世界各发达国家对玻璃钢废弃物的回收利用十分重视,研究得较早。如:美国在80年代即开展热分解回收方法可行性研究;日本通产省于1990年设立玻璃钢再资源化处理委员会,并下设调查、标准化、切断破碎、粉碎利用和热塑性玻璃钢处理等七个技术分会,自1991年起,制定了多部有关玻璃钢回收利用和促进回收利用的法令政策;欧美确定了以“省资源、再利用、再资源化、最终处理”为指导方针的玻璃钢废弃物处理的发展方向。各国政府和玻璃钢企业都投入大量人力物力,先后开发出多种回收方法,如:热解回收法、粉碎回收法、能量回收法、水解或醇解回收法、生物回收法等,其中较为经济实用的是热解回收法和粉碎回收法,并已开发出专用设备。
国内目前还没有有效的处理办法,只能采取简单的填埋或焚烧办法,但前者造成土壤的破坏和土地的浪费,后者由于焚烧过程中产生大量废气造成环境污染。而且处理费用高,处理量有限,远不能满足热固性复合材料废弃物数量剧增的要求。随着对热固性复合材料废弃物回收的环保呼声的日益强烈,热固性复合材料废弃物已成为社会问题,严重影响热固性复合材料在建材、汽车等行业的进一步应用。如何处置这些日积月累、越来越多的热固性复合材料废弃物已成为制约我国玻璃钢/复合材料行业健康发展的关键问题。
我国玻璃钢/复合材料行业经过多年的发展和应用开发,热固性复合材料废弃物数量逐年递增,回收利用已直接影响玻璃钢/复合材料行业的发展,因此,研究热固性玻璃钢固体废弃物回收处理方法,建立一整套关于热固性复合材料废弃物收集、加工、回收料应用等现代化回收体系,已迫在眉睫。同时提出新的材料认识观、发展观、评价观和设计观,加强设计和生产质量管理,提高制品质量和寿命,缓解热固性复合材料废弃物的排放量以及大力开发新型易回收利用的绿色热固性复合材料,增强环境保护协同性,是摆在每一个玻璃钢/复合材料企业和研究者面前的急需解决的问题。
1、SMC/BMC复合材料的再生利用方法
SMC/BMC制品的回收技术有三种方法比较可行:物理循环:造粒;化学回收:热裂解;能量回收。
物理循环方法是基于直接利用废弃树脂基复合材料制品,并不改变其化学性质的一种回收方法。由于热固性复合材料一旦固化,就不会在热和压力的重新作用下转变成另外一种产品。因此,必须将热固性复合材料切割或粉碎成一定的形状,当作填料或增强材料使用。一种方法是将整个热固性复合材料粉碎使用,另外一种方法是粉碎后从中获得玻璃纤维。
化学循环方法主要是指高分子材料通过清洗、粉碎、干燥后,进行化学处理,从而得到有用的化工原材料或油品的过程。
能量循环方法是指燃烧不能以其他方法加工的混合塑料或残留物,以利用其释放的能量,包括燃烧废物获取能量和燃烧废物燃料获取能量。
SMC/BMC复合材料的回收处理示意图见图,回收方法比较见表:
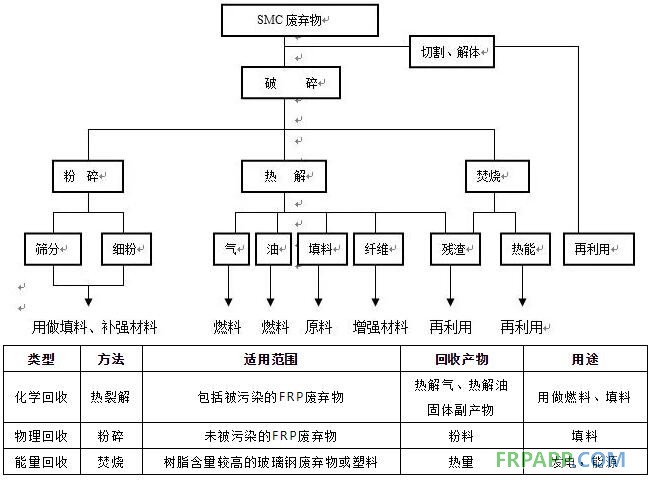
(1)热解法:热分解回收热固性复合材料废料中的有机物质
热解法是一种在无氧的情况下,利用高温使热固性复合材料废弃物分解成燃气、燃油和固体三种回收物的方法。其中每一种回收物都可以进一步回收利用。该种方法回收利用的效果较好,同时对设备的要求较高,难度大,投资建厂成本高,回收费用较高。
(2)粉碎法:将玻璃钢废弃物粉碎成微粒作热固性复合材料填料
将玻璃钢废弃物粉碎成粒度不同的粉末,选用适宜粒度范围的回收料作为填料使用。这种方法,生产成本较低,处理方法简单,但在制造微粉时,粉碎成本相对较高,作为微粉添加到SMC/BMC或其他玻璃钢产品中,往往随着添加量的增加,降低新制品的强度。另外,该方法还存在一些突出的缺点,如原料受到限制(只能处理废弃物中未被污染的废弃物);玻璃纤维在粉碎的过程中容易卷曲结球,无法进行再加工处理利用,成为另一种不可降解的废弃物,因此,回收利用率较低。
(3)焚烧法
传统的焚烧法指的是区别于简单焚烧的能量回收技术,即将含有有机物或者完全为有机物的废弃物在专用的焚烧炉里进行焚烧处理,同时将燃烧的热量转化为其它能量。但是焚烧炉的造价较高,使得焚烧处理费用高达2000元/吨。并且由于热固性玻璃钢中有机物的含量较低,燃烧放热较少,焚烧后的灰分不能再利用,只能填埋,因此,该种方法一直没有被广泛应用。
近年来,日本新开发了玻璃钢焚烧联助水泥生产工艺技术,将玻璃钢废弃物用作水泥生产的燃、原料。该方法是把玻璃钢废弃物先粉碎为粒径10mm大小的粉末,吹入水泥窑炉内,作为燃料燃烧,残渣作为水泥原料使用。其显著特点是:能把玻璃钢废弃物全部处理完毕,达到100%回收。玻璃钢废弃物一部分转化成能源,可以减小部分燃料用量;另外,因窑内温度高,产生的有害气体极少,没有有害气体污染空气的问题。
2、SMC/BMC复合材料破碎技术研究
无论采用何种回收方法,第一步都是将FRP产品加工成需要的尺寸,即粉碎。根据再利用方法不同,所提出的要求也不同,所以单一粉碎设备不能满足要求,需联合配套、分级处理。主要配套设备有废弃物清洗线、切割机、输送机、破碎机、微粉机、除静电装置、收尘装置等。本部分主要对适用于SMC复合材料的前处理进行研究。
广义的破碎是指从外部施加压缩、打击、剪切、摩擦等力,使物体破碎、尺寸变小等操作的总称。从所得产品即粉碎后的粒度看,大致可以分为把大尺寸物体破碎到某种程度的粗碎,和破碎到所谓粉体状态的狭义的粉碎两类。但是,即使粉碎原理完全相同,由于设备大小不同,粉碎产物的粒度也不同。因此,明确区分各种概念非常困难。按照粉碎程度的不同可以把粉碎划分为粗碎、中碎、细碎,细碎可以进一步划分为微粉碎、超微粉碎、特超微粉碎。
用破碎机进行的破碎操作是用单独使用或组合使用压缩、冲击、剪断三种方法对被破碎物实施破碎操作。根据其作用力和构造的不同,破碎机种类繁多,有从岩石或塑料的破碎到塑料板或布的破碎等等种类,选择适应破碎废弃物的种类和量的机种非常重要。另外选定时,用机械厂家的实物机或试验机做试验试着进行破碎,根据实际使用情况,听取意见,充分调查其性能、安全性、消耗品的更换频率、破碎成本等非常重要。
(1)常温破碎
剪切破碎是靠固定刀和活动刀之间的啮合作用来剪切废物。刀间的啮合可以将废弃物切开或者割裂。冲击破碎是靠安装在中心轴上高速旋转的旋转刀的强有力的冲击作用破碎物体。经受一次冲击不能破碎的物体撞到固定刀上进一步破碎,撞击弹回的废弃物被挤压在旋转刀和固定刀之间靠剪切左右破碎。
(2)低温破碎
干式常温破碎具有噪音大、振动强、粉尘多、消耗动力大等缺点。为了解决这些问题,开发了冷冻低温破碎技术。利用材料在低温下能发生脆化、破碎容易等特点,对FRP废弃物进行低温破碎。与常温破碎相比,低温破碎具有如下特点:①不同材料的脆化温度不同,因此在操作温度相同的情况下,不同材料有不同的破碎程度。但是同一种材料破碎后的粒度非常均匀。②破碎后的形状适合进行下一步工作。
低温冷却的介质是液氮。液氮制冷温度低、无毒、无反应、无爆炸、资源丰富、但是液氮制冷需要消耗大量能量。能否有效益是低温破碎技术实用化的关键。目前,由于液氮费用昂贵,低温破碎的对象仅限于常温破碎困能的材料。
(3)破碎设备
适用于FRP废弃物的破碎机,按其作用力度的大小分,有压缩型破碎机、冲击型破碎机、切断型破碎机、压缩切断型破碎机、冲击切断型破碎机等等。常见的各种破碎机如表所示:

备注:1 A-C表示不同的施力方式
A:压缩(0-0.4m/s)
B:冲击(100-200m/s)
C:打击(0.7-8m/s)
2字母O代表此方式可行
3、SMC/BMC复合材料的再生利用
(1)热裂解产物的再生利用
SMC汽车研究协会指出:SMC经裂解后,再回收固体副产物,用作填料要比物理回收的成本还要低。并且热裂解法的最大的优点是适用于处理被污染的废弃物,例如处理经油漆、粘接或混杂材料的热固性复合材料部件,而且金属异物在热裂解后从固体副产物中除去。因此,热裂解法是最具开发应用前景的回收技术。
(a)裂解温度对SMC/BMC的热裂解过程的影响
在300、400、500、600和700℃下进行的热裂解所得产物由表给出。从中可以看出,在300℃式的热裂解是不完全的,因为这时的固体产物(82.6wt%)比理论值(72.6wt%)(由原材料成分分析得出)要高很多。相反的,400-700℃下的固体产物均几乎与理论值相当,所以,可以推断出全部的有机物质在高于400℃时都分解了。
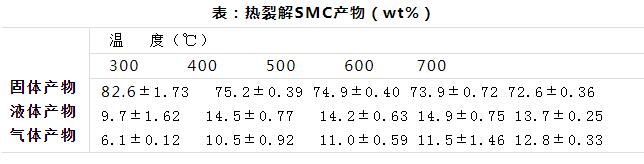
关于液体热裂解产物,从表可看出其产量从400-700℃范围内与温度无关,均约为14%,但在300℃却只得到相对少的液体产物(9.7wt%),这明显是由于在此温度下不完全热裂解造成的。由表3.28看出,从400-700℃,气体产物含量为10-12%,但在300℃热裂解产物中,由于不完全裂解,气体产物较少(6.1%)。
(b)SMC/BMC制品的热裂解产物资源化分析
a)热裂解液体产物的性质及应用
SMC热裂解液体产物是一种有机混合物,通常被称为油,并混有一些水相产物。在分析这种液体之前,先进行离心分离,以便将其中约4-6%的水分离出来,结果显示,产物中的水基本来自于原SMC料中的潮气。
经离心分离过的热裂解油经过了仔细的分析研究。在300、400、500、600和700℃的5个试验温度下所得SMC热裂解油的基本成分的H/C摩尔比和GCV值见表。由表可以看到,H/C比值相当低(1.1-1.3),这反映了液体的芳香特性,而较高的氧含量(10-16%)则来自于聚合物中的氧化结构。这些值在400-700℃之间亦基本不受温度影响,但在300℃时,H/C比值和氧含量均比在其他温度时高。
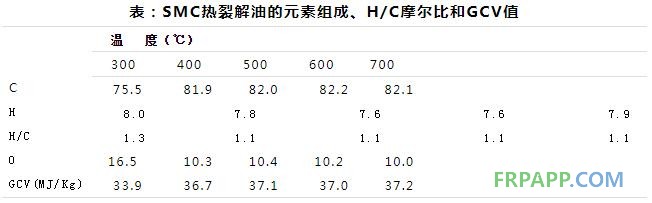
根据各温度下的热裂解油GC/MS分析,可以知道:(A)在各温度下所得的总油量估计约为73-76%。(B)各温度下所得的SMC热裂解油都是非常复杂的有机混合物。其主要成分含有5到21个碳,分子量在86到324之间。它包含了大量芳香物(64-68%)和大量氧化物(24-27%),如酮,羰基酸,烷基苯和芳基萘等。这些芳香和氧化物的出现是很合理的,因为被热裂解的SMC料是苯乙烯(芳香族的)交联的邻苯二甲酸的聚合物。相关报道指出,在一些较SMC低芳香性的聚合物材料(如橡胶)的热裂解试验中,所得的油也具有很强的芳香性,这是由于脂肪和芳香族物质的再结合反应以及脂肪族的环化反应造成的。(C)至于温度对油的组成成分的影响,由分析从400到700℃的色谱图是非常相似的,它们包含几乎相同的峰,因此它们包含了相同的主要成分。而300℃是的色谱图则相对简单些,它含有较少的峰,因此300℃时只有13种成分,而在较高的温度有20-25种成分。
在各温度下得到的热裂解油与商业1号燃料油(ASTM240)的GCV值都相当接近,并且,由于这些油不含污染元素,因此可以用作相当好的液体加热燃料。
b)热裂解气体产物的性质应用
SMC/BMC热裂解气体产物中含有丰富的CO和CO2,这些碳氧化物是由SMC中聚合物的酯健断裂分解得到的。由Kominsky所作热裂解试验中(使用了相同的聚合物材料)所得到的气体也含有大量的CO和CO2(分别为54.2%和34%)。由于CO2在SMC裂解气体产物中的高含量,其GCV值很低(14-16MJ/Kg);。由表可知,400℃以上,影响可以忽略,但在300℃时,产生了比更高温度时更多的CO和较少的CO2,因此300℃使得气体产物的GCV值更高。热裂解工艺过程中所产生的气体产物一般可循环利用于生产过程中所需要的热量。
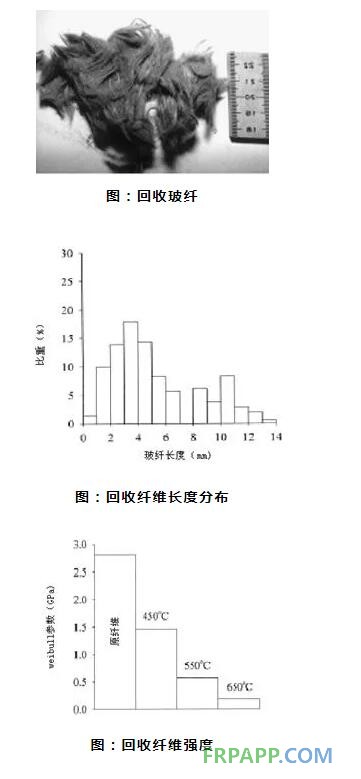
加热对回收的纤维的杨氏模量没有显著影响。原始的纤维和回收的纤维模量都约为70GPa。由于回收短纤维制备的复合材料潜在应用价值主要对硬度要求较高,而不是强度,这个结果令人十分满意。
▶回收玻纤的应用
回收的纤维最直接的再利用是以不连续纤维形式(如模压料或表面纱)为基础的半成品材料。从回收的纤维的含量高达50%的样品观察来看,其拉伸、弹性及冲击性能均没有显著影响。但是,若替代品超过50%,拉伸、弹性及Charpy冲击强度都显著下降。由上述单纤维测试发现,回收纤维的含量不影响模量。作为轻质替代品如汽车头灯外壳和仪表板等,为其提供了商业应用的光明前景。一些技术人员正在研究基于专用DMC组分配方的小型头灯的制造(如图所示),其组分为不饱和聚酯树脂,Al(OH)3填料和重18%的无碱玻纤(50%6mm原始短切纤维束和50%这种工艺回收的纤维)。BMC用普通方法制造,必须组分配方和工艺没有变化。含有回收的纤维的组分配方与常规混合物没有不同,模塑部分产生表面涂层(表面处理剂)适合镀银金。用回收纤维制的BMC机械性质与控制的没有显著不同,尽管冲击强度稍有下降,但电性能没有改变。
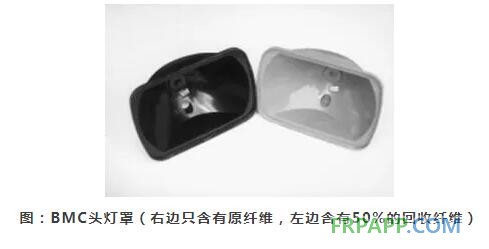
▶回收填料的应用
回收的填料主要成分为CaCO3。在300℃时,热裂解固体残留物中仍有有机物存在,但在400-700℃下有机物分解完全,固体中主要是玻纤和CaCO3,并且含有约4%的类似焦炭的含碳产物。研究还表明在600和700℃进行的热裂解试验中,原来SMC中的一部分CaCO3分解成CO2和CaO。这种分解对固体残留物在复合材料中的回收利用是很有害的,因为金属氧化物有增稠的作用,所以会影响复合材料的成型工艺过程。作为填料,回收填料可以替代50%的碳酸钙。用回收填料制备的SMC平板的性能与常规SMC配方基本相同。其物理性能和外观质量见表:
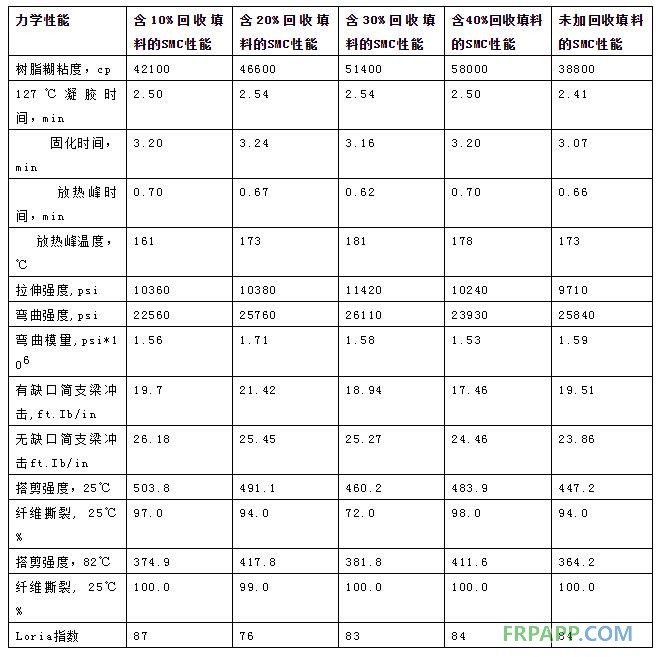
通用汽车公司于1993年在Chevrolet Corvette的内仪表板上应用了回收的复合材料填料,这成为了北美首家在汽车上利用回收SMC的汽车厂。1995年,克莱斯勒公司率先在Dodge Ram货车的整个车身材料中使用回收填料并将填料用在了Neon客车的阻流板上
福特汽车公司在Econoline货车引擎盖上,Ranger小型轻便卡车的格栅开启型仪表板和Aerostar小型货车引擎盖内仪表板中都使用了回收填料。这也是一个在福特网络内收集成型后废料的较好的方法。另外,在欧洲有三种汽车部件产品含有回收的SMC填料(Audi 的备用胎架、VWPolo发动机舱和VM Passat 的前面板)。在日本,Toyota CALIB的行李架的内舱用回收的复合填料。
到1995年末,汽车工业共计使用4百万lbs以上的回收复合材料填料。而当年的目标是将约为750万lbs的废料全部用完。1994年,使用回收填料的SMC占总生产量的3%。随着需求的增长,对SMC回收利用的要求也越来越大。
▶粉碎物的再生利用
粉碎法是目前国外普遍采用的SMC回收方法。根据处理方式和程度的不同,粉碎回收料可以是粗颗粒的粒料、细颗粒的粒料、一定品质的纤维。这些回收料的用途主要取决于粒料的粒径分布及纤维的完整性。如粒度达到25×25mm的SMC大块碎块可以用于制作胶合板、轻质水泥板、和保温材料等材料。而粒度在3.2mm~9.5mm的碎料可以用在屋顶沥青、BMC混凝土骨料、聚合物混凝土及路面材料中做增强材料或者填料;而充分细碎的颗粒其粒度大约有60μm甚至更细,可以用在SMC、BMC或者热塑性塑料中为填料。
SMC粉碎后在SMC中替代碳酸钙作为填料使用是SMC粉碎回收最主要和最重要的应用。试验证明,SMC废弃物回收粗粉碎粒料用于BMC,用量可达50%;粉料用于SMC,用量可达30%;以SMC废弃物灰色粉料为例,全部取代CaCO3和玻纤制得的BMC制品力学性能是标准BMC的70%,而充模性能提高50%-100%,密度下降15%以上。用于BMC的粗粉碎料中的纤维较标准BMC中的纤维的增强效果差。
SMC废弃物回收粉料用于BMC、SMC材料性能见以下两表。从中可以看出:回收料在BMC和SMC中用量分别达到50%和30%时,对材料的机械性能影响不大,但却使材料比重下降较大,可制得轻质产品
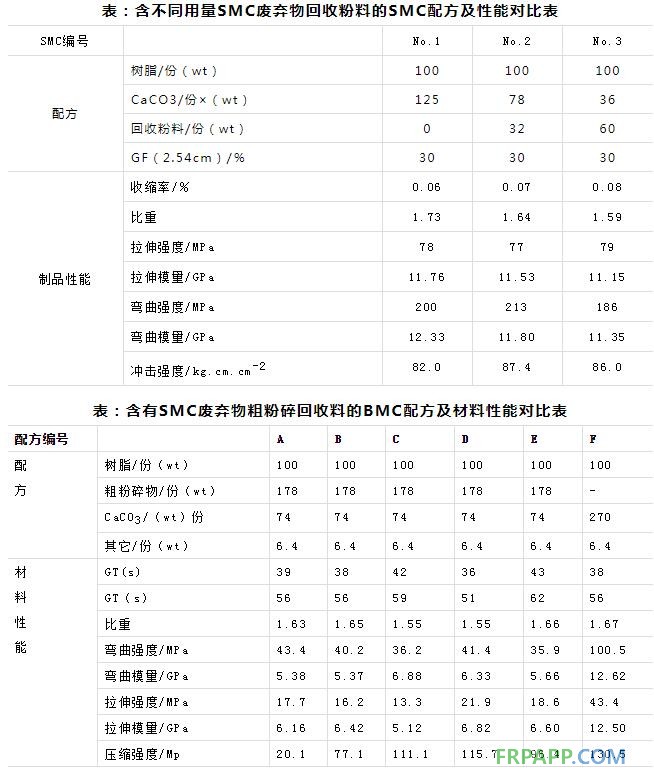