2.2 经济优势
(1)原材料的直接在线生产模式极大降低了最终制品的成本,避免了半成品较高的采购及相关物流仓储成本;
(2)由于生产所需原材料为直接采购,原料的快速变更可弥补半成品原料采购所带来的周期长、管理费用高的问题,间接降低了生产成本;
(3)加工过程中原料占用量低——低启动消耗,解决了压制初期原材料损耗的问题;
(4)利用塑化料余温立即模压成型,消除了半成品板材二次加热所产生的能量损耗,且生产过程全部由程序控制,生产线自动运行,显著降低整体能耗;
(5)热塑性LFT材料为可回收塑料,LFT生产线可在线处理回收材料,环保的同时也带来了极佳的经济效益;
(6)减少了大量人工操作,劳动力成本降幅可观。
2.3 技术优势
(1)配方调整更灵活多样,只需对LFT-D生产线设备做相应调整,即可使用PP、PA6、PET、ABS、PC等不同聚合物粒料,并且对于不同产品的特殊要求可现场快速调整原料比例;
(2)玻璃纤维作为复合材料制品中保证机械性能的重要组分,连续可调的成型技术将大大优化制品的性能;
(3)最终制品保留了超过20mm的玻纤长度,解决了大批量陕速生产中玻纤长度过短带来的机械强度过低的问题;
(4)出色的混料工艺,可保证玻纤与塑料充分混合,即使在筋肋部也能够保证均匀的纤维分布;
(5)优越的流动性,极大改善了制品的表面质量;
(6)LFT-D设备的高度自动化,保证了制品的质量稳定性。
3 应用领域
3.1 应用范围
当前,LFT-D生产技术最主要的应用领域仍然是汽车制造方面。
在汽车轻量化进程中,在保证汽车安全性的前提下,整车重量每减轻10%,常规燃油效率可提高6%~8%,复合材料替代金属材料已经成为产业发展的主流趋势。作为汽车产业轻量化中的领先技术,LFT-D热塑性复合材料已在众多知名整车厂得以应用,目前制造模式较为成熟的零部件有前端模块、保险杠支架、仪表板骨架、座椅骨架、车底防护板、内饰件支架、车轮罩、蓄电池托盘、杂物箱盖、后掀背门、备胎箱等。见表2。
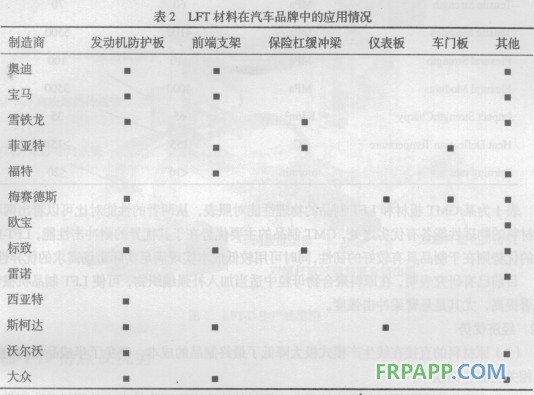
3.2 应用实例
3.2.1 底部防护板/底部导流板
车底护板早期是附装在白车身上用于保护重要组件的一些小板,后由于80年代末90年代初,德国制定了非常严格的车辆噪声防护法,使得其演变成覆盖整个底盘的大板。随着底部护板的发展,其形状也从简单平板变得更加复杂,功能开始兼具吸音、隔热、防腐蚀、高刚性、高冲击强度等性能。材料则由钢材、铝材演变为GMT,直至90年代晚期产生了成本更低、成型方式更为灵活的在线配混直接LFT-D技术,还有部分生产厂家开始使用纤维高度膨松的轻质高强热塑性塑料LWRT,其韧性不及传统GMT但比刚度很高,并具有优良的吸声性能。
汽车底护板的制造及应用已经较为成熟,在大众途观,上汽荣威350、550、750,上汽E50电动车等车型中均有使用。
3.2.2 前端模块
传统的汽车前端模块是由几十个零部件供应商将钣金件送至整车厂,然后进行总装,由于前端模块很重,对于总装线装配效率和生产节拍的要求很高。现在,使用LFT技术并配合零部件模块化生产模式,将照明、冷却、减震等组件提前组装,形成前端模块总成后再送至整车厂,已经成为了一个新的供应模式。
从表3中可以看出,国内对于LFT材料的使用已经越来越普及。
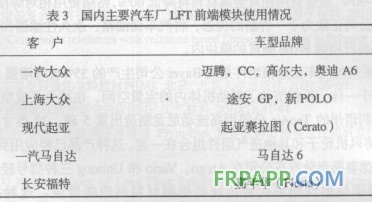
3.2.3 座椅骨架
通过将金属座椅骨架模型在专业分析软件中进行模拟优化布局,可定制出适用于在LFT-D工艺中生产的制件形状,并通过在总成中加装镶嵌条进行局部增强,在撞车时可保护乘客防止错位,在冲击时优化LFT和局部无间断增强的延展性和变形能力,LFT可替代钢铁减重超过40%,并可达到高度的集成功能,实现功能一体化。
长城汽车哈弗H5中座椅骨架即采用了LFT-D技术制成。