第2章面向艇体的真空导入成型工艺设计系统总体设计
2.1引言
国内对真空导入成型工艺的研究多是通过实际生产进行经验的积累,相对而言理论研究方面并不成熟。为了开发面向游艇艇体的真空导入成型工艺设计系统,需要建立系统总体框架,将工艺知识、数值模拟以及数据管理等集成起来,实现工艺设计的高效化。
本章首先对艇体真空导入成型工艺过程进行分析;然后深入研究树脂在模腔内的流动原理,分析常见缺陷;最后构建系统功能框架,并分析其工作过程。
2.2艇体真空导入成型工艺模型
2.2.1真空导入成型工艺原理
在真空导入成型工艺中,首先将增强材料沿刚性模具表面铺覆,进而铺放辅助树脂流动的高渗透介质以及起到隔离作用的隔离层,并铺设树脂管、真空管;然后利用真空袋密封,抽真空并验证气密性后,打开树脂注射开关利用压力差将树脂注入模腔内完成填充;最后固化成型。该工艺的成型特点是不借助外界压力设备,仅在大气压力作用下,采用特定的树脂分配系统促进树脂的流动。其工艺原理如图2-1所示。
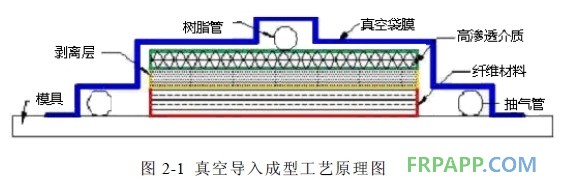
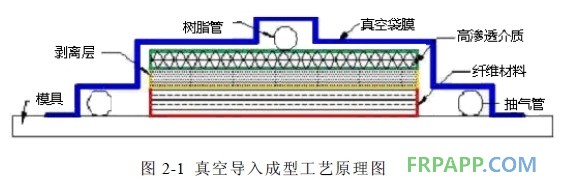
2.2.2艇体真空导入成型工艺过程分析
面向游艇艇体的真空导入成型工艺所需装备设置如图2—2所示。其成型步骤及注意事项如下:
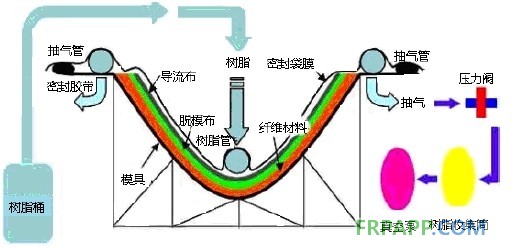
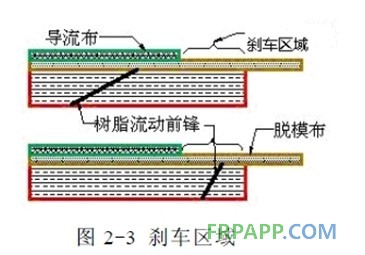
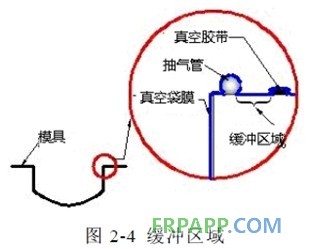
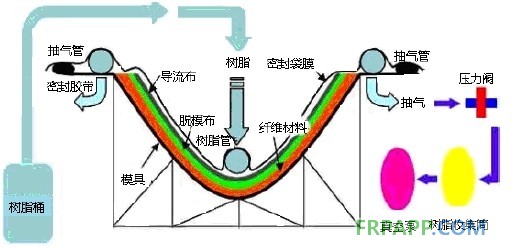
1.准备模具 由于游艇属于大尺寸小批量制件,在实际生产中为节省成本,模具一般为木模居多。为保证施工顺利及成型质量,模具必须满足以下条件:
(1)模具表面必须平整并具有良好的气密性,以保证真空度。对于分块模具,要用雕塑土填充模具结合处的缝隙。
(2)具有足够的刚度,防止由于真空压力造成模具变形而影响艇体外形。对于木模,一般采用夹层板或三合板增强其刚度。
(3)模具应具有良好的耐热性,避免因树脂固化放热变形。
(4)模具应具有不少于15cm的凸缘法兰边,以方便真空管的铺设和密封胶带的密封。
2.打蜡及脱模剂 由于脱模剂价格高,最好的方法是打多次蜡和一次脱模剂,这样既可降低成本又能保护模具,而且脱模后可在艇体外表面形成一层保护膜。
3.喷涂胶衣 胶衣厚度一般控制在0.4-0.6mm之间,可分2-3次作业。尺寸较大的模具用喷枪喷洒,小的用刷子即可。
4.铺放增强材料并设置浇注系统 增强材料的铺放应严格按照所设计铺层方案进行,树脂管路和抽气管的设置原则是保证树脂浸润整个模腔。另外要注意:
(1)为方便脱模,脱模布尺寸要大于增强材料的尺寸,并延伸至抽气管下方,如图2-3所示。
(2)预留刹车区域,如图2-3所示。为了减小螬强材料预成型体上下表面树脂流动前锋的距离,通常使导流布在流动方向上的尺寸小于增强材料的尺寸。这样可以有效减缓树脂在上表面没有导流布的区域的流动速度,防止上表面的树脂过早被抽气管吸入树脂收集桶而在下表面处形成千斑、干区等缺陷。
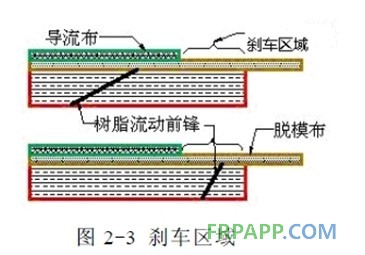
(3)设置缓冲区域,如图2-4所示。为了防止树脂进入抽气管时造成胶带对真空袋边缘的的密封功能失效,通常在抽气管与密封胶带之间预留一定的距离,从而减缓树脂流动的冲击。
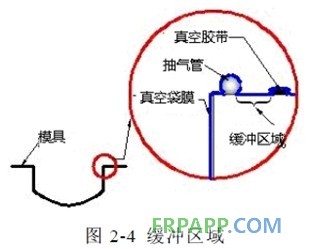