0·前言
酚醛树脂(PF)因具有价格低廉、耐热、耐烧蚀、阻燃、发烟少及工艺性良好等优点而被广泛应用,至今仍用作树脂基耐烧蚀材料的主要基体树脂。PF作为聚合物基复合材料的基体树脂,制造耐高温防热烧蚀材料,在航空航天等国防尖端技术领域获得广泛应用。
PF分为热塑性和热固性两种,传统的PF由于中等的热氧稳定性、内在的脆性、吸水率高以及缩聚固化后会产生小分子挥发物等缺点而阻碍其发展,因此寻求一种化学方法对其进行改性势在必行。可以采用的改性方法有:①在热塑性PF的主链上引入热稳定性好的加成固化基团;②对酚羟基进行结构改性;③采用合适的固化剂使热塑性PF通过羟基的加成反应来固化;④加入功能型反应物,通过反应共混对PF进行结构改性[1]。在上述方法中,加成固化是一种最常用的改性方法。对热塑性PF而言,加成固化就是在一定条件下在PF分子中引入不饱和的官能团,通过不饱和基团之间的加成反应使分子之间发生交联,改进其加工性差的缺点。热固性的PF由于具有甲醇基和酚羟基,使其耐水性很差。另外加成固化和PF的热固化使得热固性PF存在二元固化,更加提高了其热氧稳定性和机械性能。目前国内外研究的主要是热塑性PF的加成固化,热固性PF相对来说研究较少。本文主要介绍几种最常见的加成固化型PF。
1·加成固化型PF
加成固化型PF的合成方法之一是在热塑性PF的主链上引入热稳定性良好的不饱和基团。
1.1烯丙基化PF
烯丙基化线性PF是线型PF和烯丙基氯在适当条件下合成的,合成产物可以通过烯丙基基团自身的热聚合完成,反应速率和交联密度取决于反应中心在聚合物分子中的含量。该树脂可以用来制造玻纤增强塑料、模塑料、浇铸体以及具有优异耐热性、力学强度和耐化学介质的浸渍复合材料等。但是,要使烯丙基基团完全固化非常困难,而且由烯丙基自聚形成的交联结构为脂肪链,因此其耐热性仍不十分理想[2]。Knop[3]等研究表明:烯丙基一般需要在250℃加热6 h进行后固化,以提高其固化度,如此就有可能使交联网络中一些脆弱基团发生热分解,使得耐烧蚀性能不理想,热性能变差。因此,如何降低固化温度,提高固化度是今后研究的一个关键。
许多国内外学者近年来致力于这一方面的研究,在降低固化温度的情况下,可以通过与双马来酰亚胺(BMI)化合物的反应共混来降低烯丙基化热塑性PF的固化温度,提高固化度。烯丙基化的PF与BMI化合物之间的反应可以用来合成一系列的聚合物体系,在这样的反应共混物中,通过对BMI或酚环进行结构改性,都可能进一步提高树脂的性能。Zheng[4]等合成了烯丙基化PF与BMI的共聚物,并研究了反应机理和热力学性能。研究发现:线性PF的相对分子质量和烯丙基化程度都会影响树脂的性能,当PF相对分子质量为450,烯丙基化程度为50%时,树脂具有最好的耐热性和弯曲强度。罗振华[2]等合成了烯丙基化程度可达173%的烯丙基PF,并将该树脂与BMI反应共混制得BMI改性的烯丙基PF体系(BMAN)。树脂固化物的起始热分解温度约为430℃,明显高于普通PF的对应值(约300℃)。另外发现BMAN树脂固化物800℃下残炭率不到40%(质量分数),而普通PF在该温度下的残炭率约为50%~60%(质量分数)。与普通PF相比,BMAN树脂固化物中存在相当比例的由烯丙基基团自聚所形成的交联网络,因此芳环结构比例相对降低。尽管烯丙基自聚提高了树脂的交联密度,赋予其更好的耐热性,但是由烯丙基自聚形成的交联结构由脂肪链构成,因此当温度升高到一定程度时,这些结构会迅速分解,从而导致了固化树脂高温残炭率相对较低。
郑知敏[5]等用聚硅氧硅氮烷改性的烯丙基PF的热分解温度和高温残炭率都有较大提高,在900℃氮气条件下,与纯烯丙基PF相比,聚硅氧硅氮烷改性烯丙基PF残炭率提高了41.4%(质量分数)。目前国内外研究较多是BMI改性烯丙基化热塑性PF,以提高其固化度进而提高耐热性,但是效果不是很理想,而对于热固性树脂酚羟基的保护和树脂的加成固化无人研究,这是国内外PF研究的空白。
1.2炔丙基化PF(PN)
近年来,利用PF与含有炔基官能团的化合物反应合成一系列高性能树脂,并且在该树脂中掺杂聚合物形成共混物使得性能进一步提高,此类改性工作主要是针对PF中的酚羟基进行的。酚环上羟基对位和邻位的碳原子容易受到亲电试剂的进攻,这为PF改性提供了一条新的途径,也为寻找浸胶工艺性好、固化温度低、固化过程易于控制、残碳率高、耐热性好且适合大规模生产的加成型树脂提供了新的线索[6]。
1.2.1含有炔丙基醚基团的PF
含有炔丙基醚官能团的PF虽然在商业上很少使用,但是该树脂已发展成为先进复合材料、电气、胶粘剂及涂层等方面EP(环氧树脂)的疏水替代物。大多数的热固性树脂(如EP、BMI等),吸水率高达5%,导致树脂具有较低的湿热物理化学性能,亲水性也很容易导致基体的分层。但是很多复合材料的湿热性能要求的温度超过230℃,显然,高的吸水率限制了这种聚合物在电气方面的应用。炔丙基醚和EP结构的相似性有利于制备、加工和研制热稳定性更好的聚合物。炔丙基醚PF可以由PF前驱体和炔丙基卤化物发生William(威廉森)加成反应而制得[7]。王明存[8]等合成了PN。研究发现:该类树脂具有良好的工艺性,100℃时黏度不超过400 mPa·s;树脂可以在200~250℃进行热固化,热固化物耐热性比传统PF有明显改进,玻璃化温度(Tg)高达370℃的;高温力学性能好,力学损耗峰约为370℃,初始热分解温度在400℃以上;树脂热固化物的碳化产物是典型的玻璃碳。该类新型含炔基PF有望在热结构材料、防热烧蚀材料和高性能树脂共混组分方面具有很好的应用前景。
王明存[9]等在后续的研究中合成了PN和聚芳基乙炔树脂(PAA)的反应共混物,同时还研究了共混树脂的性能。研究发现:PN与PAA形成均相体系;树脂固化工艺性能优良,适合多种成型工艺;树脂的耐热性能优异,900℃、m(PN)∶m(PAA)=1∶1时,共混树脂残碳率为66%(质量分数)。其可作为新型的防热复合材料和高温结构材料的基体。
1.2.2乙炔基封端的PF
端基为乙炔基的加成固化型PF是以碱为催化剂,通过间乙炔基苯基重氮硫酸盐和PF间的偶合反应制备的(见图1)。
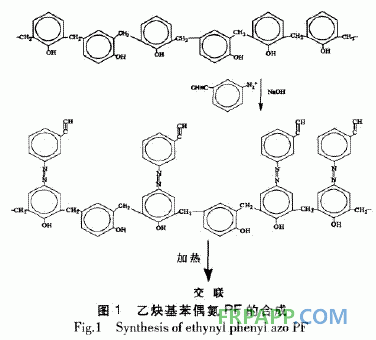
这种聚合物和热固性PF相比,具有更好的热稳定性和耐无氧烧蚀性,且热稳定性和无氧烧蚀残留率随交联密度的增大而增加。在700℃,热固性酚醛的残炭率为60%~62%(质量分数),乙炔基封端的PF的烧蚀残炭率为72%~75%(质量分数)。
李学梅[6]等研制的间乙炔基苯偶氮PF(EPAN),其工艺性好、固化反应活性高。用该树脂制备的硅基/炔基PF复合材料,高温力学性能保持率好,残炭率高(800℃时残炭率约为79.5%)。
1.2.3含有苯乙炔基团的PF
在PF中引入苯乙炔基团,将使交联结构中芳环含量增加,因而可以进一步提高树脂体系的耐热性。改性树脂体系通过加热固化,其固化产物是一种三维网络结构,这种结构使固化后的树脂具有高的Tg,良好的热稳定性、耐水性和耐溶剂性,较好的韧性及较高的力学性能[10]。改性树脂体系在250~275℃加热固化,固化时间为1 h,比传统的含有苯乙炔基官能团的聚合物的固化时间短得多。这是由于树脂固化机理的不同引起的。一般认为,树脂的固化机理(见图2)是乙炔的加成聚合及苯酚与碳碳三键的加成反应[11-12]。
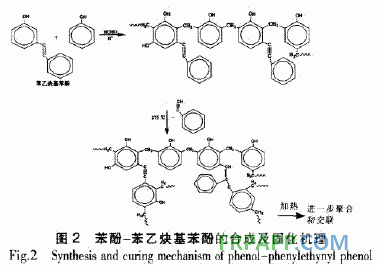
罗振华[13-14]等制备了间乙炔基苯基马来酰亚胺(APMI)改性的PN,合成了APMI单体,并对其热固化行为及固化物的耐热性进行了考察。结果表明:该单体表现出优良的固化反应活性和优异的耐热性,其固化峰值温度约为198℃,Tg约为508℃,800℃下的残炭率约为59%,表明该单体有望成为一种理想的耐高温复合材料基体;以APMI和PN合成的共聚树脂(APMI-PN),其固化反应温度明显比PN低,并且随APMI含量的增加,耐热性和热稳定性呈规律性升高,复合材料室温力学性能明显提高,尤其是弯曲强度(提高65%)。
1.3 PF-EP体系
PF-EP是一种研究成熟的加成固化型树脂,通常是利用EP上的羟基反应,使其和热塑性PF一起固化,这是制备加成固化型PF最简单的方法。常使用多元酚作为EP的固化剂,固化产物具有较好韧性的致密网状结构。这种PF-EP与双酚A型EP配合使用可以用作覆铜板生产。
潘国元[15]等以对羟基苯甲醛与双酚A反应合成多官能度酚醛EP,因侧链刚性基团的引入及官能度的增加,有利于固化完全,提高固化物交联密度。其固化物的Tg、力学性能及耐热降解性能大大提高,Tg为285℃(提高了50℃),树脂质量损失5%时的温度为515.6℃,在800℃条件下的质量损失率为59.1%
Liu[16]等用新型的含磷芳烷基PF与线性PF混合作为固化剂,固化形成的PF-EP具有良好的热力学性能。树脂Tg可达159~177°C,耐热性好(320°C),还能延缓热降解速率,具有较高的残炭率和极限氧指数(26~32.5)。此外,用三聚氰胺改性的线性PF取代纯线性PF固化PF-EP,树脂具有更高的Tg(160~186°C),极限氧指数可达28~33.5。Campaner[17]等利用两种腰果酚PF作为EP固化剂,合成了m(酚醛)∶m(环氧)<60∶40的PF,并对其进行了改性。结果表明:该树脂的机械性能和耐热性能均有提高(在低于400°C时性能没有明显改变,并且只有一个热降解过程)。
此外,Tsai[18]等研制了一种PF固化EP纳米复合材料,具有优异的热性能、力学性能和防护性能,可广泛用于电路板等方面。
另一种情况是用热固性PF和双酚A型EP混合物,制成的复合材料可以兼具两种树脂的优点,改善它们各自的缺点,从而达到改性的目的。这种混合物具有EP优良的粘接性,改进了PF的脆性;同时具有PF优良的耐热性,改进了EP耐热性较差的缺点。这种改性是通过PF中的羟甲基与EP中的羟基及环氧基进行化学反应,以及PF中的酚羟基与EP中的环氧基进行化学反应,最后交联成复杂的体型结构来达到目的,是应用最广的酚醛增韧方法。EP-PF的固化一般是在磷酸三苯酯的催化下进行的。Morgan[19]等研究了如图3所示的一种改性体系。图3中A由n(壬基酚)∶n(二聚环戊二烯)=2∶1组成。该EP-PF体系的断裂韧性显著提高(KIC为1.32 MPa·m1/2),并且具有更高的Tg和更低的吸水率;当EP主链中含有部分4,4′-二亚苯基结构,并用热塑性PF进行固化时,树脂体系具有更高的分解温度[20]。在提高上述性能的同时,树脂的力学性能并没有显著降低。
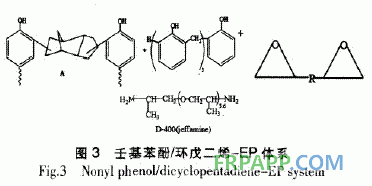
1.4含有苯基马来酰亚胺基团的PF
在PF中引入耐热性优良的BMI,因两者之间发生氢离子移位加成反应,所以对部分酚羟基具有隔离或封锁作用,使改性树脂的热分解温度显著提高,对于改善摩阻材料的耐高温性能有很大作用。由于烯基的引入损失了PF的耐热性能。马来酰亚胺可作为耐热性较佳的加成型基团,如引入BMI基团的PF改性体系,具有较佳的耐热性能,但该类树脂的溶解和加工性能较差。而采用羟基苯基马来酰亚胺作为耐热加成基团的改性树脂,其溶解、加工性能良好,但酚羟基容易氧化,且强极性、易吸水,对材料的电性能和机械强度产生不利的影响[21-22]。周大鹏[23]等合成了N-苯基马来酰亚胺(PMI)改性PF。试验选用PMI作为耐热、加成型组分引入到PF的分子中,利用滴加苯酚的方式,提高了PMI的反应活性;合成产物固化后的耐热性能明显好于传统热塑性PF,分解温度提高了61℃,最终的成碳率也提高了32%。含有马来酰亚胺基团的热塑性PF,是一种通过马来酰亚胺基团的加成聚合而固化的新型PF。苯酚、N-(4-羟基苯酚)聚酰亚胺和甲醛的混合物在酸催化下的反应如图4所示[24]。
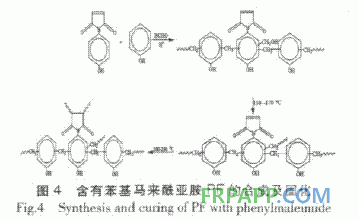
此外,杨洋[25]等利用高邻位PF与邻苯二甲腈偶氮盐之间的偶合反应,制备了带有邻苯二甲腈基团的新型高邻位PF,结构中的腈基在加热条件下可以进行加成固化反应,通过相同方法制备了取代基团含量不同的PF并进行了研究。结果表明:最高取代度为89%,随着取代度的增加,树脂的相对分子质量呈现递减趋势;固化过程中偶氮键在160~230℃附近分解,腈基的加成固化出现在260~340℃。与传统的PF相比,固化后的树脂具有更好的热稳定性和更高的残碳率。
酚醛氰酸酯树脂也是一种加成固化型PF,其以线型PF为骨架,酚羟基被氰酸酯官能团所替代而形成的PF衍生物,在热和催化剂作用下发生三环化反应,生成含有三嗪环的高交联密度网络结构大分子。该树脂是制备高速数字及高频用印刷电路板及大功率电机绝缘配件的极佳材料,也是制造高性能透波结构材料和航空航天用高性能结构复合材料最理想的基体材料。
2·结语
近年来,合成的固化型PF性能优异,可应用于航天、航空和电子等行业,但并未实现工业化生产,而且还存在固化不完全、耐热性能差等缺点。在今后的研究中,应该采用添加粒子和加成固化同步进行的方法改进树脂的综合性能,相信PF的应用将会更加广泛。