喷射成型工艺(二)

发布日期:2020-03-24 来源:复材应用技术网 浏览次数:
1237
核心提示:喷射成型工艺流程和工艺参数1、喷射成型工艺流程喷射成型工艺流程如图所示:2、喷射工艺参数 在喷射成型时,大部分工艺参数都是
喷射成型工艺流程和工艺参数喷射成型工艺流程如图所示:
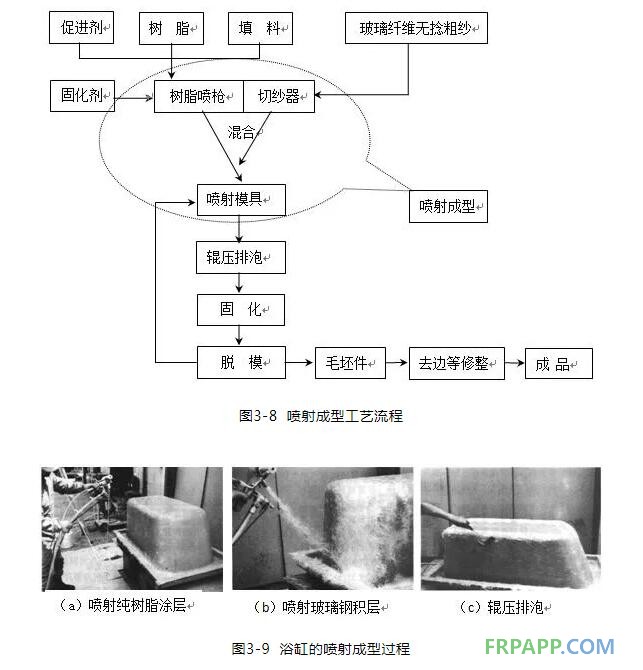
在喷射成型时,大部分工艺参数都是对通过操作设备来控制的,所以,选用不同类型或不同型号的喷射机,其控制参数的操作会有不同,实际生产中,要结合设备自身的参数,制定该设备专用的操作说明书,标明控制点及控制范围。以气动柱塞外混喷射机为例,喷射成型操作时需要控制的,或可以调整的参数主要有以下几项: (1)引发剂比例 喷射系统中,促进剂用量一般是固定的,引发剂用量可根据环境(温度和湿度)和制品的要求在0.5%~4%之间调整,故每次喷射前应作凝胶试验。在喷射装置中,一般先将树脂与促进剂按固定比例充分混合,也可从厂家直接购进预促型树脂,然后将树脂与引发剂分别通过树脂泵和引发剂泵在喷枪内部或外部混合。 (2)树脂泵压力 树脂泵压力主要根据树脂温度、黏度、喷涂面积等因素选择,通常通过试验确定。压缩空气管径和管长对出口压力也有较大影响。当压力合适时,喷在模具上的树脂无飞溅、夹带的空气少,气泡能在1~2分钟内自行消失,表明喷涂面宽度适中,故可以此作为调节压力的标准。 (3)喷射量 喷射量太大,影响制品质量,喷射量太小又降低生产效率,因此应控制适中。喷射量与喷射压力和喷嘴直径有关,改变动力源压力可以调节喷射压力。喷嘴直径在1.2~3.5mm之间选择,可使喷射量速度在8~60克/秒之间调整。 (4)喷枪夹角 预加速树脂和引发剂在喷枪外的混合程度与喷枪出口的夹角有关。不同夹角喷射出来的树脂混合交距不同,一般喷枪夹角为20度,喷枪口与模具表面距离为350~400mm,这样便于操作,胶液混合的质量均匀。如果要改变喷射距离,则需调整喷射夹角以保证树脂在到达成型面前交集混合。确定喷射距离时,要考虑制品的形状和胶液飞散等因素。 (5)纤维与树脂的混合 被切断的纤维在落到模具之前应与喷出的树脂系统充分混合以防止制品中纤维和树脂分布不均匀。 (6)喷射走向 一般的喷射走向是从上到下、从右到左、平行、匀速地移动,不能走弧线。相邻的两个行程间的重叠宽度为前一个行程宽度的三分之一以便得到一个均匀连续的纤维层。前一层与后—层的走向应交叉或垂直以达到均匀覆盖的目的。喷枪与喷涂面的夹角最好为90度。 (7)纤维品种、含量与长度 喷射用无捻粗纱在制品中的含量(质量分数)通常控制在30%左右。低于25%辊压方便,但制品强度太低;纤维含量高于45%时辊压困难,气泡也较多。纤维长度以25mm为宜(1英吋)。 通过设备参数的调整,最终实现对喷射速度、混合效果、纤维含量的控制;通过操作工人的操作,实现产品厚度的均匀性、可控性和对复杂产品的工艺适应性。如果刚刚接触喷射成型操作,相关参数设定及其效果判断还不熟练时,要放慢速度,仔细摸索其中规律,喷射工艺总体来说对操作人员的依赖还是十分明显的,熟练的喷射工可以凭经验调整各种参数,并以浸渍状态判断纤维含量,最终成型高质量的喷射产品。即使是同一产品,对于不同局部的厚度、纤维含量等的要求也可能存在区别,机械地调整各参数只能符合一般性要求,具体情况还需要具体分析对待,久而久之,才能熟练掌握喷射成型工艺。 (1)成型环境温度 喷射成型宜在20℃~35℃之间进行,高温环境中,树脂固化过快,不好控制,影响制品质量;温度过低时,胶液黏度骤增,浸渍困难,固化慢。 (2)制品喷射成型工序要尽量标准化,以免人为因素产生过大的质量差异。 (3)为避免压力波动,造成喷射量不稳定,喷射机应由独立管路供气,气体要彻底除湿,以免影响固化。 (4)盛装胶液的容器最好有加热保温功能,以保证胶液的黏度适宜。 (5)喷射开始时,应注意纤维和树脂的喷出量,调整气压,以达到规定的纤维含量。 (6)纤维切割不准时,要调整切纱器的辊间距,并调整气压。必要时,需用转速表重新校验切纱转速。 (7)喷射成型时,在模具表面先喷涂一层树脂,然后再开动切纱器,喷射最初和最后层时,应尽量薄些,以获得光滑的表面。 (8)喷枪移动速度要均匀,不允许漏喷,不能走弧线,相邻两个行程间重叠宽度应为单行程的三分之一,以得到均匀连续的涂层,每层涂层的走向应交叉或垂直以使均匀覆盖。 (9)每个喷射面喷完后,立即用压辊辊压,要特别注意凹凸表面,排出气泡后再喷下一层。 (10)特殊部位的喷射,喷射制品曲面时,喷射方向应始终沿曲面的法线方向;喷射沟槽时,应先喷四周和侧面,然后再在底部补喷适量纤维,防止底部的树脂含量过高;喷射转角时,应从夹角部位向外喷射,防止在尖角处出现胶集聚。喷射成型制品存在的问题是离散系数大,其分散性比手糊成型工艺还高(见下表),且喷射成型工艺对每个操作者的操作技能要求比较高,这就要求在进行 (1)在进行结构设计前,先进行工艺参数的确定,以确保产品达到设计要求; (2)根据所定工艺参数,制作喷射样板,并进行各项性能测试,测试数据为结构设计的重要依据; (3)在主要受力部位,可采用喷射短切纱与方格布结合使用的方法,来提高材料的机械性能,满足制品的使用条件。
1、流挂现象(垂流)
|
|
|
提高树脂的黏度和触变指数(厚度大于5mm时效果不大),提高树脂喷出的压力 |
|
|
|
|
4、固化不足及固化不匀
|
|
|
调整 固化剂喷嘴,使用稀释的固化剂,增加喷出量,使控制更精确 |
|
|
|
|
|
|
5、粗纱切割不良
|
|
|
|
|
|
|
|
|
提升动力,特别是使用压缩空气动力时,除保证一定压力外,还要注意气源的流量问题 |
|
|
|
|
|
|
|
模具的颜色应与产品树脂的颜色差别尽量大些,以便更易观察脱泡程度和浸渍情况 |
|
|
7、玻璃纤维堆积
产生的原因
|
解决措施
|
树脂黏度太大
|
保证树脂黏度,触变性,浸渍性及固化特性
|
粗纱粘接剂太软
|
选择更硬的粘接剂
|
喷出的纤维量不匀
|
使树脂和纤维的喷射速度一致,均匀喷射
|
8、厚度不匀
|
|
|
制定成型面与喷射枪的距离,喷射方向,树脂和纤维的粘接剂的一致性等操作标准,并通过训练以提高熟练程度 |
|
|
|
根据产品的复杂程度及产品设计的积层,选择合适的树脂固化时间 |
|
|
9、白化及龟裂
|
|
|
|
纤维表面附有防碍树脂浸润的不均匀性表面处理剂如水,油,润滑酯等 |
|
|
|
|
|
|
|
|
|
|
|
喷射工艺存在的最大问题是分散性大,为降低分散性,必须使材料、技术、设备维护、工艺管理制度化,标准化。 (2)操作标准 喷射参数及喷射方法、脱泡方法、缺陷的解决方法。 (3)工程管理项目 树脂温度、模具、喷射时树脂与纤维比例,喷射量,重量、固化温度、模具温度、产品固化后的硬度。 (4)设备管理项目 喷射成型化、泵、空气压缩机、固化炉、输送管道。 为了确保生产出质量满足要求的制品,必须实施经过充分研究的管理系统,确定的生产管理。而产品的检验是这个生产管理中十分重要的一项。产品检验大致分为:常规检验和性能检验。 (1)目测 依靠肉眼对中间产品及成品的内、外表面进行观测,看是否有缺陷和伤痕等。检验时要特别注意涉及增强材料的损伤、纤维分布不均,裂纹,浸渍不良,污垢等 (2)重量检验 由制品的重量来检验材料用量。重量在规定范围以外,视为不合格。 (3)厚度检验 作为制品的检验内容,除重量外还要检验厚度,厚度可以使用螺旋测微仪或者测厚卡钳等工具。 (4)其他 常规检验的其它项目有尺寸检查,功能检查,结构检查等。 性能检验的主要项目有:结构部件及重要组成部分的强度检验(拉伸强度、拉伸弹性模量、弯曲强度、弯曲弹性模量、硬度、耐腐蚀性等),还有对制品整体的强度试验。各项检测的控制指标,对于不同的产品来讲有不同的要求,检测时可根据相关的标准进行产品质量的评定。 目前,喷射成型工艺主要应用于大型玻璃纤维增强聚酯树脂产品的制造,建筑物补强等领域,代表性产品如浴缸、整体卫生间、卡车导流罩、高顶、净化槽、船身、机罩及容器与管道的内衬层等等。
随着复合材料工业的迅速发展,成型设备及原材料体系都不断得到改进行和完善,喷射工艺也是如此。 原材料方面,有一种美国开发的hyrizon树脂是聚酯树脂与异氰酸树脂共混得体系用于喷射成型,其特点是纤维伏倒性好,几乎不需要除泡操作,大大提高了生产效率,且其固化后的玻璃钢性能也好于聚酯树脂。该树脂使用前是双组分,A组分是异氰酸酯与苯乙烯的混合物,B组分是聚酯树脂与酯化反应催化剂的混合物,当喷射成型时在喷枪处混合,聚酯树脂与苯乙烯混合后发生交联反应,异氰酸酯与酯化反应催化剂混合发生酯化反应,两种反应产物相互纠缠到一起形成复合高分子物 ,固化物兼有聚酯树脂的强度和刚度及聚异氰酸氨酯的韧性,耐水性,耐腐蚀性也优异。 设备方面,美国格拉斯公司推出的第三代外混型喷射机,其特点是维修简便,无需清洗,不易阻塞,提高了物料的利用率。其外混喷枪的特点是:实现了固化剂和树脂的完全均匀混合,混效果好过内混型设备,同时该喷枪还增加了空气助流包容技术,在喷射出的物料周围形成一道“气幕”,有效降低的物料的飞散,较其它设备,既能更好的改善工作环境,提高产品质量,并且由于减少了飞散,提高了材料的利用率,降低了产品成本。 瑞典Aplicator公司制造了采用工业机器人进行喷射生产的设备,采用连续供料系统,由机械手携带喷枪进行喷射操作,所有相关参数均数字化并可进行预先设定,编程控制,这一自动化的改进,把操作人员从恶劣的环境中解脱出来,同时操作的稳定性、均匀性、产品重现性均大大优于人工操作,解决了喷射工艺离散性大的问题。
[ 工艺技术搜索 ]
[ 加入收藏 ]
[ 告诉好友 ]
[ 打印本文 ]
[ 违规举报 ]
[ 关闭窗口 ]