2.2.3艇体真空导入成型充模过程数学模型的建立
由于真空导入成型对RTM成型的继承性,本文在RTM充模过程数值模拟的基础上,对艇体真空导入成型的充模过程进行分析。
真空导入成型的关键是通过分配系统使树脂在表层快速流动,并在厚度方向缓慢浸润。同时,由于艇体厚度非常小,树脂在导流布上的流动距离远远大于在厚度方向上的流动距离。由此可知,真空导入成型的充模过程主要取决于导流介质的平面渗透率及预成型体厚度方向的渗透率,而预成型体的平面渗透率并不属于关键因素。在上述分析的基础上,可以假设预成型体的浸润完全是通过树脂在厚度方向的流动完成的,忽略树脂在预成型体平面方向的流动。由此,可以将艇体真空导入成型的充模过程分为两个部分:第一是树脂在导流布平面方向的流动,可视为RTM成型工艺中树脂在二维薄板内的流动;第二部分是树脂在厚度方向由高渗透介质向预成型体渗流,预成型体吸收了从导流布渗漏出的树脂,其流动示意图如图2-6所示。由此,建立了艇体真空导入成型充模过程的渗漏模型。
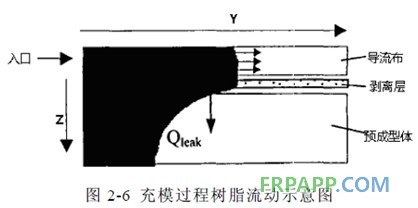
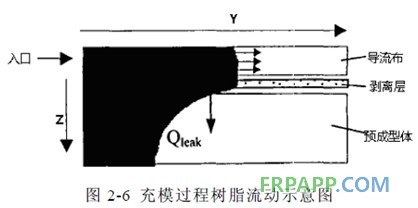
对于RTM二维流动的研究大多是基于流体在多孔介质中流动的达西定律进行的[33-38],其充模过程的二维等温数学模型如下:


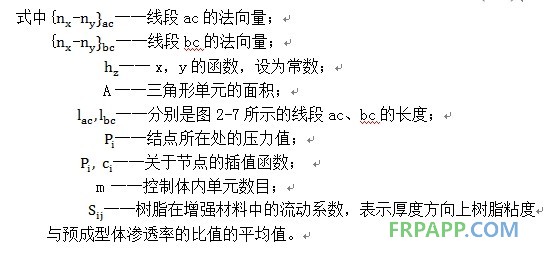

通过上述分析,在式(2-1)中加入Qleak项,则渗漏模型的控制方程可写为:

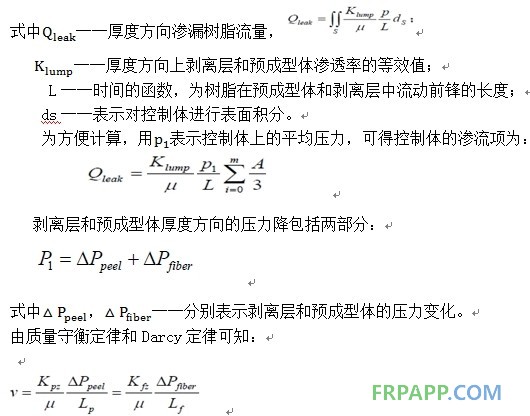
式中 Lp一一预成型体中树脂横向流动前峰长度;
Lp----剥离层介质的厚度。
由此可得表面速度y如下:
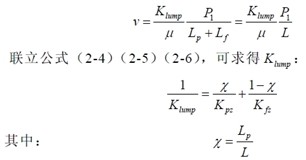
2.3工艺参数对艇体真空导入成型的影响及材料选择原则
复合材料制件成型的显著特点是材料与结构同时一体成型,因此,艇体成型中任何一处缺陷都有可能导致整个艇体的报废,造成难以弥补的损失。针对实际生产中容易出现的缺陷,结合其成型原理分析各个工艺参数对成型质量的影响尤为关键[39]。本节从渗透率、树脂特性、真空度以及浇注系统的设计这几个方面进行分析[40-42],得出成型材料的选择原则,以更好的完善工艺设计。
2.3.1工艺参数影响分析
1.渗透率
渗透率是表征树脂在压力梯度下通过增强材料时流动的难易程度的物理量。在艇体真空导入成型过程中,由于艇体尺寸大,仅仅依靠外界大气压力与模腔内真空之间形成的压力差很难完成填充。因此,通常利用渗透率较高的导流布并铺设树脂管道来促进树脂流动,完成对整个模腔的填充。由于导流布渗透率高而增强材料渗透率相对低,充模过程中树脂在导流布表面迅速流动,同时在厚度方向上缓慢浸渍增强材料。可以通过改变导流布使用比例来控制增强材料预成型体上下表面树脂流动前锋的距离。铺层时,刹车区域的设置正是利用了这个特点。
2.树脂粘度
树脂流动是树脂在预成型体中传递、运输的前提和保证。通常情况下,
将材脂在增强材料中的流动看做是不可压缩黏性流体在多孔介质中的流动,其流动状态可由Darcy定律来描述,如下: