6管口试压
由于玻璃钢管之间采用承插式 双“O” 型密封圈连接,所 以每安装一根管道,就要在承插口处 进行打压,以检测双“O”型密封圈的密封效果。用试压泵直接通过管顶的试压孔。加水打压至管道工作压力的1.5倍后停泵(操作过程中要打开排水阀排气),观察2min,压降值不超过试验压力的5%,且管口没有渗漏现象时。管口试压即为合格。若压降降低较快。说明密封效果不佳 ,需重新安装,以确保整个管道系统总体试压成功。
7管道验收
(1)检查径向挠曲值。按照规范要求,玻璃钢管道安装完毕24h内,应测试管道的初始径向挠曲变形,管道不得出现隆起、扁平和其他突变现象。
(2)水压试验。为了全面检查管道的安装质量,按照《给水排水管道工程施工及验收规范》规定的试验方法进行试压,允许渗水量可以按照钢管的标准执行。
(3)由于玻璃钢管之间采用承插式 双“O”型密封圈连接,所以每安装一根管道,就要在承插口处进行打压,以检测双“O”型密封圈的密封效果。用试压泵直接通过管顶的试压孔。加水打压至管道工作压力的1.5倍后停泵(操作过程中要打开排水阀排气),观察2min,压降值不超过试验压力的5%,且管口没有渗漏现象时,管口试压即为合格。若压降降低较快,说明密封效果不佳,需重新安装,以确保整个管道系统总体试压成功。
8退管操作及修补方式
(1)在玻璃钢管道安装过程中,往往会有不合格现象发生,一般玻璃钢管道安装不合格的原因有3种:一是管道承口与插口的质量差异,这种情况出厂检验时被忽视;二是承插口内有沙粒未清除;三是因橡胶圈安装不到位,导致其扭曲变形,或者在安装过程中两侧的手拉葫芦用力不均匀使橡胶圈扭曲变形第三种情况发生的可能最大,只要玻璃钢管道安装不合格,就必须进行退管,检查橡胶圈,找出原因重新安装。

支座可由长300 mm的L5角钢制作,将厚 10 mm的60mmX60mm的铁板焊堵于角钢一端,在角钢一边的外侧沿其长度方向垂直于角钢板面焊上2根Φ10、长为 30mm、间距为 100mm的圆钢即可。使用时,先在需要退出的管道承口上,沿管轴线方向在适当位置打出Φ10间距为 100mm的2个钻孔,将支座的圆钢插入钻孔 (角钢有堵头的一端必须在母口的对面),然后将千斤顶的底座紧靠在管道的母口上,千斤顶的顶部支承在角钢支座的堵头上,按动千斤顶的加压杆,即可在短时间内轻松将管道退出。然后用粘过树脂的12mm螺杆将承口上的钻孔拧紧堵死,退管工作完成。
(2)玻璃钢管道在运输、安装及回填时难免受到损坏,在管线注水打压前都要必须对管道最后检查一遍,检修人员在管内活动困难,检修速度慢,影响了整个工程的进度。可以现场制作简易管道车用于检修。选择一段废弃的管道(管道直径要比被检修的管道小一级),截取900mm左右长度,管轴线方向把管道剖开,剖成弧长500mm的板材作为管道车的车板,在四个角上安装万向轮。(参见图4)检修管道时,将管道车置于管道中,检修人员钻入管道,仰面躺在车上,用脚蹬车,即可快速进行检修。
(2)玻璃钢管道在运输、安装及回填时难免受到损坏,在管线注水打压前都要必须对管道最后检查一遍,检修人员在管内活动困难,检修速度慢,影响了整个工程的进度。可以现场制作简易管道车用于检修。选择一段废弃的管道(管道直径要比被检修的管道小一级),截取900mm左右长度,管轴线方向把管道剖开,剖成弧长500mm的板材作为管道车的车板,在四个角上安装万向轮。(参见图4)检修管道时,将管道车置于管道中,检修人员钻入管道,仰面躺在车上,用脚蹬车,即可快速进行检修。
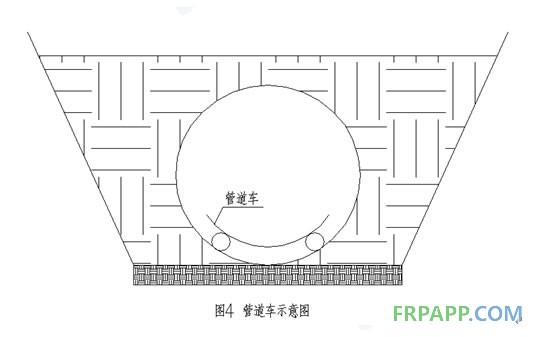
9沟槽回填
(1)当管道连接好后,必须尽快进行水压试验并进行回填,防止管道发生浮动和热变形。
(2)按照设计要求选择管区的回填材料,并进行正确的管区回填与夯实。对管道底部两端的腋角部位,应按照设计支承角的要求进行回填与夯实。
(3)回填前应清除沟槽内的杂物,并且排除积水,不得在有积水的情况下进行回填。
(4)管区应进行对称分层回填,不得单侧回填。每次回填厚度应根据回填材料和回填方法确定。砾石和碎石宜为300mm,砂宜为150mm。
(5)管区的夯实应从管沟壁两侧同时开始,逐渐向管壁方向靠近,严禁单侧夯实。管顶的夯实应达到要求的密实度,管区回填料的压实度为95%。
(1)当管道连接好后,必须尽快进行水压试验并进行回填,防止管道发生浮动和热变形。
(2)按照设计要求选择管区的回填材料,并进行正确的管区回填与夯实。对管道底部两端的腋角部位,应按照设计支承角的要求进行回填与夯实。
(3)回填前应清除沟槽内的杂物,并且排除积水,不得在有积水的情况下进行回填。
(4)管区应进行对称分层回填,不得单侧回填。每次回填厚度应根据回填材料和回填方法确定。砾石和碎石宜为300mm,砂宜为150mm。
(5)管区的夯实应从管沟壁两侧同时开始,逐渐向管壁方向靠近,严禁单侧夯实。管顶的夯实应达到要求的密实度,管区回填料的压实度为95%。