1. 引言
随着科学技术的发展,对材料性能的要求日益提高,单质材料很难满足性能的综合要求和高指标要求。而复合材料与单质复合材料的性能相比,性能更加优越。近年来,复合材料得到了迅猛发展,广泛应用于航空航天工业和汽车工业领域。
复合材料一般由增强体和基体组成,经过设计,通过对原材料的选择、各组分分布的设计和工艺条件的保证等,使原组分材料优点互补,呈现出优越的综合性能,如高强度、高模量和低密度等。纤维增强复合材料是由高强度高模量纤维、树脂基体以及纤维和树脂间的界面构成。传统的纤维增强复合材料的成本较高,层压复合材料因为缺少Z向的纱线,在厚度方向的力学性能较差。三维机织复合材料的出现克服了传统层压复合材料容易分层的缺陷,而且预制件是一块整体,具有近似网状的结构,减少了工艺流程,降低了成本,具有优良的抗冲击性能[1, 2]。
近年来,对混杂结构增强复合材料的研究得到了发展。因为混杂结构,即在同一块基体中,含有多种增强体,能满足设计者特别的要求。混杂的主要目的:获得较高性能的复合材料,既保持材料原有的优点,又能克服本身的缺陷;降低成本,使用比较廉价的材料作为复合材料的组分,但不影响性能。
玄武岩连续纤维具有优良的物理机械性能,拉伸强度、弹性模量及断裂伸长都比较大,在一些应用领域内完全可以代替玻璃纤维、碳纤维等充当复合材料的增强体,而且性价比非常优越[7-9]。玄武岩连续纤维的使用范围特别广,还具有很强的耐酸、耐碱性能,高电绝缘性能及对电磁波的高透过性,隔热、隔音特性,防电磁辐射的特性,过滤净化特性等性能,因而得到广泛的应用。
芳纶纤维具有超高强度、高模量、耐高温、耐酸耐碱、质量轻等优良性能,芳纶可用作先进复合材料,用于航空航天领域、舰船、汽车工业中;用作防弹制品,可以用来制作硬质防弹装甲板、软质防弹背心;可以用于基础设施和建材、芳纶增强混凝土、芳纶增强木材、传送带、缆绳、特种防护服装、体育运动器材、电子设备等方面[10]。
本文主要制作了三维正交混杂机织(芳纶/玄武岩纤维)复合材料,通过比较两种混杂结构复合材料拉伸和剪切性能,探讨了混杂模式对混杂复合材料拉伸和剪切性能的影响。
2. 实验部分
2.1材料
所用的两种纤维是玄武岩纤维和芳纶纤维 (Kevlar 129),其中玄武岩纱线密度为670tex;芳纶纱线密度为314tex。树脂基体为环氧618和固化剂5510。
2.2制作工艺
2.2.1三维编织工艺
三维织造工艺在三维正交织机上完成。在本实验中,在三维正交织机上织造了两种不同的织物,分别是层间混杂结构和层内混杂结构。所谓的层间混杂结构,就是与传统混杂结构相似,在经向和纬向上包含一层玄武岩纱线和一层芳纶纱线;层内混杂结构就是在同一层中玄武岩纱线和芳纶纱线交替排列。层内混杂结构的预制件比较复杂,需要双向引纬,因此,在经向和纬向上,玄武岩纱线和芳纶交替排列。预制件的经纬密度为5根/cm,六层经纱,七层纬纱。三维正交织物结构如图1所示。
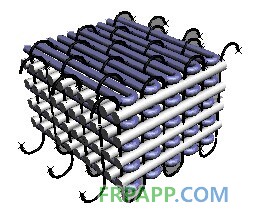
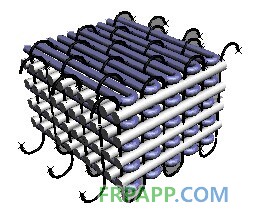
图1 三维正交织物结构
2.2.2复合材料固化工艺
采用真空辅助树脂转移成型方法固化制作复合材料。在压强为0.7MPa的条件下,浸润预制件,从室温升高到80℃,保持2小时,再升温至100℃,保持0.5小时,再降至室温,完成固化。
2.3物理性能
2.3.1密度测量
采用排水量的方法测量复合材料的密度。将每种复合材料制成25cm×25cm的试样,浸润在水中,记录排出水的体积值。在电子天平上称量每件试样的重量,并记录,计算出每件试样的密度。如表1所示。
表1 混杂复合材料的密度
复合材料
|
经纱层数
|
纬纱层数
|
复合材料密度
(g/cm3)
|
厚度(mm)
|
纤维种类
|
|
经纱
|
纬纱
|
|||||
层间混杂
|
6
|
7
|
1.51
|
5.10 ±0.05
|
K+B
|
K+B
|
层内混杂
|
6
|
7
|
1.44
|
5.00 ±0.07
|
K+B
|
K+B
|
注:表中K表示芳纶纤维(314tex),B表示玄武岩纤维(670tex)。
2.3.2计算体积含量
本实验采用试样法直接计算纤维体积含量。将每种复合材料制成100mm×100mm的试样。用排水量法测出每件试样的体积。分别数出经向和纬向的纱线数量,包括Z纱的数量。根据已知的纱线特数,可以计算出每件试样中芳纶纤维和玄武岩纤维的重量和体积,考虑到复合材料中的空隙,进而得出基体、芳纶纤维和玄武岩纤维的体积含量,如表2所示。
表2 混杂复合材料的纤维和基体体积含量
复合材料
|
经纱
|
纬纱
|
Z纱(%)
|
总的纤维体积含量(%)
|
基体(%)
|
||
玄武岩纤维(%)
|
芳纶纤维 (%)
|
玄武岩纤维 (%)
|
芳纶纤维(%)
|
||||
层间混杂
|
6.03
|
6.89
|
11.92
|
18.17
|
8.19
|
51.20
|
48.8
|
层内混杂
|
6.26
|
7.15
|
14.22
|
16.27
|
6.82
|
50.72
|
49.27
|
2.4拉伸测试
2.4.1试样制作
本实验中,对于两种三维机织混杂复合材料即层间混杂和层内混杂,分别准备三种试样:0°(经向)/45°/90°(纬向)。对于0°和90°,分别制作了5个试样。对于 45°,制作了三个试样。所有的试样是根据GB/T1447-2005标准制作的。在喷水切割机上切割试样。试样在0°和90°方向上切割成25mm×250 mm的矩形。然后将其打磨成狗骨头形,如图2所示。试样的最小宽度是10mm. 试样在45°方向上也切割成25mm×250 mm的矩形。
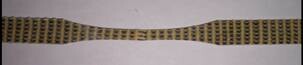
图2拉伸测试试样
2.4.2拉伸和剪切测试工艺
根据GB/T 1447-2005标准测试方法测试拉伸性能。Instron 3382 可以加载100KN。对层间混杂和层内混杂复合材料进行测试。两种复合材料分别在经向(0°) 和纬向(90°)进行拉伸测试,每组五个试样。通过载荷峰值和试样的截面积来计算拉伸强度。在试样中间贴有应变片,通过这些试样的应力—应变曲线计算出杨氏模量。分别将拉伸强度和杨氏模量比上对应方向纤维的体积含量,得到归一化强度和归一化模量。在±45°方向上进行偏轴拉伸测试,每组三个试样,测试其剪切性能。夹头的加载速度为3 mm/min,隔距为10 cm。
3. 结果与讨论
3.1 混杂复合材料的拉伸性能
图3所示是层间混杂和层内混杂复合材料经向的拉伸应力—应变曲线,起初呈线性关系,之后由于树脂的微小裂痕,线性关系的斜率下降,然后再线性增加,直到材料失效。
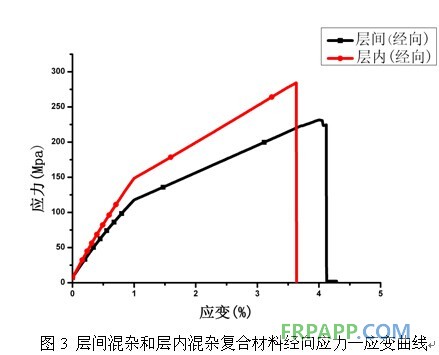
图3 层间混杂和层内混杂复合材料经向应力—应变曲线
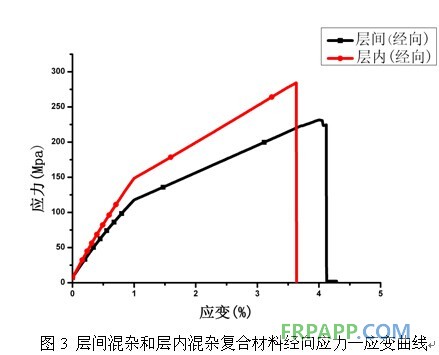
图3 层间混杂和层内混杂复合材料经向应力—应变曲线
表3所示是层间混杂和层内混杂复合材料拉伸性能的对比。其中层间混杂复合材料的经向拉伸强度为222MPa,经向杨氏模量为12.8GPa;层内混杂复合材料的经向拉伸强度为281.4MPa,经向杨氏模量为15.53GPa。可以看出层间混杂复合材料的断裂强度和杨氏模量比层间混杂复合材料高。考虑到这两种复合材料的纤维体积含量,计算出归一化强度和归一化模量,层间混杂复合材料的经向拉伸归一化强度为1718.27MPa,经向归一化模量为99.07GPa;层内混杂复合材料的经向拉伸归一化强度为2098.43MPa,经向归一化模量为115.81GPa,可见层内混杂复合材料的归一化强度比层间混杂复合材料的归一化强度大22.12%,层内混杂复合材料的归一化模量比层间混杂复合材料的归一化模量大16.9%。因为纤维排列方式不同,可以推论出纤维排列方式对混杂复合材料拉伸性能的影响是显著的。在层内混杂复合材料中,玄武岩纱线和芳纶纱线的交替排列层有助于载荷的传导;而在层间混杂复合材料中,因为每层纱线组分不一致,层与层之间容易产生应力集中,因而降低了复合材料的拉伸强度和杨氏模量。
表3 层间混杂和层内混杂复合材料拉伸性能的对比
复合材料
|
拉伸方向
|
拉伸强度(MPa)
|
杨氏模量(GPa)
|
归一化强度(MPa)
|
归一化模量(GPa)
|
层间混杂
|
经向
|
222
|
12.8
|
1718.27
|
99.07
|
层内混杂
|
经向
|
281.4
|
15.53
|
2098.43
|
115.81
|
图4所示的是层间混杂和层内混杂复合材料经向的拉伸破坏模式,两种材料经拉伸破坏后,在断口处,纤维被抽拔出来,纤维和基体发生断裂,纤维与基体的界面脱胶,不同的是,因为层间混杂复合材料的层间容易产生应力集中,被抽拔出的纤维较多,层内混杂复合材料的断面比层间混杂复合材料的整齐。
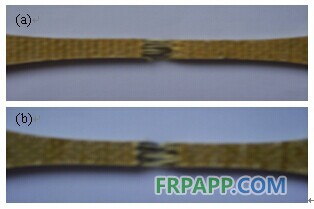
图 4 (a)层间混杂复合材料经向和(b)层内混杂复合材料经向的拉伸破坏
所示的是层间复合材料在经向和纬向的拉伸应力—应变曲线,其变化关系与图3反映的相同。
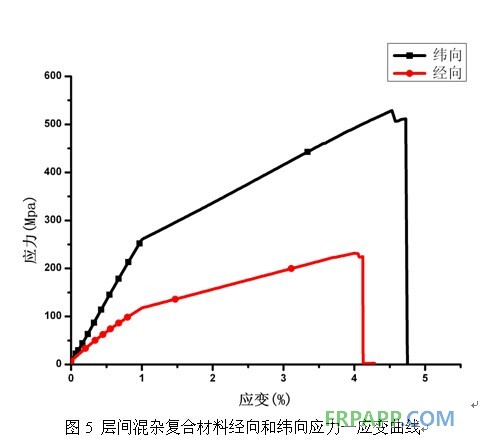
表4所示的是层间混杂复合材料经向拉伸和纬向拉伸性能的对比,层间混杂复合材料的经向拉伸强度为222MPa,经向杨氏模量为12.8GPa;纬向拉伸强度为538MPa,纬向杨氏模量为26.4GPa,可以看出纬向的拉伸强度比经向的高,纬向的杨氏模量比经向的高。考虑到经向和纬向的纤维体积含量,计算出归一化强度和归一化杨氏模量,层间混杂复合材料的经向拉伸归一化强度为1718.27MPa,经向归一化模量为99.07GPa;纬向拉伸归一化强度为1787.97MPa,纬向归一化模量为87.74GPa。纬向的归一化强度比经向的高,但纬向的归一化模量比经向的低,纬向的归一化强度比经向的大4.06%,纬向的归一化模量比经向的小11.44%,因为纬向的纤维体积含量比经向的高,层间混杂复合材料的纬向归一化强度比经向的高;但纬向较高的纤维体积含量增加了纤维间相互滑移,导致纬向的归一化模量降低,而且由于Z纱的存在和织造工艺中经纱预加张力的影响,有利于经向归一化模量的提高。
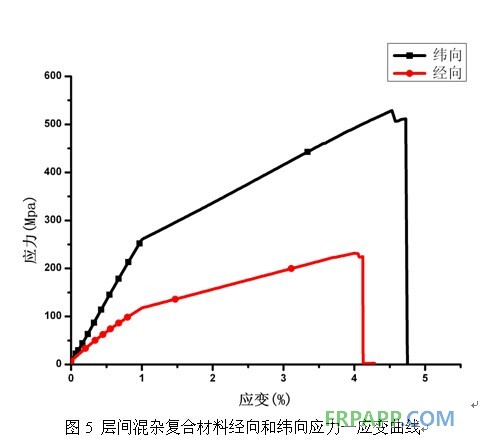
表4所示的是层间混杂复合材料经向拉伸和纬向拉伸性能的对比,层间混杂复合材料的经向拉伸强度为222MPa,经向杨氏模量为12.8GPa;纬向拉伸强度为538MPa,纬向杨氏模量为26.4GPa,可以看出纬向的拉伸强度比经向的高,纬向的杨氏模量比经向的高。考虑到经向和纬向的纤维体积含量,计算出归一化强度和归一化杨氏模量,层间混杂复合材料的经向拉伸归一化强度为1718.27MPa,经向归一化模量为99.07GPa;纬向拉伸归一化强度为1787.97MPa,纬向归一化模量为87.74GPa。纬向的归一化强度比经向的高,但纬向的归一化模量比经向的低,纬向的归一化强度比经向的大4.06%,纬向的归一化模量比经向的小11.44%,因为纬向的纤维体积含量比经向的高,层间混杂复合材料的纬向归一化强度比经向的高;但纬向较高的纤维体积含量增加了纤维间相互滑移,导致纬向的归一化模量降低,而且由于Z纱的存在和织造工艺中经纱预加张力的影响,有利于经向归一化模量的提高。
表4 层间混杂复合材料经向拉伸和纬向拉伸性能的对比
拉伸方向
|
拉伸强度(MPa)
|
杨氏模量(GPa)
|
归一化强度(MPa)
|
归一化模量(GPa)
|
经向
|
222
|
12.8
|
1718.27
|
99.07
|
纬向
|
538
|
26.4
|
1787.97
|
87.74
|
图6所示的是层间混杂复合材料的经向和纬向的拉伸破坏模式,在经向和纬向破坏后,在断口处,纤维被抽拔出来,纤维和基体发生断裂,纤维与基体的界面脱胶,不同的是,因为层间混杂复合材料的纬向纤维体积含量比经向高,纬向较高的纤维体积含量增加了纤维间的相互滑移,纬向被抽拔出的纤维较多
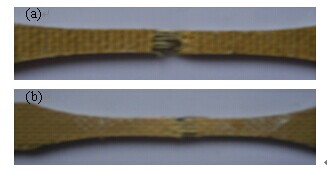
图6 (a)层间混杂复合材料经向和(b)层间混杂复合材料纬向的拉伸破坏
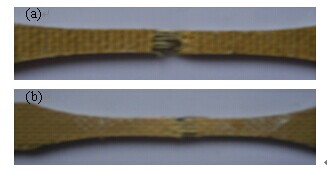
图6 (a)层间混杂复合材料经向和(b)层间混杂复合材料纬向的拉伸破坏
3.2 混杂复合材料的剪切性能
图7所示的是层间混杂和层内混杂复合材料±45°偏轴向拉伸应力—应变曲线,其变化关系与图3反映的相同。
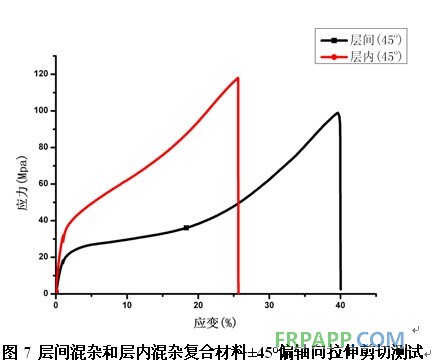
表5所示是层间混杂和层内混杂复合材料的剪切性能对比。层间混杂复合材料的剪切强度为102MPa,剪切模量为3.15GPa;层内混杂复合材料的剪切强度为122MPa,剪切模量为3.97GPa,层内混杂复合材料的剪切强度和剪切模量都比层间混杂复合材料的高,层内混杂复合材料的剪切强度比层间混杂复合材料的大19.61%,层内混杂复合材料的剪切模量比层间混杂复合材料的大26.03%。因为在层内混杂复合材料中,玄武岩纱线和芳纶纱线的交替排列层有助于载荷的传导;而在层间混杂复合材料中,因为每层纱线组分不一致,层与层之间容易产生应力集中,因而降低了复合材料的剪切强度和剪切模量。
表5 层间混杂和层内混杂复合材料的剪切性能
复合材料
|
剪切强度(MPa)
|
剪切模量(GPa)
|
层间混杂
|
102
|
3.15
|
层内混杂
|
122
|
3.97
|
图8所示的是层间混杂和层内混杂复合材料±45°偏轴向拉伸破坏模式。两种材料拉伸破坏后,在断口处,纤维被抽拔出来,纤维和基体发生断裂,纤维与基体的界面脱胶,断口呈45°斜面,不同的是,因为层间混杂复合材料的层间容易产生应力集中,被抽拔出的纤维较多,层内混杂复合材料的断面比层间混杂复合材料的整齐。
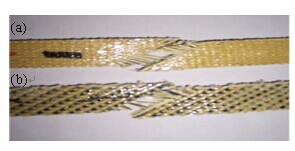
图8 (a)层间混杂和(b)层内混杂复合材料剪切测试破坏
4 结论
层内混杂复合材料的经向归一化强度和经向归一化模量比层间混杂复合材料的高。层间混杂复合材料纬向的归一化强度比经向的高,但纬向的归一化模量比经向的低。层内混杂复合材料的剪切强度和剪切模量比层间混杂复合材料的高。层间混杂和层内混杂复合材料经向的拉伸破坏模式、层间混杂复合材料的经向和纬向的拉伸破坏模式和层间混杂和层内混杂复合材料±45°偏轴向拉伸破坏模式,两种材料经拉伸破坏后,在断口处,纤维被抽拔出来,纤维和基体发生断裂,纤维与基体的界面脱胶,但偏轴拉伸的断口呈45°斜面。而且因为层间混杂复合材料的层间容易产生应力集中,被抽拔出的纤维较多,层内混杂复合材料的断面比层间混杂复合材料的整齐;因为层间混杂复合材料的纬向纤维体积含量比经向高,纬向较高的纤维体积含量增加了纤维间的相互滑移,纬向被抽拔出的纤维较多。