碳纤维90%以上是碳原子,和其他金属相比质量较轻。另外,因碳分子是按纤维方向规则排列的二维网状结构,因而拥有强韧的特性。
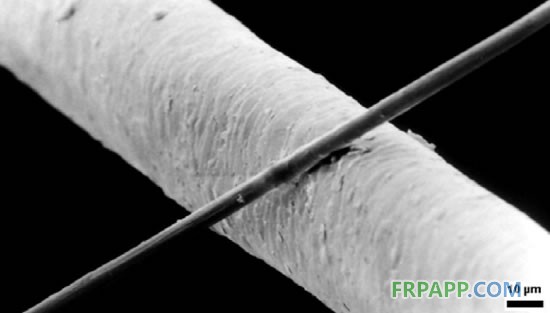
CFRP泛指由碳纤维和聚合物树脂复合而成的碳纤维复合材料料,环氧树脂CFRP其比强度、比模量综合指标,在现有结构材料中是最高的。CFRP抗拉强度一般都在3500Mpa以上,是钢的7到9倍,抗拉弹性模量为230到430Gpa亦高于钢,但它的比重却不到钢的1/4;CFRP的比强度达到2000Mpa以上,而A3钢的比强度仅为59Mpa左右,其比模量也比钢高。
CFRP不仅轻而强,轻而刚而且具有耐高温、耐腐蚀、耐疲劳、结构尺寸稳定性好以及设计性好、可大面积整体成型等一系列特点,所以在汽车轻量化中得到不断增长的应用。
CFRP还具有非常卓越的能量吸收性能,从而进一步保证了CFRP车辆的安全。据报道,在柱式撞击和侧面撞击中,CFRP材料均表现出了优越的安全性能。即使在局部承受较重的点式力量时,CFRP也决不会凹陷。乘客和电池组件能得到完美地保护。CFRP零部件比同类钢质零部件减重50%以上,比铝制部件减重30%以上,却能够提供同等强度。
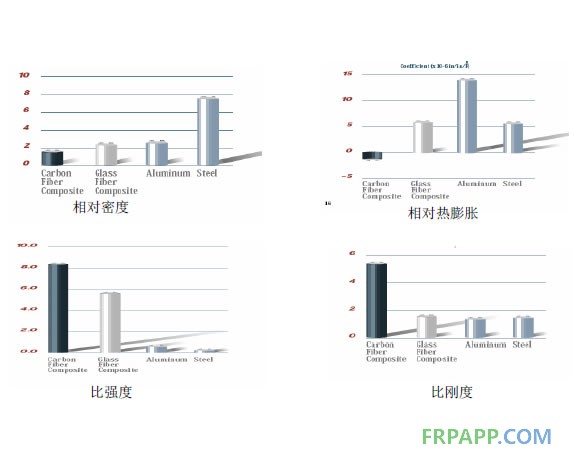
CFRP是新能源汽车必然选择
政府制定严格的车辆燃料经济性标准和二氧化碳排放法规是新能源汽车选择CFRP的重要推手。以美国为例,2017至2025年美国新款乘用车的燃料效率要求达到4.32升/ 100公里,比当前车辆水平几乎提高一倍。据估算,典型的乘用车需减重245kg才能达到此目标。
电动汽车的结构型式所需的条件非常独特:电动汽车的传动系要比满油箱的内燃机汽车的传动系还要重,在同样续驶里程条件下,电动汽车的重量比传统汽车要超过200~300 kg甚至更多。因此为保证电动汽车有较好续驶里程和可承受的成本,电动汽车的车身重量必须减重50%以上。在所有轻量化材料中,CFRP是唯一能将钢质零部件减重50~60%,却能够提供同等强度的先进材料。
CFRP的主要优势在于它的强度重量比和刚度重量比,除此之外,CFRP还拥有较高的抗腐蚀性和较强的气候稳定性,其使用寿命明显长于金属材料,无须昂贵的防腐蚀保护措施。另外,CFRP材料具有非常卓越的能量吸收性能。在柱式撞击和侧面撞击试验中,CFRP材料均表现出了优越的安全性能。
从创意设计开始就定位轻量化、大批量、低成本的技术路线
对新能源汽车,特别是纯电动汽车而言,从创意设计开始始终如一最大限度考虑车辆轻量化十分重要,因为除了平衡蓄电池增加的重量,车辆重量也是限制续驶里程的一个重要因素。
对新能源汽车,在研发CFRP部件的制造工艺同时应同时考虑使其实现生产自动化,从而使得这一生产工艺可以在高生产安全性条件下实现经济的、高品质的大规模生产非常重要。
CFRP在新能源汽车上的应用并非强度、模量越高越好,而是在滿足新能源汽车强度安全的前提下,成本越便宜越好。不仅应推广价格便宜的大丝束碳纤维及其工艺制品还可适当地采用回收碳纤维,最大限度地降低新能源汽车的制造成本。
在全价值链坚持可持续发展,落实可持续性量化目标
在新能源汽车全价值链中坚持可持续发展,具体制定落实可持续性量化目标是新能源汽车开发获得成功的关键所在。我们不能一方面为节能减排开发新能源汽车另一方面在新能源汽车全价值链方面破坏或浪费环境资源。
新能源汽车可持续性发展同样具有三个层面的含义:生态、经济和社会。生态的可持续性指要保持自然和环境适于后代人的生存和发展,也就是我们这代人在资源利用上要承担起相应的责任。经济的可持续性要求经济交往能为竞争和繁荣提供一个可持续、具有足够承受能力的基础。社会的可持续性要求社会的发展可以让一个群体的所有成员有机会参与其中。
新能源汽车应用CFRP减重节能减排是环保的,但生产使用CFRP也会产生大量生产废料和报废旧车的CFRP部件,这在新能源汽车开发初期必须要加以认真考虑和解决。CFRP废料和废旧车身零部件应按种类进行分类收集处理并积极用于循环再造的工艺,并且这一工艺能适应批量生产的需要或用于其它用途,以降低成夲和节省宝贵的资源。
实事求是,走扬长避短、合作共赢之路
GFRP在汽车中的应用在世界上已有六十多年的悠久历史,CFRP在世界F1赛车中的应用也有将近四十年历史,国外尤其是欧美在汽车CFRP上积累了较丰富的设计、制造、应用方面的经验和大量的成功范例,而在中国汽车CFRP领域我们基夲上是空白,存在较大的差距这是一个基本事实。
根据复合材料定义,我们知道复合材料因为不是特定的物质,而是材料使用方法的概念,它不受特定材料性能的限制,可以根据用户的需求通过选择不同的原材料组合进行自主设计,所以,复合材料的结构设计及其优化是一项基础性和应用性很强的工作,需要有数据库和丰富的实践经验。
不同的成型工艺会导致复合材料产品的性能和成本出现较大的差别。同时复合材料构件的形状、原材料的性能也是影响其成型工艺的主要因素。
复合材料的结构优化是一个非常复杂的问题,复合材料失效准则及失效模型的不完善限制了复合材料优化设计的发展,目前国内对复合材料的优化设计研究仍然处于发展的初步阶段。
德国宝马CFRP新能源汽车案例
BMW i3碳纤维单体构造乘员舱具备了高韧性与高吸收能量能力,在Euro NCAP的测试中,i3於64km/h正面撞击与32km/h侧面撞击测试中都获得了优异成績。
德国宝马公司已量产的i3系4人座纯电动汽車采用了CFRP制造的单体构造乘员舱模块以及铝合金构造的底盘模块,整备质量仅为1195kg,其中锂离子电池重量为230kg,CFRP重量为140kg,比传统电动车减轻了250~350kg。
日本东丽CFRP新能源汽车案例
日本东丽公司开发的两人座TEEWAVE AR1纯电动概念車整备质量仅为846kg,其中锂离子电池重量为220kg,CFRP使用约160kg ,比起钢制汽車重量減少53%。
东丽CFRP单体车身构造为中空构造一体成型,重量仅为45kg,远低于钢制EV车体的50%;部件数量仅为3件,是钢制EV车体的1/20 ,成型周期不到10分钟。
韩国现代CFRP新能源汽车案例
韩国现代Intrado燃料电池概念车一次补充燃料可行驶644km,百公里加速时间将低于12秒。
现代Intrado概念车的全车架、引擎盖以及侧板采用CFRP,质量比传统钢板制造的轻60%,这将大大提高燃油效率。
中国奇瑞CFRP新能源汽车案例
奇瑞公司在今年的北京车展上推出了插电式混合动力车艾瑞泽7,这款车的碳纤维车身是由奇瑞和中国科学院共同研究打造的,奇瑞称这是中国第一台车身主体由碳纤维复合材料构成的车型。
中国长城华冠CFRP新能源汽车案例
在今年的北京车展上北京长城华冠汽车技术开发有限公司发布了该公司的最新作品,一款名为前途(EVENT)的纯电动跑车概念车。据介绍,作为首款中国自主研发具备量产状态的纯电动跑车,以节能、环保为设计出发点,产品集成了众多汽车行业的前沿科技,提供了真正意义上满足用户使用的纯电动车产品。
长城华冠EVENT车体内外覆盖件整体采用CFRP材料,从而使得产品本身既能保证优于传统金属钣金的力学及安全性能,又使得产品重量大幅度降低,提高了产品的动力性、经济性。