(1)压机
压机是模压成型的主要设备。压机的作用是提供成型时所需要的压力以及开模脱出制品时所需的脱模力。最早使用的是手扳压机,因操作强度太大已被淘汰;此后出现的机动压机减轻了劳动强度,但操作维修复杂,噪音大,吨位低;液压机吨位大,动作平稳,压力和速度可自由调整,现大多采用液压机。
液压机是用液体(油或水)来传递压力的设备,一般由动力机构、控制机构和执行机构三部分组成。按液压机机身结构可分为框架式和三梁四柱式。为了加工合格的模压制品,液压机应保证的工艺参数和使用要求是成型压力、工作速度和温度和时间控制。本部分对液压机的工作原理与分类进行简单介绍。
(a) 液压机的工作原理
液压机是利用液体来传递压力的设备。液体在密闭容器内传递压力遵循帕斯卡定律:在互相连通而且充满液体的若干容器内,若某处受到外力的作用而产生静压力时,该压强将通过液体传递到各个连通器内,且压强数值相等,如图所示。
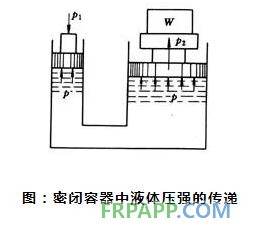
(b)液压机的组成和分类
如图示,为典型液压机的结构。它是由机身、工作油缸、活动横梁、顶出机构、液压传动机构和电器控制系统组成。
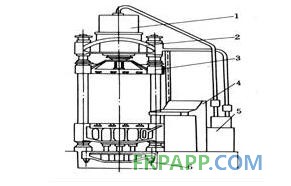
1-油缸;2-机身;3-动横梁;4-电气装置;5-液压传动装置 ;6-顶出装置
图:典型液压机的结构
液压机可按如下几种方式进行分类。具体分类见表:
(c)液压机的选择
采用液压机成型复合材料制品时,一般应考虑以下因素:
a)压机吨位
在选择成型制品压机时,应按照制品最少承受的单位压力来选择压机的最小吨位。而对于模压料需横向流动的偏心制品或深度尺寸大的制品,压机吨位可以按照制品投影面积承受高达7-10MPa的单位压力来计算压机吨位。
b)压机行程
压机行程是指压机活动横梁可移动的最大距离。压机的最小量程应不小于960mm,相应的压机开档尺寸为1200 mm。对于大型压机而言,以上尺寸都要相应增大。
C)压机台面尺寸
对于小吨位压机,其台面尺寸应为750mm(从左到右)×960mm(从前到后),较大吨位的压机,其台面尺寸最小应为1200(从左到右)×9600mm(从前到后)。
d)压机台面精度
当压机的最大吨位全部均匀的施加于2/3台面的面积上时,活动横梁和压机台面被支撑在四角支座上时,其平行度为0.025mm/m。
e)压力增长
当压力从零增长到最大吨位时,所需要的时间最长为5s。
f)压机速度
压机速度可用两速制和三速制。采用两速制时,高速推进速度为7500mm/min,慢速闭合时,速度为0~250mm/min,其间速度可以调节。采用三速制时,高速推进速度为10000mm/min, 中速推进速度为2500mm/min,慢速闭合时,速度为0~375mm/min,其间速度可以调节。
(d)SMC制品专用压机
SMC多用来制造大型薄壁或结构不规则的高深度制品,所需成型压力和温度较低,但成型时间短,需要在一定程度上控制流程状态,因此针对SMC制品的成型特点发展了低成型压力的液压机,并出现了专用的SMC液压机。SMC专用液压机总压力高、工作台面大,活塞空载运行速度高,具有多种加压速度,对上下工作台面的平行度和刚度要求高。
SMC专用压机可分为两种,一种是成型小型制品(相对一般的BMC制品而言要大一些)用的压机,另一种是成型大﹑中型制品用的压机。由于SMC材料本身的特点以及它最大的应用领域——汽车工业的独特要求,从而使得对SMC成型压机的要求更加严格。SMC尤其适合生产表面积很大的薄壁制品,因而要求压机必须有“三大”即:大工作台面﹑大工作行程和大吨位。同时必须有良好的刚性,能承受较大的偏心载荷,以及精密的确保压机台面平行度的控制装置,以保证材料在高压成型过程中,两半模具始终保证有理想的平行度,从而使制品的厚度在大面积范围内仍能保持均匀。
目前,SMC专用压机吨位范围为63~3000T,大型压机台面尺寸可达1.25m×(1.0~3.2)m,上﹑下台面的距离可达2.5m。大多为液压机,具有多种不同类型,最常用的是圆柱式压机和框式压机。圆柱式压机采用圆柱来支撑上﹑下台面,这些圆柱对活动台面起导向作用,但它只能承受有限的偏心载荷,平行度不好保证。而框式压机通常用于大面积制作的成型,并正在迅速取代圆柱式压机,它们常用于超过250Tt的承载场合,具有良好的平行度,可承受相当大的偏心载荷。
SMC专用压机应考虑以下参数:
a)台面尺寸
1500t以上的压机,台面尺寸3.0m×2.0m者居多。
b)压机开档
是指压机工作台和活动横梁之间的全开距离。一般可根据模具闭合高度与预定需压制的最深制品高度尺寸之和的两倍来确定。SMC压机的开档一般都比较大,某些大型制品其开档甚至可达2.5m。
c)行程
是指活动横梁的移动距离。至少为预定压制的最深制品高度尺寸的3倍,SMC压机的行程一般都在1.5~2.0m左右。
d)吨位
压机总吨位按台面面积乘上4.2~5.6MPa的单位压力计算,压力调节精度应在±5%范围内,回程力为额定压力的20%~25%。
e)速度
高速推进 25000 mm/min
中速推进 2000~15000 mm/min
加压及开模 0~750 mm/min(可调节)
高速回程 20000 mm/min
压力增长 2s
(2)模具
(a)模具结构
典型模具结构如图43.278所示。它是由上模和下模两部分组成。上、下模闭合便装于加料室和型腔中的模压料受热受压,变为熔融状态充满整个型腔。当制品固化成型后,上、下模打开,利用顶出装置顶出制品。模具可进一步分为如下各个部件。
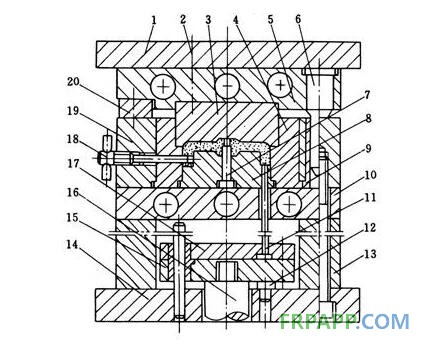
1上板 2螺钉 3上凸模 4凹模 5加热板 6导柱 7型芯 8下凸模 9加热板 10 导向套 11顶杆12档钉 13垫板 14底板 15垫板 16拉杆 17顶杆固定板 18侧型芯 19型腔固定板 20承压板
图:典型模具结构
①型腔 直接成型制品的部位。图示的模具型腔由上凸模3、下凸模8、凹模4构成。
②加料室 指凹模4的上半部。
③导向机构 由布置在模具上模周边的四根导柱6和装有导向套10的导柱孔组成。导向机构用以
④侧向分型抽芯机构 模压带有侧孔和侧凹的制品,模具必须设有各种侧向分型抽芯机构,制品才能脱出。
⑤脱模机构 由顶出板17、顶出杆11等零件组成。
⑥加热系统 一般热固性模压料成型需要在较高的温度下进行,因此,模具必须加热。常见加热方式有:电加热、蒸汽加热等。
(b)模具分类
a)根据与压机联接方式分
①移动式模具 属于外装卸模具。模具不固定在压机上。一般情况下,模具的分模、装料、闭合及成型后制品从模具内取出均在机外进行。模具本身不带加热装置。这种模具适用于压制批量不大的中小型制品。移动式模具结构简单,制造周期短,造价低。但是加料、开模、取件等工序均为手工操作,劳动强度大,生产效率低,模具尺寸及质量不宜过大。
②固定式模具 属于机内装卸的模具。它固定在压机上,且本身带有加热装置整个生产过程即分模、装料、闭合、成型及顶出产品都在压机上进行。固定式模具使用寿命长,适于生产批量大,尺寸较大的制品。
③半固定式模具 这种模具介于上述两者之间,一般为上模固定在压机上,下模可以沿着导轨移动,用定位块定位。
b)按分型面特征分类
分型面是为了将已经成型好的制品从型腔中取出或者为满足安装嵌件及排气等成型的需要。
①水平分型面 分型面平行于压机的工作台面。
②复合分型面 分型面垂直于压机的工作台面
③垂直分型面 分型面既有平行于压机的工作台面的,也有垂直于压机的工作台面的。
c)按上、下模闭合形式分
①敞开式模具 如图(1)所示,该模具特点是没有加料室。此类模具结构简单,造价低,耐用,易脱模,安装嵌件方便。
②密闭式模具 如图(2)所示。模具的加料室为型腔上部的延续部分,无挤压面。压机所施加的压力全部作用在制品上。模压料的溢出量非常少。制品的密实性好,机械强度较高,且飞边在垂直方向,易于去除。这种模具适合成型形状复杂、薄壁、长流程的制品,也适用于流动性小、单位压力大,比容大的模压料。其缺点是1加料量必须准确控制,2模具凸模与加料室边壁摩擦,边壁容易损伤,在顶出时带有有损伤痕迹的加料室壁又容易将制品表面损伤。
③半密闭式模具 如图(3)所示。该种模具型腔上有加料室,型腔内有挤出环,制品的密实性比敞开式模具成型的制品好,且易于保证高度方向尺寸精度,脱模时可以避免擦伤制品。
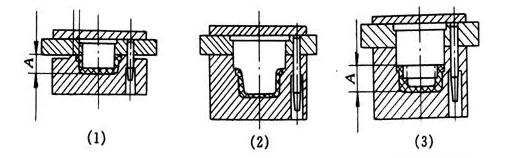
(1)敞开式 (2)半密闭式 (3)密闭式
图:模具按照闭合形式分类
片状模塑料成型模具采用半溢式垂直分型结构,将会获得较好的结果。因为这种设计能确保成型压力有效的施加于制品上,从而使制品获得良好的表面,同时又具有足够的间隙使被捕集的空气逸出。溢料间隙的平行段的长度均可变化,其精确的尺寸主要取决于特定制品的大小和形状。小制品溢料间隙最好为0.08mm,而大制品则溢料间隙应增大,直到约为0.18mm的最大值。溢料间隙过小,空气的逃逸比较困难;过大则会助长料在该方向上的流动,从而导致纤维取向产生波纹及削弱制品强度。溢料区平行段的长短,根据在模具内所要求的不溢性程度而确定。一般来说,平行段长度越长,不溢性程度越高,有利于模压料进入筋和槽的位置,制品的表面质量好。但是平行段长度过长就容易捕集空气,在复杂形状的制品中,可能会造成多孔性。
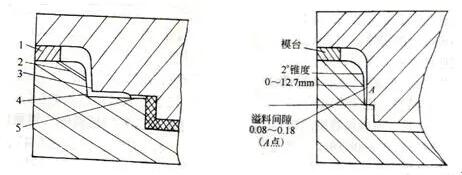
1-模台 2锥度(2。) 3-间隙(0.08-0.18mm) 4-间隙(1.0-1.5mm) 5-间隙(0.08-0.13mm)
(1)半溢式水平分型模具结构 (2)半溢式垂直分型模具结构
图:模具结构
虽然垂直分型结构的模具对片状模塑料来说比较好,但是,复杂制品的模具制造相当困难,而且价格昂贵。在这种情况下,可使用半溢式水平分型模具结构。从图中可以看到其溢料间隙与垂直分型模具的间隙在同一范围内。凹模壁的斜度也为20 ,但是在某些情况下,为了增加模具的不溢性,斜度可适当减小。从制品边缘到模具壁之间的距离可以变化,但凸台区的宽度必须保持在2.0~5.0mm范围内。因为凸台区承受了一定的压力,所以降低了制品上所承受的有效压力。即使减小凸台的宽度,也仍不能使片状模塑料制品的毛边厚度小于0.05~0.15mm。因此一般设计凸台面之间的间隙为0.08~0.13mm。从凸台到溢料线的部分应有1.0~1.5mm的间隙,以避免在该点产生的流动限制。
(c)模具材料
选用模具材料时,应根据产品的批量、工艺方法和加工对象进行选择。SMC模具应选择易切削、组织致密、抛光性能好的材料。下列几种钢材是制造模具经常选择的材质:
(1) P20(3Cr2Mo):常用于注塑模具,是质量较好的钢材。
(2) 738:注塑模具钢,超级预加硬塑胶模钢,适合高要求持久性塑胶模具,抛光良好,硬度均匀。
(3) 718(3Cr2NiMo):预加硬钢,长期生产的注塑模用,抛光性、蚀花加工性更佳,质量比P20略好。
(4) 40Cr: 合金调质用钢,适用于制作模具A、B板,硬度及抛光性能略胜于50C钢材。
(5) 50C:模具普遍使用的钢材,适用于制作注塑模架、五金模架及零件。
(6) 45#钢:以前最常用的模具钢材,硬度较低,不耐磨,塑性、韧性较好,因此加工性能较好,价格也相对比较低廉。现在通常用45#钢来加工垫块、压板等辅助备件。
(d)模具加工精度
模具加工精度主要有三个方面的因素:尺寸公差、形位公差、表面粗糙度。我们通常对模具厂家提的加工精度要求主要是尺寸公差和表面粗糙度。尺寸公差又大致分两类:外形尺寸和模腔尺寸。对于模具外形尺寸,要求比较宽松,实际加工尺寸和模具图纸理论尺寸的误差不超过±1.5mm都算合格。而模腔尺寸精度要求必须按图纸严格控制,一般不超过0~0.1mm。我们所说的模具表面精度一般指表面粗糙度,处理后一般要求模具型腔粗糙度
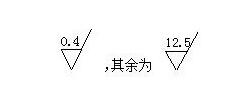
我们可根据实际产品表面要求提出相对应的模具表面加工精度。
(e)剪切边(溢料边)间隙和长度
前面已指出在不同结构的模具内剪切间隙和长度的确定范围,间隙和长度对不同的SMC品种应取不同的值。
1)剪切边间隙 最小收缩的片状模塑料为0.05~0.1mm;低和中等收缩的片状模塑料为0.1~0.20mm。
2)剪切边长度 最小收缩的片状模塑料为2~4mm。
3)剪切边硬度 HRC50~55。
4)模具的平行度 应在0.127mm的范围。
5)导销和衬套 导销最小长度应保证在阳模进入下模前至少已进入衬套相当于其直径一半的长度,导销的最小直径为模具长度加宽的2%,衬套应有出气孔和润滑附件。
6)顶出销 顶出销必须紧密配合和磨光,防止片状模塑料的进入。它们也应具有0.05~0.13mm的间隙。其硬度为HRC65~80,当使用最小收缩系统时,应考虑适当的顶出形式。尤其模制筋或凸起部时特别重要,顶出销可用机械式或液压驱动。
(f)表面处理
为了提高模具表面耐磨性和耐蚀性,常对其进行适当的表面处理。
模具镀铬是一种应用最多的表面处理方法。镀铬层在大气中具有强烈的钝化作用,能长久保持金属光泽,在多种酸性介质中均不发生化学反应。镀层硬度达1000HV相当于HRC65,因而具有优良的耐磨性。镀铬层还具有较高的耐热性,在空气中加热到500℃时其外观和硬度几乎不发生变化。
渗氮具有处理温度低(一般为550~570℃)、模具变形甚微和渗层硬度高(可达1000~1200HV,相当于HRC65~72)等优点,因而也非常适合模塑料制品模具的表面处理。含有铬、钼、铝、钒和钛等合金元素的钢种比碳钢有更好的渗氮性能,用作SMC模具时进行渗氮处理可大大提高耐磨性。表面处理对模具寿命的影响见下表:
表:模具表面处理对寿命的影响