1 绪论
1.1复合材料的应用与研究
复合材料,是由两种或两种以上不同性质的材料,通过物理或化学的方法,在宏观上组成具有新性能的材料。各种材料在性能上互相取长补短,产生协同效应,使复合材料的综合性能优于原组成材料而满足各种不同的要求。复合材料具有质量轻、比强度、比模量高,较好的延展性、抗腐蚀、隔热、隔音、耐高温、性能可设计性等特点,因此被大量用于航空航天等军事领域和民用领域,是制造飞机、火箭、航天飞行器等的理想材料。
在航空工业中,复合材料的应用越来越广泛,而且成为衡量飞机性能的重要参数。复合材料成型技术在应用过程中不断积累应用经验,提高技术水平, 完善配套技术, 从非承力构件整流蒙皮逐渐发展到承力构件尾翼、机翼, 从简单结构层合壁板, 逐渐发展到整体复合材料结构尾翼和机翼。先进树脂基复合材料在飞机上的应用可以实现15% ~30%减重, 可有效降低飞机的结构重量, 提高飞机的机动性能和有效载荷等。飞机结构复合材料化已经成为趋势, 先进树脂基复合材料已经成为不可缺少的关键航空结构材料。从上世纪90 年代开始, 先进战斗机大量使用先进树脂基复合材料, 如F - 22飞机复合材料的用量达到约25% , F - 35 复合材料用量达到35% ,主要应用包括机翼、机身、尾翼等主要承力构件。先进树脂基复合材料在民用飞机的应用从2003 年用量得到了跨越发展, 空客公司的A380宽体客机复合材料的用量增加到24% , 波音公司的B787飞机复合材料用量达到约50% , 空客公司在研究的A350XWB复合材料用量将达到52%。随着国内先进树脂基复合材料性能的提高, 制造技术的不断成熟, 配套无损检测和装配等技术的完善, 国内先进树脂基复合材料在直升机、歼击机和大型飞机得到相当的应用。歼击机复合材料的用量已经达到6% ~9% , 主要包括机翼、平尾、垂尾、前机身、鸭翼、襟副翼、腹鳍等; 直升机复合材料用量达到25% ~33% ,主要包括旋翼系统和机身结构。先进树脂基复合材料机翼、平尾、垂尾、鸭翼、直升机机身、尾段等复合材料构件已经实现批量生产。

1.2树脂基复合材料的应用现状
复合材料按其基体材料的不同可分为聚合物复合材料、金属基复合材料和无机非金属基复合材料,我们通常所说的树脂基复合材料属于聚合物复合材料,现阶段复合材料的应用以它最广,占所有复合材料总量的90%以上。所以本文主要讲述了树脂基复合材料的成型工艺。
先进复合材料主要指热固性树脂或热塑性树脂为基体、高性能连续纤维为增强体的一类材料,对于飞机承力结构而言,尤其以碳纤维/环氧树脂基复合材料和碳纤维/双马树脂基复合材料用量最大。先进复合材料是通过一定的工艺方法由树脂和纤维复合而成的,与传统的金属材料不同,树脂基复合材料工艺过程具有材料形成和构件成型同时完成的特点,即复合材料形成时其结构尺寸与构件基本一致,只需少量的后加工便可使用。这个特点一方面使得一些对于传统材料难以加工的构件成为了可能,另一方面也决定了工艺过程对于复合材料性能和成本的重要性。目前,随着复合材料工业的迅速发展,树脂基复合材料正凭借其本身固有的轻质高强、成型方便、不易腐蚀、质感美观等优点,越来越受到人们的青睐。
1.3树脂基复合材料成型工艺
树脂复合材料的成型方法主要包括两部分:热塑性树脂复合材料成型和热固性树脂复合材料成型。热塑性树脂基复合材料的成型方法包括树脂传递模塑成型法、模压成型法、注射成型法、拉挤成型法、弹性体储存成型法和纤维缠绕成型法等:热固性树脂基复合材料成型方法主要包括层压成型法、模压成型法、手糊成型法、拉挤成型法和缠绕成型法等。
1.4 本文研究方向
本文着重介绍了树脂基复合材料缠绕成型工艺及其应用,主要包括缠绕成型的原材料、工艺流程、影响制品的因素、制品容易产生的缺陷和解决办法。
2. 树脂基复合材料缠绕成型工艺
2.1树脂基复合材料缠绕成型工艺定义
缠绕成型工艺是一种连续化制备复合材料的方法,将浸过树脂胶液的连续纤维(或布带、预浸纱)按照一定规律缠绕到芯模上,然后经固化、脱模,获得制品。
2.2缠绕成型工艺方法分类
根据纤维缠绕成型时树脂基体的物理化学状态不同,分为干法缠绕、湿法缠绕和半干法缠绕三种。
(1)干法缠绕 干法缠绕是采用经过预浸胶处理的预浸纱或带,在缠绕机上经加热软化至粘流态后缠绕到芯模上。由于预浸纱(或带)是专业生产,能严格控制树脂含量(精确到2%以内)和预浸纱质量。因此,干法缠绕能够准确地控制产品质量。干法缠绕工艺的最大特点是生产效率高,缠绕速度可达100~200m/min,缠绕机清洁,劳动卫生条件好,产品质量高。其缺点是缠绕设备贵,需要增加预浸纱制造设备,故投资较大此外,干法缠绕制品的层间剪切强度较低。
(2)湿法缠绕 湿法缠绕是将纤维集束(纱式带)浸胶后,在张力控制下直接缠绕到芯模上。湿法缠绕的优点为:①成本比干法缠绕低40%;②产品气密性好,因为缠绕张力使多余的树脂胶液将气泡挤出,并填满空隙;③纤维排列平行度好;④湿法缠绕时,纤维上的树脂胶液,可减少纤维磨损;⑤生产效率高(达200m/min)。湿法缠绕的缺点为:①树脂浪费大,操作环境差;②含胶量及成品质量不易控制;③可供湿法缠绕的树脂品种较少。
(3)半干法缠绕 半干法缠绕是纤维浸胶后,到缠绕至芯模的途中,增加一套烘干设备,将浸胶纱中的溶剂除去,与干法相比,省却了预浸胶工序和设备;与湿法相比,可使制品中的气泡含量降低。
三种缠绕方法中,以湿法缠绕应用最为普遍;干法缠绕仅用于高性能、高精度的尖端技术领域。
2.3缠绕成型工艺特点
纤维缠绕成型的优点 ①能够按产品的受力状况设计缠绕规律,使能充分发挥纤维的强度;②比强度高:一般来讲,纤维缠绕压力容器与同体积、同压力的钢质容器相比,重量可减轻40~60%;③可靠性高:纤维缠绕制品易实现机械化和自动化生产,工艺条件确定后,缠出来的产品质量稳定,精确;④生产效率高:采用机械化或自动化生产,需要操作工人少,缠绕速度快(240m/min),故劳动生产率高;⑤成本低:在同一产品上,可合理配选若干种材料(包括树脂、纤维和内衬),使其再复合,达到最佳的技术经济效果。
缠绕成型的缺点 ①缠绕成型适应性小,不能缠任意结构形式的制品,特别是表面有凹的制品,因为缠绕时,纤维不能紧贴芯模表面而架空;②缠绕成型需要有缠绕机,芯模,固化加热炉,脱模机及熟练的技术工人,需要的投资大,技术要求高,因此,只有大批量生产时才能降低成本,才能获得较的的技术经济效益。
2.4缠绕成型工艺的原材料
复合材料缠绕工艺所用的原材料主要有增强材料和基体树脂材料两大类。
(1)增强材料 缠绕成型工艺对增强材料的要求是:有较高的强度和模量;对粘结剂有较好的浸润性;成型过程中不起毛、不断头。常用的增强材料有:玻璃纤维、碳纤维、芳纶纤维、超高相对分子质量聚乙烯纤维等。可根据制品的性能要求选择。
(2)基体树脂 对基体树脂的要求是:能满足制品的性能要求(如力学性能、耐热性能、耐老化性能、介电性能等);对增强材料有良好的浸润和粘接性,有较低的固化温度。常用的树脂有:不饱和聚酯树脂、环氧树脂、酚醛树脂和聚酰亚胺树脂等。
在干法缠绕成型工艺中采用浸渍无纬带作为原材料。
2.5缠绕成型工艺流程
缠绕成型工艺流程图如下图所示
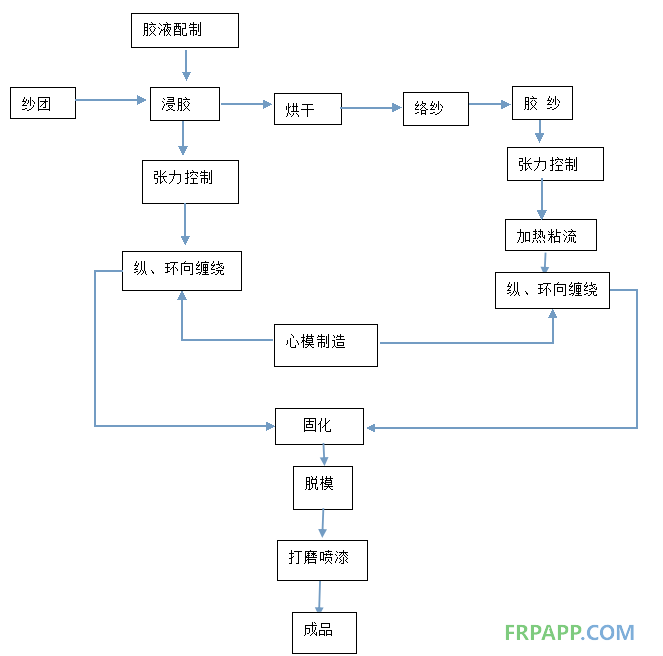
其工艺过程有如下工序组成:胶液配制、纤维烘干及热处理、芯模或内衬制造、浸胶、缠绕、固化、检验、修正、成品。选择合理的缠绕工艺参数,是充分发挥原材料特性、制造高质量缠绕玻璃钢制品的重要条件。影响缠绕玻璃钢制品性能的主要工艺参数包括玻璃纤维的烘干和热处理、玻璃纤维浸胶、缠绕速度和环境温度等。这些因素彼此之间存在有机联系,因此将他们结合在一起研究。
(1)纤维的烘干和热处理
玻璃纤维表面含有水分,不仅影响树脂基材和玻璃纤维之间的粘结性能,同时将引起应力腐蚀,并使微裂纹等缺陷进一步扩展,从而使制品强度和耐老化行下降。因此,玻璃纤维在使用前最好经过烘干处理。
当用石蜡型浸润剂的纤维缠绕时,使用前应先除蜡,以便提高纤维和树脂基材之间的粘结性能。
(2)玻璃纤维浸胶含量的分布
在玻璃纤维的生产和应用过程中,浸润剂起着不可替代的关键作用。浸润剂含量是玻璃纤维成品纱中一项重要的理化指标,它不仅直接影响成品纱的外观质量,而且更会影响成品纱的性能质量。浸润剂含量过低,就会出现严重的毛丝、散丝等现象,并显著降低纤维的抗拉强度;浸润剂含量过高,虽然在一定程度上会提高纤维的抗拉强度,但一般会降低纤维在树脂中的浸透速率,影响纤维与基体的界面结合程度。此外,浸润剂还是玻璃纤维工业中成本价格比例较高的主要原料之一,成品纱的浸润剂含量越高,其生产成本越大,因而会降低经济效益。由此看来,玻璃纤维的生产要想同时达到既降低生产成本而又提高产品质量,就必须加强对浸润剂含量的控制。在现行玻璃纤维行业标准中,对成品纱的浸润剂含量指标要求为0.5%-2%,这只是在玻璃纤维没有品种分类、浸润剂技术指标参差不齐情况下概括性的大范围全容标准。随着玻璃纤维分类的细化、浸润剂技术的发展,各厂家在实际生产中都对某一种类玻璃纤维或某一浸润剂配方都有一个相对较小的控制范围,以利于生产的稳定和产品质量的稳定。一般缠绕型、拉挤型等纱的浸润剂含量大致在0.5%-0.9%范围内,而纺织型纱大多在1%以上。
纤维胶含量是在纤维浸胶过程中进行控制的。浸胶过程可分为两个阶段,首先是树脂胶液涂敷在增强纤维表面,之后胶液向增强纤维内部扩散和渗透。这两个阶段常常是同时进行的,缠绕工艺的浸胶通常采用浸渍法和胶辊接触法,如下如所示:


图(a) 图(b)
(4)缠绕张力
缠绕张力是缠绕工艺的重要参数。张力大小、各束纤维之间张力的均匀性以及个缠绕层之间纤维张力的均匀性,对制品力学性能、密实度和含胶量有较大影响。
(5)固化制度和环境温度
玻璃钢固化有常温固化和加热固化两种,这由树脂体系决定。固化制度是保证制品充分固化的重要条件。直接影响玻璃钢制品的物理性能和其他性能。对不同性能要求的玻璃钢制品,即使采用相同的树脂系统,固化制度也不完全一样,不同树脂系统的固化制度不一样。对各种树脂配方没有一个广泛适用的固化制度,只能根据不同树脂的配方、制品的性能要求,并考虑制品的形状、尺寸、及构造情况,通过实验确定出合理的固化制度,才能提高制品的质量。
树脂系统的粘度随着温度的降低而增加。为了保证胶纱在制件上进一步浸渍,要求缠绕制品的周围温度高于15度。用红外线加热制品表面,其温度在40度左右,这样可以有效提高产品质量。
3.缠绕成型工艺中常见缺陷及解决办法
3.1 国产先进复合材料无法完全满足缠绕成型制造的需求
我国先进复合材料存在的问题为:生产规模小、质量差、价格高、应用基础研究薄弱等。深层次上表现为原材料供应的“瓶颈”效应,即国产复合材料的性能、质量、规格、价格以及供货能力等方面达不到高性能铺放成型制品的要求,
无法满足国防、航空航天及民用领域对复合材料的迫切需要。国外预测我国将成为最大的复合材料制造商和用户,需求量将占世界的1/4。基于复合材料的基础性、先导性、战略性特点,从源头解决好复合材料的供应问题,才能使我国缠绕、成型制造技术的快速发展成为可能。
3.2低成本复合材料缠绕成型制造技术
复合材料缠绕成型普遍存在制造成本问题。在缠绕成型过程中,所用设备专一,制造工艺复杂。要使复合材料缠绕成型制造真正进入到产业化阶段,还需作更深一步的研究,发展制造过程优化及工艺控制技术,降低制造成本,拓展缠绕成型制造技术应用领域。
3.3复合材料缠绕成型制造技术的相关理论与方法
通过对复合材料缠绕成型制造技术数十年的研究和成功应用,人们对其有了更深刻的认识。近年来,欧美等发达国家缠绕、铺放成型制造技术在航空、航天及民用领域的大量应用,这其中的原因是多方面的,科学合理的理论与方法是其中的重要因素之一。鉴于此,我国需要建立并不断完善缠绕成型制造技术的相关理论与方法。
通过对复合材料缠绕成型制造技术数十年的研究和成功应用,人们对其有了更深刻的认识。近年来,欧美等发达国家缠绕、铺放成型制造技术在航空、航天及民用领域的大量应用,这其中的原因是多方面的,科学合理的理论与方法是其中的重要因素之一。鉴于此,我国需要建立并不断完善缠绕成型制造技术的相关理论与方法。
3.4复合材料缠绕成型制品的规范与标准。
将复合材料缠绕、铺放成型制品规范化、标准化,使试验和分析更好地结合起来,形成生产和评价的统一指标,可促进全行业的技术发展,显著改进制品的一致性。建立复合材料缠绕、铺放成型制品有效性能实验表征与评价体系,定量化评价成型制品的可靠性和安全性,对于减少风险,降低成本有着不可忽视的作用。
3.5 工艺过程的检验与管理
CAD/CAM与缠绕、铺放成型工艺的结合,有助于缩短产品设计周期、减少废品率、提高制品的质量,提高自动化水平及生产柔性。国内外均有一些实用化的软件问世,但与传统CAD/CAM技术相比,复合材料成型CAD/CAM技术的研究才刚刚起步,研究成果有限。