喷射成型工艺是利用喷射设备将树脂雾化,并与即时切断的纤维在空间混合后,落在模具面上,然后压实排出气泡,固化成型的一种工艺方法。喷射成型是在手糊的基础上发展起来的,其将手糊操作中的纤维铺覆和浸胶工作由设备来完成,是一种相对效率较高的成型工艺。
一、分类
喷射成型工艺有多种分类方法
按喷射的动力形式可分为气动型和液压型
气动型是由压缩空气从喷嘴高速流出,引射喷出树脂的一种方式,特点是雾化效果好,但飞溅严重,操作环境极差。
液压型是采用常规动力给封闭腔内的树脂施加一定的压力,再经枪口射出,利用喷嘴的特殊结构进行雾化,其特点是减轻了飞溅,改善了操作环境。
2. 按胶液的混合形式可分为预混型、内混型和外混型三种类型
预混型是指树脂液体在加入喷射设备之前就将各组分混合好,再送入设备经喷嘴喷出,其主要特点是设备简单,但需要清洗全部管路,容易出现树脂固化堵塞。
内混型是指将树脂和固化剂等组分在枪头内部的紊流混合器内混合后,经喷嘴喷出,查询更多复材工艺登录复材应用技术网,其特点是没有直接雾化固化剂,环境污染小,但枪头部分仍需要清洗,如有不当,会造成堵塞。
外混型是指树脂和固化剂均单独、同时喷出枪嘴雾化,在雾化空间中混合的一种类型,其特点是:可实现枪头免清洗,但由于固化剂的单独雾化,对环境造成的污染比较严重。
二、 喷射成型工艺的优缺点
喷射成型是由手糊成型发展而来,主要针对手糊工艺中的一些瓶颈问题进行改进,如增强材料的铺覆以及树脂的均匀浸渍等,喷射成型工艺与手糊工艺相比,主要有如下优点:
(1)生产效率是手糊工艺的2-4倍;
(2)利用粗纱代替织物,降低了材料成本;
(3)成型过程中无接缝,制品的整体性好;
(4)可在生产过程中,自由调节产品壁厚、纤维含量及纤维长度等;
(5)可以加入大量的填料,降低成本。
喷射工艺的缺点主要有:
(1)产品纤维含量、厚度均匀程度等很大程度上取决于操作工人的技术水平,可控性较差。
(2)增强材料以短切形式存在,树脂含量较高,产品强度不高;
(3)操作过程中由于需要雾化和分散,原材料的损耗较大;
(4)由于雾化和分散的原因,操作现场环境差;
(5)阴模成型比阳模成型难度大,大型制品比小型制品更适合喷射工艺;
(6) 由于需要设备,初期投资比手糊方法要大。
喷射工艺的材料及模具
一、原材料的选择
合理的选择原材料是保证产品质量,降低产品成本的重要环节,原材料的选取一般要满足以下要求:产品要求的各种性能指标;适应喷射成型的工艺特性;价格低,货源充足等。
1.符合喷射成型工艺的树脂
用于喷射成型的树脂,一般要满足以下条件:
(1)黏度 对于喷射成型工艺,要求树脂易于喷射并易于雾化,这样才能更好的浸润玻璃纤维,还可以加入更多的填料,以降低产品成本。如树脂黏度过大,喷出、雾化、浸润都可能出现问题。一般可选用黏度为0.3-0.8Pa·s之间的原料树脂。
(2)触变性 触变性是喷射成型树脂最重要的特点,因为在针对大型或有垂直面的模具进行操作时,树脂很容易流动,造成较高位置出现干纱,如果采用黏度更大的树脂或增加填料用量,一是不易浸渍纤维,二是辊压时排泡困难,无法进行,所以树脂的触变性显得尤为重要,其作用是尽量保证树脂留在所喷落的位置不流动。喷射工艺中树脂的触变性一般控制在1.5~4。
(3)固化特性 喷射操作需要一定的时间,而且产品的大小形状的不同,操作时间也会有差异,这就需要所用树脂有较适宜的固化特性和可控性。
(4)浸渍脱泡性 要求树脂对纤维的浸润性要好,经过辊压浸渍,气泡容易排出。
目前用于喷射成型的树脂体系主要为不饱和聚酯树脂和乙烯基酯树脂,大部分产品均采用室温固化体系,为进一步提高生产效率,也有采用80℃以下中温固化体系材料。
2.符合喷射成型工艺的纤维
从成型工艺角度考虑,纤维应满足以下基本条件:
(1)硬挺度适当,切割性良好;
(2)不易产生静电,分散性好;
(3)浸渍性好,浸渍速度快;
喷射成型工艺中采用的增强材料是玻纤粗纱,为防止其快速运动和磨擦中产生静电,常用的表面处理剂以沃兰为主,现在又开发了切割性较好的硅烷系处理剂。
纤维分散性好是保证喷射制品厚度及均匀性的重要因素,同时也能使之与树脂的混合更充分,从而使喷射在立面上的纤维不易脱落。也能够加速浸润过程。
二、喷射成型用模具
模具是喷射成型中必不可少的依托工装。喷射工艺中合理的模具设计同样是质量和成本的重要决定因素之一,在模具设计中,需要考虑的主要有以下因素。
(1)符合产品设计的精度要求;
(2)有足够的强度和刚度,能够承受生产过程中接触的外力作用;
(3)脱模性良好;
(4)对产品的收缩放量有充分的考虑,喷射产品的树脂含量一般较高,成型后的制品收缩率也相对较大,在模具设计中,特别是阴模成型时,要充分考虑材料收缩将会给产品尺寸带来的影响;
(5)模具的圆角设计,在产品允许的范围内,模具的圆角设计得越大,越有利于喷射成型;
喷射成型的设备及辅助工具
喷射成型设备,从简单的喷射成型机到自动化的喷射成型生产线,经历了一个较长的发展过程。喷射成型工艺所用的主要设备是喷射机。国外在60年代已经开始了喷射设备的研制开发工作,目前在用的喷射设备,大部分是欧美国家生产的设备,由于材质技术、加工精度及市场等因素影响,国产喷射机的发展较为缓慢。
喷射机主要由树脂输送系统、树脂喷射系统和无捻粗纱切割系统组成,即输料泵、喷枪和切纱器。其功能是将树脂与固化剂等助剂混合喷出并雾化、将纤维按设定长度切断并分散喷向树脂的雾化扇面上,由树脂夹带纤维落向模具表面,随喷射方向的移动,在模具表面形成一层疏松的纤维、树脂混合物。其中,树脂的喷出速度和纤维的切割速度均单独可调,从而实现产品要求的纤维含量。不同类型的喷射机,其各组分的混合顺序、喷出方式、速度和比例的调整方式可能存在差异,但均可实现上述功能。
下面以应用最为广泛的柱塞式喷射机为例,对喷射机的各系统原理简述如下:
一、树脂输送系统
该系统主要为液体原料提供足够的动力,同时可以实现树脂与固化剂的不同比例设定。实现树脂等组分的输送有多种方式,有压力罐式,有柱塞泵式,有齿轮泵式等,目前应用最多是还是柱塞泵式喷射机。
常用的柱塞泵式喷射机一般只有两个联动的柱塞泵,一个用于泵送树脂液体,另一个作为伺服泵,按设定比例配送固化剂,主要结构如图所示:
portant; overflow-wrap: break-word !important;">从结构可知,这种设备也几乎是专为不饱和聚酯树脂体系设计的,其固化剂的配比范围为0.5-4%,适合不饱和聚酯树脂体系,生产过程中,如果还需要加入第三种以上组分,则只能将其它组分预先加入到树脂中并搅拌均匀后,才能接入喷射机。 portant; overflow-wrap: break-word !important;">树脂的输送量由往复气缸的运行速度决定,而这一速度也是由气源的压力和流量决定的,通常情况下,我们控制树脂的流量都是通过调整马达的供给气压得以实现。而且最终的树脂流量还与树脂本身的黏度等有关,实际生产中一般在调整好设备参数后,都要先在容器中试喷一些树脂,通过称量来确定喷射的流量或速度。 portant; overflow-wrap: break-word !important;">稳定的固化剂比例是树脂输送系统的最关键指标,伺服泵是一种经计算的机械联动泵,理论上可以绝对保证固化剂的配比,结构简单,成本低,所以被广泛使用,但由于柱塞泵的结构限制,在泵速过慢或有一定程度磨损,查询更多复材工艺登录复材应用技术网,或有脏污时会有内部泄漏的情况发生,造成固化剂的比例不足,所以使用时还要格外注意随时检查。为了解决这个问题,也有先进一点的设备,在固化剂的管路中增加流量监测及报警装置。 portant; overflow-wrap: break-word !important;">柱塞泵是往复泵的一种,往复泵的特点是在往复行程顶点处有短暂的停顿,所以其输送的液体也会随之出现脉动现象,新式的喷射机采用在输出管路中增加一个缓冲罐的方式,来减弱脉动现象,效果不错。另外,由于树脂和固化剂是机械式联动机构,所以脉动也是完全同步的,这对固化剂比例基本无影响,只是影响瞬间的纤维-树脂比例,实际生产中也很难测出这一影响的程度,故此,喷射机的脉动现象对喷射工艺及制品质量的影响比较小。 portant; overflow-wrap: break-word !important;">压力罐式的喷射机,有单罐式,有双罐式。单罐式的很简单,就是一次性将树脂所有组分都混合好后,再加入到压力罐中,加压,使之通过管路输送到枪头。双罐式是指把树脂和固化剂分别置入两个压力罐,加压输送,利用压力的大小及流通口径的大小来控制比例,这是一种非常不稳定的控制方法,目前这种设备应用已经很少见到。 portant; overflow-wrap: break-word !important;">齿轮泵式喷射机,这是目前较新形式的机种,这种泵输送压力大,不易发生内泄漏,可定量输送,设备维护次数大大减少,各方面性能较之柱塞泵,均有不同程度的提高,价格偏高。
二、树脂混合及喷射系统
portant; overflow-wrap: break-word !important;">除预混型压力罐式喷射机外,其它机型基本都是将树脂胶液和固化剂两组分同时输送到枪头,内混型枪头是使两组分在喷出枪头之前进行混合,主要由一个静态混合器来实现;外混型枪头是两组分均单独喷出枪头,喷出后以雾状相互交织碰撞,实现混合。两种枪头各有优缺点,对比如下: portant; overflow-wrap: break-word !important;">表3-1 内混和外混设备性能比较 portant; overflow-wrap: break-word !important;">
portant; overflow-wrap: break-word !important;">树脂的喷出一般都是由不同型号的喷嘴来实现的,可根据要求,选用不同流量、不同角度的喷嘴。 portant; overflow-wrap: break-word !important;">三、无捻粗纱切割喷射系统 这里主要介绍玻璃纤维切纱器,喷射机上用的切纱器是一种专用的切纱器,体积小巧,可以固定在喷射枪头上,随枪头运动,其功能主要是将无捻粗纱切成0.5-2英吋长的短切纤维,然后分散喷出与雾状树脂碰撞混合,再落到模具表面形成积层。
切纱器上可调的参数主要有两个,一是切纱速度,二是短切纱的长短。切纱速度主要由调节气动马达的转速来控制;纤维的长短主要由刀片的安装间距来决定,常用的短切纱长度为1英吋,过短时制品强度下降幅度较大,过长时,不易切割和分散,故障率会明显增加,浸润困难,生产效率也会受到影响。 切纱器使用中,与刀轮对应的支撑辊会发生磨损,需要定期检查调校或更换,切纱速度主要由气马达的转速决定,一般在更换设备、更换原材料、更改要求指标时,都要在调好转速后,用容器分别接盛树脂和纤维,同时喷射,然后通过称重来确认纤维含量,再开始喷射产品。
四、其它辅助工具 在玻璃钢喷射成型工艺中,除毛刷、剪刀有所用处外,广泛的经常使用的手工工具是压辊。压辊的种类很多,就材质来讲,有塑料压辊和金属压辊之分,按结构和形状又有圆柱状,圆盘异形及柔性与刚性之分。一般压辊沿轴线设有轴孔,和手柄连在一起的辊轴即穿在轴孔中。柔性压辊有塑料制成的和钢丝缠制的螺旋形的,柔性压辊用于玻璃钢喷射成型制品的异形曲面,圆柱形压辊用于产品的平面和柱状面,其它异形压辊主要用于产品的沟槽、圆角等处的成型,压辊的作用是将喷射后蓬松的积层压实,排出其中的气泡,压辊的凸出部分在滚轧纤维的同时,其沟槽结构可以顺利的导出气泡,并且在树脂偏多的地方,沟槽内还可以蓄积一定量的树脂,在辊压其它树脂少的地方时,会自动释放以浸渍纤维,故而在一定程度上起到调节含胶量的作用。 总之,喷射成型工艺是一种借助于机械的手工成型工艺,喷射机及辅助工具固然对制品质量会有一定影响,与其它成型工艺相比,喷射操作工的技术素质和认真的态度对制品质量的影响会更大一些。
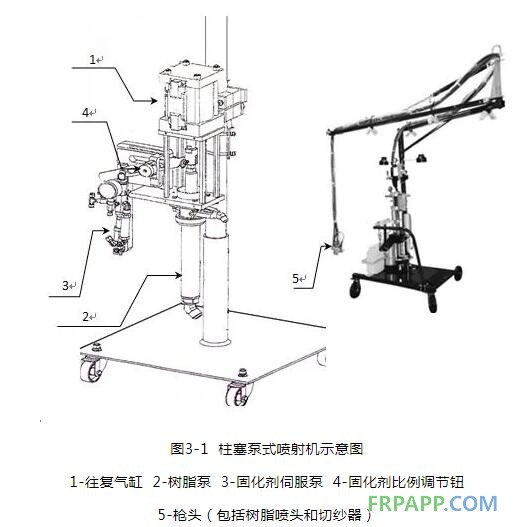
二、树脂混合及喷射系统
portant; overflow-wrap: break-word !important;">
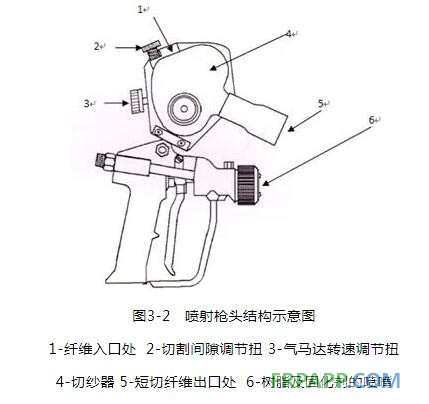
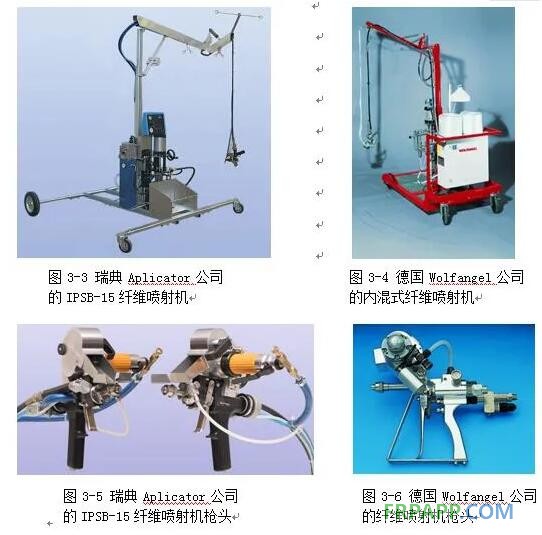
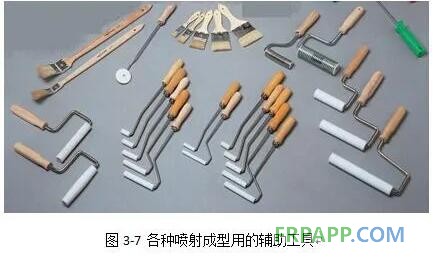