天线罩的一般下料形式和铺叠后的效果如图3所示。可以看出,常用的下料形式是保证不了核心区和其它区域严格的电性能要求。

分析可知,此雷达天线罩的核心区是双曲面外形,从理论上来讲是不能展开为平面的,但我们巧妙利用玻璃布的部分可延展性,再利用复合材料模拟软件FiberSim的优化设计和仿真,设计出如下优化的下料形式,其铺叠后的效果如图4所示。可以优化设计的下料形式能够完全满足核心区和其它区域的设计要求。
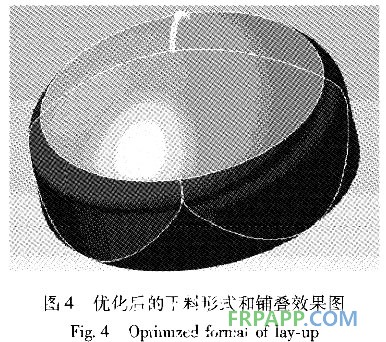
比较上面两种下料形式的铺叠效果可以看出,优化的下料形式在核心区无搭接,而且核心区拼缝明显少于一般的下料形式。另外,优化的下料形式比一般下料还具有以下优点:玻璃布的利用率从50%提高到80%、下料效率和铺叠效率也有相应提高。
2.5 蜂窝夹芯与蒙皮的胶接成型工艺
NOMEX蜂窝夹芯与蒙皮的胶接工艺,常采用两种方法:二次成型和三次成型。二次成型是先将外蒙皮(或内蒙皮)在模具上裱糊成型后进行第一次固化,然后与蜂窝芯胶接,并在蜂窝芯子上裱糊内蒙皮(或外蒙皮),再进行第二次固化;三次成型是将外蒙皮在模具上裱糊后固化,然后将蜂窝芯子胶接在外蒙皮上进行第二次固化,最后在蜂窝芯子上裱糊内蒙皮,并进行第三次固化。实践证明,三次成型的质量要比二次成型质量要好,但生产周期长,成本高。不论是二次成型还是三次成型,都不熊同时保证内外蒙皮表面的光滑。
本研究中,由于有内、外蒙皮两个模具,内、外蒙皮可以分别铺叠固化,有效地保证了内、外蒙皮表面质量和厚度,而且不增加制造成本,然后在内蒙皮上铺放胶膜和NOMEX蜂窝进行预粘,再铺放胶膜,装配外蒙皮,最终固化。采用这样的胶接工艺,有利于固化时低分子挥发份的排除,夹层内的成型质量也容易检查,缺陷也能及时排除,保证了内、外蒙皮和蜂窝的胶接质量。
2.6 外蒙皮装配工艺
上面所说的二次成型和三次成型法中不存在外蒙皮(或内蒙皮)的装配问题,因为外蒙皮(或内蒙皮)在蜂窝上直接裱糊。而采用凸模成形,又要求外表面光滑,外蒙皮的装配就成了非常困难的关键工序。因为蜂窝夹层结构的蒙皮一般都很薄,外蒙皮的刚度很小,胶膜又很粘,在装配过程中,蒙皮极易和胶膜粘在一起,无法保证装配到位,引起蒙皮和蜂窝芯脱粘,导致整个产品的报废。装配工序是蜂窝夹层结构制造过程中的一个基础的重要工序。如果装配工序处理不好,就会面对由天气决定是否制造的尴尬局面(一般在零下温度时,胶膜不太粘,装配的问题不大)。
我们巧妙改进装配工艺,有效解决了这个基础问题,在以后的制造过程中,未出现由外蒙皮装配而引起的问题。
3 检测结果与结论
对成型后的天线罩进行了一系列测试,主要包括核心区和其它区域电性能测试、基本力学性能测试、罩体厚度、无损检测、表面质量等。各项指标均达到相关的技术标准。
本文选用玻璃布/中温改性环氧、胶膜和NRH系列NOMEX蜂窝夹芯体系,采用双凸模固化成型,通过FiberSim软件优化设计下料形式,采用创新的装配手段,合理的胶接和固化工艺,研制出完全满足设计要求的高性能的雷达天线罩。