与金属材料相比,直升机采用先进复合材料还能达到减重、抗疲劳、防腐蚀和易修补损伤等目的,特别是在功能化设计处理后,还可以提高防雷达探测能力和抗坠毁能力。与定翼机相比,旋翼直升机的飞行速度相对较慢,除了发动机部位阻燃、隔热的要求较高之外,一般来说,改性环氧树脂基复合材料的耐热等级即可以满足大部分使用要求。从抗撞损性能角度考虑,在重量等同情况下,设计机体结构时优先选用复合材料代替金属材料,因为用碳纤维复合材料制备的波纹梁地板构件已经能够吸收机身撞击时产生的大部分能量。用芳纶纤维复合材料制备的飞行员坐椅结合撞损能量吸收系统兼备了减重、减震以及复合陶瓷板防弹的功能。
复合材料的优势在旋翼桨叶的应用上得到了最充分的发挥,它使旋翼桨叶气动外形的改进以及旋翼动力学特性的优化成为可能。旋翼是外部噪音的主要来源,型面、扭曲度、端部形状的优化都能达到减少声发射的效果。设计中尽量减少凹形形状和金属零部件、采用透波/吸波材料,可减少雷达反射面积。更重要的是复合材料能使交变载荷下的旋翼寿命大幅度提高。金属桨叶的寿命一般不超过3 000h,而复合材料桨叶寿命可达10 000h至整机设计寿命。这使桨叶的全寿命成本大幅度降低,同时提高了飞机的可靠性。
桨叶芯材选用泡沫塑料/Nomex蜂窝芯还可使主桨叶具有良好的破损安全性,耐撞击,对缺口效应不敏感,弹伤后扩散缓慢,不会骤然断裂的特点,适应了武装直升机的抗易损性要求。对于桨毂材料,主要考虑抗疲劳特性,通常选用高强度玻璃纤维粗纱增强环氧树脂基体制备,这样可以同时具备很高的可靠性和抗弹伤能力。这些优点使得先进复合材料在直升机上的大量使用成为必然的发展趋势。国内在20世纪80年代从法宇航引进的“海豚”直升机制造专利技术,EC-120复合材料机身制造装配技术,特别是北京航空材料研究院研制的系列化航空级复合材料预浸料和多机型直升机承力结构部件等,都有助于扩大国产先进复合材料在新机型上的应用。
1 主桨叶用复合材料预浸料性能
直升机桨叶材料选用中温固化预浸料。预浸料用热熔胶膜法生产,主要浸渍工艺参数有纤维张力、浸渍温度、压力和走带速度等。控制树脂熔体粘度约100Pa·s、刮胶温度约70℃、走带速度约1~2m/min时比较容易成膜。为提高刚度,使用M40J碳纤维作为增强体。其复合材料指标与性能测试值见表1。模压法试制的主桨叶和桨毂组成的旋翼是直升机的升力面和操纵面。主桨叶在快速变化及复杂的空气动力环境中承受高交变气动载荷,其考核内容包括疲劳试验和疲劳寿命估算。疲劳寿命估算的原则是:在载荷作用下以变形计算为基础,对试样剖面各点扫描确定各种组合材料的当量动态最大应变值。以当量动态最大应变计算106疲劳极限,应用数理统计和MINER线性累积损伤理论,查出试样剖面各种组合材料的寿命,取最小值,再取各段的极小值给出寿命。试制件至少能够满足2 400h的装机寿命指标。

2 扭力调节杆用复合材料预浸料性能
扭力调节杆件(柔性杆)是直升机主减速器悬挂组件中的重要部件。通过前后2个柔性杆的变形吸收主减速器传递下来的振动。杆件两端分别装有承扭接头和滑动接头,主要承受弯矩和压力。复合材料不易产生突发性脆性断裂,而且其铺层可设计性能够更加充分地发挥复合材料各向异性的受力特征。
本课题选用改性环氧树脂基体及其RC10.800高强型连续玻璃纤维粗纱作为原材料。采用连续玻璃纤维窄带熔融树脂预浸机组制备了改性环氧/RC10.800连续玻璃纤维预浸料。预浸料线性质量为(24.95±0.35)g/m;幅宽为(34±0.5)mm,连续长度≥85m/盘,可以满足连续缠绕成型一根柔性杆件的要求。预浸机组的工作原理为熔融树脂直接浸渍方式,挥发分含量≤0.8%。为了使树脂含量精确地控制在(23±1)%的范围内,机组上必须安装合适的加热段和有效的挤胶辊,分别调节控制24团玻璃纤维粗纱的过程张力和窄带收卷张力,机组工作的全过程通过计算机实时控制。对制件的功能考核内容包括静刚度试验、疲劳试验和疲劳寿命分析。对复合材料基本力学性能的要求包括常温和实际工作环境温度(80℃)下的拉伸、压缩、弯曲、剪切的强度和模量,特别是材料的106疲劳极限强度,以及经过加速湿热老化处理后力学性能的变化等。为了满足这些要求并且便于热熔预浸工艺操作,试验中选用了不同种类、不同分子量的环氧树脂作为基础树脂,配合改性芳香胺类固化剂和促进剂进行优化组合。首先遇到的问题是,在生产线使用的成型工装模具和固化工艺都已经确定的前提下,只能优先调节对固化工艺影响明显的树脂基体的凝胶时间与其相适应。其中使用促进剂M的凝胶时间与设计指标最为接近。DSC曲线中的放热峰从410K至482K,峰值为440K,反应热18.51cal/g(77.50J/g)。
热熔预浸工艺参数依赖于树脂基体的流变行为,使用HAAK流变仪测试分析了树脂基体的“粘度-温度”曲线:基体在低于80℃时熔体粘度高达103Pa·s,不易平整成膜;在90~110℃范围内,粘度约为102Pa·s,比较适合使用热熔工艺制备胶膜;当温度进一步升至150~160℃时,树脂基体粘度降至最低点,约为几十Pa·s;然后随着温度升高而很快进入凝胶状态。对比热熔预浸工艺前后基体树脂的“粘度-温度”曲线可见,热熔预浸工艺过程没有明显降低树脂基体的操作期。
研制的RC10.800热熔预浸料的物理性能见表2,从表中可见,挥发分含量仅为0.4%,有利于降低制件的孔隙率,提高疲劳寿命;要求预浸料线性质量在±0.35g/m的范围内波动,有利于预浸机组参数的精确调节。
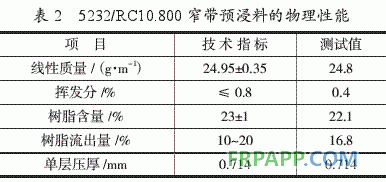
使用研制的改性环氧5232/RC10.800预浸料,按照规定的固化工艺制样,测试了研制材料的基本静态力学性能,以及百万次弯曲、拉伸和剪切疲劳极限强度等动态性能。抗环境性能测试采用48h水煮快速老化试验。其中A表示试样经过48h水煮后立刻进行测试;B表示试样经过48h水煮,再置入100℃烘箱内干燥处理24h后进行测试。测试结果见表3。从表3中的力学性能测试结果可见,研制的改性环氧5232/RC10.800复合材料力学性能实测值与要求的技术指标基本相当,可以进行制件的批生产工艺试验。
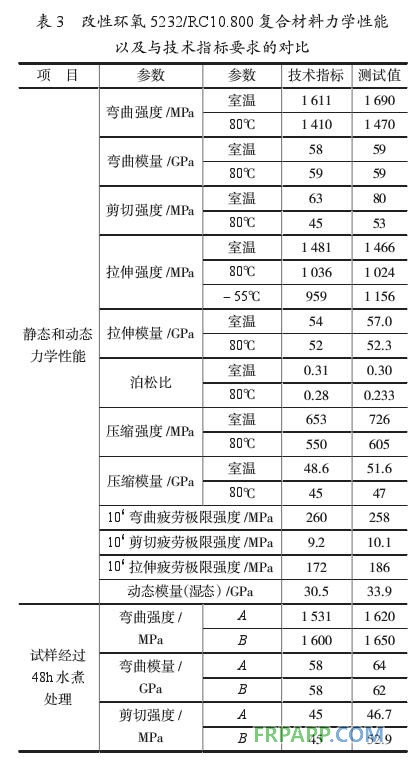
3 波纹梁用复合材料预浸料性能
按照设计图纸要求,选用本课题组研制的4种5224改性环氧树脂基碳纤维预浸料制备波纹梁。它们分别是由热熔法预浸工艺制备的5224/G803缎纹碳布、5224/G827单向碳布、用于制件局部表层的5224/914Kevlar布和5224/T300无纬带,其挥发分含量指标明显低于使用通常溶液法制备的预浸料,而且树脂含量很容易通过胶膜厚度的精确调节进行控制,其物理性能见表4。上述4种5224改性环氧树脂基预浸料具备良好的铺覆工艺性。
按设计铺层在不同阶段进行预压实处理,以确保波纹梁制件的孔隙率降至最低,并使制件厚度尺寸满足设计图纸的要求。
测试了树脂基体的“粘度-温度”曲线。树脂基体在常温时具有较高的粘度,随着温度上升至120℃,粘度从几千降至几十Pa·s;然后在140~150℃时进入凝胶状态,形成交联网络。树脂基体属于增韧环氧,流动度较小,模具周边预加工几个排胶孔以防制品积胶。考虑到钢制组合模具的质量达数百kg,固化过程中模具温度明显滞后于热压罐的温升速率,所以取消中间的保温阶段,依靠相对缓慢的升温速率来保证钢制模具的实测温度与设定温度同步。加压在树脂进入凝胶点之前进行,有利于夹裹在树脂内的残余挥发分含量尽可能被最后排挤出体系,消除产生孔隙率的根源。
装入组合模具内的预浸料坯固化成型工艺条件是:在室温抽真空,真空度至少要达到0.09MPa;然后以1.5~2℃/min的升温速率从室温升至(135±5)℃时开始加压(0.6±0.1)MPa;继续升温至180℃,恒温2h后卸真空和外压;自然降温至60℃以下,卸模。5244/G803、5244/G827和5224/T300碳/环氧复合材料随炉试片的基本静态力学性能见表5。从表中的测试结果可见,随炉试片的拉伸、压缩、弯曲强度和模量,以及剪切强度都符合相应材料标准规定的使用要求。
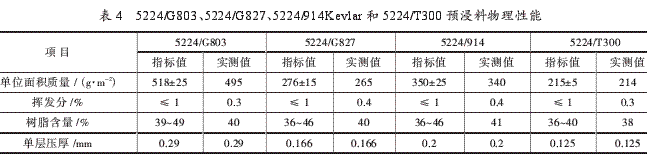
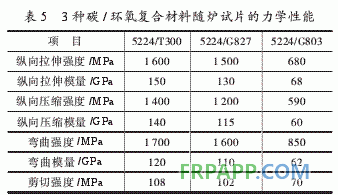
成型过程中采用软模和真空袋协同加压方式,目的在于尽可能将预浸料坯整体压实。波纹梁两端桁板与幅板拐角处能否压制到图纸要求的倒角尺寸并使此处纤维排列不紊乱,是成型工艺中的操作难点。为了使软模和钢模之间在拐角处的成型压力均衡有效,操作过程中尽可能只铺设单层吸胶毡。卸模后发现此层吸胶毡已经大部分吸满挤出的树脂胶液,且制件重量超出设计值约5%。作为改进措施,试用平均降低3%树脂含量的碳布预浸料重复进行上述成型试验,取得了相应的减重效果。
按照复合材料构件通用技术条件(HB7224-95),使用接触脉冲反射法、USIP12型超声波探伤仪(5MHz聚焦探头)对使用不同树脂含量预浸料成型的碳/环氧复合材料波纹梁制件进行检测。其原理是利用材料与缺陷区域对超声波信号反射幅度的差别,检测复合材料内部的裂纹、脱粘、孔隙及分层等缺陷。检测后均未发现上述制备过程缺陷,制件都可以通过此标准中规定的“一级”无损检测指标。波纹梁结构元件的静态和动态力学性能进行了测试。钢制组合模具配合硅橡胶软模适合用于制备满足型面尺寸要求的直升机用复合材料波纹梁承力结构元件。5224碳/环氧预浸料满足波纹梁制件的成型工艺要求,、其最大特点是无损检测合格率高。
4 结束语
研制的直升机用先进复合材料部件通过了试验室阶段评审、工厂工艺试验和试验台功能考核,性能满足设计要求。