑料等。对于开孔型芯材(如蜂窝状),树脂会充满其空穴,加重了制品的重量和成本,因此这类芯材不宜选用。
VARIM工艺的常见缺陷及原因分析
2.1.气泡和白斑
如图2所示,在VARIM工艺中,树脂在纤维织物中的渗透流动可以分为宏观流动和微观流动,其中树脂在纤维束空隙之间的流动称为宏观流动,而树脂在纤维束内部纤维单丝之间的流动称为微观流动。如果宏观流动与微观流动的流动速度不同,即两者的流动前缘存在不一致时,树脂就会在纤维织物层内发生横向渗透,从而导致局部“包气”的现象,其中在制件的表面层表现出气泡的产生,而在制件的内部层表现出白斑的产生。
局部“包气”现象的产生是因为树脂的宏观流动和微观流动不一致,其中宏观流动前缘的流速与灌注压力梯度有关,灌注压力梯度越大,宏观流动越快;而微观流动前缘的流速与纤维单丝之间的毛细管作用力有关,毛细管作用力越大,微观流动越快。因此,如图3(a)所示,当灌注压力梯度小于毛细管作用力时,树脂微观流动前缘的流速就会大于宏观流动前缘的流速,此时纤维束内部的树脂发生横向渗透,而将纤维束空隙之间的残余气体包裹,形成大气泡;相反,如图3(b)所示,当灌注压力梯度大于毛细管作用力时,树脂宏观流动前缘的流速就会大于微观流动前缘的流速,此时纤维束之间空隙的树脂就会向纤维束内部发生横向渗透,了解更多工艺资料登录复材应用技术网,而在纤维束内部形成小气泡。为了减少及避免局部“包气”现象的产生,通常需要预先抽真空并在设定的真空度维持一定的时间,从而尽可能的排除密闭模腔内的空气,同时适宜将树脂灌注流道设计成树脂沿着纤维织物垂直(90°)方向流动,而不是如图3和图4所示的树脂沿着纤维织物平行(0°)方向流动。
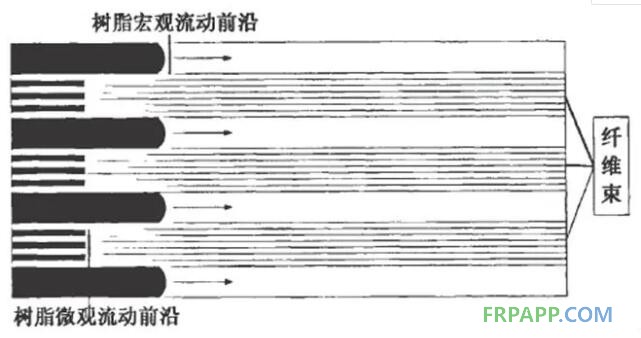
图2 真空辅助模塑成型(VARIM)工艺中,树脂的宏观流动和微观流动示意图[6]
局部“包气”现象的产生是因为树脂的宏观流动和微观流动不一致,其中宏观流动前缘的流速与灌注压力梯度有关,灌注压力梯度越大,宏观流动越快;而微观流动前缘的流速与纤维单丝之间的毛细管作用力有关,毛细管作用力越大,微观流动越快。因此,如图3(a)所示,当灌注压力梯度小于毛细管作用力时,树脂微观流动前缘的流速就会大于宏观流动前缘的流速,此时纤维束内部的树脂发生横向渗透,而将纤维束空隙之间的残余气体包裹,形成大气泡;相反,如图3(b)所示,当灌注压力梯度大于毛细管作用力时,树脂宏观流动前缘的流速就会大于微观流动前缘的流速,此时纤维束之间空隙的树脂就会向纤维束内部发生横向渗透,了解更多工艺资料登录复材应用技术网,而在纤维束内部形成小气泡。为了减少及避免局部“包气”现象的产生,通常需要预先抽真空并在设定的真空度维持一定的时间,从而尽可能的排除密闭模腔内的空气,同时适宜将树脂灌注流道设计成树脂沿着纤维织物垂直(90°)方向流动,而不是如图3和图4所示的树脂沿着纤维织物平行(0°)方向流动。
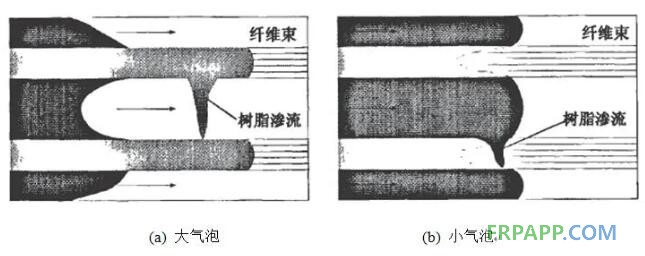
图3 真空辅助模塑成型(VARIM)工艺中,气泡和白斑缺陷形成的示意图[6]
1.1.干斑和干区
在VARIM工艺中,树脂在纤维束之间的流动速度不一致,如果树脂灌注流道或纤维织物铺层设计不合理,就会导致“流道效应”或“短路效应”的发生,树脂在低阻力区域的流动速度将会显著大于高阻力区域的流动速度,高达10~100倍,从而树脂将主要在低阻力区域内发生流动和渗透,使得高阻力区域内的纤维织物不能充分浸渍甚至完全未浸渍,制件在宏观上表现出干斑和干区的不良现象。纤维织物与树脂之间的浸润性匹配不良、纤维织物局部结构松散或过于紧密或扭曲变形、夹心芯材与纤维织物之间的空隙过大等原因都可能会造成制件出现干斑和干区的不良现象。
1.2.褶皱和翘曲
在铺层阶段,如果纤维织物没有铺设紧密和平整,树脂在灌注过程中就有可能挤压甚至冲散纤维束,导致固化后的制件出现褶皱和翘曲的不良现象。此外,树脂发生凝胶反应和固化交联反应时,会具有一定的体积收缩率,并且会释放出大量的反应热,在很大的内应力或热应力下导致松散的纤维织物发生扭曲变形,进而引起制件出现翘曲的现象。为了消除褶皱和翘曲不良现象的发生,要求纤维织物及预成型件的铺设要展放平整,宜选用体积收缩率小、放热量小的树脂体系,并且采用合理的固化制度和散热循环系统。
1.3.过抽和缺胶
在VARIM工艺中,为了维持树脂灌注过程仍具有很高的真空度,确保灌注所需的真空压力梯度以及制品的质量,需要持续地抽真空排出密闭模腔内、纤维束间空隙的残余气体。如果真空通道设置不合理,或树脂灌注管道设置不合理,抽气的同时就容易将大量的低粘度树脂也抽走,从而导致制品出现大面积缺胶,产生过抽的不良现象。
1.4.杂斑和富胶
在铺层阶段,如果在纤维织物层中夹杂团块状物体,将会使局部区域内的纤维织物发生变形,导致树脂胶液出现局部富集,固化后的制件则出现凹凸不平的杂斑。
与缺胶现象相同,富胶现象的产生也主要是由于真空通道和树脂灌注管道铺设不合理所致,这是因为树脂在灌注进口处的压力为大气压,而其流动前缘处的压力几乎为零,这样离真空管口越远(即树脂灌注进口),树脂含量越高,相应的纤维含量越低;了解更多工艺资料登录复材应用技术网,而离真空管口越近(即树脂流动前缘),树脂含量越低,相应的纤维含量越高。因此,真空通道和树脂灌注管道铺设不合理,或者树脂达到出口处时就立即关闭树脂进口和真空系统,就会导致树脂灌注进口区域出现富胶的现象,大尺寸、大厚度制件也将会出现厚度不均的现象。
为了削弱上述的富胶现象,需要合理设置真空通道和树脂灌注管道,并且在树脂达到出口处后,关闭树脂灌注进口,而在不出现过抽的情况下,继续维持抽真空一段时间,使树脂压力稳定地减少,尽量使制件各区域的树脂含量均匀一致。此外,较大厚度的芯材和加强筋边界处也会出现胶液富集的现象,因此需要铺设一些三角形或梯形材料作为过渡,避免富胶现象的产生。
VARIM工艺的应用
VARIM工艺作为一种新型的复合材料成型工艺,始于20世纪80年代末,该工艺一开始并没有受到人们的高度重视,未能实现其潜在的巨大商业价值。直至1996年,由于在船舶上的成功应用,VARIM工艺才在当年的SPI复合材料年会上得到人们的认可和重视。由于VARIM工艺具有成本低、产品质量高、适合制造大型、复杂整体结构制件等诸多优点,因此经过十多年的研究和应用,VARIM工艺已经不再局限于船舶工业的应用,而广泛应用到了很多军用和民用设施的建设上,如军用舰船、导弹舱、雷达罩、风电叶片、桥梁、汽车外壳、冷藏箱等。
航空大型部件
战机座舱:美国洛克希德-马丁公司(Lockheed MartinCorporation)研制的F-35战机首次采用了VARIM工艺制造座舱,成本比热压罐工艺下降了38 %。
大型飞机机翼:在由美国NASA(National Aeronautics and Space Administration)资助的“波音预成型体”计划中,V System Composites公司采用VARIM工艺,研究了机翼结构复合材料及带加强筋机身整体复合材料夹层结构的成型,而波音公司则研究了大型飞机机翼蒙皮的整体成型。
大型舰艇及上层建筑
在船舶工业中,英国VosperThornycroft(VT)公司采用VARIM工艺为英国皇家海军制造了270多艘复合材料扫雷舰,并还制造了运输船、作业艇、救生艇船体和海洋港口工程结构等。North End公司使用VARIM工艺制造了长达27.5 m的船体,并经检验船体层合板的空隙率几乎为零,且力学性能与热压罐低温固化成型的制件相当,但制造成本却大幅度地降低。英国Sandown级扫雷艇采用非磁性材料制造,整个舰艇的所用上层建筑和部分内部结构制件均为VARIM工艺所成型,可以抵抗很强的冲击。美国海军DD21 Zumwalt级隐身驱逐舰和瑞典海军YS2000 Visby级隐身反潜轻型巡洋舰都采用了VARIM工艺成型的泡沫夹芯结构作为舰船壳体。佛山市宝达船舶工程有限公司使用VARIM工艺对含有芳纶纤维的混杂增强材料和乙烯基树脂进行了复合成型,制造生产了13.6 m的海关超高速摩托艇。
大型复合材料风电叶片
近年来,VARIM工艺被广泛应用于大型复合材料风电叶片的整体成型。相比于手糊成型工艺,VARIM工艺生产风电叶片的生产效率大幅度的提高,操作环境显著改善,树脂使用量可减少30 %,并且产品质量稳定,重复性好。丹麦艾尔姆(LM)玻璃纤维制品有限公司采用VARIM工艺开发了长达60 m的风电叶片。
采用VARIM工艺制造叶片,主要可分为以下几步工序:
(1)模具准备:对模具进行清理,并涂覆脱模剂。
(2)铺覆增强材料:根据设计要求,铺覆纤维织物。该工序除了织物的型号、位置以及搭接的尺寸必须满足设计要求外,还要保证铺覆的平整以及清洁。

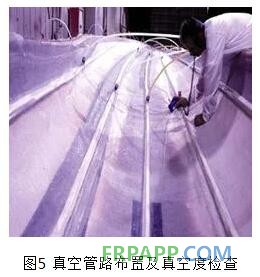
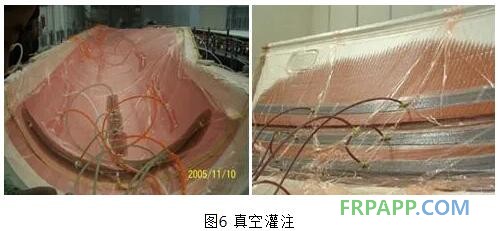
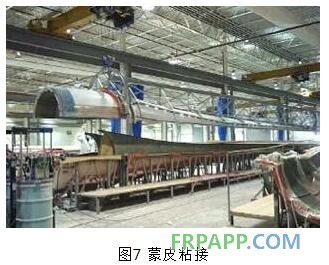

[1] A. Goren, C. Atas.Manufacturing of polymer matrix composites using vacuum assisted resin infusionmolding [J]. Archives of Materials Science and Engineering, 2008, 34(2): 117-120.
[2] 祝颖丹, 李新华, 王继辉, 高国强. 高渗透介质型真空注射成型工艺的研究[J]. 复合材料学报, 2003, 20(4): 136-140.
[3] 李柏松, 王继辉, 邓京兰. 真空辅助RTM成型技术的研究[J]. 玻璃钢/复合材料, 2001, (1): 17-23.
[4] 赵晨辉, 张广成, 张悦周. 真空辅助树脂注射成型(VARI)研究进展[J]. 玻璃钢/复合材料, 2009, (1): 80-84.
[5] Xiudong Sun, Shoujie Li, L. James Lee. Molding fillinganalysis in vacuum assisted resin transfer molding [J]. Polymer Composites, 1998,19(6): 807-817.