0 前 言
PMI(聚甲基丙烯酰亚胺)泡沫材料是目前聚合物泡沫芯材发展的最新材料,具有密度小、耐高温性优、介电常数和介电损耗低、耐疲劳性能佳、耐电压强度和比强度高等诸多优点,因而已广泛用于复合材料夹层结构的芯材,在高速列车、船舶和航空航天等领域中得到广泛应用。
受成品PMI泡沫材料的尺寸和形状所限制,在其夹层结构整体成型过程中,对PMI泡沫材料进行拼接和填充补强已不可避免。现有的蜂窝补强用发泡类胶粘剂材料[4]虽可满足低密度、耐高温和高强度要求,但仍无法满足PMI泡沫材料常温拼接定型的工艺要求;现有的低密度糊状胶粘剂材料[5]虽满足PMI泡沫材料常温拼接定型的工艺要求,但无法实现与复合材料预浸料蒙皮共固化的成型工艺,并且其耐热性满足不了设计要求。
本研究采用脂环族胺类/芳香族胺类作为复配固化剂,制备的低密度糊状胶粘剂具有常温可拼接定型、中温和高温均可固化成型的优势,完全满足EP预浸料一PMI泡沫材料夹层结构件的热压罐成型的工艺要求。该胶粘剂在密度、耐热性、力学性能和工艺性能上达到了较好的平衡,并且填补了国内在该领域的研究空白,对进一步拓宽PMI泡沫材料夹层结构件在航空航天等领域的应用范围具有重要的意义。
1. 试验部分
1.1 试验原料
双酚A型环氧树脂(EP),工业级(牌号0164),上海树脂厂;环氧活性稀释剂,工业级(牌号501B),武汉远城科技发展责任有限公司;核/壳型橡胶(牌号CSR一3,粒径300~900 nm),自制;异佛尔酮二胺(IPDA),工业级,德国巴斯夫公司;4,4 一二氨基二苯甲烷(MDA),工业级,湖北洪湖双马树脂厂;4,4 一二氨基二苯砜(DDS),工业级,上海群力化工有限公司;中空玻璃微球,工业级(牌号S38HS),美国3M公司;PMI泡沫材料,工业级(牌号110WF),德国Rohm公司;硅烷偶联剂(KH一560),工业级,市售;EP预浸料,自制。
1.2 试验仪器
Instron4505型电子材料试验机,美国Instron公司;DSC7型差示扫描量热仪,美国PE公司;Q800型电子散斑干涉仪,德国Ettemeyer公司;PTR65型三辊研磨机,德国Puhler公司;BLLON一500型超声波分散仪,上海比朗仪器有限公司。
1.3 试验制备
1.3.1 双组分低密度糊状胶粘剂的制备
(1)A组分(以改性EP为主体,核/壳型聚合物为增韧剂):首先将501B加入到EP中,搅拌均匀;然后加入自制的CSR一3,机械搅拌和超声波分散若干时间,使上述物料混合均匀;随后加入经硅烷类偶联剂(KH一560)表面处理过的玻璃微珠,充分搅拌均匀后得到A组分。
(2)B组分(以复合胺类化合物为主体):将固体芳香胺类固化剂(MDA/DDS混合物)加入到脂环族胺类固化剂(IPDA)中,搅拌均匀;然后用三辊研磨机研磨至均匀,得到B组分。
(3)按照m(A组分):m(B组分)=6:1比例,将两者混合均匀,得到低密度糊状胶粘剂。
1.3.2 PMI泡沫材料夹层结构件的制备
当配胶量为200 g时,低密度糊状胶粘剂的适用期可达到3 h左右,并且其触变性良好;PMI泡沫材料经该胶粘剂拼接或填充后,具有不塌陷、不流淌之优点。
首先采用自制双组分低密度糊状胶粘剂将PMI泡沫材料拼接定型,室温静置8 h;然后将EP预浸料铺贴在拼装后的PMI泡沫材料两侧,采用热压罐工艺成型后,得到PMI泡沫材料夹层结构件。
1.4 测试或表征
(1)剪切强度:按照GB/T 7124-2008标准(常温)和GJB 444-1988标准(中温、高温)进行测定。
(2)初粘力或平面拉伸强度:按照GJB 130.4?1986标准进行测定。
(3)压缩强度:按照GB厂r 1041-2008标准执行。
(4)热性能:采用差示扫描量热(DSC)法进行表征(N 气氛,升温速率5 K/min)。
(5)胶粘剂的韧性:采用电子散斑干涉技术对夹层结构件进行无损检测,若胶层拼缝、补强处无断裂、开缝等现象,说明该胶粘剂韧性良好。
(6)胶粘剂的视密度:按照式(1)计算而得。
D=G/V=G/( L×T×H) (1)
式中:D为胶粘剂的视密度(g/cm3 );G、V分别为固化后胶粘剂试样的质量(g)、体积(cm3 );L、T、H分别为试样的长度、宽度、厚度(mm)。
2. 结果与讨论
2.1 增韧剂对低密度糊状胶粘剂性能的影响
本研究为热固化型PMI泡沫材料拼接用低密度糊状胶粘剂,固化产物从固化温度(最高175℃)降至室温过程中,其在玻璃态区域的收缩率将产生较大的内应力,故胶层易脆裂、拼接界面易出现缺陷;另外,当温度从固化温度降至室温时,体系因各组成(如胶粘剂、PMI泡沫材料和EP预浸料等)膨胀系数不同而易产生界面应力。因此,采用增韧体系改善胶粘剂的韧性,是解决上述问题切实可行的有效方法之一。
本研究以CSR一3(聚甲基丙烯酸酯为壳、有机硅橡胶为核的耐热核/壳型橡胶)作为传统液体橡胶的替代品,对低密度糊状胶粘剂进行增韧改性;有关试验证明,用预先设计好的核/壳型橡胶粒子与被改性树脂共混后,固化前后该橡胶粒子的成分、形态、大小及其在树脂中的分布状态均保持不变(即上述诸多性能与固化过程特别是固化温度无关)[6],这对胶粘剂常温可凝胶、中温和高温均可固化成型显得尤为重要。
在其他条件保持不变的前提下,CSR一3含量对低密度糊状胶粘剂剪切强度和压缩强度的影响如图1所示。
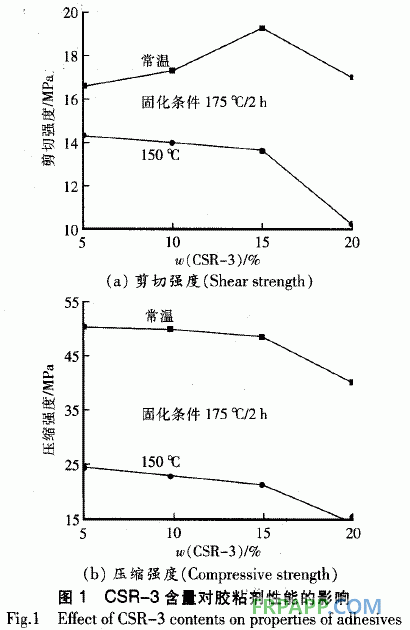
由图1可知:随着CSR一3含量的不断增加,低密度糊状胶粘剂的常温剪切强度呈先升后降态势,高温剪切强度、常温压缩强度和高温压缩强度均呈先缓后快的下降态势;当w(CSR一3)=15%(相对于EP质量而言)时,其常温、高温剪切强度和压缩强度均相对较大。
用户单位将该胶粘剂用于PMI泡沫材料夹层结构件的制备,并采用电子散斑干涉技术对该结构件进行无损检测,以进一步考察固化成型过程中胶粘剂的韧性大小。检测结果表明:该结构件的胶层拼缝处、补强处无断裂、开缝等现象;说明该胶粘剂的高韧性特点得到了工程应用方面的验证。
2.2 固化剂对低密度糊状胶粘剂性能的影响
作为PMI泡沫材料拼接用低密度糊状胶粘剂,要求其在常温条件下能拼接定型,在中温、高温条件下能与EP预浸料共固化成型。为满足上述工艺要求,本研究以常温可凝胶的中低温固化剂/高温固化剂作为复配固化剂。
脂环族胺类固化剂,大多属于低黏度液体,其活性低于脂肪胺类固化剂,适用期较长,固化反应缓和且放热量相对较小(其中脂环族胺类IPDA具有无色、黏度低、挥发性小和固化产物不易泛黄等特点,能够满足常温凝胶、中低温固化的使用要求);芳香族固化剂选择MDA和DDS固化剂。对上述固化剂的复配比例进行调整,当m(IPDA):m(MDA):m(DDS)=10:10:5时,获得了理想的放热曲线,如图2所示。
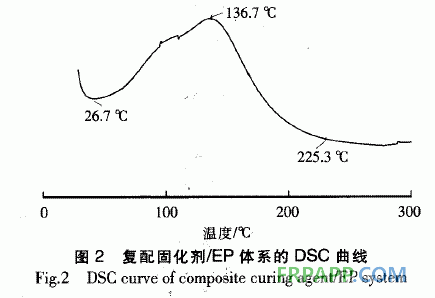
由图2可知:复配固化~I]/EP共混体系只有1个明显的放热峰,说明两者在固化过程中的协调性良好;固化体系的起始反应温度(25℃左右)较低,表明常温可凝胶;固化体系的放热峰顶温度为136.7℃,反应终点温度为225℃左右,表明该复配固化剂可满足与中温、高温EP预浸料共固化的成型条件。
采用上述复配固化剂/EP预浸料固化体系制备低密度糊状胶粘剂,并将该胶粘剂用于PMI泡沫材料的拼接,则室温放置时间对PMI泡沫拼接材料初粘力的影响如图3所示。
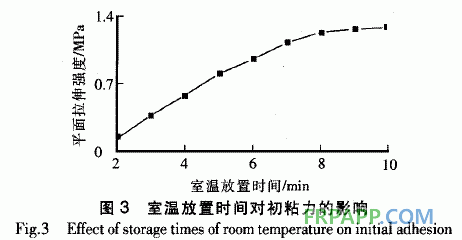
由图3可知:该胶粘剂的室温(25 oC)放置时间越长,PMI泡沫拼接材料的初粘力(平面拉伸强度)越大;当室温放置时间≥8 h时,初粘力增幅趋缓。综合考虑,选择室温放置时间为8 h时较适宜。
2.3 玻璃微珠含量对低密度糊状胶粘剂性能的影响
在低密度糊状胶粘剂中,普遍选择中空玻璃微珠作为无机轻质填料。中空玻璃微珠具有密度低、压缩强度高、熔点高、电阻率大、导热系数和热收缩系数小等诸多优点,采用l%左右的偶联剂溶液(乙醇/水体积比为9:1)对其表面进行处理,可有效提高其与胶粘剂基体树脂的界面结合力。
在其他条件保持不变的前提下,玻璃微珠含量对低密度糊状胶粘剂性能的影响如表1所示。由表1可知:玻璃微珠含量越多,低密度糊状胶粘剂的视密度、剪切强度(常温、高温)和压缩强度(常温、高温)均呈下降态势。
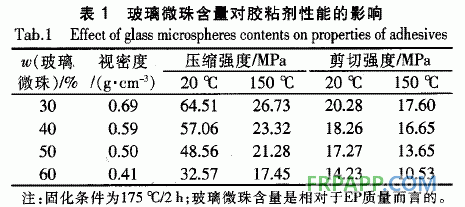
本研究还考察了玻璃微珠含量对该胶粘剂施工性能的影响。当 (玻璃微珠)=30%或40%时,胶液流淌性较大、施工困难;当W(玻璃微珠)=60%时,胶粘剂自黏性较差,并且其力学性能降幅较大;当W(玻璃微珠)=50%时,胶粘剂既具有较高的力学性能,又具有良好的施工性能(胶液触变性好、不流淌、不塌陷),并且满足PMI泡沫拼接材料的工艺要求和使用要求。
2.4 固化工艺条件对低密度糊状胶粘剂性能的影响
本研究研制的低密度糊状胶粘剂具有与中温或高温EP预浸料共固化的特性,其不同固化条件时的力学性能如表2所示。
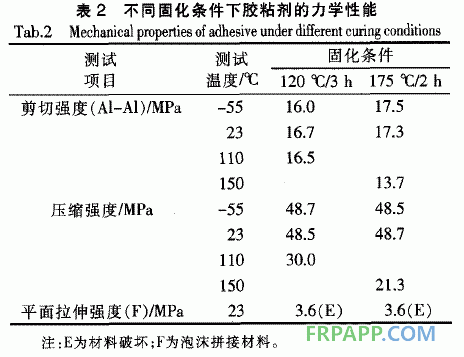
由表2可知:低密度糊状胶粘剂在中温(120℃/3 h)或高温(175℃/2 h)固化条件下均具有良好的剪切强度和压缩强度,其平面拉伸破坏均为本体PMI泡沫材料破坏,说明该胶粘剂满足PMI泡沫拼接材料的使用要求。
3 .结语
(1)本研究以低黏度EP为基体树脂、核/壳型橡胶为增韧剂、高强度玻璃微珠为填充料和混合胺为固化剂,制备了PMI泡沫材料夹层结构件的拼接和补强用低密度双组分糊状胶粘剂。
(2)采用单因素试验法优选出制备低密度双组分糊状胶粘剂的最优方案为主剂中m(EP):m(增韧剂):m(玻璃微珠)=100:15:50、复配固化剂中m(IPDA):m(MDA):m(DDS)=10:10:5。
(3)由最优方案制成的低密度双组分糊状胶粘剂,具有常温可凝胶拼接定型、中温(120℃)和高温(175 ℃)均可固化成型的工艺特性,完全满足EP预浸料一PMI泡沫材料夹层结构件的热压罐成型工艺要求。