0 前言
毛羽现象一直是困扰玻璃纤维生产的重要问题。解决毛羽问题实际上是一个系统工程,从浸润剂到拉丝、烘干、退解、织造,每道工序均有许多值得关注的细节,但在生产中往往容易忽视。引起玻纤毛丝的原因很多,从生产工艺角度来分析有:玻璃融化不好及澄清不良、拉丝工艺参数设置不合理、烘干工艺或原丝调理工艺不当等。从浸润剂角度来分析有:成膜剂配方不合理、浸润剂含量偏低、浸润剂使用环节不当等。从加工工艺的角度分析有:环境温湿度、退解(络纱)工艺、原丝调理工艺、烘干工艺等。本文主要从浸润剂技术、玻璃熔制工艺、拉丝工艺、加工环境、退捻(络纱)工艺、烘干工艺等几个方面分析毛羽产生的原因及预防。
1 、玻璃纤维
玻璃纤维是一种性能优异的无机非金属材料,主要成分为二氧化硅、氧化铝、氧化钙、氧化镁、氧化钠等。玻璃纤维单丝的直径从几个微米到二十几米个微米,相当于一根头发丝的 1/20-1/5 ,每束纤维原丝都有数百根甚至上千根单丝组成,通常作为复材料中的增强材料,电绝缘材料和绝热保温材料,电路基板等,广泛应用于国民经济各个领域。
玻璃纤维之特性:
(1)拉伸强度高,伸长小(3%)。
(2)弹性系数高,刚性佳。
(3)弹性限度内伸长量大且拉伸强度高,故吸收冲击能量大。
(4)为无机纤维,具不燃性,耐化学性佳。
(5)吸水性小。
(6)尺度安定性,耐热性均佳。
(7)加工性佳,可作成股、束、毡、织布等不同形态之产品。
(8)透明可透过光线。
(9)与树脂接着性良好之表面处理剂之开发完成。
2、玻璃纤维的性能
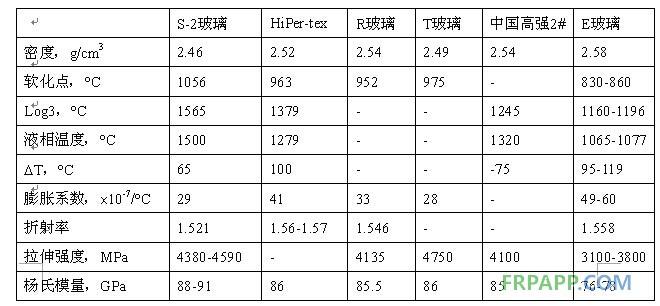
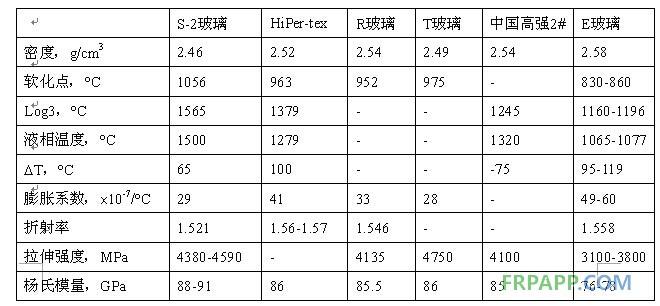
3、毛羽的危害
由于玻纤高模量、低伸长率,加工过程中易产生高张力,从而发生脆性断裂。无碱纤维脆性最小,中碱次之。玻纤纱断裂时,一个断裂点形成两根毛丝。从毛丝的形态来分还可分为长毛丝、短毛丝、绒毛、毛团等。毛丝可造成以下危害。
(1) 造成纱线强度降低。
(2) 给后道工序使用带来困难,如单丝涂塑窗纱用玻纤细纱和长纤增强热塑性塑料用玻纤长丝,对纱的光洁度、完整性和集束性要求很高,稍有毛丝即不能正常生产。
2 毛丝产生的原因及解决措施
2.1 原丝浸润剂含量偏低会造成原丝集束不良,单根散丝极易磨断磨毛,出现大量的毛丝。
解决措施:
(1)适当提高浸润剂固含量,研究发现中碱池窑生产的原丝由于喷雾等原因,需要适当提高浸润剂固含量才能保障原丝含油率。
(2)提高浸润剂附着力,在浸润剂中添加聚乙烯醇(PVA)、聚乙烯吡咯烷酮(PVPK)等高粘度物质,可使浸润剂粘度提高。
(3)控制喷雾流量,及时检查雾化状态。
(4)及时解决单丝涂油器石墨辊出现鱼眼和花辊现象,就及时清洗或更换涂油辊。
2.2玻璃熔化不好或澄清不良毛丝,由于未融化好的玻璃存在结石、气泡等缺陷会在加工过程中造成单纤维断裂而产生毛羽。
解决措施:
(1)稳定玻璃的熔制工艺,提高熔化质量。
(2)使用鼓泡技术强化玻璃的澄清。
(2)使用鼓泡技术强化玻璃的澄清。
2.2浸润剂配方对毛羽的影响。浸润剂成膜剂、润滑剂、偶联剂等成分均对毛羽的产生有重要的影响。
解决措施:
(1)选用适当的成膜剂。环氧酯,利用环氧酯基团反应活性大、易开环的特点,接上各种浸润剂性能所需的分子链段。线性饱和聚酯,在浸润剂中还可起到润滑增塑作用,用作硬质纱增塑剂,渗透快,不易迁移。还可用于树脂型纺织浸润剂,柔软、爽滑、减少毛丝。水性聚氨酯。水性聚氨酯成膜后强度高、弹性好,对玻纤保护集束作用好,可减少毛丝。
(2)选用适当的润滑剂润滑剂对减少玻纤毛丝起着至关重要的作用,玻纤浸润剂中使用的润滑剂大致可分为非离子及阳离子润滑剂两大类。非离子润滑剂有:乙氯基脂肪酸硫酸盐及其衍生物、咪唑啉、二甲基硅油乳液、磷脂酸等。阳离子润滑剂有:脂肪酸季铵盐、脂肪酸磷酸氢盐、脂肪酸四乙烯或胺络合物等。玻纤表面强烈吸附水分,并使水分子极化,水分子中H+与SiO-,AlO-牢固结合,造成OH-向外,所以玻纤表面为阴离子性的。因此玻纤润滑剂中广泛采用阳离子型润滑剂,其与玻纤表面结合良好,减少毛丝。对于硬质纱浸润剂可采用2~3种阳离子润滑剂,而软质纱浸润剂为使膜柔软、增塑,一般为非离子润滑剂与阳离子润滑剂同时使用。浸润剂配方中润滑剂的用量一定要适当。一般阳离子湿态润滑剂用量在0.2%以下,过多则易造成原丝筒变形,如果是硬筒拉丝就会形成喇叭筒,软筒拉丝就会造成原丝筒塌筒、退解困难,都会造成毛丝。干态润滑剂的用量也要控制适当,过多则影响纱的集束性,尤其在成膜剂的玻璃化温度较低,膜整体偏软的情况下,这样退纱或织造时易粘附于机件上,形成黑色粘稠物,会引起毛丝。
(3)选用适当的偶联剂。浸润剂中偶联剂与玻纤表面以-Si-O-Si-健结合,修补玻纤表面微裂纹,阻止玻纤在微裂纹应力集中处断裂,可减少毛丝。对于增强型浸润剂,偶联剂变质或偶联剂水解不良也是造成毛丝的因素之一。
2.3浸润剂使用不当造成的毛羽。由于浸润剂使用过程中温度的变化造成浸润效果的变化,及循环油固含量的变化都会影响原丝浸润剂含量进而造成加工过程中产生毛羽。
解决措施:
(1)严格控制好小循环的浸润剂固含量及其波动(严格控制好喷雾角-控制好喷雾水侵入浸润剂的侵入量);
(2)严格控制好各个小循环所带涂油器的数量;
(3)严格控制好浸润剂温度;
(4)严格控制原丝饼的原始含水率。原丝饼的含水率反应原丝束“吃油”的好坏和充分程度;过多的原丝含水率又会造成浸润剂的迁移加重。因此,原丝饼的原始含水率必须严格控制。
2.4 拉丝工艺参数设置不合理也容易造成毛羽。拉丝工艺参数设置不合理容易造成原丝成型不好、张力过大等。
解决措施有以下几点:
(1) 调节工艺位置,尤其是控制好扇形单丝在石墨辊上的包角和集束轮位置。将单丝包角尽可能调整小,一般为3o左右,这样可以有效地降低拉丝张力。同时集束轮槽要定期转动一定的角度,否则会磨宽,造成原丝散丝并产生毛丝。
(2) 根据不同的浸润剂性能及原丝品种选择不同的卷绕比。卷绕比=机头转速/排线转速。即排线旋转一周时,机头的旋转圈数。卷绕比的意义在于控制卷绕角、原丝缠绕的重复性,决定了退解效率和丝饼退绕效率。卷绕角越高,成型约稳定。为使得丝饼顺利退解,一般要大于6o。如丝饼重量小,厚度小,可使用较小的角度。平行排丝会造成退解时脱圈。主要控制速比不能为整数或整分数,一般在三位小数以上。
(3) 根据原丝品种选择不同的排线钢丝。螺旋排线钢丝为原丝提供一个高速移动,并按预定模式缠绕到原丝筒上。螺旋排线的几何形式是基于阿基米德曲线,并产生线性运动,但原丝的性能会改变这种运动并导致产生波形动作。排线钢丝规格(形状、材料)是决定排线效果的极为重要的因素。排线钢丝形状不准确、局部过度磨损(造成形状改变)、排线钢丝变形、安装不准确(指高、低端安装时的外露尺寸和每副排线钢丝安装的对称、端脚的平行度等等)、材料过软(没有一定的弹性、刚性)、材料不纯、不爽滑(材料本身低劣、有毛刺、裂纹等)。
(4)漏板温度不均匀产生的毛羽。漏板温度不均匀致使拉丝过程中单丝张力不均,造成原丝泡泡纱,加工过程中单纤维断裂产生毛羽。经试验二者造成毛羽的程度相差40%。
2.5绕丝筒上原丝间粘并如果绕丝筒上原丝左右、上下之间粘并,在退解时一股纱退出往往造成另一股纱受损,只要有一根或几根单丝断裂就会造成大面积网状毛纱,粘并严重时还会造成退解、脱圈。因此这也是毛丝现象产生的一类重要原因。
解决措施:
(1)适当降低原丝浸润剂含量。浸润剂含量过高时在原丝之间产生粘并,造成退解时单纤维断裂引起毛羽。
(2) 浸润剂配方中可添加少量具有隔离效果的润滑剂。既起到良好的润滑作用,又可起到隔离防粘并效果。
2.6 原丝爽滑性不够,与导纱材料动摩擦系数大摩擦是造成毛丝的最直接原因。
解决措施如下:
(1) 提高导纱材料的光洁度和耐磨性。
(2) 络纱时将滑动摩擦改为滚动摩擦,减少接触点,磨擦系数。
(3) 提高原丝的爽滑性。第一是检查浸润剂中干润滑剂用量是否足够。第二是浸润剂配方中添加高效的润滑剂。使用过程要注意润滑剂用量不需要很大,否则容易引起散丝,加剧毛羽的产生。
2.7 静电过大
静电会造成原丝对各摩擦点的粘附,并造成纱线蓬松、散丝,增加毛丝。因此在浸润剂中添加抗静电剂,消除静电的不利影响。常用的抗静电剂有:无机抗静电剂如氯化铵、氯化锂、硝酸锂等;有机抗静电剂如SN等。抗静电剂的用量一般为0.05%~0.3%。配制浸润剂时,抗静电剂要充分稀释后再加入配制罐中,避免电解质浓度过高影响成膜剂乳液的稳定性。纺织纱退解时捻线机接触纱线的各部件可抹上一薄层有机抗静电剂,实践证明这样也可有效地减少毛丝的产生。
2.7 原丝筒温湿度控制不好。
解决措施:
(1)根据不同的成膜剂体系制定适宜的调制工艺,特别是纺织细纱。适宜的调理工艺有利于浸润剂更好的成膜,加工过程中可以对原丝提供良好的保护,从而减少毛羽的产生。我们在生产单丝涂塑纱的过程中对比同一批次的原丝在不同的调理工艺下,毛羽产生的程度高达56%。
(2)控制退解(络纱)车间温湿度。玻璃纤维加工过程中受温、湿度的影响极大,适宜的温湿度可以减少加工过程中毛羽的产生。一般情况下纺织纱控制在温度23℃左右、相对湿度60%左右比较合适。
2.8烘干工艺不当造成的毛羽,原丝未完全烘干或烘干过度、纱线发脆对都会引起玻纤制品的毛丝。
解决措施:
(1)原丝未烘干或未达到浸润剂成膜所需的烘干温度及时间,浸润剂中各组份分相,未充分融合成一完整膜,此时原丝集束抱合力差,散丝,同时纱线不滑爽,摩擦系数大,毛丝多。
(2)原丝筒刚进烘房时,起始温度不能太高,并要加强排湿,尤其是张力过大、卷绕过紧的原丝筒、超大原丝筒、直接无捻粗纱团,更要增大排湿量和热风循环。
(3)采用微波烘干或微波辅助烘干,可降低迁移,对减少毛丝有帮助。
2.9退捻(络纱)工艺不当产生的毛羽。退捻(络纱)过程中由于纱线高速运动,集束不好的单根纤维极易因张力过大而断裂而产生毛羽。
解决措施:
(1)根据不同的纱线选择不同的成型方式及车速。由于纱线张力在很大程度上决定于车速,因此必须严格控制车速在合适的范围内,特别是纺织纱及硬质纱。硬质纱络纱工艺不当容易造成浸润剂膜破裂,纱线硬挺度降低、集束性不好从而影响使用效果。
(2)对纺织细纱根据不同的品种选择合适的尼龙勾。
A、尼龙钩的形状对毛羽的影响
根据生产实践得出,曲率半径大的尼龙钩曲面状呈圆形,与纱线接触的摩擦力相对小,纱线弯折的幅度小,断裂的玻璃纤维少使得毛羽少,对纱线的硬挺度影响小;而曲率半径小的尼龙钩曲面呈三角形,与纱线接触的摩擦力相对大,纱线弯折幅度大,使玻璃纤维纱线容易断裂而产生毛羽,并且会影响纱线的集束性,使纱线硬挺度降低。如图1所示。
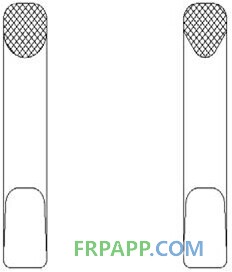
圆形曲线 三角形曲线
图1 尼龙钩与纱线接触示意图
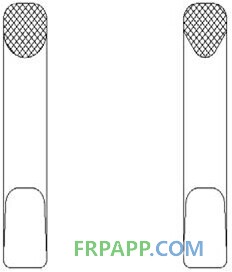
圆形曲线 三角形曲线
图1 尼龙钩与纱线接触示意图
图2所示为采用质量200,mg的尼龙钩,形状分别为三角曲面和圆形曲面,捻线后检测的毛羽分布图,分别检测了管纱内层、中层和外层的毛羽情况。从图2可以看出,三角曲面对纱线毛羽的影响更大,不利于玻璃纤维纱线的加捻;而圆曲面对纱线毛羽影响相对较小。此外,尼龙钩在与钢领配合中,由于外形不同也会形成纱线通路空间的大小不同,造成对纱线毛羽的不同影响。细线为三角形曲面,粗线为圆形曲面。
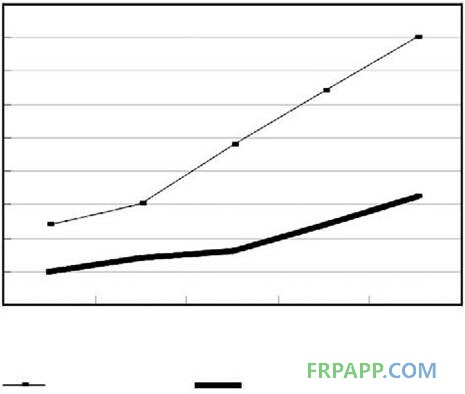
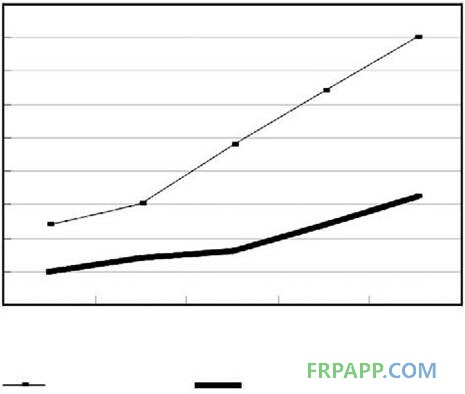
图2
B、尼龙钩的材质对毛羽的影响
玻璃纤维纱对捻线机尼龙钩的要求是具有良好的耐磨,尼龙钩长期裸露在外面,会吸收空气中的水分,影响尼龙钩的重量,从而影响纱线张力而容易产生毛羽。因此,尼龙钩必须在密封条件下运输和保存,开封后的在使用后也要立即密封保存。
C、尼龙钩的重量对毛羽的影响
如果尼龙钩重量过重会造成气圈小,纱线受到的张力过大,就会增大尼龙钩与纱线摩擦力,会造成纱线断裂,形成毛羽的几率加大。同时钢领容易磨损,捻出的管纱卷绕硬度大,纱线硬挺度降低,对减少成纱毛羽和断头都不利,卷绕过程中会产生较多毛羽。如果尼龙钩重量过轻,纺纱张力过小,运行不稳定,气圈大,捻头轻,纱线抖动,气圈膨胀,尼龙钩与纱线摩擦相对小,但易碰击隔纱板产生毛羽,并且管纱卷绕硬度过小,容易变形,不利于退解。
我们在实际生产中总结出加捻不同线密度的玻璃纤维纱,应该选择不同重量的尼龙钩以适应捻线卷绕工艺,具体数据见表1。
表1 根据不同纱线线密度选择不同重量的尼龙钩
玻璃纤维纱线 136 68 34
线密度/tex
|
选用尼龙钩 420~450 190~210 110~125
质量/mg
|
D、尼龙钩使用时间对毛羽的影响
通过测试数据的分析,我们认为随着使用时间的增加,尼龙钩在钢领上的磨损增加,会增加产生毛羽的比例。由实践中我们得出玻璃纤维的线密度不同,尼龙钩的使用时间也不同,如表2。
表2 玻璃纤维纱线的线密度与尼龙钩使用时间的关系
玻璃纤维纱线 136 68 34
线密度/tex
|
尼龙钩使用 24~36 24~36 24
时间/h
|
4 结论
玻纤浸润剂的配方设计、配制工艺均与玻纤纱的毛丝问题息息相关。文中介绍了一些使用效果较好的润滑剂可供选用,并建议成膜剂的选择也要考虑既具有成膜性又具有润滑性。除了浸润剂的使用要注意解决毛丝问题,同时控制玻纤拉丝的张力、降低原丝退解时的摩擦、有效控制原丝的烘干条件等生产工艺控制也是解决毛丝问题的关键。另外,加强操作工的责任心、提高企业管理水平,都是解决毛丝问题的关键所在。玻纤毛丝问题产生的原因是多种多样的,关键是要能通过表象分析出内在的原因,然后根据分析出的原因实施有效地解决措施。