(1)BMC生产设备
团状模塑料的生产设备一般由两种混合器和挤出机组成。第一种混合器为高速分散机。高速分散机的速度可调节,机头可以提升。桨叶布置与结构应具有高的混合效率与混合速率。第二类混合器应用最广泛的是双轴或双桨式混合器。按照其桨叶结构不同,分为Σ型桨叶和Z型桨叶混合器。
(a)高速分散机
为了使树脂糊分散均匀,需要使用剪切速率很高的搅拌机。目前,常用的搅拌机图片见图。此种高速分散机是对两种或者多种液体和固体粉末状物料进行搅拌、溶解和分散的高效设备。其主要技术参数见表。
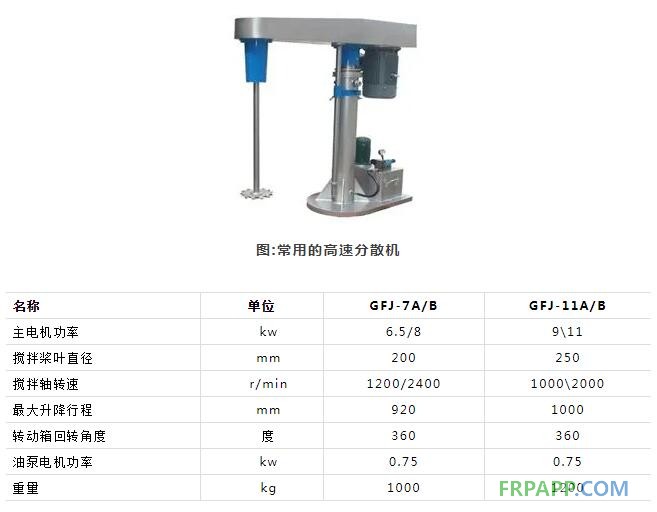
(b)双轴式混合器
BMC生产过程中所用的捏合机一般为双桨式捏合机。这种捏合机具有高效、快速和充分三大特点。由于生产厂家不同混合器的桨叶形式也不相同。图列举了几种双轴式捏合机的桨叶结构图。其中,最常用的桨叶结构为Σ型桨叶和Z型桨叶。图:捏合机图片。
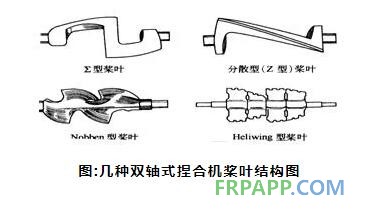
Σ型双桨捏合机的桨叶与混合器之间的间隙很小,约为0.5 mm~1.27mm,容易残存树脂,所以最好将桨叶和捏合机壁之间的间隙固定为6.4 mm或9.6 mm,这样既可以实现BMC物料的充分混合,又可以使增强材料的离析程度降低到最低限度。Σ型双桨捏合机的缺点是清洁比较困难。
Z型双桨捏合机的结构不仅易于清洗,而且在混合过程中,增强材料的加入、混合更加容易。在双桨捏合机中,混合室带有通水夹套,可以通冷水或热水。这样可以进行温度控制,使物料温度保持在40℃左右,可以降低树脂糊的粘度,增加BMC的产量。为了方便卸料和清洗,桨叶应可以反转,整个混合室也应可以翻转90度,以便将混合好的物料从捏合机中倒出。桨叶和混合室壁之间的间隙大小随混合器大小而定。如混合器容量为8.5L的捏合机,其间隙为3.2 mm,而容量为190~380L的捏合机,间隙为6.35 mm~9.5 mm。
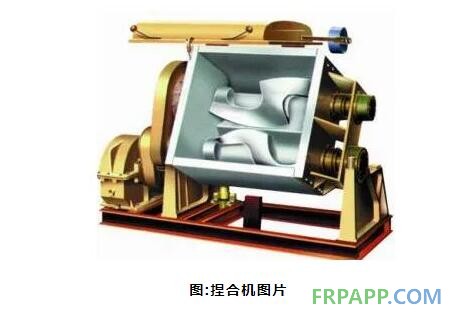
(c)团状模塑料挤出机
为了使团状模塑料更加致密,并便于以后的成型操作,当它在混合器中完成了其制备过程后,往往将其送入一台挤出机中进行进一步的加工。
挤出机的作用是压紧团状模塑料,驱除多余的空气,并且为了使团状模塑料在成型时便于使用而挤成一定质量和形状的料块。为进一步除净空气,挤出机上带真空室就更加有效。
当团状模塑料玻璃纤维含量高时,富有弹性,不能压缩成低松散性的毛坯,也不能成功地挤压成致密的类似绳状的料块。
当团状模塑料的玻璃纤维含量较低时(通常在20%以下),通过选择适当的填料和树脂,可以将团状模塑料挤压成圆木(棒)状,或切成较小的弹丸。精确的制丸可适应大批量生产,如在用多孔模成型。这样的小丸在制品固化期间容易放在加料板上,从而减少了压机开启的时间。精确的制丸也适用于自动化成型操作中的振动喂料;对于较大的制品,切成棒状是适宜的。
挤出过程有时会引起纤维的取向,使团状模塑料性能具有方向性,同时由于挤压过程引起纤维束的部分破断而使冲击强度降低。
在团状模塑料挤压工艺中,影响团状模塑料质量的因素有挤出机膛内尺寸、螺杆设计、膛内温度和团状模塑料在加入挤出机时的温度、生产速度、出口模的尺寸和形状、模具温度等。这些因素对不同材料所造成的影响程度是不同的,所以对某一材料的挤出工艺条件应根据实际情况,经反复试验后确定。。
国外使用的挤出机是粘土型挤出机,具有一根直径很粗的螺杆。螺杆通常都要经过抛光和镀铬处理,以便易于清洁和延长使用寿命。表列举了几种Bonnot粘土型BMC挤出机的基本参数。图是国产双螺杆挤出机。
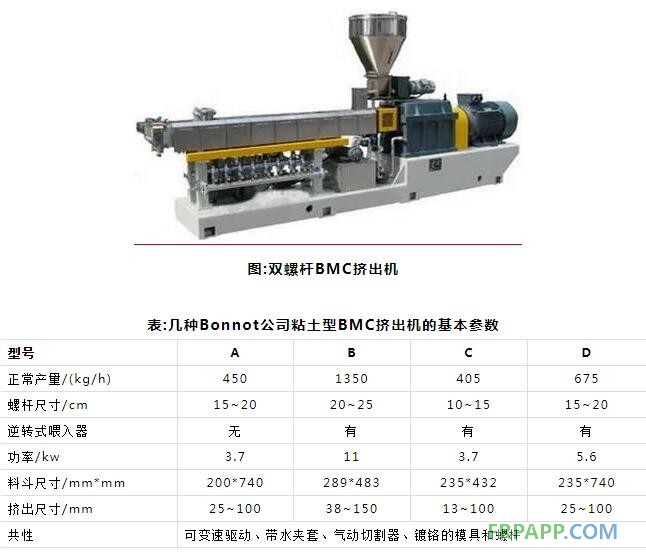
(2)BMC生产技术
在捏合机中,各部分的混合分两步进行。首先将树脂、颜料、引发剂及填料充分混合,然后加入增强材料。在增强材料加入之前,混合时间不能太长,混合强度不能太大。而加入增强材料后,混合时间仅需要保证其均匀分布即可。
典型的混合程序:
▶在同一容器中,将引发剂和氧化镁加入已经混合好的树脂中搅拌10分钟。
▶将填料加入容器中,搅拌10分钟。
▶加入增强材料后捏合5分钟。
▶挤压或按需要保持松散状态。
▶增稠24小时后可以使用。
混料工艺中的影响因素
混料工艺的影响因素很多。如树脂糊体系的组成和粘度、增强材料的类型和长度、混合器类型、混合工序、混合温度、混合时间等均可影响到混料工艺。
▶树脂体系的粘度
树脂体系的粘度应控制在一定范围内,以使其对增强材料的离析倾向的影响最小。就成型过程而言,为防止因某一种组分优先流动而导致产品产生孔穴和不均匀现象,树脂糊体系应具有较高的粘度。但是对混合过程而言,过高的粘度会造成制品的浸渍效果变差,影响其力学性能。
▶增强材料
常用的增强材料为玻璃纤维增强材料。玻璃纤维具有较高的机械强度和低的吸水率,但是在混合过程中容易产生纤维离析的现象。为减少此种倾向,混合器的浆—壁间隙至少不低于6.4mm。
纤维的类型对制品的性能也具有很大的影响。高集束性纤维在混合过程中保持高的集束性,并且制备的预混料的拉伸强度尤其是熔接痕处的拉伸强度比普通纤维提高50%。中集束性纤维在混合过程中的损伤少,但制品的成型工艺性能及表面性能差。
▶混合温度
热混合可以改善混合工艺,提高制品强度。在热混合过程中,所有的组分都是温热的。树脂和填料的温度在49~54℃。玻璃纤维的预热温度为66℃,并且少量分批加入混合器中。这样制备的预混料与室温混合的预混料相比,弯曲强度、压缩强度、弯曲模量、拉伸强度都有一定程度的提高。同时,制品的表面质量得到了提高。
▶混合时间
混合时间对制品的机械性能有明显的影响。增加混合时间将会降低制品的机械性能。如对纤维含量为35%的高集束纤维进行热分散时,混合时间由5分钟延长到8分钟、13分钟、30分钟时,制品的弯曲强度分别从原来的113MPa降低到113MPa、83.3MPa、65MPa。
▶加料顺序
混合时各组分的加入顺序和每次加料后的混合时间非常重要。加料不能太快以免混合不均匀,也不能太慢,以免引起纤维和材料的破坏,从而降低材料的强度。混合也不能过早的停止,以免混合物中存在未浸渍的纤维,从而影响 制品的表面质量。玻璃纤维一般在其他成分混合好后才均匀而缓慢的加入,而不是同时加入混合器中。较好的方法是采用机械供给器,使玻璃纤维均匀的分布在混合器的整个区域内。