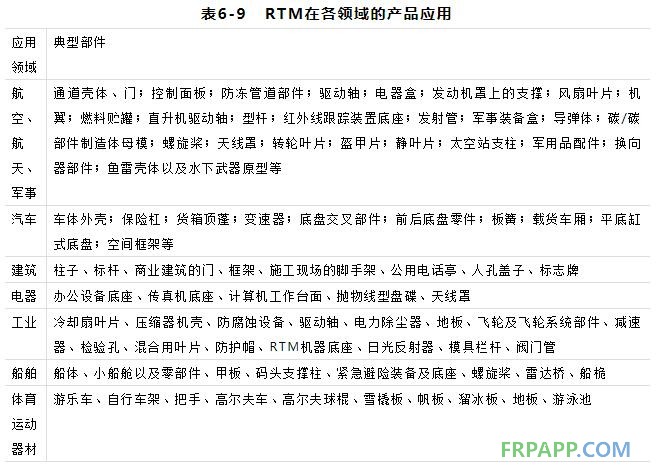
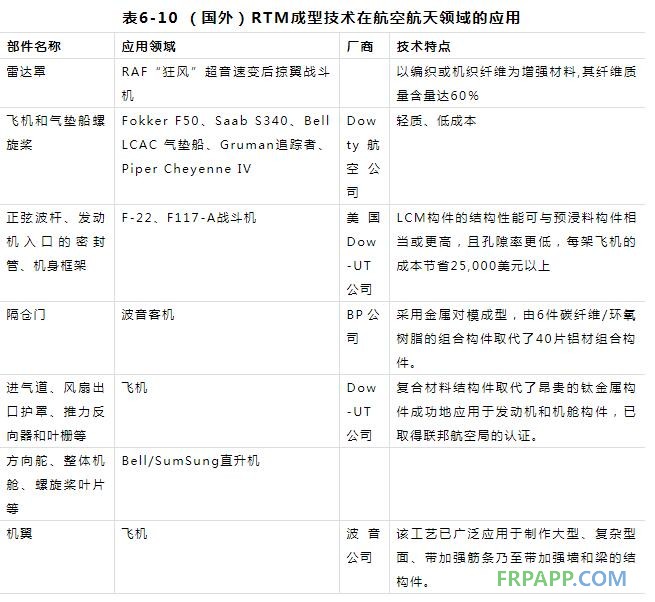
表6-11 RTM成型技术在舰船和装甲车辆上的应用
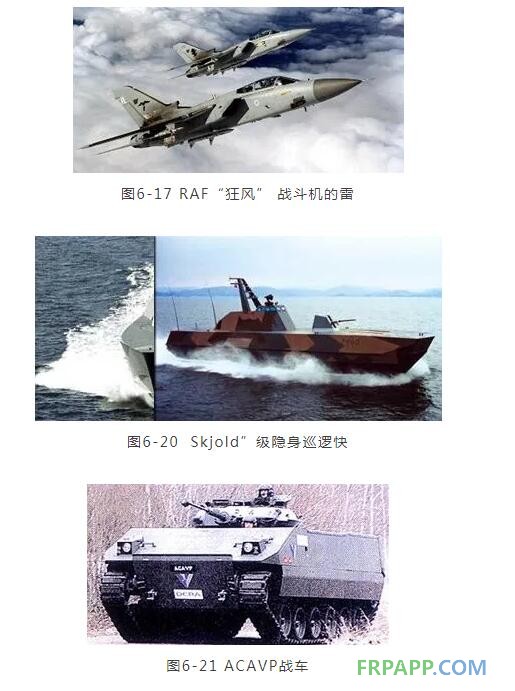
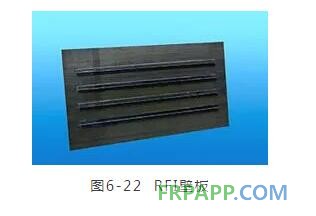
国内应用和研究RTM工艺的单位较多,如航空材料研究院、637所、703所、北京玻璃钢研究设计院、北京航空航天大学等。应用的产品有雷达罩、全碳纤维复合材料桨叶、导弹稳定翼等。
二、汽车部件
复合材料在汽车工业中的应用已经有相当长的历史,20世纪90年代以后,汽车工业开始使用RTM工艺制造零部件。汽车工业是RTM应用最早、规模最大的领域。
1970年前后,用RTM工艺加工Corvette车型的仪表盘,GM试验研究的全复合材料承力构架,达到钢制构架性能而减重20%。近年来采用RTM工艺已工业化生产了FIEERO轿车和雪佛莱LUMINA“子弹头” 汽车等车型的车身覆盖件和零部件,年产量已分别达到6.5~10万辆。1992年Chrysler研发出Viper跑车的RTM车壳;1994年Fort研发出RTM Transit商用车的高顶,1995年研制RTM Fiesta轿车的后扰流板。
Iveco卡车驾驶室的高顶采用RTM法成型,由意大利的Pianfei IPA的Mondovi厂制造。车顶总成的总面积为6m2,重量为45kg,树脂为间苯树脂,采用的预成型材料是热成型连续纤维毡。
SP5A驾驶室顶由Polymer Engineering 公司用RTM方法生产,配套服务于ERF 卡车,面积达到12m2。
材料:Class 1 BS 476 Part 7聚酯树脂;
结构:6个独立泡沫嵌件、攻丝嵌件;
模具:FRP加热模具;
生产线:双模具、双工位的模具安装系统;
后加工:经过计算机控制的多轴机器抛光后,进入喷涂车间。
巴西Technofibrac SA公司,广泛采用低成本的RTM成型工艺生产大型卡车车顶、面罩,豪华客车及公共汽车前脸、后尾,铺路车、油矿车车身、驾驶室总成等大型玻璃钢车辆部件,为Buscar、Ford、Volkswagen、GM、Honda等许多世界知名的汽车公司配套,1998年达到年产2,200吨的生产批量。
意大利的Sistema用RTM工艺为为Iveco车型配套制造箱式货车、卡车和教练车的车身、车顶,车顶最大达到14m2。他们认为,其优点是具有较好的空气动力学特性,在85km/h的车速下,减少空气阻力20-25%。
Advanced technology transit bus(ATTB)公司使用FRP减轻自重、减少油耗和尾气排放。由Metropolitan Transportation Authority(MTA)公司制造车体结构,比传统的公共汽车减重达4000kg,传统的公共汽车车体结构由数千个部件组成,但ATTB只有4个部件,采用VARTM复合夹芯工艺制造,选用Dow Chemical 公司Derakane环氧乙烯基树脂和PVC泡沫夹芯板,制造了包括:车顶、侧板、底盘和侧防撞板。
国内代表性的RTM工艺汽车部件有北京玻钢院生产的奥拓尾翼、半透明卡车遮阳罩、中国重汽“飞龙”卡车面罩、陕汽德御车型翼子板;北京玻璃钢制品有限公司生产的北方奔驰导流罩、二汽非金属零件公司生产的“猛士”车型的发动机罩等。
三、游艇
船用玻璃钢部件的特点是面积大,一般多采用VARTM技术或SCRIMP工艺制造。目前在游艇制造方面应用非常多。SCRIMP工艺特别适合制造大型复杂结构的部件,部件尺寸越大,成本优势越明显。同时,一些嵌入件,如肋、加强筋和芯材都可以在成型 时放入部件中一次成型。
四、其它领域
如下图所示的公用电话亭外壳,产品重量12Kg,采用Light-RTM工艺环形生产线制造。生产线单模循环周期1小时,生产线有25个模具,日产量可以达到600件。
图6-32为北京玻钢院复合材料有限公司生产的RTM油站地下储油罐井盖,其特点是重量轻,承载能力高,最大可承载40吨,是比较有代表性的复杂夹芯加筋结构整体成型产品。