在玻璃纤维的生产和应用过程中,浸润剂起着不可替代的关键作用。浸润剂含量是玻璃纤维成品纱中一项重要的理化指标,它不仅直接影响成品纱的外观质量,而且更会影响成品纱的性能质量。浸润剂含量过低,就会出现严重的毛丝、散丝等现象,并显著降低纤维的抗拉强度;浸润剂含量过高,虽然在一定程度上会提高纤维的抗拉强度,
但一般会降低纤维在树脂中的浸透速率,影响纤维与基体的界面结合程度。此外,浸润剂还是玻璃纤维工业中成本价格比例较高的主要原料之一,成品纱的浸润剂含量越高,其生产成本越大,因而会降低经济效益。
由此看来,玻璃纤维的生产要想同时达到既降低生产成本而又提高产品质量,就必须加强对浸润剂含量的控制。在现行玻璃纤维行业标准中,对成品纱的浸润剂含量指标要求为0.5%~206,这只是在玻璃纤维没有品种分类、浸润剂技术指标参差不齐情况下概括性的大范围全容标准。随着玻璃纤维分类的细化、浸润剂技术的发展,各厂家在实际生产中都对某一种类玻璃纤维或 某二浸润剂配方都有一个相对较小的控制范围,以利于生产的稳定和产品质量的稳定。一般缠绕型、拉挤型等纱的浸润剂含量大致在0.5%—0.9%范围内,而纺织型纱大多在1%以上。
由于浸润剂的传统名称叫“润滑油’’,本文简以“油”代指浸润剂,浸润剂含量简称为“含油率”。在生产过程中对成品纱含油率的调节控制可以通过以下三种途径进行:
1 调整所配制浸润剂的固含量
浸润剂是由少量有效组分被大量水稀释而成的乳液,有效组分在浸润剂中所占的百分比即是浸润剂的固含量。经过烘干过程大量水份蒸发散失,而浸润剂的有效组分以固体膜形式保留于成品纱中,其在成品纱中所占的百分比被称为玻璃纤维的浸润剂含量,即成品纱的含油率。由此可以看出:玻璃纤维含油率与所使用浸润剂的固含量成正比关系,即固含量越大,成品纱含油率越高;固含量越小,而含油率越低。但由于受生产工艺因素的影响,两者之间一般不是线性关系,而且不同的拉丝机所拉的丝两者的比例关系也各不相同,其中最主要的因素就是浸润剂的机器甩失率各不相同。在生产工艺条件未改变的情况下,通过长期的数据积累和分析,可得出在一定范围内成品纱含油率与浸润剂固含量之间相对稳定的比例关系,按此比例关系对固含量进行调节,从而达到控制含油率的目的。
2 改变涂油辊的转速
我厂采用转辊式涂油器对拉制的玻璃纤维进行浸润剂的涂敷,使用材质是现今行业普遍采用的中细粒度级高强纯石墨,一般转速控制在60~80r/min之间效果较为理想。涂油辊的材料是决定其带油能力的内在因素;而涂油辊的转动线速度决定了其实际带油量的多少,后者具有更重要的工艺生产意义。涂油辊转动线速度与其带油量之间的关系如图l所示:
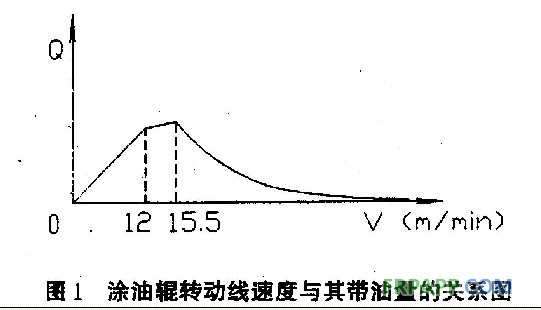
当涂油辊转动线速度V在(12—15.5)m/min(相应转速为55~80r/min)之间时,随着转速的提高,涂油辊带油量相应缓慢增加,使纤维涂油量增多,成品纱含油率逐渐提高;当V< 12m/min或V>15m/min时,涂油辊带油量明显减少,使成品纱含油率急剧下降而不稳定。当转速太快时,会使涂油辊表面吸附的浸润剂因离心力太大而沿外圆切线飞失,因此造带油量的下降。而由于拉丝速度远远大于涂油辊转动线速度,当涂油辊转速太慢时,会使一定时间内通过涂油辊的部分段玻璃纤维束涂油太少,甚至没涂上油,造成涂油不均和生丝现象。
3 上下位移调节集束轮位置
从漏板处拉下来的玻璃纤维分散单丝经涂油辊涂油后再经集束轮合并成一股原丝:当集束轮下移时,纤维束与涂油辊表面的接触面宽度增大,即涂油面积增大,涂油量增多,使成品纱含油率提高;反之当集束轮上移时会使成品纱含油率降低。集束轮的上下位移是有一定范围的:向上调节不可能超越涂油辊;向下调节也并不是无限制的,过度下调将使集束轮与涂油辊之间距离过长,随着拉丝机排线器的转动振荡会造成原丝抖动幅度增大,特别容易引起飞丝。
总的来说,这三种方法各有特点:用调整固含量的方法可以大范围、大幅度地调整含油率,而且简便易行,但效果较滞后;改变涂油辊转速的调整必须在工艺范围内,幅度不宜过大,而且涉及到调节机器速比,比较繁琐麻烦,仅适合于改进并确定新的生产工艺;调节集束轮位置简便快捷,效果明显,但亦不宜大幅度调整,只适用于微调。综上所述,三种方式途径不同,目标同一,各有优劣,彼此互补。我厂就是在生产过程中根据具体情况采用不同的方法对成品含油率进行控制,获得了比较好的效果。