缠绕工艺制造的管、罐等产品结构大体分为3层:内衬层、结构层和外保护层。
(1)内衬层。内衬层是制品直接与介质接触的那层,它主要作用是防腐、防渗、耐温。因此,要求内衬材料具有优良的气密性、耐腐蚀性,并且耐一定温度等。
内衬材料有金属、橡胶、塑料、玻璃钢等不同材质。根据不同用途与生产工艺要求来选定,作为化工防腐用时,则玻璃钢内衬是最佳选择。这样即可避免粗而重的金属制品,又可避免内衬层与结构层之间粘接的麻烦。并且,这种玻璃钢内衬适应性强。通过改变内衬材料的种类、配方,使之在可以满足化工防腐上各种不同工艺的要求。根据容器内所贮存介质的种类、浓度和温度等技术要求选择内衬材料。
(2)结构层。结构层又称为增强层。它的作用主要是保证产品在受力的情况下,具有足够的强度、刚度和稳定性。而增强材料——玻璃纤维则是主要的承载体,树脂只是对纤维起粘接作用,并在纤维之间起着分布和传递载荷的作用。因此选择高强度、高弹性的增强材料和性能良好的树脂是提高结构层承载能力的重要因素。这对航空及军用产品尤为重要。对于普通工业防腐及民用产品,在保证产品具有足够的承载能力的前提下,还要从经济成本、工艺性能等因素综合考虑,选择增强纤维和树脂。
另外,结构层的承载能力还要受到纤维缠绕方向的影响,要求增强层在不同方向上具有不同的强度。这时,可以通过结构计算确定缠绕角。例如,对内压容器,确定合适缠绕角,使环向强度与轴向强度相比,近似等于内压载荷所引起的环向应力和轴向应力之比。目前,采用最多的纤维铺设方式有螺旋缠绕和环向缠绕两种,有时可将这两种铺设方式进行组合,使螺旋方向缠绕承受轴向应力,环向缠绕则主要承受环向应力。试验研究表明,对于内压圆筒型容器,组合缠绕型比单一螺旋缠绕更有效;而对于外压圆筒型容器,加筋是加强层提高承载能力的一种结构形式,例如:地下管道、贮罐采用加筋形式会更有效地抵抗由土壤所产生的压力(外压力)所引起的变形和翘曲。
随着复合材料技术的不断发展,采用夹层结构(如:夹砂层)纤维缠绕可有效提高玻璃钢管的刚度,夹层结构管材的强度高、刚度大、重量轻、造价低、使用寿命长、耐腐蚀、无毒无味等特性,优于传统的钢管、预应力水泥管、铸造管等。随着夹层结构管技术的发展,夹砂(石英砂)纤维缠绕玻璃钢管材正逐步取代传统的输水管材。如河北中意玻璃钢有限公司生产的玻璃钢贮罐、工艺管和夹砂纤维缠绕管等产品。
(3)外保护层。一般情况下为了延长玻璃钢制品的使用寿命,不仅要求内衬防腐性能好,加强层具有足够的承载能力,而且要求产品外表面也应具有一定的防护性能,特别是对于露天的设备。对于安装在室外的玻璃钢制品,间苯二酸型或双酚A型树脂中加入石蜡,就足以保护制品8~10年。由于紫外线光可损害聚酯树脂,因此当采用聚酯树脂时宜添加紫外光吸收剂,可以将紫外光转变成热能或次级辐射出去,大大降低产品变黄的速度,提高透光率,从而提高玻璃钢的耐候性。一般情况下要严格限制这类材料的使用,必须使用时,要尽可能地使其价格和对聚酯树脂改变的性能减至最小。紫外线吸收剂的使用量(按树脂质量计)为:0.2%~0.5%。
二、缠绕制品的应用
由于缠绕玻璃钢制品具有上述各特点,因此,在化工、食品酿造业、运输业及军工等方面获得比较广泛的应用。
1. 管道
纤维缠绕管道制品因其强度高、整体性好、综合性能优异、容易实现高效的工业化生产,综合运营成本较低而被广泛地应用于炼油厂管道、石油化工防腐管道、输水管道、天然气管道和固体颗粒(如粉煤灰和矿物)输送管道等方面,如图下图所示。
目前,美国各地用的纤维缠绕管道总长占整个运输工具的三分之一,所负担供应的能量(包括石油、天然气、煤、电)占全国需用量的一半以上。在我国工业生产中,纤维缠绕管道同样已被大量地采用。图7-35为新疆某输水重点工程成功采用的Ø3.1m玻璃钢管,单管长12m,重16吨,工程一次安装通水成功无泄漏。
2006年北京高碑店电厂烟塔合一除硫系统中,烟气管道采用ECR纤维增强乙烯基酯树脂制作的玻璃钢管,直径达7m(如下图所示),以立式缠绕机与卧式缠绕机现场制造,质量甚得好评。
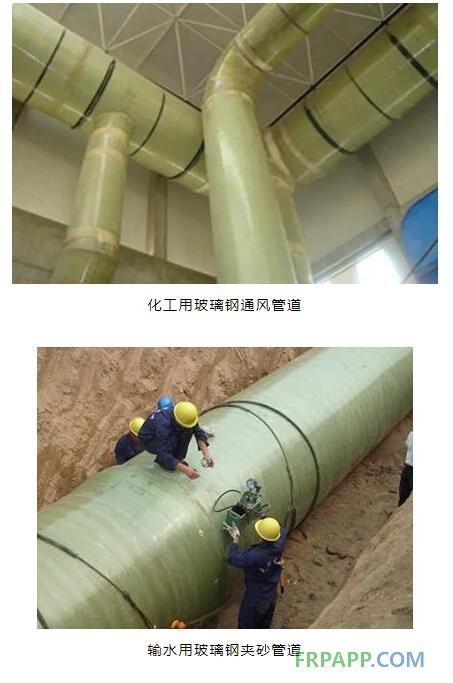
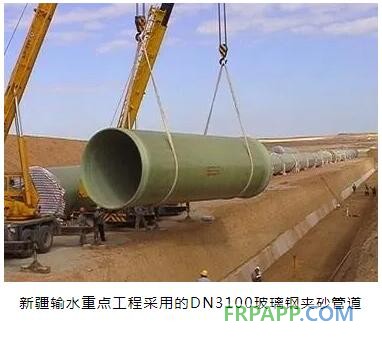
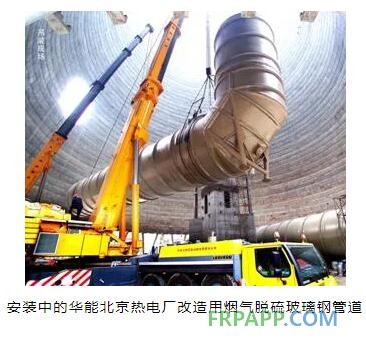
纤维缠绕管道在我国市场需求量巨大、前景广阔,尤其表现在油田应用方面,如:
(1)大庆油田每年新增油水井2500多口(2005年5000口),管道总需求2000km,其中高压注水管道为500 km,油田改造项目计划需油田管线为1000 km左右,以每公里管线工程费用15万元计算,大庆油田每年用于管道的工程费用可达3亿元以上;
(2)吉林油田每年管道需求在1000km左右。其中高压玻璃钢管道在500km以上;
(3)辽河油田每年管道总需求为1800 km左右,其中高压注水管为600 km以上;
(4)胜利油田每年管道总需求2200 km,其中高压注水管为1000 km以上;
(5)大港、华北、中原、江汉、江苏、新疆、青海、长庆等其他油田的高压玻璃钢管材的需求量也逐年增加,全国每年油田系统的玻璃钢管材的总需求量可达6000 km以上,工程投资可达9亿元以上,其中70%以上的管线可由高压玻璃钢管道替代。
另外具有强劲市场态势的井下油管,其市场需求量比高压玻璃钢地面管线管更大。
2. 储罐
储运化工腐蚀液体,如碱类、盐类、酸类等,采用钢罐很容易腐烂渗漏,使用期限很短。改用不锈钢成本较高,效果也不及复合材料。采用纤维缠绕地下石油储罐,可防止石油泄漏,保护水源。用纤维缠绕工艺制成的双层壁复合材料储罐和管道,已在加油站获得广泛应用。
这类储罐和管道通常用E玻璃纤维/不饱和聚酯树脂制成,在制造过程中可通过加入石英砂或其它填料来提高刚度,降低制造成本。图即为化工用的大直径玻璃钢储罐。
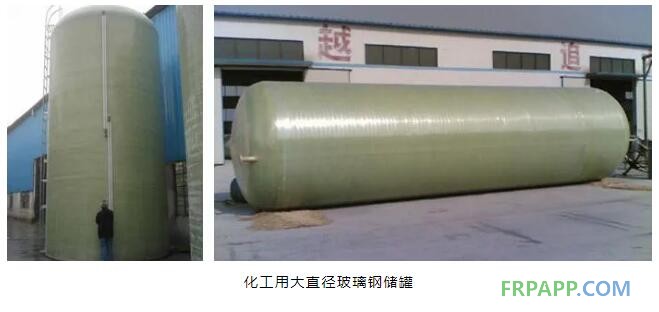
3. 压力制品
纤维缠绕工艺可用于制造承受压力(内压、外压或两者兼俱)的压力容器(包括球形容器)和压力管道制品(如图7-38所示)。缠绕压力容器多用于军工方面,如固体火箭发动机壳体、液体火箭发动机壳体、压力容器、深水外压壳体等。缠绕压力管道可充装液体和气体在一定压力作用下不渗漏、不破坏,如海水淡化反渗透管和火箭发射管等。先进复合材料的优异特性使纤维缠绕工艺制备的多种规格火箭发动机壳体和燃料储箱得到成功的应用,成为现在乃至将来发动机发展的主方向,它们包括小到直径只有几厘米的调姿发动机壳体,大到直径3米的大型运输火箭的发动机壳体,如下图所示。
纤维缠绕复合材料压力容器已在航空、航天、造船等领域获得广泛应用。用碳纤维和芳纶纤维缠绕的薄壁金属内衬高压容器以其高结构效率、高性价比优势成为航天飞机和人造地球卫星的首选。所用的内衬材料包括不锈钢、钛合金、铝合金和热塑性塑料等。容器充装的介质有氮气、氧气、氢气和氦气,形状多为环形、球形(如图所示)和扁椭球形,直径范围从0.3~1.01米。
小型压力容器已在个人生命保障系统获得成功应用。属于这类用途的容器有消防员供氧器(如图7-41所示)、登山队员的供氧器等。这类容器大多用芳纶纤维/环氧树脂或玻璃纤维/环氧树脂制成,具有重量轻、便于携带、高疲劳寿命和高可靠性的综合特性。纤维缠绕工艺制造的压缩天然气(CNG)气瓶如图所示,已经成为标志性的新型能源载体。
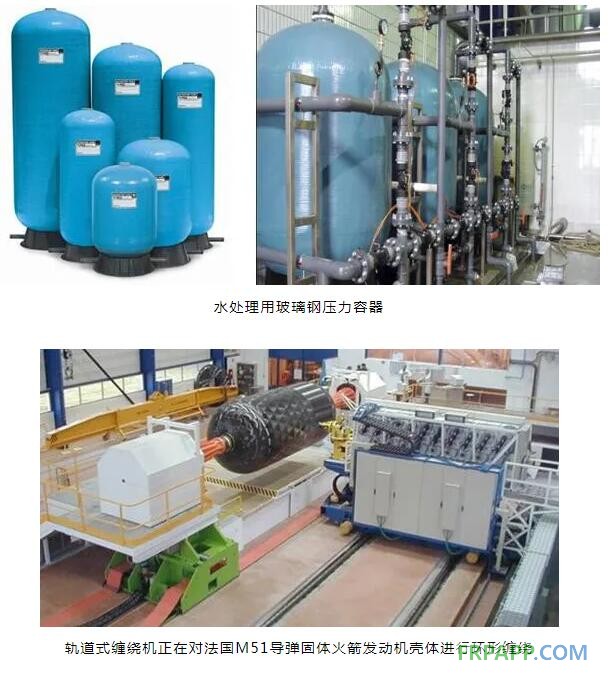
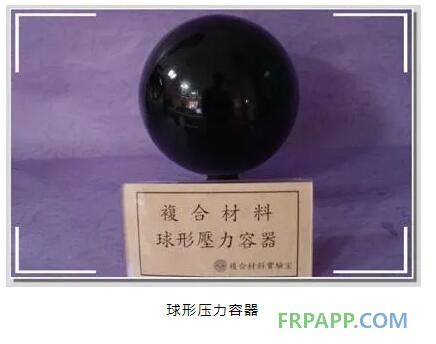
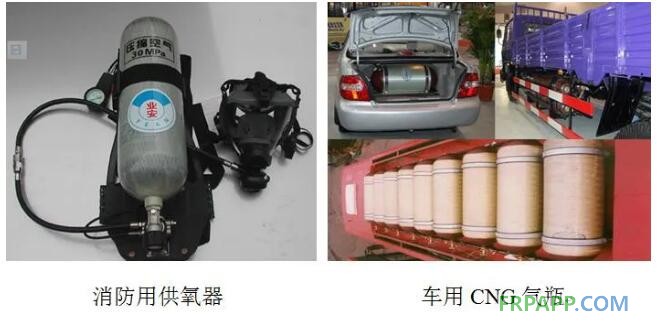
1986年至今,我国已生产玻璃钢/复合材料呼吸气瓶、CNG(压缩天然气)瓶和燃料电池用氢气瓶等超过15万只。1997年我自主研发的环形压力容器投入使用。2006年我引进德国技术装备(内衬制造、纤维缠绕),在苏州建立年产能达11万只复合材料气瓶的生产基地。中材科技(苏州)公司生产的复合材料气瓶已成为全球四大品牌之一。
4.其他
在机械工程上有时需要轻质高强的部件如新型无梭纺织机上的剑杆,是代替“梭子”穿线的,来回往复速度快,要求轻质、高强、刚度大,在此方面纤维缠绕工艺制备的碳纤维/环氧复合材料管具有其它材料无法比拟的优势。
复合材料转动轴如图所示,是为宇航工业提出并得到应用的,主要用于直升飞机,如尾旋翼长套轴、主旋翼厚壁转动轴等。1986年冷却塔工业开始采用复合材料转动轴,这种传动轴的主要优点为耐腐蚀、重量轻、振动小、寿命长。
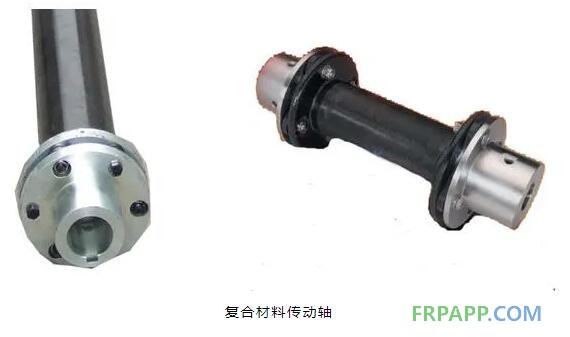
电气设备中的开关装置、高压熔断器管、回路断路器及高压绝缘体等均可采用纤维缠绕工艺制造,在这些制品中纤维缠绕复合材料爆破强度高,电绝缘性能好的特点得到充分的发挥。此外大型电机上的绑环和护环、车用飞轮转子等也是纤维缠绕复合材料制造的,其比强度高、线膨胀系数小、蠕变率低,绝缘性能良好,非磁性和性价比远优于无磁钢。
纤维缠绕复合材料在电气工程上应用很广,可用纤维缠绕技术制造输配电电线杆、天线杆及工程车臂杆等。
纤维缠绕制品在体育器材方面的应用,会使竞技体育提高到一个新的水平,所以发达国家在这方面均有大量人力与资金的投入。如纤维缠绕高尔夫球拍杆、滑雪杖、羽毛球杆、猎枪管均可采用碳纤维/环氧复合材料制造,如图所示。
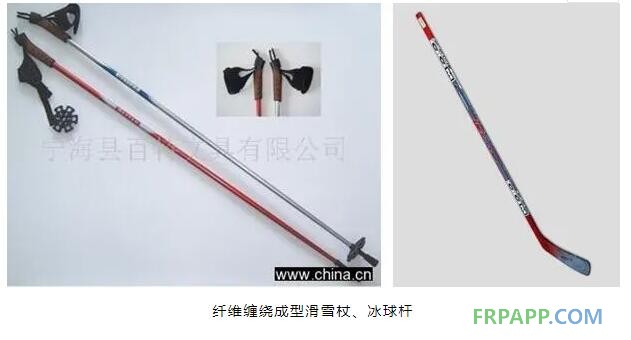
三、典型缠绕制品
1. 大直径储罐
自20世纪80年代以来,具有轻质高强和耐腐蚀等特点的玻璃钢储罐在我国石油、化工、冶金、酿造、环保和医药等领域获得越来越多的应用。最初由于成型工艺和交通运输等方面的原因,玻璃钢储罐直径一般小于4m。近些年来,随着我国经济的持续增长,市场上对大直径储罐的需求量迅速增加:
(1)油田方面
国内几个大油田如大庆油田、胜利油田和江汉油田等均使用了大直径玻璃钢储罐。以大庆油田为例,该油田仅在1995年一年内至少使用了2台直径10m、2台直径7.5m和7台直径5.5m的大直径玻璃钢储罐。目前该油田大直径玻璃钢储罐的使用量已有几十台,最大直径达10m。2006年11月,在中原油田采油二厂濮三污水站水质治理改造工程中建成300m3缓冲罐2座,1000 m3 收油罐2座,采用以机械缠绕为主、手工糊制为辅的制造工艺,主体设备在现场制作。
(2)化工领域
化工领域是大直径玻璃钢储罐的另一个重要的应用领域。国内一些大的化工企业,如云天化工集团、锦州化工集团和苏州化工集团等单位均在其技改中选用了大直径玻璃钢储罐。其中,苏州精细化工厂使用的直径11m的玻璃钢储罐据称为国内在用的最大直径的缠绕成型玻璃钢储罐。
(3)冶金行业
冶金行业是大直径玻璃钢储罐的又一个重要应用领域,如1995年铜陵有色公司选用的填料塔、空塔沉降槽及填料塔沉降槽,1996年铜陵金属工程公司选用的一级动力波、气体洗涤塔和二级动力波等设备均为大直径玻璃钢储罐制作而成。
目前缠绕玻璃钢储罐可达的最大直径为25m,以储存2.5万吨原油计算,储罐的高度达63.7m,因此多采用立式、现场缠绕成型。
在立式缠绕中,模具放置在托架上保持模具表面与地平面垂直,通过几个可伸缩的悬臂将托架固定在模具中央一个大的轴承上,此轴承由液压驱动,通过管线与模具旁不远处的一个液压泵相连。缠绕小车轨道垂直立于模具旁,整个装置由微机控制,缠绕时,模具水平旋转,小车在轨道上上下运动,利用二者之间的相对运动完成缠绕。通过计算机控制程序输入不同的缠绕角,即可控制模具旋转与小车运动之间的相对速度,从而分别实现螺旋或环向缠绕。立式缠绕的最大特点是:由于可伸缩悬臂的长度具有可调性,所以,和其他方法相比,它可生产出更大直径范围的玻璃钢储罐。利用此法缠绕出直径为25m的玻璃钢储罐,为世界上最大直径的缠绕成型玻璃钢储罐。
为克服产品的运输问题,大直径储罐多采用现场缠绕(如图所示),即将玻璃钢储罐的生产设备拆成若干部分,连同原材料一起运至现场,再将设备拼装起来,进行生产。此法优点是可克服交通条件给大直径玻璃钢储罐运输带来的制约。
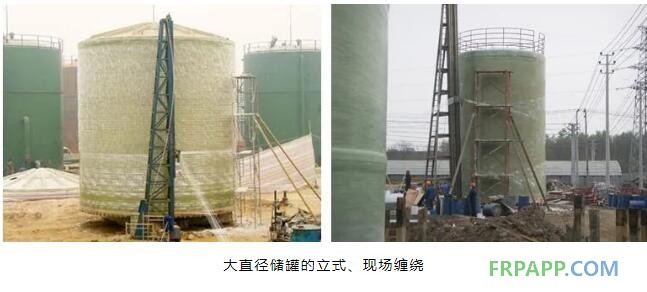
在结构设计方面,立式储罐罐体的不同高度受静压不同,因此不同高度的罐壁可具有不同的厚度。为节省材料、降低成本,罐体壁厚多采用上薄下厚的结构形式,并综合各种不同的影响因素,其中重点考虑风压及震载的影响,编制计算机程序进行运算。
在铺层设计方面,玻璃钢储罐罐壁一般由以下3层组成:
(1)内层
内层由富树脂层及中间层组成。富树脂层由内衬树脂加有机纤维聚酯毡增强,树脂含量90 %以上,厚度控制在0.5mm左右,主要提供制品的耐腐蚀性和防渗透能力。中间层由内衬树脂和无碱玻璃纤维喷射纱组成,树脂含量控制在70 %~80 %,厚度控制在2mm左右,主要是保护富树脂层,提高内层的抗内压失效能力,阻止裂纹扩散。
(2)结构层
结构层即增强层,采用无捻玻璃纤维粗纱和玻璃织物(或短切纤维毡) 增强,承受拉应力、压应力和各种外载荷,保护内层。结构层的最内层设计为环向层,因为其不仅容易铺垫在最里层,而且容易通过调整往复行程的距离来满足各分段不同壁厚的要求;结构层的中间层设计为大角度纵向层,以抵抗运输、安装、风载和地震等诸多复杂工况下产生的纵向应力;结构层的最外层设计为环向层,以使整个结构层形成“反对称”的结构形式,避免拉弯耦合效应。结构层的厚度按静液压、风载和震载等载荷条件计算确定,树脂含量控制在30 %~40 %。
(3)外层
外层即外富树脂层,树脂含量大于90 %,厚度控制在1.5mm左右。采用玻璃纤维表面毡增强,也可采用0.1~0.2mm薄玻璃带增强,同时在树脂中加入紫外线吸收剂以防止老化。该层主要是保护外壁不受外界机械损伤和防紫外线老化。
在选择原材料时,玻璃钢储罐坚持质量优先、兼顾价格的原则,由于各层的作用不同,在材料选用上各有不同:内衬层直接与介质接触,其材料选择对控制缠储罐的渗漏起关键作用,储存酸性介质通常选用乙烯基树脂,储存碱性介质采用双酚A型树脂,如197#树脂,要求储罐耐水则采用如189#树脂,要求储罐耐碱、耐水采用无碱玻纤,耐酸用中碱玻纤,内衬则采用表面毡、短切毡共同增强,以便提高含胶量,增强抗渗能力;结构层主要满足储罐的强度及刚度要求,选材应充分考虑所选树脂基体必须与缠绕用玻纤有良好的浸润性,以便形成致密的结构;外表面与外界环境直接接触,按耐老化要求选材。
在成型工艺方面,储罐壁成型时制造圆柱形带封头的模具,分以下四步进行:
(1)手糊成型内层中的富树脂层;
(2)喷射成型内层中的中间层;
(3)立式缠绕成型结构层;
(4)手糊成型外层。
储罐制造完毕后,须对罐体进行气检,检查其强度、刚度及密封性。若储罐存在气眼、气孔等缺陷,充气气压将无法保证,则须查找缺陷处,然后及时采取措施处理。
2. 反渗透膜壳
反渗透是用足够的压力使溶液中的溶剂(一般常指水)通过反渗透膜(一种半透膜)而分离出来,方向与渗透方向相反,可使用大于渗透压的反渗透法进行分离、提纯和浓缩溶液。利用反渗透技术可以有效的去除水中的溶解盐、胶体,细菌、病毒、细菌内毒素和大部分有机物等杂质。反渗透膜的主要分离对象是溶液中的离子范围,无需化学品及可有效脱除水中盐份,系统除盐率一般为98%以上。所以反渗透是最先进的也是最节能、环保的一种脱盐方式,也已成为了主流的预脱盐工艺。反渗透技术的应用范围包括:
▶制药、医药行业无菌、无热源纯化水制取;
▶电子、电力行业用超纯水;
▶生物医药用水;
▶化工、化妆品配料用水;
▶苦咸水、海水淡化;
▶电镀涂装行业所用溶液配给,零件清漂洗;
▶精密机械、特种材料,光电材料,石英制品行业用的清洗,配给,冷却水;
▶饮用纯净水、食品饮料用水。
反渗透膜壳是反渗透设备的重要组成部分,用以承受膜法分离提纯时施加的压力,最初多为不锈钢材质,随着纤维缠绕工艺水平的提高,玻璃钢膜壳的应用越来越广,其特性优点包括:
(1)基于复合材料结构的可设计性,可以通过改变玻璃纤维的含量和分布,在一定范围内获得不同强度和弹性性能的玻璃钢膜壳,以承受不同的载荷。如对于双向受力的结构,可以考虑双向铺层或多向铺层的方式,选用适当的纤维用量或改变各单层的铺层方向,以满足结构性能要求,实现容器在工作压力条件下处于最佳的受力状态,充分发挥制品的结构性能,真正体现出“轻质高强”这一概念。
(2)纤维缠绕具有良好的工艺性,可根据产品的尺寸、形状和结构特性等进行综合设计,以最大限度地减少成型、加工次数或只需一次成型即可,缩短生产周期,减少能源消耗。
(3)在室温条件下,玻璃钢的导热系数一般在0.15-0.36w(m.k)范围内,大约仅是金属材料的1/100-1/1000,其绝热性能是金属材料所无法比拟的,这一特性使得玻璃钢膜壳能对反渗透膜起到良好的温度变化保护作用。
(4)玻璃钢膜壳具有突出的耐腐蚀性,通过合理的选材和适当的工艺,玻璃钢不仅对多种低浓度的酸、碱、盐介质及溶剂有良好的稳定性,而且有良好的抗大气、海水和微生物的性能。
目前国内已有多家玻璃钢反渗透膜壳的生产厂家,哈尔滨乐普等国产膜壳的质量和技术已达到国际先进水平、进军国际市场,如图所示。
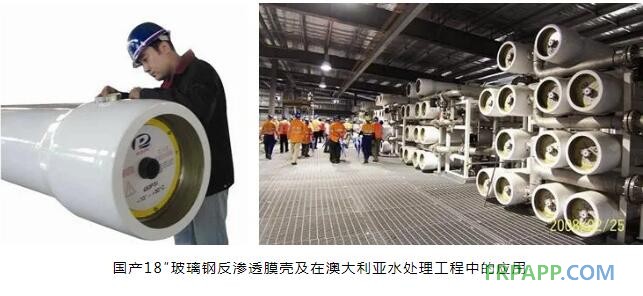
3. CNG气瓶
随着世界经济的发展,全世界的汽车产量和汽车保有量都在不断增加,依据国外1994年的研究报告及世界上石油的蕴藏资源和消耗量的预测,到21世纪中叶,汽车以石油作燃料的时代将会结束。天然气作为汽车燃料是一种燃烧干净、价格便宜而又使用安全的气体,因而发展燃气汽车成为未来重要的发展方向。燃气汽车的重要和关键零部件之一是CNG气瓶,这类气瓶综合了复合材料的高比强度、可设计性以及内衬的良好气密性、优良的耐蚀性等诸多优点,使其达到高承压能力、高疲劳寿命、质轻、耐腐等优良性能的完美结合,这也使得对复合材料CNG气瓶的研制开发成为国内外的一大热点。
在同样容积和压力下,复合材料CNG气瓶比钢质气瓶的重量可减轻1/3~2/3,二者相比较,显然复合材料CNG气瓶在汽车运行节能上更具有优势;同时复合材料在受到撞击或高速冲击发生破坏时,不会产生具有危险性的碎片,从而降低或避免了对人员和车辆的损害。
近年来,随着复合材料成本的降低,成型工艺的不断改进,使得复合材料CNG气瓶在国内外倍受青睐,尤其在轿车和轻型车上的应用极具竞争力。复合材料CNG气瓶是先通过拉伸、旋压等工艺制成铝胆,并在铝胆外采用高强度纤维缠绕。国外已经用它来取代钢制气瓶。1994年我开始开发CNG气瓶,并首先在首都公交车上装车使用(一辆车用90升气瓶9只),目前北京已成为世界城市中以CNG为动力的公共汽车拥有量最多的城市。
由于复合材料气瓶采用不同的材料制成,在荷载作用下,表现出的应力状态不同:铝胆为弹塑性材料,而外部的纤维一般采用高强度纤维及碳纤维、环氧树脂、有机纤维、环气树脂等缠绕而成,具有比强度大,比刚度高等诸多优点,如碳纤维T300/环氧5208的比强度是铝的6.3倍,比刚度是铝的4.16倍。对于这种基底为塑性、表面采用脆性的纤维来增强的复合材料,基体的破坏应变通常比纤维的破坏应变高得多,往往在基体进入塑性状态时,外部纤维材料仍处于弹性状态。从失效方式上看,复合材料瓶体的失效往往是铝胆先出现龟裂,铝胆的开裂使气瓶漏气是复合气瓶早期破坏的主要原因之一。另外,纤维与基体复合后,会改变它们原有的强度性能,如纤维与基体粘牢后的,即使某一纤维断裂,也只影响局部应力分布。图7-47即为CNG气瓶在汽车上的应用。
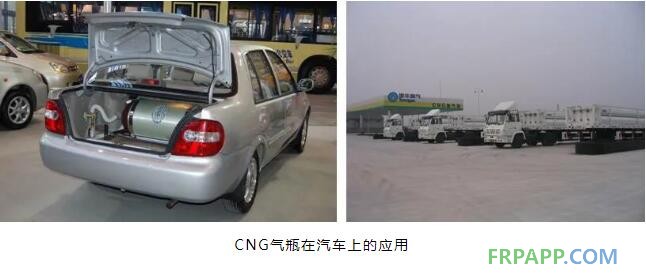
4. 夹砂管道
纵观我国玻璃钢夹砂管及设备的发展历程,在16年来的不断探索、研制和开发过程中,得到了飞快的发展。
(1)第一代加砂工艺:从国外引进的上加砂,兜砂纸兜砂
从1993年开始,以引进意大利加砂工艺和设备为主,这种工艺和设备是由模具上方通过皮带输送机将石英砂洒落到模具上方,用兜砂纸将石英砂兜住,靠淋胶头向石英砂外层淋树脂,不加滚压,如图所示。
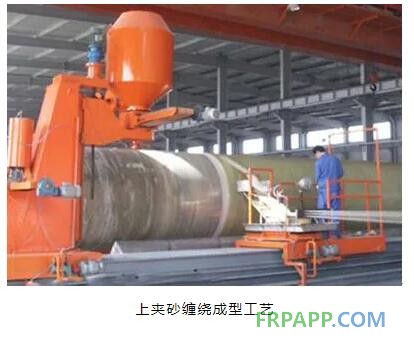
这种工艺和设备的缺点主要有三点:1、由于兜砂纸强度低,张力小,石英砂层无法施加滚压,因而石英砂层密实度低、气孔多、刚度差、树脂含量高,造成质量不稳定,成本高;2、由于兜砂纸强度低,对树脂浸透能力差加之设备输胶能力不够,造成每次加砂层的厚度不能超过3一5mm,生产效率低;3、石英砂是以自由落体形式洒落到模具上方,洒落过程中产生大量粉尘,如模具稍有偏心或转速不均,落到模具上的石英砂厚度就厚薄不均,夹砂管外表面不可能平整。
(2)第二代加砂工艺:国内企业改进的上加砂,兜砂布兜砂
起于90年代末,为克服第一代加砂设备和工艺的缺点,在设备构造和材料上作了大量尝试和改进:1、采用大流量输胶系统,并经改进后将树脂喷淋到石英砂里层,树脂通过挤压从里向外渗透,减少了树脂用量和损耗,降低了成本;2、增加了机械液压装置,提高了石英砂的密实度和管道的刚度及表面平整度;3、采用高强度兜砂布,使一次夹砂层厚度提高到6-8mm,提高了生产效率。缺点是:加砂工作面高、操作不方便、粉尘较大,仍存在加砂层厚度不均现象,生产效率不高。
(3)第三代加砂工艺:下加砂和分层淋料下加砂(图),兜砂布兜砂
2000年下半年研制,这种工艺是在缠绕工作台的对面通过一套下加砂装置将石英砂预浸上树脂,以静态方式,始终跟模具同步的转速把石英砂用兜砂布从模具下方紧紧裹到管芯模上,树脂通过从上到下水平振动、从里向外挤压渗透,渗透中利用了离心力作用,加快了树脂渗透速度,提高了树脂分散均匀性,生产过程机械化,不抛洒,粉尘小,树脂含量低,厚度均匀、平整度好。但为达到管道的质量稳定,需把夹砂层内的树脂含量控制在20%以上才能使管道的力学指标稳定,管道成本降不下来。
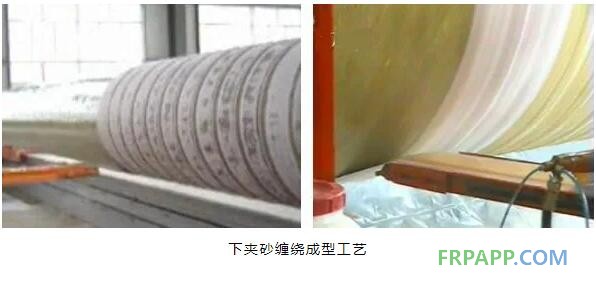
(4)第四代加砂工艺:湿法搅拌下加砂
2004年由衡水华成玻璃钢有限公司研制成功,有自主知识产权。这种工艺是用加砂装置将石英砂和树脂搅拌均匀,通过输砂平台,用兜砂布把石英砂从模具下方紧紧裹到管芯模上,通过机械碾压装置对夹砂层进行同步碾压。这种工艺的优势有以下几方面:
①加砂前预先搅拌砂浆,可以精确控制夹砂层的树脂含量,控制成本;
②生产效率高,加砂与碾压、环向纤维缠绕可同步进行;
③加砂层气孔非常少,夹砂层的密实度和平整性很好,力学性能高(弹性模量高);
④加砂厚度可控制,一次加砂厚度为5-30mm,可精确控制;
⑤在保证管道质量的前提下,大大降低了管道原材料成本。