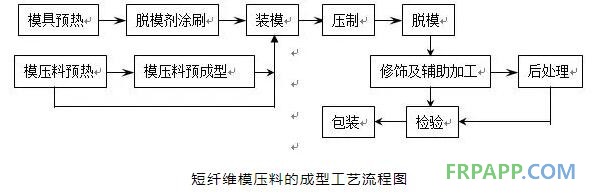
1. 压制前的准备
(1)装料量的计算
在模压成型工艺中,对于不同尺寸的模压制品要进行装料量的估算,以保证制品几何尺寸的精确,防止物料不足造成废品,或者物料损失过多而浪费材料。常用的估算方法有①形状、尺寸简单估算法,将复杂形状的制品简化成一系列简单的标准形状,进行装料量的估算;②密度比较法,对比模压制品及相应制品的密度,已知相应制品的体积,即可估算出模压制品的装料量;③注型比较法,在模压制品模具中,用树脂、石蜡等注型材料注成产品,再按注型材料的密度、重量及制品的密度求出制品的装料量。
(2)脱模剂的涂刷
在模压成型工艺中,除使用内脱模剂外,还在模具型腔表面上涂刷外脱模剂,常用的有油酸、石蜡、硬脂酸、硬脂酸锌、有机硅油、硅脂等。所涂刷的脱模剂在满足脱模要求的前提下,用量尽量少些,涂刷要均匀。一般情况下,酚醛型模压料多用有机油、油酸、硬脂酸等脱模剂,环氧或环氧酚醛型模压料多用硅脂和有机硅油脱模剂。
(3)预压
将松散的粉状或纤维状的模压料预先用冷压法压成重量一定、形状规整的密实体。采用预压作业可提高生产效率、改善劳动条件,有利于产品质量的提高。
(4)预热
在压制前将模压料加热,去除水分和其它挥发份,可以提高固化速率,缩短压制周期;增进制品固化的均匀性,提高制品的物理机械性能,提高模压料的流动性。
(5)表压值的计算
在模压工艺中,首先要根据制品所要求的成型压力,计算出压机的表压值。成型压力是指制品水平投影面上单位面积所承受的压力。它和表压值之间存在的函数关系:
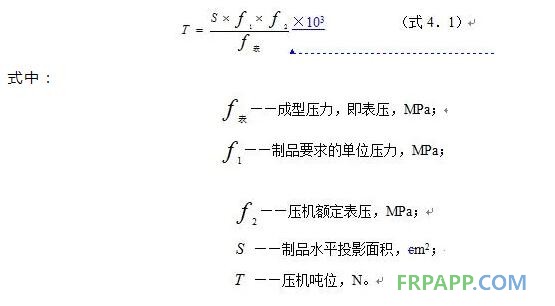
在模压成型工艺中,成型压力的大小决定于模压料的品种和制品结构的复杂程度,成型压力是选择压机吨位的依据。
2.压制工艺
(1)装料和装模
往模具中加入制品所需用的模压料过程称为装料,装料量按估算结果,经试压后确定。装模应遵循下列原则:物料流动路程最短;物料铺设应均匀;对于狭小流道和死角,应预先进行料的铺设。
(2)模压温度制度
模压温度制度主要包括装模温度、升温速率、成型温度和保温时间的选择。
(a)装模温度
装模温度是指将物料放入模腔时模具的温度,它主要取决于物料的品种和模压料的质量指标。一般而言,模压料挥发份含量高,不溶性树脂含量低时,装模温度较低。反之,要适当提高装模温度。制品结构复杂及大型制品装模温度一般宜在室温~90℃范围内。
(b)升温速率
指由装模温度到最高压制温度的升温速率。对快速模压工艺,装模温度即为压制温度,不存在升温速率问题。而慢速模压工艺,应依据模压料树脂的类型、制品的厚度选择适当的升温速率。
(c)成型温度
树脂在固化过程中会放出或吸收一定的热量,根据放热量可判断树脂缩聚反应的程度,从而为确定成型温度提供依据。一般情况下,先确定一个比较大的温度范围,再通过工艺—性能试验选择合理的成型温度。成型温度与模压料的品种有很大关系。成型温度过高,树脂反应速度过快,物料流动性降低过快,常出现早期局部固化,无法充满模腔。温度过低,制品保温时间不足,则会出现固化不完全等缺陷。
(d)保温时间
指在成型压力和成型温度下保温的时间,其作用是使制品固化完全和消除内应力。保温时间的长短取决于模压料的品种、成型温度的高低和制品的结构尺寸和性能。
(e)降温
在慢速成型中,保温结束后要在一定压力下逐渐降温,模具温度降至60℃以下时,方可进行脱模操作。降温方式有自然冷却和强制降温两种。快速压制工艺可不采用降温操作,待保温结束后即可在成型温度下脱模,取出制品。
(3)压力制度
压力制度包括成型压力、合模速度、加压时机、放气等。
(a)成型压力
成型压力是指制品水平投影面积上所承受的压力。它的作用是克服物料中挥发物产生的蒸汽压,避免制品产生气泡、分层、结构松散等缺陷,同时也可增加物料的流动性,便于物料充满模具型腔的各个角落,使制品结构密实,机械强度提高。
成型压力的选择取决于两个方面的因素:a模压料的种类及质量指标。如酚醛模压料的成型压力一般为30~50MPa,环氧酚醛模压料的成型压力为5~30MPa,b制品结构形状尺寸。对于结构复杂,壁厚较厚的制品,其成型压力要适当增加。外观性能及平滑度要求高的制品一般也选择较高的成型压力。
(b)合模速度
装模后,上下模闭合的过程称为合模。上模下行要快,但在与模压料将接触时,其速度要放慢。下行快,有利于操作和提高效率;合模要慢,有利于模内气体的充分排除,减少气泡、砂眼等缺陷的产生。
(c)加压时机
合模后,进行加压操作。加压时机的选择对制品的质量有很大的影响。加压过早,树脂反应程度低,分子质量小,粘度低,树脂在压力下易流失,在制品中产生树脂集聚或局部纤维裸露。加压过迟,树脂反应程度高,粘度大,物料流动性差,难以充满模腔,形成废品。通常,快速成型不存在加压时机的选择。
(d)卸压排气
将物料中残余的挥发物、固化反应放出的低分子化合物及带入物料的空气排除过程称为排气。其目的是为了保证制品的密实性,避免制品产生气泡、分层现象。
(4)制品后处理
制品后处理是指将已脱模的制品在较高温度下进一步加热固化一段时间,其目的是保证树脂的完全固化,提高制品尺寸稳定性和电性能,消除制品中的内应力,减少制品变形。有时也可根据实际情况,采用冷模方法,矫正产品变形,防止翘曲和收缩。
在模压制品定型出模后,为满足制品设计要求还应建立毛边打磨和辅助加工工序。毛边打磨是去除制品成型时在边缘部位的毛刺飞边,打磨时一定要注意方法和方向,否则,很有可能把与毛边相连的局部打磨掉。
对于一些结构复杂的产品,往往还需进行机械加工来满足设计要求。模压制品对机加工是很敏感的。如加工不当,很容易产生破裂、分层。
3.典型配方模压成型工艺
选定何种工艺主要取决于模压料类型,此外还应考虑生产效率及制品结构、尺寸性能要求等。慢速成型工艺见表1,快速模压成型工艺见表2:
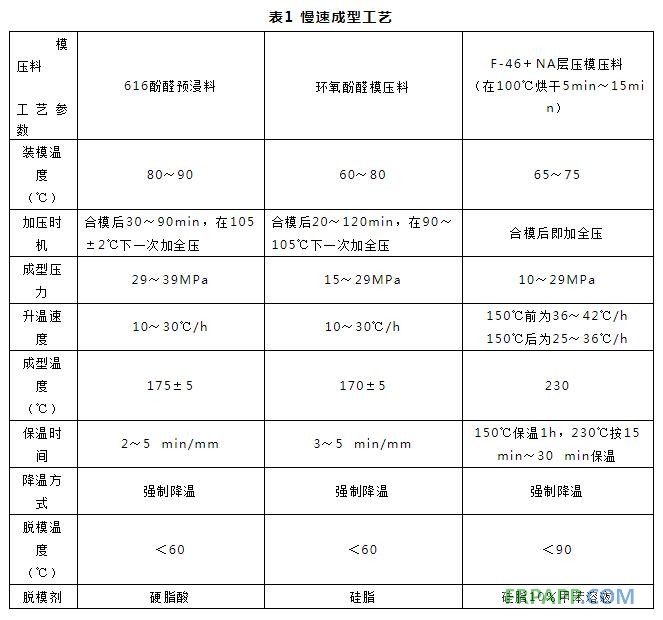
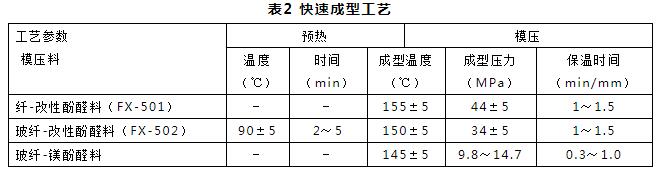
4.短纤维模压料制品常见缺陷及其原因
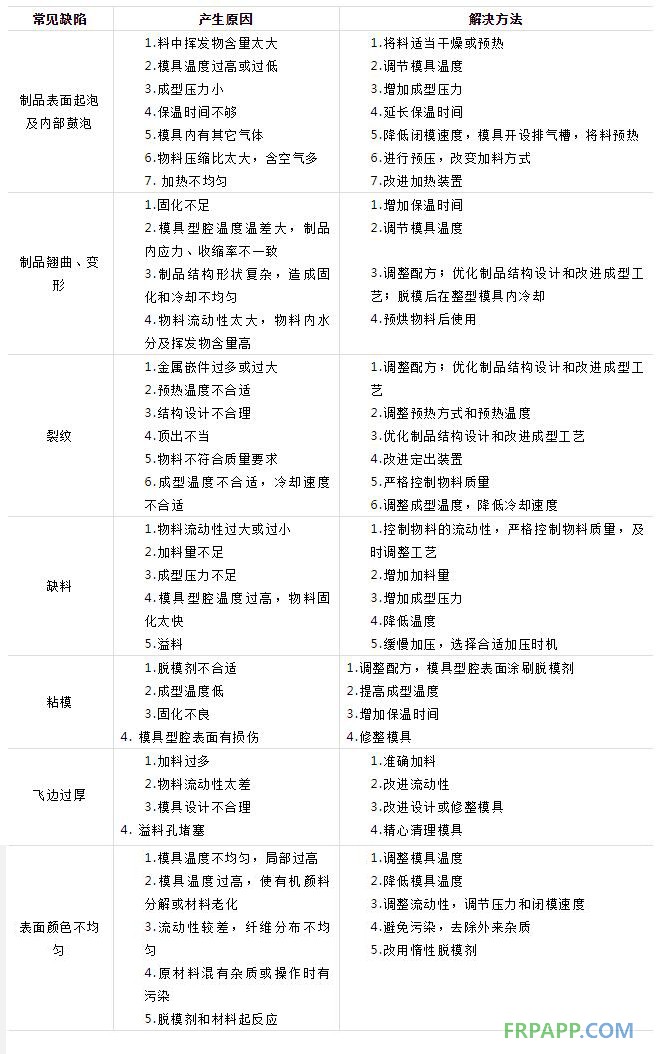