随着世界能源危机的日益严重,以及公众对于改善生态环境要求的呼声日益高涨,风能作为一种清洁的可再生能源日益受到重视。世界各国在风能开发利用方面投资的持续增长,导致风力发电设备制造业成为许多国家最热门的经济领域,相应的市场规模获得急剧扩大[1]。风力发电叶片作为风电机组的核心部件之一,其好坏直接影响到风力发电机转换风能的效率,因此业内对于叶片材料的性能要求越来越严格。环氧树脂是叶片的重要材料之一,国内叶片厂家长期以来均依靠进口,不仅价格居高不下,叶片制造成本偏高,很大程度上制约了我国风电行业的发展。
普通的环氧树脂黏度大,直接应用于风电叶片层合板制作的话,不仅渗透困难、注射压力高、充模时间长,而且树脂中夹带的气泡不易除尽。目前业界普遍采用的是使用单官能团的环氧稀释剂或者非反应型稀释剂来降低环氧树脂的黏度,但是经过稀释后的环氧树脂力学性能以及热性能明显降低[3-4]。为了保持环氧树脂所固有的优良性能的同时,降低黏度,使其适应风力发电叶片制作工艺的要求,需要研制一种环氧树脂,其低黏度以及优良的力学性能,可以满足风电叶片生产工艺的要求。
1 实验部分
1·1 材料
A组分:E51型环氧树脂,岳化生产; B组分:1,4-丁二醇二缩水甘油醚,安徽恒远化工有限公司生产;C组分:胺类固化剂,自制,胺值498。
1·2 方法
环氧树脂浇铸体制备:按照比例配置好的环氧树脂体系搅拌均匀后室温脱泡,浇入模具中,待稳定后升温至预定温度固化8h,然后自然冷却脱模,供性能测试使用。
1·3 仪器以及测试方法
弯曲、冲击性能采用GB/T 2570-1995在GOPOINT-TS2000S万能实验机测试;黏度在SNB-1数字旋转黏度计上依据GB 10247-88测试。
2 结果与讨论
2.1 树脂与固化剂配比对体系拉伸性能的影响
以B∶A为20∶100为例,探讨固化剂的用量对于浇铸体拉伸性能以及断裂伸长率的影响,由表1可知,固化剂含量由23%增加到25%时,浇铸体样条的拉伸强度达到最高值63·9MPa,拉伸模量也达到最大值2880MPa;含量达到28%时,拉伸强度、拉伸模量反而下降。其原因可能是固化剂含量少,会使得浇铸体系反应速度变慢,在同样的固化速度下固化不完全,仍有未反应的原料在室温下缓慢反应,从而影响其力学性能;而固化剂过多,使得固化反应速度过快,分子链未得到充分舒展便已经发生反应成为交联网状结构,降低了浇铸体的韧性。考虑到固化剂的用量不仅仅影响力学性能,而且也会决定树脂体系的适用期,因此获得较佳综合性能的固化剂含量应为25%。
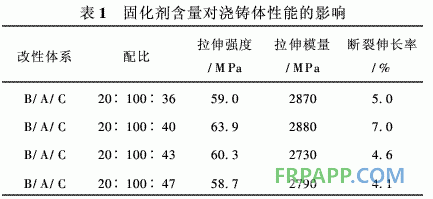
2.2 活性稀释剂的用量对体系拉伸性能的影响
随着稀释剂用量的增加,环氧树脂体系中环氧基团的含量也在同步增加,所需固化剂的量随之增大,以便在不同稀释剂用量下仍能使环氧体系性能达到最优。将优化过的固化剂与1,4-丁二醇二缩水甘油醚、CYD128按照比例混合后,真空脱泡并于80℃下固化8h,对其拉伸性能进行考察,可以看出,增加1,4-丁二醇二缩水甘油醚的量,体系拉伸性能随之提高;当活性稀释剂与环氧树脂比例达到20∶100时,拉伸强度与断裂伸长率达到最高。(见图1)其原因可能在于适量加入这种带有反应基团的稀释剂,降低了体系黏度,可以使得树脂与固化剂分子之间充分接触,有利于分子链运动形成链状或者三维网状结构,一定程度上改善了环氧树脂的韧性;但是稀释剂含量过多,也会使得体系交联密度降低,导致拉伸强度反而有所下降。
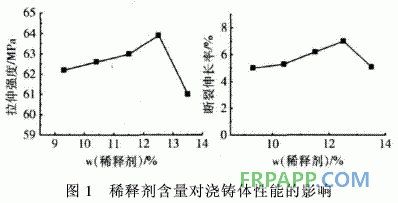
2.3 活性稀释剂的用量对体系黏度的影响
双酚A型环氧树脂25℃时的黏度在8000mPa·s以上,如此高黏度的树脂直接用于风力发电叶片的制作,不仅体系流动速度慢,而且树脂体系对复合材料的浸润能力太低,容易产生气泡,因此需要加入适量的活性稀释剂来降低体系的黏度。
如表2所示,纯环氧树脂固化体系的黏度为419mPa·s,按照20∶100比例加入稀释剂,则固化体系的黏度可以降低至171mPa·s,考虑到需要尽量保持环氧树脂体系的力学性能,确定稀释剂与环氧树脂的配比为20∶100。
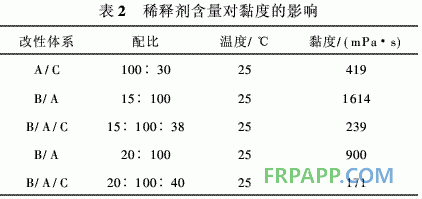
3 结论
研究了双酚A型环氧树脂体系,所使用的1,4-丁二醇二缩水甘油醚是一种稀释效果良好、对产物力学性能影响较小的性能优异的活性稀释剂,当这种稀释剂与E51型环氧树脂CYD128及固化剂的配比为20∶100∶40时,性能达到最佳拉伸强度为63·9MPa,拉伸模量为2880MPa,断裂伸长率为7·0%,25℃时体系黏度为171mPa·s,可望用于风电叶片的制作。