
由Darcy定律可知,要加快树脂流动速度,除了铺设高渗透率导流网提高整体渗透率外,另一个有效方式是选择合适的树脂粘度。树脂粘度太高,会导致流速变慢,充模不完全;树脂粘度太低,流速太快,容易造成浸渍不完全,形成千斑等缺陷。实际生产中,树脂粘度一般为100-300cps。
3.真空压力
在游艇艇体的真空导入成型过程中,模腔内部与外界大气压之间的压力差是树脂浸润增强材料的唯一动力。同时抽真空对于排出增强材料中的空气
进而避免形成气泡有着重要作用。还可以通过改变真空压力控制艇体中的纤维含量。值得注意的是,真空压力的选择必须谨慎:太高的压力会减小模具
寿命,并影响增强材料自身的结构;压力太小则存在无法充模完全的风险。实际生产中,真空负压应不小于0.08MPa,大于0.095Mpa最佳
4.浇注系统加
4.浇注系统加
真空导入成型的关键在于通过设置树脂分配系统使树脂迅速填充模腔,其中浇注系统的设计至关重要。浇注系统的设置包括流道布置方式,注射口
和抽气的位置选择。它们的选择原则是确保树脂能够充满整个型腔,并在最短时间内完全浸润纤维,并尽可能的减少干斑、富脂、过抽等缺陷的产生。
2.3.2成型过程缺陷分析
通过对艇体真空导入成型工芝过程及工艺参数的分析,得出艇体真空导入成型中常见缺陷与工艺参数之间的关系,并提出了初步的解决方案,如图2-8所示。
实际生产中,艇体充模完成后一般采取常温固化。当出现低度固化时,可以通过延长固化时间进行改善,有条件的情况下,可以对固化温度进行调节,以更好的完成固化。对于不完全填充,由于真空压力的限制,最主要是通过改进浇注系统进行改善。干斑的形成与预成型体渗透率不均匀、浇注系统设计不合理等息息相关。为了避免气泡的产生,除了增强系统气密性外,还可通过改善浇注系统以及铺层方案进行调节。富脂和过抽则可以通过改善模具、调节固化真空度、优化流道控制开关等加以解决。
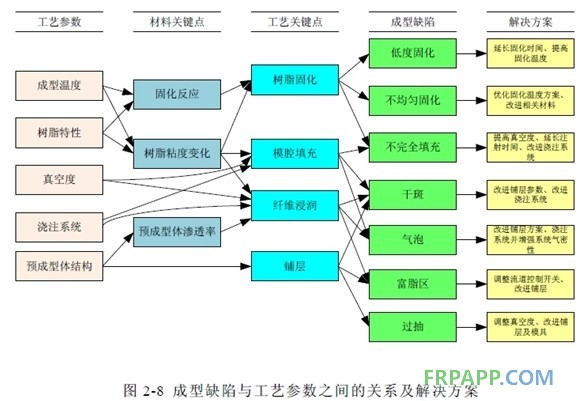
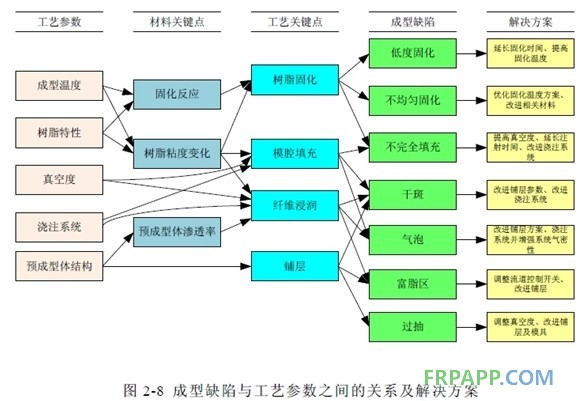
2.3.3材料选择原则
综合考虑上述两节分析,为保证成型质量,对所用材料的选择方法归纳如下:
1.树脂
真空导入成型对树脂的要求一般有以下几点:
(1)树脂体系粘度 如上节所述,树脂最佳粘度范围为100-300cps。
(2)凝胶时间适宜 不同的工艺乃至不同的制件,对凝胶时间的要求并不相同。因此树脂的凝胶时间应可变易控,具有合适的操作周期。对于艇体成型而言,要求树脂体系的低粘度平台时间不少于30min,以避免树脂在灌注过程中就发生剧烈的凝胶反应和固化交联反应。为控制凝胶时间,可以向树脂添加一定配比的固化剂。其中环氧树脂需用专用固化剂。
(3)固化放热峰值适中 高过的放热峰值会对模具造成损伤,降低模具的使用寿命。同时,放热峰值过高时,若散热不良造成局部焦化,将影响产品质量。树脂放热峰值应不高于80℃。
(4)其他物理化学性能 包括良好的力学性能,以满足工程应用的高
要求,如抗热氧老化性、耐化学腐蚀性、阻燃性、无毒、低成本等。
适用于真空导入成型工艺的树脂包括环氧树脂、乙烯基树脂、不饱和聚酯树脂、酚醛树脂等低粘度树脂。
2.增强材料
艇体真空导入成型过程中,材料与结构同时成型,另外艇体形状复杂,为了保证成型质量,对增强材料的要求有:
(1)渗透率相对高,能快速浸润树脂。
(2)随模性好即沿模具表面铺覆容易,以满足形状复杂制品成型的要求。
(3)满足制品的主要性能要求。
3.真空袋膜
由于艇体成型过程操作复杂,很容易对真空袋造成破坏。因此,要求真空袋具有良好的延展性、柔韧性、抗穿刺性;同时要具有较高的耐热温度以
免树脂固化放热时变形而影响气密性。真空袋的颜色最好为浅色,这样方便观察树脂在模腔内的流动。常用的真空袋膜有耐高温尼龙膜和聚丙烯膜。
4.密封胶带
密封胶带应具有高弹性、表面粘结性以及耐温性等性能,保证在制品的成型周期内保持优异的密封性能。
5.导流布
在真空导入成型中,导流布是确保树脂能够充满整个模腔的关键因素。利用其较高的渗透率,可以大幅度提高树脂的渗透和流动。因此,要求其对树脂流动阻力小,铺覆性好。常用的导流布有尼龙网和机织纤维。
6.剥高层介质
剥离层介质的作用是将艇体与导流布隔开,方便固化脱模后清除真空辅 助介质,避免其粘附在制品上。一般选用低孔隙率、低渗透率的薄膜材料作为剥离层介质,如PE、PP多孔膜等。
7.导流管与抽气管
导流管与抽气管都是螺旋管。可通过改变管的直径来调节树脂在管中的流动速度。抽真空时,为了避免管道被压扁,要求管壁有一定的厚度,能够抵抗真空压力,保证树脂流动顺畅。
2.4游艇艇体真空导入成型工艺设计系统总体方案