FuPro研究项目开发了一种从纱线加工开始直到生产出汽车部件的连续的生产工艺:
★ 首先,采用一种新型的并排混合纱线(GF/PA6)和精细的编织技术生产连续的软管;
★ 然后,在特别开发的完全自动化的预成型工艺中,卷起料卷、展开并切割成所需要的长度,铺叠成多层预成型件并拉到吹塑薄膜上;
★ 在随后的固结步骤中,预成型件在变温模具中得到快速加热和冷却。在吹膜上施加压缩空气,预成型件浸渍形成型腔的三维形状。
这种薄壁的固结模具经3D打印制成,它允许温度沿表面均匀分布且热质量低。
一种集成了热回收装置的新型油温系统(oil tempering system)在固结过程中实现了高温梯度和低能耗。
通过向模具中埋入其他的金属嵌件或复合材料补片,即可在型材上成型出载荷引入元件。
这种固结的空心型材与有机板材结合后,再采用注塑成型技术对其进行二次成型。
由于注塑成型过程中的压力较高,必须确保空心型材稳定,为此而开发了两种不同的方法:
★ 一种是基于粒子的稳定方法,它投资成本较低,尤其适合小批量的生产;
★ 针对大批量的生产,则开发了一种适用的液压成型技术来保持型材稳定。
总之,这项新工艺为大批量的轻量化应用实现了集空心型材、曲面有机板和复杂肋结构于一体的复合材料设计。通过生产一种集成有安全带的座椅靠背,这项工艺得到了证明。
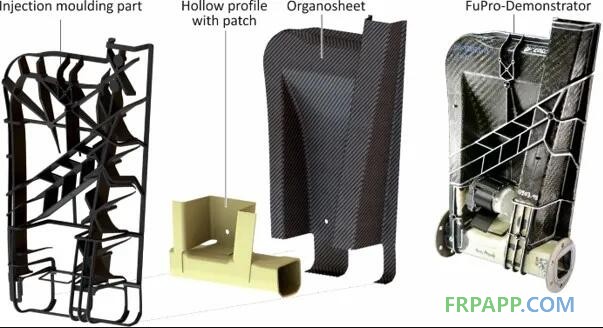
FuPro座椅靠背示范件的设计:在一个一体化的轻量化结构中整合了复合材料的空心型材、有机板材和注塑成型件
新工艺带来的价值
FuPro座椅靠背示范件表明,与现有技术相比,这项新工艺及所具有的设计可能性具有真正的优势。相比传统的钢结构设计,它减轻了大约30%的重量,而且一个单独的集成部件就取代了以往的10个冲压弯曲件和一个塑料支架。
由于可以集成螺栓、卡扣等,使得大量的附加装配元素被省略。
虽然该部件的成本比钢结构的略高一点,但功能的高度集成却大大降低了项目投资成本,特别是取消了冲孔和弯曲模具、连接工艺和过时的防腐处理过程。
就总成本而言,目前这项新工艺在中、小批量的生产中是有利可盈的。
总之,这项创新工艺带来的主要优势包括:
★ 复合材料实现了新的设计可能;
★ 重量明显降低;
★ 可以实现大批量的自动化生产;
★ 高度的功能集成;
★ 项目投资的显著降低。
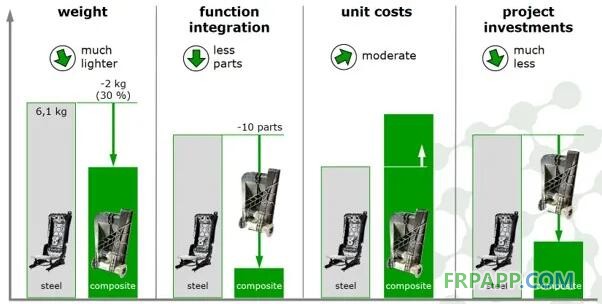
传统的钢座椅靠背与复合材料示范件结构的比较
为确保所有的技术提高到一定的成熟度(TRL),该项目研究分为两个阶段:
★ 第一阶段是以普通的曲面原型结构作为示范,建立了技术和设计可能性的广泛知识库,一大重点是实现柔性编织软管的自动化操作并将它们加工成多层预成型件。
基于实验室规模的试验,开发了一个典型的预成型工位,用于开展空心型材的半自动化生产试验。
同时,还首次将3D打印的模具用于变温固结成型,并对高达300℃下的加工性能进行了详细分析,这两个变量的稳定性也首次得到了测试。
通过在原型件上进行力学试验,获得了有关混合结构的结构性能经验,特别是空心型材、有机板材和注塑配混料之间的粘接性。
★ 第二阶段,利用这些知识开发出一种示范结构以及相应的工业化程度的工艺链。这样,就为每个生产步骤提供了高度自动化的解决方案。该座椅靠背示范结构在实际条件下得到了设计、仿真、制造和成功的测试。
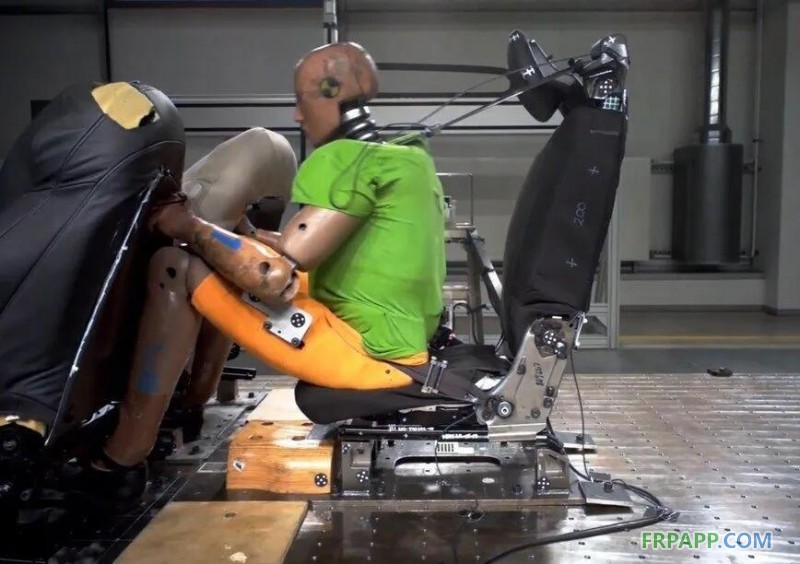
集成了安全带的FuPro座椅靠背正在进行碰撞试验
最终,该项目开发的所有技术至少有5项达到了技术成熟度。参与该项目的所有合作伙伴都期待着FuPro技术能够尽快进入批量应用。目前,单一的技术已实现批量应用,比如,混合纱线、加热系统(tempering system)和3D打印的固结模具。
这项创新对环境的影响
从混合纱开始,整个FuPro工艺极其高效。
开发的自动化预成型工艺具有过程控制和对材料不均匀性高度宽容的特点,因此废品率几乎为零。
这种混合纱构成本身就能实现基体材料对增强材料的快速、低压浸渍。
具有能量回收装置的油温系统结合3D打印的模具,显著降低了变温固结过程所需要的热能。
基于高度的结构整合,额外的连接过程被取消,从而减少了对粘合剂或其他粘接剂的需要。
由于整个结构由玻璃纤维/聚酰胺6构成,因而确保了高度的可回收性。
在注塑成型步骤中,可以使用从生产废料回收的散料。此外,塑料的使用不再需要额外的防腐处理(阴极浸涂),从而减少了对化学品的使用并降低了能耗。