SMC/BMC(片状模塑料/团状模塑料)是20世纪60年代在西德发展起来的一种新型玻璃钢模压材料,由于它具有轻质高强、耐腐蚀的特点,同时具有优良的电性能及成型工艺性,已广泛应用于各个领域。
在制备SMC/BMC中,要得到高品质的片材,需要控制的因素很多,但最关键的是树脂糊的粘度控制,这是影响片材质量最重要的因素。目前用于SMC/BMC的增稠剂一般有两种:①氧化镁;②二异氰酸酯化合物。
2 MgO增稠
通过不饱和聚酯(UP)的端羧基与氧化镁配位形成网状结构,进而使聚酯的粘度增大。这一增稠方式中,树脂糊的粘度可以通过两个阶段进行考察和控制,即未增稠粘度增稠粘度。
2.1 树脂未增稠粘度
树脂糊未增稠粘度即树脂在未加入增稠剂前的粘度,在增稠前,其粘度取决于配方中各种原材料的配比,原材料本身的粘度特性及作业环境的温度。在配方中,由于各原材料本身的粘度不同,以不同的比例加以混合,所得到的树脂糊粘度也各不一样,尤其是固体原材料的加入,对粘度的影响最大。其次是同一种填料,填料的粒度和吸油值不同对粘度的影响也较大。粒度和吸油值是一对矛盾,相对来说,粒度超小,吸油值就越大,反之则相反。不同吸油值的填料对树脂糊的粘度也有很大影响。所以在选择填料时,除了要考虑制品本身的功能特性外,还要根据工艺的要求合理选择一定粒度的填料。
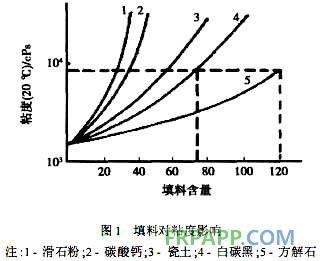
2.2 树脂糊的增稠粘度
UP中的羧基和碱金属氧化物发生反应生成中性盐和水,使树脂糊粘度大幅度上升,失去粘性,变成非粘性,这一过程叫增稠过程。在增稠反应中,碱金属氧化物只与树脂中的羧基发生反应,不干扰聚酯链和苯乙烯双键,所以增稠后的树脂不影响在制成品时的聚合反应。影响树脂增稠的因素很多,主要包括增稠剂的用量、增稠剂本身的活性、树脂酸值、水分含量以及环境温度等。
1 前 言 SMC/BMC(片状模塑料/团状模塑料)是20世纪60年代在西德发展起来的一种新型玻璃钢模压材料,由于它具有轻质高强、耐腐蚀的特点,同时具有优良的电性能及成型工艺性,已广泛应用于各个领域。 在制备SMC/BMC中,要得到高品质的片材,需要控制的因素很多,但最关键的是树脂糊的粘度控制,这是影响片材质量最重要的因素。目前用于SMC/BMC的增稠剂一般有两种:①氧化镁;②二异氰酸酯化合物。 2 MgO增稠 通过不饱和聚酯(UP)的端羧基与氧化镁配位形成网状结构,进而使聚酯的粘度增大。这一增稠方式中,树脂糊的粘度可以通过两个阶段进行考察和控制,即未增稠粘度增稠粘度。 2.1 树脂未增稠粘度 树脂糊未增稠粘度即树脂在未加入增稠剂前的粘度,在增稠前,其粘度取决于配方中各种原材料的配比,原材料本身的粘度特性及作业环境的温度。在配方中,由于各原材料本身的粘度不同,以不同的比例加以混合,所得到的树脂糊粘度也各不一样,尤其是固体原材料的加入,对粘度的影响最大。其次是同一种填料,填料的粒度和吸油值不同对粘度的影响也较大。粒度和吸油值是一对矛盾,相对来说,粒度超小,吸油值就越大,反之则相反。不同吸油值的填料对树脂糊的粘度也有很大影响。所以在选择填料时,除了要考虑制品本身的功能特性外,还要根据工艺的要求合理选择一定粒度的填料。 ![]() 2.2 树脂糊的增稠粘度 UP中的羧基和碱金属氧化物发生反应生成中性盐和水,使树脂糊粘度大幅度上升,失去粘性,变成非粘性,这一过程叫增稠过程。在增稠反应中,碱金属氧化物只与树脂中的羧基发生反应,不干扰聚酯链和苯乙烯双键,所以增稠后的树脂不影响在制成品时的聚合反应。影响树脂增稠的因素很多,主要包括增稠剂的用量、增稠剂本身的活性、树脂酸值、水分含量以及环境温度等。 |

根据增稠机理和增稠过程可知:增稠反应是一个动态平衡过程,增稠剂用量增大,增稠速度也增加,而且,如果树脂的酸值越大,表明树脂中羧基的浓度就越大,增稠的速度也越快。树脂糊中微量水分对增稠粘度有极大的影响,在增稠初期,微量水分的存在起到了增稠反应的催化作用,使增稠反应速度加剧,树脂糊粘度在短时间内达到很高的粘度;同时,增稠反应中有水生在,如果树脂糊中含水量较大,就会掏增稠反应,使树脂残留粘性,影响增稠反应的正常进行。实践表明,树脂糊中水分含量一般要求控制在0.15%以内为好。
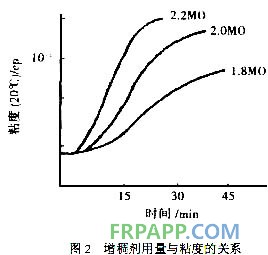
在粘度的控制当中,还有一个十分重要的因素,那就是温度,温度升高,使分子间的布朗运动加剧,利于增稠剂的扩散,同时提高了反应物的活化能,使增稠速度加快,树脂糊的增稠粘度增大。在实际生产中,树脂糊的温度控制在30~35℃之间,粘度上升比较均匀,利于SMC/BMC的制备。
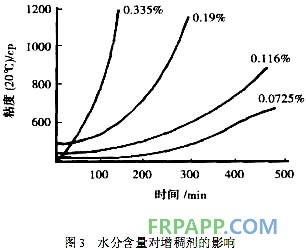
2.3 树脂糊粘度与SMC/BMC质量的关系
制备SMC/BMC是靠树脂糊浸渍玻璃纤维完成的,玻纤的浸渍质量将直接关系到片材的质量。而玻纤的浸渍质量除玻纤本身因素外,主要取决于树脂糊的粘度,同时,不同的玻纤含量要求不同的粘度才能得到良好的浸渍。玻纤含量大,要求树脂糊粘度相对要小,反之则可以适当的增大。所以控制树脂糊的粘度是制备SMC/BMC的关键工序。
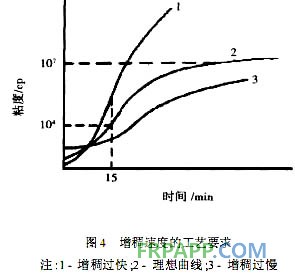
理想的增稠路线是:在片材复合的初期,要求树脂糊的粘度相对较小,以利于玻纤的浸渍,待玻纤浸渍完全后,又要求树脂糊的粘度迅速增大,不致于使胶液流失,并尽快的适合于模压操作。通常情况下,在初始的15min内,树脂糊的粘度不超过6*10(4)cp为宜。