无论我国或国外,波纹板成型工艺流程及工艺原理大致相同,仅设备机构和某些工艺措施存在差异。根据制品的波纹方向相对于成型过程中制品前进的方向,FRP波纹板成型工艺分为横波成型和纵波成型两种,其工艺流程如图10-2。
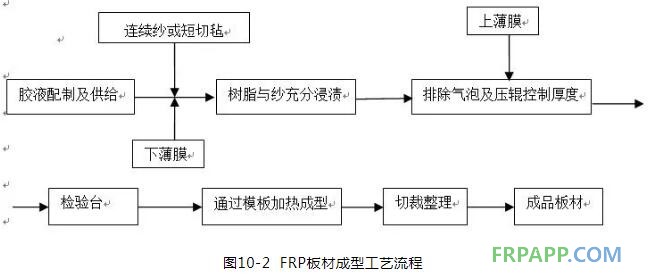
由于横向成型设备国内没有,国外也很少,实用性不大,这里就不做介绍。
二、FRP板材连续成型机组
FRP连续成型机组示意图如图10-3所示。
以此类推,一般连续生产的FRP板材厚度不超过4mm,如有特殊需要或特殊板型以上用短切玻璃毡的组合可以做适当调整。
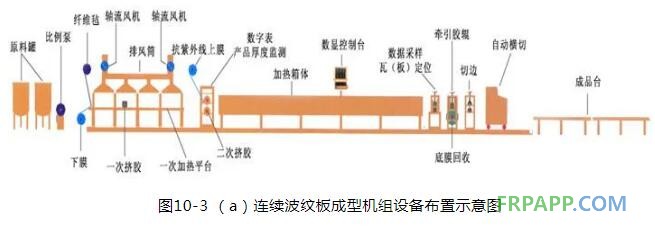
设备原理及生产过程:
(1)自动配料和树脂浸渍
树脂、促进剂及固化剂通过比例泵,被准确计量后进入混合器。均匀混合后的树脂落在张紧的下层薄膜上,经过专门机构形成树脂层。树脂的施放数量由可调的刮刀进行控制。连续纤维经过切刀被切割成定长的纤维均匀洒落到树脂层上(或者短切纤维毡铺放到树脂层上),查看更多复材工艺文章登录复材应用技术网,进行浸胶,并通过一个加热区加速浸渍速度。上部再放一层防老化膜,这样上下薄膜间的玻璃纤维与树脂层组成一个夹层带,通过后面的辊压机构排除汽泡并确定产品厚度,其厚度可以通过调节装置精确调节。
(2)胶凝、成型与固化
夹层带通过不同的模板逐步形成要求的波形,然后进入固化炉,来自热交换器的热空气和夹层带自身固化放出的热量,使夹层带固化定型。
(3)薄膜卷取
离开加热炉后的波纹板在空气中冷却,下薄膜可以揭开并反卷,以备处理。
(4)玻璃钢板材切割
固化了的波纹板经过牵引机牵引进入切割装置,首先用可以边锯切成要求的宽度,再由横切锯将产品切成要求的长度。切割时采用水冷却切割锯片并除尘,含有粉尘的水浆经沉淀池深水沉淀后排出。
(5) 设备控制功能
按照生产工艺要求,可调节比例泵,使各种原料按要求的比例自动配比。浸胶台的温度可以自动控制,确保浸渍和排放汽泡充分。炉体温度分三个温度梯度,各区温度分别自动控制,通过调节电加热器、引风机、排风扇,使各区温度能够更好的满足生产要求。按照生产工艺要求,牵引速度可以任意调节。调整切割锯的行走速度,使之与产品主牵引速度相匹配。根据生产要求,切割长度任意。生产线可由自控系统或手动操纵,以保证生产的正常进行。
工艺参数确定及品质控制
FRP波纹板成型过程中,影响制品性能和质量的因素较多,包括树脂胶液配方,增强材料、工艺参数、工艺措施等。
一、树脂胶液配方
1、常温固化配方
FRP板材的树脂胶液的配方是在通用不饱和聚酯树脂的常温固化配方基础上,考虑常温配方但是加热成型等因素,来进行调整。
不饱和聚酯树脂 100份 异辛酸钴(或萘酸钴) 0.1-0.5份
过氧化甲乙酮 2份
如生产二级阻燃板材,因为阻燃剂三氯乙基磷酸酯(TCEP)有阻聚作用,考虑将促进剂异辛酸钴(或)的用量加大(直接使用反应型阻燃树脂除外)。添加阻燃剂是不能达到以及阻燃效果的,应控制添加量不要超过17%,否则板材力学性能和耐候性根本无法保证。
2、高温固化配方:添加TBPB或TBPO,在高温100℃以上开始固化成型。
3、光固化:使用光固化引发剂,紫外线照射引发固化反应。目前生产过程中使用的并不多(一般在胶衣板材的胶衣凝胶部分使用),但也是一个发展方向。
二、树脂用量及控制方法
FRP板材树脂投料量的控制是通过调节上下刮胶刀之间的间隙来实现。一般控制在64~70%的树脂含量,这样就会计算出一定速度厚度的板材每小时用胶量,可以作为树脂配料的参考。有效的入胶量调节依赖于实践经验,因为随着混合树脂粘度变化(阻燃剂的加入、色浆的加入、填料的加入都会影响混合树脂粘度的变化)、工作温度变化、车速变化都会影响上下刮胶刀之间能够有效涂布在薄膜上的树脂量。现在国内先进的设备已经可以自动伺服跟踪调节树脂添加量,但前期需要以生产厂家大量的经验数据为基础,还要加上很强的实践操作。
三、纤维的用量及调控
1、如果FRP板材选用短切玻璃纤维毡作为增强材料,则板材厚度和纤维布置如下:
板材厚度 (mm) |
0.8 |
1.0 |
1.2 |
1.5 |
2.0 |
2.5 |
3.0 |
|
短切毡配置 EMC(克) |
300 |
450 |
300+300 |
300+450 |
450+450 |
300+450+450 |
450+450+450 |
2、FRP板材选用短切纱作为增强材料,最直接的测量方式:切纱设备开一定的转速,洒落1米长,1米宽的短切纱丝,收起,称重,然后按重量和转速的线性关系来控制投纱量。现在的设备在纱的控制方面操作相对简单得多,只要准确的第一次测量完毕,确定了正确的线性比例,剩下的事情就是在操作端输入板材厚度和需要的含纱量就完成了,通过变频器对厚度的同步跟踪控制,决定了车速的变化对它不再有影响。
四、FRP板材厚度及检验台控制
根据板材要求的厚度来调节厚度控制辊间隙。在厚度控制辊前面,树脂和纤维应良好浸润,只要前面比例控制得当,厚度控制辊这里自然形成一层树脂堆积带,保证了板材内气泡绝大部分被赶出,有一些遗留,在检验台部分还有时间将气泡排除。国标规定FRP板材厚度公差范围±0.1mm,很多工厂自行制定的厚度公差为±0.05。这只是一种近乎理想状态的规定,平板及小波纹板材(如波高15mm)很容易实现,而波峰很高的板材(波高140mm)绝对无法控制在这个范围,所以GB/T14206-2005如果再进行修订建议考虑波高对板材断面厚度偏差的影响,进而规定一个和板材波高相关的厚度公差范围。。
五、FRP板材成型和烘箱控制
FRP板材经过检验台进入烘箱(成型区),在十几道到几十道(根据对板材断面形状的复杂程度和精度要求而定)模板的控制下,经过预成型及凝胶固化,最后进入到后固化区。在整个固化成型过程中,每段对温度的要求不同,烘箱没有明显的分界线,根据功能性分为预成型区、凝胶固化区、后固化成型区。
前面9m烘箱一般视为预成型区,内装模板,查看更多复材工艺文章登录复材应用技术网,板材断面形状好坏完全取决于模板。生产前温度要加热到90℃左右,待到连续生产达到平衡时温度一般控制在55~70℃。
中间12米烘箱是凝胶固化区,内装模板,继续控制板材断面,开始凝胶固化并有一定强度。此段温度应控制在70~90℃。但是如生产的板材是一级阻燃类,则温度和车速都相应要低一些,因为一级阻燃树脂后固化放热很剧烈,如果这里温度过高,则后面后固化区成形的板材会因温度太高而被烧得变黄;如果是二级阻燃添加烈性板材,这里的温度很难超过70℃,而且后固化区温度更低。
后端12米烘箱是后固化成型区,这里已经没有模板,板材已经有了较高的强度,在加热中继续固化反应,直至达到较高的固化度85%以上。此段没有太严格的温度控制,但不能太高,在生产一级阻燃和厚度较厚板材时,应配备冷风降温散热设备,以保证板材质量。
对于模板尺寸,除了按板材断面尺寸所有线性长度不变外,查看更多复材工艺文章登录复材应用技术网,还要考虑树脂固化收缩率,所以模板的有效宽度应略大于成品板材有效宽度,这是一个经验数字(板材成型温度、厚度、板型都对收缩有影响)。
FRP板材在固化度达到85%就可以下线作为成品销售,所以在FRP板材生产出来一年内强度都在增加。
注:以上温度为常温固化配方加热成型温度控制参考温度,如选用高温固化配方,则温度相应调整为110℃、130℃、90℃左右。
六、切割与堆放
FRP板材后固化初步完成后,经冷却、纵切(去掉两侧毛边)、横切(按要求长度尺寸)、标识成为成品板材。以前纵切都是电动锯切割,在2004年后越来越多的厂家使用无动力剪式切割,优点是无灰尘,这在环保要求越来越高的今天有极高的意义。
产品堆放中应注意板与板之间能紧密贴合的板型如平板、V-820、V-900等,尽量避免太多层板叠放,因为这样堆放可能会造成后固化再继续,而固化放热排不出,最后中间的板材会因高温而变成黄色。
为了生产出更好的板材,一般设备会在树脂刮刀和厚度控制辊之间的台面下设置加热设备,以便树脂玻纤更好的进一步浸润。上下薄膜的张紧程度和通过展平辊后的平整度也会影响板材外观质量,车速(一般为3~6米)的加快也会使板材表面发花气泡增加,原材料的选用当然是更大的影响板材内在质量的重要因素。因此质量的控制是多方面因素,只有每个环节的严格控制才能生产出优质的板材。