1 前 言
玻璃钢复合夹芯板以其重量轻、强度高、刚性好、耐腐蚀、保温、隔音等特点在市场上得到越来越广泛的关注。在国外,玻璃钢复合夹芯板材已经广泛应用于集装箱箱体板、高速列业内饰板、建筑用模板、城市道路用隔音板等产品上。在国内,玻璃钢复合夹芯板制品也日益增多,具有可观的经济效益。
夹层结构制造技术分干法成型和湿法成型两种。干法成型是先将蜂窝夹芯和面板做好,然后再将它们粘接成夹层结构;湿法成型是面板和蜂窝夹芯均处于未固化状态,在模具上一次胶接成型,固化,脱模后修整成产品。在国外部分国家已经实现了玻璃钢复合夹芯板的规模化制造工艺,主要是湿法连续固化成型,自动化程度很高,大大降低了生产成本。国内玻璃钢复合夹芯板的生产则以手工为主,夹芯板的生产存在质量不稳定、生产效率低等一系列问题,复合材料不能发挥最大的效率,造成资源浪费,由此造成夹芯板的成本偏高,影响了夹芯板的推广应用。我们通过大量试验研究,首次独创性地采用拉挤工艺连续成型玻璃钢夹芯板材,解决了集模具、材料、配方、工艺于一体的塑料蜂窝玻璃钢夹芯板材制造技术问题,实现了该类产品的规模化生产,工艺流程如图1所示。
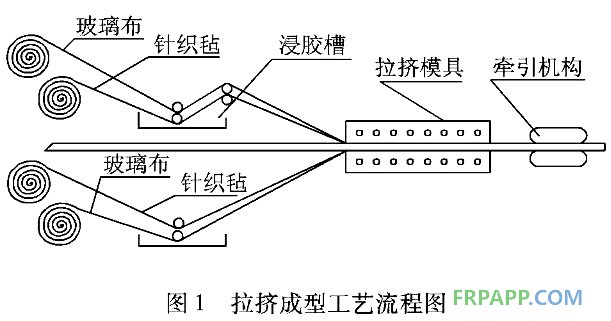
2 工艺研究
在夹芯板的结构设计中,我们采用热固性玻璃钢作为面板,以毡和布为增强材料,芯材则采用了热塑性聚丙烯塑料蜂窝,该蜂窝结构硬挺,不易变型,整体操作性强,且抗压抗剪能力较强,经过一系列的试验研究我们成功实现了这种复合结构制品的连续拉挤成型工艺。
2.1 夹芯板低温拉挤成型技术研究
2.1.1 低温固化体系的研究
在树脂体系一定的情况下,成型过程的放热性况与选用的引发剂体系和成型温度有直接关系。聚丙烯塑料蜂窝的熔点在160度左右,而普通拉挤成型工艺的成型温度在135~165度,放热峰温度达到180度以上,因此寻找半衰期合适并调节引发剂用量,使其在成型温度下的放热峰温度在140~150度。且满足连续成型的引发体系成为本项目的技术关键之一。
普通拉挤成型工艺所用的引发剂多为高温引发剂,表1列出了常用的高温引发剂。
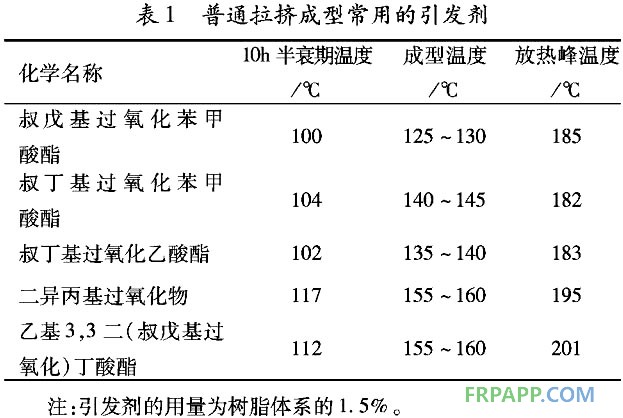
由表1可见,常用的树脂引发体系在反应过程中放热蜂温度比较高,均超过160度,不能满足夹芯板连续成型的要求。因此,必须全部选用或者部分选用10h半衰期温度低的引发体系作为夹芯板连续成型的引发体系。表2列出了采用的低温引发剂。
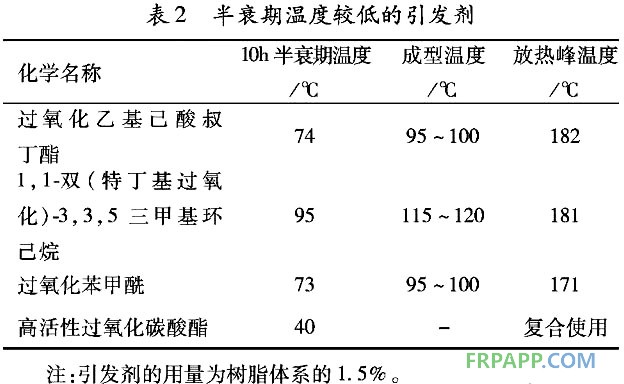
由表2可以看出,单纯使用低温引发体系不能降低放热峰温度,无法实现放热峰温度为140~150度的指标。为此,项目组决定对上述高温和低温引发剂进行复合来解决此问题,具体测试数据见表3。
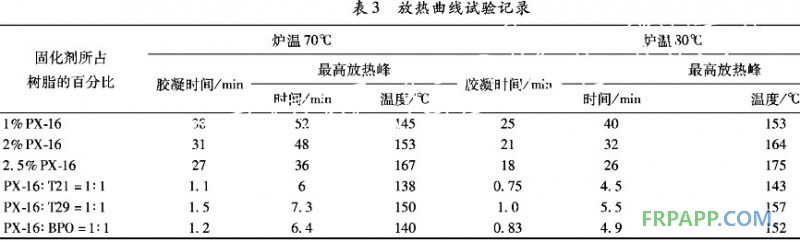
试验表明,选用复合引发体系即能加快固化速度,又能降低放热峰温度,能够满足拉挤成型的工艺要求。通过上述试验,初步确定选择引发体系为低温引发剂PX-16与中温引发剂T21以1:1复合,用量为树脂用量的2%做为低温快速成型拉挤夹芯板的引发剂体系。
2.1.2 低温固化体系内脱模的研究
为实现连续过程中的脱模,在配方体系中必须添加内脱模剂。做为内脱模剂应该满足如下要求:①在加工过程中必须是相容的;②对最终产品的物理性能不应产生有害影响;③不会产生不希望的色泽或颜色的漂移;④便于加入到树脂糊的混合操作。
在连续成型工艺中,主要采用硬脂酸金属盐和脱模油作为内脱模剂,表4列出了硬脂酸盐的熔点及松密度。
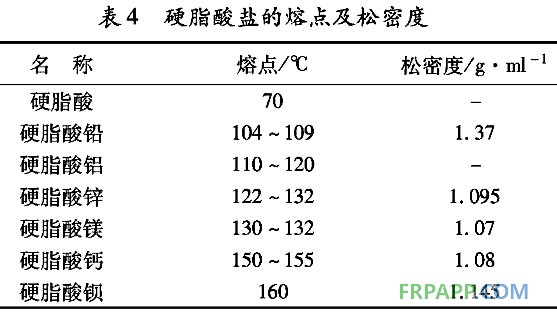
这些内脱模剂在受热时会熔化,作为第二相迁移到模具的表面上,从而实现防止树脂对模具表面粘结的功能。从这种意义上讲,所选用的内脱模剂的熔点最好刚刚低于固化温度,这样可使固化前由于脱模剂过早融化而造成的产品粘接在模具表面的可能性减小。从上表可以看出,只有硬脂酸的熔点在90度以下,可以考虑作拉挤成型夹芯板材的内脱模剂,因此选用了硬脂酸和脱模油复合脱模体系。
由于硬脂酸的状态为片状固体,在使用过程中存在着分散不均匀、易于漂浮在树脂糊表面的问题。为此,项目组通过对硬脂酸进行处理,与不饱和聚酯树脂混合后经过三辊磨研后使用,解决了脱模剂与树脂体系的相分离问题,获得了良好的使用效果。
2.2 夹芯板面与芯材的粘接技术研究
夹芯板材在生产过程中,面板与芯板的粘接强度将直接影响整个板材的性能。面板对芯材具有保护作用,使其避免受机械损伤,防止风化,隔离水与蒸汽,且防火,防腐蚀等;而芯材的作用则是将两个面板连接成整体,共同承受荷载,同时还具有绝热、隔音等作用。由于该类夹芯板面板和芯层材料性质完全不同,二者直接粘结强度较差,因此粘结强度的提高是非常关键的问题。通过以下途径和方法,在提高界面粘结强度方面取得了较好的效果;
(1)PP蜂窝表面预处理
将PP蜂窝直接使用在拉挤工艺中,由于二者之间界面粘附力低且有效粘结面积太小,致使与玻璃钢面板粘结效果非常差。通过热熔方法将PP蜂窝断面熔融后,与一层高强无纺布复合粘结,使聚丙烯热熔液浸入高强无纺布,粘结成为一个整体,从而大大增加有效粘结面积,达到增强粘结强度的作用。
(2)拉挤成型的压力控制
在拉挤成型工艺中,由于浸胶的布层、毡层连同蜂窝芯材要通过一个固定型腔尺寸的模具固化成型,只要蜂窝两面增强层的层数设计合理,即可保证产品在成型过程中得到一定的成型压力,使胶液能够渗透到蜂窝内部,使粘接强度提高,保证了界面的粘结效果,避免界面分层或粘结不实等缺陷,有效克服了手糊夹芯板面板与芯材的界面粘接效果差的问题。
(3)通过合理选用树脂体系,进一步提高粘附力
夹芯板界面粘结强度与基体树脂的粘附力也有很大关系,在成型过程中选用力学性能优异的乙烯基酯树脂后,大大提高了界面粘结强度。
3 在线全过程质量控制技术
制造过程质量控制技术是一种既包括生产技术,又包括生产质量管理的系统工程。实现制造过程的质量控制其内涵包括两个方面,①要保证优化工艺,提高产品质量;②要保证稳定不变的工艺条件,得到分散度极小的均一产品质量。
制造过程质量控制不仅要靠生产过程的自动化、工艺参数的在线控制、生产工艺参数对工艺效果的模似优化来实现,而且还必须尽可能控制过程的智能化,这是目前质量控制技术发展的主要方向。
为了保证产品在线生产质量的稳定,项目组在夹芯板各个环节的生产控制都进行了细致的研究:
(1)增强毡材的浸渍
在夹芯板材生产中应用的增强材料是连续状状的织物,如连续毡、方格布、表面毡等,要保证产品质量,尤其是加强芯层与面层的粘结效果,对于增强毡材的浸渍效果就提出较高的要求。传统的采用胶槽中固定的压杆进行浸渍的方法证实不适用于夹芯板的生产。这种方法在纤维浸渍中使用较多,但在毡材的浸渍上,由于不能使毡材有幅宽方向受到均匀的牵引,易导致毡材发生严重的变形,即纵向拉伸,模向缩小的现象,从而极大降低材料的性能和表观质量。因为这种变形对材料强度的削弱,还会造成频频的中断,影响连续生产的顺利进行。因此,项目组针对增强材料的这种特点,借鉴了缠绕工艺的浸胶型式,设计了可灵活调节毡材输送张力,并能够有效控制含胶量的一系列胶辊,很大程度上保证了增强毡材的顺利送料,减少了毡材打折现象,有效提高了产品表观质量和综合性能。
(2)胶液回流及储存装置设计
夹芯板所用的夹芯层,其主要原料为聚丙稀,聚丙稀是一种热塑性塑料,溶点为164~170度。为避免夹芯材料在模具固化过程中固化放热量过高而产生熔融,影响产品整体强度,项目组在产品的固化体系设计上,通过优化组合,采用了低温的复合引发体系。在满足以上要求的同时,也带来一定的隐患,即对于连续化工艺来说,该体系的常温存放时间将会因此而缩短,使胶槽易存在频繁凝胶的危险。为解决这一矛盾,项目组改进了传统拉挤浸胶方式,在胶液回流段和胶液储存段大胆使用了双层结构的设计,采用冷却水循环冷却回流胶液和胶槽内的胶液,从而使该体系的存放时间大大延长,圆满解决了生产和工艺的矛盾。

4 结束语
手糊成型由于受到人员操作水平及模具质量的制约,在成型过程中易出现粘结不实的现象,造成质量稳定性欠佳,产品局部强度底,但采用拉挤成型则很好的解决了这一问题,该工艺过程容易实现自动化控制,产品质量稳定,而且生产过程中基本不产生边角废料,原材料有效利用率高。解决了以往夹芯板的生产存在质量不稳定、生产效率低等一系列问题,实现了夹芯板的规模化生产以及玻璃钢夹芯板的优质、高效、低成本制造。