工艺流程
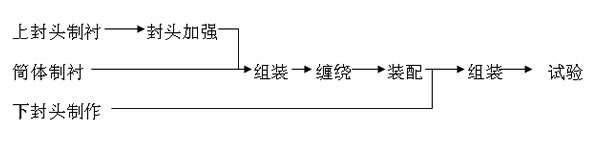
准备工作
a. 仔细阅读设计文件,注意原材料选用、各部分尺寸、模具的选用、铺层设计等关键事项。
b. 设备调试。首选认真检查设备运转及工作部位是否正常,特别要细心检查树脂-固化剂双组分泵是否有堵塞现象,之间配比是否达到设计要求;要确保制衬、缠绕、修整、脱模等设备的运行稳定和工作精度;
c. 清理模具。要求模具表面无坑凹、粉尘、杂物及其他附着物,模具要作到表面平滑,有问题及时修理、维护;
d. 缠聚酯薄膜。为方便脱模,在模具表面应包覆1层聚酯薄膜,薄膜搭接宽度1~2cm,厚度为40um之间。要求薄膜无破损,无皱折,两面光滑洁净。薄膜产品质量满足GB13950-1992的要求。
制衬
筒体在立式缠绕机相应规格的专用模具上制作,开动液压油泵旋转主驱动盘,将聚酯薄膜缠到筒体芯模上,内衬采用喷枪喷射整体制作,树脂在模具的旋转作用下分布均匀,容易赶除树脂中的气泡,内衬平整光滑,没有接缝。同时内衬按内径自然成圆弧状,防止了用平板卷成圆筒产生的微细裂纹。
封头内衬在专用模具上制作,与筒体组装时搭接宽度为按设计要求。
停止点检验:
1. 符合设计要求(包括规格尺寸、厚度、树脂含量等)
2. 内外表面平整光滑,无划痕、疵点、白化现象,内外表面无杂质、无纤维外露、无目测裂纹、无分层、无凹凸不平,色泽均匀,无明显修补痕迹,气泡直径不大于4mm,每平方米数量不多于3个。
组装
上封头与筒体组装时搭接宽度为30mm,糊制粘接外缝。组装连接部位必须打“V”形坡口,所用粘接材料与筒体封头材料一致。
停止点检验:
1. 符合设计要求(包括规格尺寸、厚度等)
2. 表面无杂质、无纤维外露、无凹凸不平,色泽均匀
缠绕
在微机控制下进行缠绕,采用螺旋缠绕、环向缠绕与玻璃布按照产品工作状态下所承受的轴向、环向应力情况进行合理的比例分配,各层纤维均匀排列,可大大提高玻璃钢各层之间的粘接性能,使各层厚度均匀,又避免了纯环向缠绕所产生的环向裂纹。
考虑到液体压力与液体高度成正比关系,既筒体受力从上至下逐渐增大,将筒体厚度设计为上薄下厚,使壁厚与受力大小相匹配。
停止点检验:
1.符合设计要求(包括缠绕角度、厚度等)
2.外表面平整光滑,无纤维外露,无明显气泡,无干纱、无断纱或未浸透现象,布线、色泽均匀。
脱模
将固化完全的储罐从机械上吊起、卸机,注意吊装时要采取措施,防止贮罐的碰撞。
下封头制作
下封头直接在基础上制作,按图纸尺寸制作围堰(以便制作封头直边),然后按照工艺铺层进行底封头制作。
停止点检验:
1. 符合设计要求(包括规格尺寸、厚度、树脂含量等)
2. 内外表面平整光滑,无划痕、疵点、白化现象,内外表面无杂质、无纤维外露、无目测裂纹、无分层、无凹凸不平,色泽均匀,无明显修补痕迹,气泡直径不大于4mm,每平方米数量不多于3个。
现场组装、装配、安装及就位
用吊车把贮罐吊到基础上的底封头上,下封头与基础直接接触,下封头起到传递载荷给基础的作用,只是在与筒体连接的拐角部位受力大且受力情况复杂,因此,下封头直接在基础上制作,与筒体采用承插式填充连接,使其与基础充分接触,增加拐角部位厚度。从外面填堵底封头与筒体间空隙(可分数次进行),再从内部糊制所有对接缝达到要求,最后安装筒体外部接管。
停止点检验:
1. 符合设计要求(包括规格尺寸、厚度等)
2. 表面无杂质、无纤维外露、无凹凸不平,色泽均匀。