2.1BMC模压成型工艺
2.1.1模压成型的优缺点:
模压成型工艺是复合材料生产中最古老而又富有无限活力的一种成型方法。它是将一定量的预混料或预浸料加入金属对模内,经加热、加压固化成型的方法[17~18]。
模压成型工艺的主要优点:
①生产效率高,便于实现专业化和自动化生产;
②产品尺寸精度高,重复性好;
③表面光洁,无需二次修饰;
④能一次成型结构复杂的制品;
⑤因为批量生产,价格相对低廉。
模压成型的不足之处在于模具制造复杂,投资较大,加上受压机限制,最适合于批量生产中小型复合材料制品。随着金属加工技术、压机制造水平及合成树脂工艺性能的不断改进和发展,压机吨位和台面尺寸不断增大,模压料的成型温度和压力也相对降低,使得模压成型制品的尺寸逐步向大型化发展,目前已能生产大型汽车部件、浴盆、整体卫生间组件等[28]。
2.1.2模压成型工艺过程
(1)物料的准备与加料
BMC一般有两种形态,一类为块(团)状模塑料(块状BMC),一类为散状模塑料(散状BMC)。一般在BMC生产的最后阶段,为了便于处理和以后的操作,通常都有一专门的设备挤压成绳条状、木节状或弹丸状。而当BMC配方中纤维含量较高时,其松散性也增加。很难做成致密的规则形状,这类材料一般都采用人工称量加料。而对于挤压成的块状模塑料则可以实现比较准确的、方便的甚至是自动化的加料方式。但是,使用挤压料坯时应注意到混合物的紧密压缩会降低其贮存寿命。这一点可能与松散的BMC内夹杂空气,抑制其聚合反应有关。同时,空气也可以带走料团内部少量之聚合热[6]。
散状BMC,由于体积比较大,需采用具有较大装料室的模具。散状材料中易滞留空气,容易在成型制品中出现多孔区或气泡。为防止这类瑕疵的出现,可用手预先挤压料团,使其成一定形状(如球形等)。
BMC在模腔内的放置位置,最好应保证在压膜闭合时,料流能同时到达模腔的各个角落。否则,料流必须从侧面流动,使制品产生裂纹、填充不良和其他缺陷。在成型孔洞的周围产生熔接线,造成制品局部强度下降。
由于手工称量速度相当慢,不利于提高生产效率。在小制品成型时,可以使多个成型件使用公用成型腔,这样仅用一块物料就可以同时成型多个制品。
形状复杂的制品,可预先按制品形状压成坯块,然后再成型,这样可以预防各凸出部分产生尺寸误差,并且不至于产生熔接线等缺点。但是,对于某些玻璃含量高的BMC,难以用机械法压制料坯,因为用机械法需要产生足够的压缩才能形成料坯,而聚酯料块有时很粘,难以从坯模上取出。
采用绳条形状的BMC模压制品时,应采用垂直加料的方式,以便使制品各方向之强度一致和收缩一致。同时每一制品只宜放置一个质量与制品相同的料团,如使用多个料团,则料团间的流动汇集点会形成明显的熔接线,该区的强度大大低于制品的其他部分。
(2)成型工艺参数的选择
由于BMC具有良好的流动性,固化过程中又无挥发物产生,因而不需使用很高的成型压力就可使物料充满模腔,完成固化过程。对某些结构简单的制品,只需0.7Mpa的压力就可成型,但是一般采用的成型压力范围3.5~14Mpa。使用较高的成型压力对加快成型速度有一定的好处,它可使多余的物料溢出,并产生精确的、填充良好的制品。但压力过高有时也会因溢料严重而造成脱模困难,某些配方,压力过高,还会引起粘模。
BMC的成型温度一般为110~170℃,成型温度的高低与BMC的固化速度、制品的复杂程度、收缩控制、流动条件等有关。欲快速固化可提高成型温度,如制品形状复杂,为保证料流有足够的时间充满模腔的各个角落,成型温度宜低些。有时为了使制品选择性粘模,可调正上、下模温差,但一般不超过10℃。
制品的固化时间与物料的固化速度有关,也与制品厚度。成型温度有关。制品越厚,则所需的固化时间越长。扁平制品,一般要在模具内实现充分的固化。但是,一般制品为缩短在压机模具组合内的时间,经常采用后处理工艺[7]。
通用型和低收缩型BMC的典型工艺参数是:
成型压力 3.5~7Mpa
成型温度 132~177℃
保温时间 45s
(3)脱模
当制品完全固化后,可以脱模。
2.2BMC注射成型工艺
2.2.1注射成型特点
注射成型与模压成型相比较,它的成型周期比模压成型短且质量也更好,成本也低。主要原因在于它在注射成型过程中,BMC料在模具内可以有效的分配,它可以使用多槽模具,不用像模压成型那样去花费很大精力在称量和在加料上。但是BMC注射成型制品的强度通常情况下没有模压成型制品的强度高[26]。
2.2.2注射成型工艺过程
BMC经料斗进入具有一定温度的料筒中受热软化,并随料筒温度的升高 和螺杆旋转或柱塞推进而不并断受到剪切,且与料筒壁摩擦生热而使BMC进一步塑化成粘流状态,然后在螺杆或柱塞的推动不经喷嘴和流道注射进高温模具中,粘度急剧增加,经适当时间的保温、固化,开模取件。从BMC人料筒至出料筒过程中,BMC在发生物理变化的同时又发生缓慢的化学变化。而从喷嘴注入高温模腔后,则发生固化反应,形成玻纤增强,填料填充的网状体型结构。
BMC注射成型的基本工艺过程:(1)加料,料筒中必须充满BMC;(2)合模;(3)注射;(4)保压,保温固化;(5)开模;(6)取件。
2.2.3BMC制品强度影响因素
为使BMC注射成型有更高的效率和更好的产品质量理想的强度,一方面必须在生产过程中严格控制3个重要参数:注射压力,注射时间和模具温度。另一方面,对原材料也要有特殊的要求,如玻璃纤维的破损,玻璃纤维的取向和树脂的分类。
注射成型条件控制:
BMC通常仅需要非常低的注射压力,一般范围为28~35MPa料筒的温度要尽可能保持得低一点,一般控制在20~60℃范围内。而模具压力温度要高一点,一般控制在135~160℃。注射速度控制在1~7/s。操作条件控制不好会影响制品的机械性能,注射速度越快,纤维取向更为严重,玻璃纤维的破损也在一定程度上与注射速度有关。
注射机和模具设计对注射成型产品的影响:
(1)注射机对注射成型产品的影响
注射机主要有螺杆式注射机和柱塞式注射机。柱塞式注射机对纤维的机械损伤小,但是空气不易排出,所以它的产品外观质量不如螺杆式注射机的制品。螺杆式注射机成型效率高,制品质量好,但是它对纤维的机械损伤比较大[23]。
(2)模具设计对注射成型产品的影响[5]
BMC材料强度主要在注口和流道中受到损伤,所以,在布局设计的时候应特别注意注口和流道的设计。浇口和流道对BMC制品的强度影响如下:
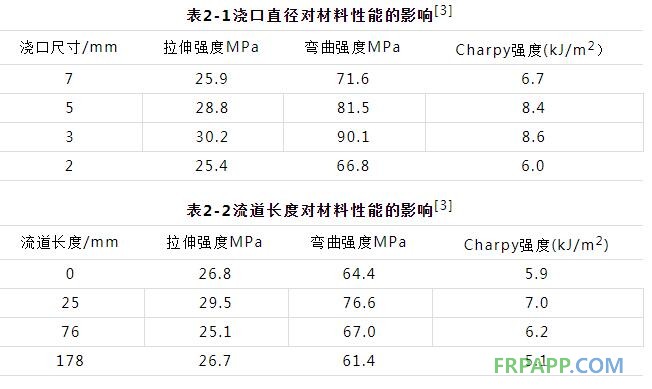
从表2-1和2-2两张表可以看出:浇口尺寸从2mm变化到7mm时,机械性能都上升;流道长度从0mm变化到178mm时,机械性能性能下降。所以说,浇口直径越大,流道长度越短,对纤维的机械损伤越小,纤维就越完整。
2.3BMC灌注成型工艺
BMC采用的原材料有不饱和聚酯树脂、填料、玻璃纤维、增稠剂等增稠剂。不饱和聚酯树脂中,选用苯乙烯单体用作不饱和聚酯树脂的单体交联剂、活性稀释剂,用量一般为30%~40%。填料选用碳酸钙。玻璃纤维选用短切玻璃纤维(6mm左右)[25]。
BMC灌注成型工艺类似于模压成型,它不需要二次加热。将不饱和聚酯树脂、填料、固化剂和其他添加剂混合,制成树脂糊,再将树脂糊与短切玻璃纤维混合,进行充分、均匀的搅拌[26]。如果搅拌不均匀会导致玻璃纤维沉积,制品的强度不均匀,局部强度过低。然后将树脂糊与玻璃纤维的混合料倒入模具中,应保证在压膜闭合时,料流能同时到达模腔的各个角落,闭合模具,进行固化。主要成型参数:成型压力:3.5~7MPa;成型温度132~177℃;保温时间:45s[21]。
等制品固化完成后,即可开始脱模。由于BMC制品中加入内脱模剂,开模后,制品容易取出。