1引言
风力发电技术是当今各种可再生能源利用中技术最成熟、最具规模开发条件及商业化发展前景的一种。为了寻求替代石化燃料的能源和减少二氧化碳及污染气体的排放,包括我国在内的许多国家都在大力发展该项技术。为了提高发电效率,风力发电设备正不断朝着大型化方向发展,其主要机型的额定功率从以前的几百千瓦级发展到现在的1~3MW,甚至更大。风力机功率的加大使得其叶轮的直径不断加大,目前一台1.5MW风力发电机的叶轮直径可达80m左右。与此同时,还需要使其尽可能的轻巧和高效,这就使得风力机叶片的设计变得非常复杂。
我国近年来对风力发电等可再生能源的发展非常重视,风电产业发展迅速,截至2008年12月31日,我国除台湾省外新增风电机组5130多台,新增装机容量约624.6万kW,当年新增装机增长率为89%,累计装机容量约1215.3万kW,建立了一批新的大型风电机组生产线[1]。但在风电产业蓬勃发展背后,却存在着大型风电机组自主设计生产能力不足的问题,国内众多叶片厂商虽然完成了叶片制造的国产化,设计技术却往往掌握在国外设计公司手里,特别是大容量风力机的能力。本文针对2MW风电机组叶片,完成了叶片的外形设计和载荷计算。
2 叶片的气动外形设计
叶片的气动外形设计是指叶片采用的翼形族、剖面弦长、扭角、相对厚度沿叶片长度方向的分布。由于风轮数值计算的网格数量大,网格生成困难、耗时等特点,同时气动设计要根据后续的计算进行优化,将其应用于叶片气动外形设计还有一定距离,现有工程计算及设计的基础仍然是动量叶素理论,它也是目前国际风电行业性能、载荷计算软件的理论基础。
2.1设计参数
设计参数一般由叶片厂商根据风电机组总装厂的要求,同时根据市场上同类叶片运行参数确定部分主要的设计参数。因为叶片设计出来是要面对市场的,如果主要参数差异较大,则面临市场面较窄,从面影响企业的发展。叶片设计参数包括风电机组风轮参数和叶片本身的技术参数,一般包括:
(1)风轮叶片数。由于三叶片的风电机组的运行和输出功率比较平稳,现代MW级风电机组一般为三叶片,二叶片比较罕见。
(2)额定风速。直接影响到风力机的尺寸和成本,在此风速下,风力机组输出额定功率。知道了平均风速和风速的频度,就可以按一定的原则来确定风速的大小,一般由风电机组整机厂商根据风场的勘测数据确定。
(3)风轮直径。由叶片适用的风区,如果是IECI类风区,额定风速较高,风轮直径会较小;相反,如果是IECII类风区或更差,要求额定风速会更低,风轮直径更大。确定了风轮直径,根据轮毂半径及风轮锥角等可得出叶片的长度。
(4)风轮转速。一般应先确定叶片运行的尖速比范围,在设计的尖速比上,所有的空气动力学参数接近于它们的最佳值,以及风轮效率达到最大值。目前运行的大功率风机都具有较高的尖速比,在6~8范围内,此类风机具有较高的风能利用系数,同时较高尖速比的风力机叶片成本也低。根据风轮设计风速和发电机转速确定的尖速比应在此范围内。由于控制气动噪声的原因,叶尖线速度一般在70m/s附近(海上风电机组略有放开),这决定了风轮的最大转速。
(5)风轮仰角和风轮锥角,防止叶尖与塔架碰撞。
(6)翼形族的选择。失速型叶片必须选择失速性能优良的翼型,变速变距叶片一般选择具有良升阻比特性的翼型。为满足结构设计的需要,叶片根部一般选用大厚度翼型,其相对厚度根据强度要求从根端的100%(圆形)过渡到40%左右。翼型的空气动力学特性是叶片气动设计的基础参数,风力机叶片的运行迎角范围是-180°~180°,雷诺数的范围也比较宽,在106~107之间。
2.2动量叶素理论
2.2.1动量理论
动量理论(MomentumTheory)定义了一个通过风轮平面的理想流管,见图1,



分别表示来流风速、流过风轮风速、风轮后尾流速度[3]。

图1动量理论理想流管
应用动量方程和伯努力方程可以推导出轴向力T和风轮转矩Q的表达式:


式中: 轴向诱导因子

切向诱导速度

P为空气密度;
u为风轮平面风的角速度;
Q为风轮的角速度;
R为风轮平面的半径[2]。
2.2.2叶素理论
叶素理论(BladeElementTheory)的基本出发点是将风轮叶片沿展向分成许多微段,称这些微段为叶素。假设在每个叶素上的流动相互之间没有干扰,即将叶素看成二维翼型,这时将作用在每个叶素上的力和力矩沿展向积分,就可以求得作用在风轮上的力和力矩。

图2叶素上的气流速度三角形和空气动力分量
由图上速度三角形可导出:

(1)

(2)
计算法向力系数

和切向力系数

:


(3)
其中Cl、Cd为叶素翼型的升力系数和阻力系数。
长度为

叶素上的空气动力合力

可以分解成法向力

和切向力

:


这时,作用在风轮平面

圆环上的轴向力(推力)和转距可表示为:



(4)
2.2.3动量叶素理论
动量一叶素理论(BEMTheory)结合动量理论和叶素理论,计算出风轮旋转面中的轴向诱导因子a和周向诱导因子b。

(5)

(6)
2.3普朗特修正因子[3]
加入普朗特叶尖和叶根修正因子F,式(5)(6)变成:

(7)

(8)
2.4Glarert修正因子[4]
当风轮叶片部分进入涡环状态时,动量方程不再适用;这时,引用Glarert修正方法。
当a>0.2时,a由下式计算;

(9)
式中,


2.5气动外形设计计算过程
入流因子计算流程如下:①给定a、b的初值,取a=0.3,b=0;②利用式(1)计算入流角;③利用式(2)计算迎角;④根据翼型空气动力特性表得到叶素的升力系数Cl和阻力系数Cd;⑤根据式(3)计算叶轮平面法向力系数Cn和切相力系数Ct;⑥利用式(7)、(8)计算a、b的新值;⑦比较a、b的值与上一次a、b的值,如果误差小于设定误差(0.001),则迭代终止;否则,再回到2步继续迭代;⑧迭代中,若a>0.2时,利用式(9)计算。
进一步可求得风轮平面圆

环上的轴向力dT(推力)和转距dM,对三叶片的叶素分量求和可以计算出风轮的转矩M,主轴功率P和推力T,并计算出风轮风能利用系数Cp和推力系数CT[2]。
2.6优化设计
利用直接优化的方法,基于动量叶素理论建立优化设计的数学模型,是一个单目标多变量的最优化设计数学模型:

式中Cp为风电机组风轮风能利用系数,λdesign为设计叶片尖速比。
设计变量是没展向变化的剖面弦长c、扭角θ和相对厚度tr,约束条件是各变量的上下限值以及叶片厂商提出的约束。
2.7实例设计
下面就我院自行设计的2MW风电机组叶片,验证气动设计的结果。由厂家提出的叶片设计的参数如下:
设计目标为风轮最大风能利用系数达到0.48。
该叶片翼形族采用NACA634系列翼型,并在此基础上提出了修改,增加后缘的厚度,在提升翼型升力的同时,增加叶片的侧向刚度,翼形升力系数和阻力系数由GarradHassen公司进行了校正。
经过几轮优化设计,并与结构计算相协调,确定了叶片的气动外形。

图3 2MW叶片的外形尺寸
完成外形设计后,由Bladed[5]软件进行了气动性能校核计算:
图4不同安装用下的风能利用系数曲线
计算结果表明:最大风能利用系数达到0.482,发生在尖速比8.4附近,满足设计目标。在6.75~10.75的尖速比范围内,风能利用系数都超过0.45。

图5风电机组功率曲线
由图5可以看出,在12m/s的风速时,已达到额定功率2MW,留有较大的风速空间。
3 叶片的载荷分析
由于风力发电机运行在复杂的外界环境下,所承受载荷情况也非常多,根据风力机运行状态随时间的变化,可以将载荷情况划分为静态载荷、动态载荷和随机载荷。动态载荷和随机载荷具有时间上和空间上的多变性和随机性,要想准确计算比较困难。而静态载荷基本上不考虑风力机运行状态的改变,仅考虑环境条件改变的情况,现就风力机的这种静态载荷计算作一简要讨论。

图6叶片载荷计算坐标系
风力机依靠叶轮将风中的动能转化为机械能,叶轮是风力机最主要的承载部件。叶轮主要承受三种力:空气动力、重力和离心力。具体的计算方法参见相关文献[2],这里不再赘述。
载荷计算是后续结构计算和试验的基础,本文在计算时,参照IEC61400-1Ed2《Windturbinegeneratorsystems-Part1:Safetyrequirements》计算,具体的工况设计见下表1。
表1IEC设计载荷工况
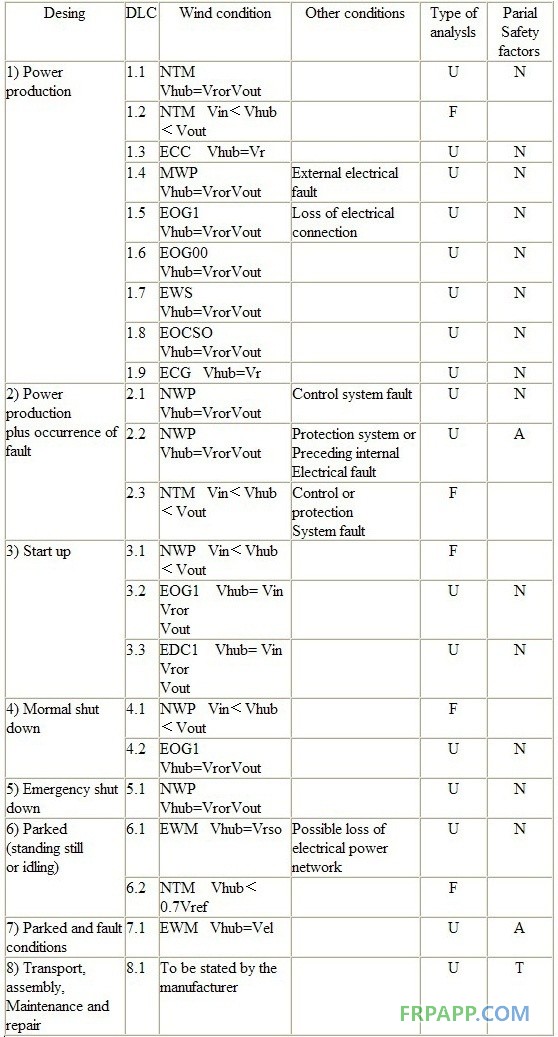
每个分类工况下,按照方位角或入流角或来流风速的不同,又有多种工况。在工况设计完毕,利用Bladed软件进行动态模拟之后,对叶片上的载荷进行统计和分析,得出极限载荷下叶片上的弯矩分布;同时进行按Weibull风速风布,进行20年寿命里的雨流统计,得出其载荷谱,然后按等效损伤原理进行等效疲劳载荷计算,得出叶片的等效疲劳载荷谱,并在此基础上计算叶片的疲劳损伤和进行疲劳试验。
结合本例,2MW叶片没展向的极限载荷弯矩图如下:


8 2MW叶片挥舞方向极限弯矩分布
4 结论
(1)本文以动量-叶素理论为基础,并结合结构计算的要求,进行了大型风力机复合材料叶片的气动外形设计,并用Bladed软件进行了气动性能分析,结果满足设计要求。
(2)按照IEC风电机组安全规范进行叶片的工况设计和载荷计算,得出叶片的极限载荷和疲劳载荷,介绍了载荷计算的方法与结果的分析。
(3)2MW风电机组叶片的设计已通过了中国船级社产品认证部的认证,验证了气动设计和载荷分析的正确性,为我国风电叶片的国产化奠定技术基础。