1 概 述
环氧树脂基复合材料因具有比强度高、比模量大、结构整体性好、可设计性强、耐疲劳性好、可修复性强及安全性好等优点而应用于航空产品结构件上,但其缺陷是脆性大、韧性差和抗冲击损伤容限低等。随着复合材料广泛地应用,特别是应用于航空产品上,提高复合材料的韧性一直是国内外复合材料领域所关注的问题。目前普遍采用冲击后压缩强度CAI值来表征复合材料的韧性。一般认为冲击能为6. 7J/m2时, CAI值在193MPa以下为低韧性复合材料; 193~255MPa为韧性复合材料;大于255MPa为高韧性复合材料1。为提高复合材料韧性,国内外研究人员进行了大量的工作。
由洪都航空工业集团自行研制的NY9200G环氧树脂体系制成的先进树脂基复合材料自1996年通过中国航空工业总公司鉴定以来,已用于某飞机结构件上,并投入批生产,取得了明显的技术和经济效益。实践证明:该树脂体系是一种工艺性好、技术成熟、性能优良及价格便宜的环氧树脂复合材料基体。但随着新型号对复合材料韧性要求的不断提高,与韧性复合材料相比,其冲击后压缩强度CAI值相对韧性复合材料CAI值193~255MPa有一定的差距。为进一步提高环氧树脂基复合材料的韧性,以NY9200G/T300环氧树脂体系为基础,开展提高环氧树脂基复合材料韧性的研究是完全必要的。
在环氧树脂基复合材料增韧方面,国内外的研究方向主要集中在以下三个方面:
1)在树脂基体中加入增韧剂,主要是加入液体橡胶。此项工作自六十年代以来一直在进行,取得了一定的进展。但液体橡胶在提高复合材料韧性的同时,也降低了其它物理机械性能。
2)在树脂体系中加入扩链剂,使环氧树脂分子首先为线形增长,然后再聚合,得到更大的聚合物,以提高复合材料的韧性。
3)从工艺上提高树脂基复合材料的韧性。如采用“离位”增韧技术提高复合材料的韧性。针对上述三种增韧方法,经过分析,我们确定采用第三种方法,即从工艺上提高树脂基复合材料的韧性,结合正在某飞机结构件上使用的NY9200G/T300环氧树脂体系,采用“离位”增韧技术提高NY9200G/T300复合材料的韧性。所谓“离位”,从复合原理上讲,就是将复相增韧技术中的增韧相从基体中分离,让它单独与增强相复合,在不改变原有热固性预浸料所有工艺优点并保持其面内力学性能的同时,大幅度提高了复合材料的冲击损伤阻抗,并兼顾了低制备成本2。其形成的双连续的3-3结构作为高效的增韧微结构,大大提高了层间剪切强度、GⅠC、GⅡC和抗冲击损伤性能,从而达到增韧效果。该增韧方法既不改变其原体系中的固化反应历程又不改变固化物的化学结构,是一种在工艺过程中加入增韧物的物理增韧方法。在研究过程中,采用“离位”增韧技术对NY9200G/T300环氧树脂体系复合材料进行增韧,通过常规力学性能试验、韧性性能试验、螺接挤压强度试验和加筋板研制及其冲击后疲劳静强度试验,将其与未增韧的NY9200G/T300环氧树脂体系复合材料性能进行比较,考核“离位”增韧技术的增韧效果,从而得出结论。同时,摸索“离位”增韧技术成型工艺,考核验证其结构件功能,以期大幅度提高该复合材料冲击后压缩强度CAI值。
本研究完成后已实现下列主要技术目标:
1)在基本保持NY9200G/T300复合材料力学性能和工艺性能的同时,“离位”技术增韧的NY9200GES/T300复合材料冲击后压缩强度CAI值平均达到260MPa。
2)采用“离位”增韧技术,不仅不会降低NY9200G/T300复合材料的螺接挤压强度,而且还使其略有提高。
3)按典型铺层研制的加筋板,采用“离位”增韧技术,冲击后疲劳静强度高于同时制备的同种未增韧加筋板。
2 试验部分
2. 1 NY9200GES/T300“离位”增韧预浸料的制备
采用“离位”增韧技术,对NY9200G/T300环氧树脂体系进行增韧,得到NY9200GES/T300“离位”增韧预浸料。
2. 2 NY9200GES /T300“离位”增韧预浸料的固化工艺参数NY9200GES/T300“离位”增韧预浸料的固化工艺参数同NY9200G/T300环氧树脂体系,即:先升温至130±5℃,保温30~35min后,再加外压≥0. 5Mpa,然后升温至175~180℃,保温2~2. 5h。
2. 3 “离位”增韧复合材料的韧性性能和常规力学性能试验
NY9200GES/T300增韧复合材料韧性性能和常规力学性能的测试均按目前先进复合材料行业通行采用的国标或相应的标准进行,具体标准见表1和表2。所需试板均在同一热压罐内同一批次固化成型,固化工艺参数同NY9200G/T300环氧树脂体系。NY9200G/T300环氧树脂复合材料的韧性性能和常温常规力学性能以公开发行的中国航空材料手册第6卷(复合材料)中的数据为准,以此为基础作为试验的空白样,两者测试标准一致。(NY9200GES/T300增韧复合材料韧性性能和常规力学性能的测试由北京航空材料研究院完成。)
2. 4 复合材料螺接挤压强度试验
选定的螺接挤压强度试样为φ6单钉双剪和φ5双钉单剪(包括沉头和平头)两种,试样材料分别为NY9200G/T300和NY9200GES /T300复合材料层压板,铺层顺序均为[±45/(0)2/±45/90/±45/(0)2/90],铺层比例都为40/50/10。(螺接挤压强度试验在中国飞机强度研究所完成。)
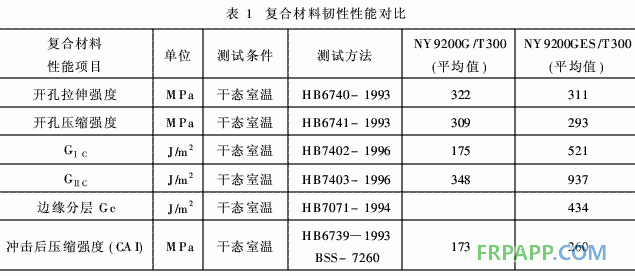
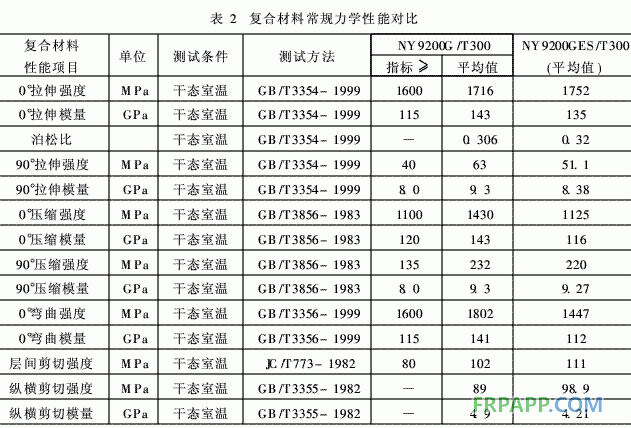
2. 5 加筋板的研制及其性能试验
为全面考核“离位”技术对NY9200G/T300复合材料增韧的效果,按增韧方法研制1件加筋板,见附图。该加筋板是按某型号飞机垂尾翼盒根部碳纤维铺层、比例缩小的模拟垂尾盒段件,我们对其进行冲击后疲劳静强度试验。同时制备1件未增韧的同种加筋板进行冲击后疲劳静强度试验,并将试验结果进行比较。(加筋板冲击后疲劳静强度试验在中国飞机强度研究所完成。)
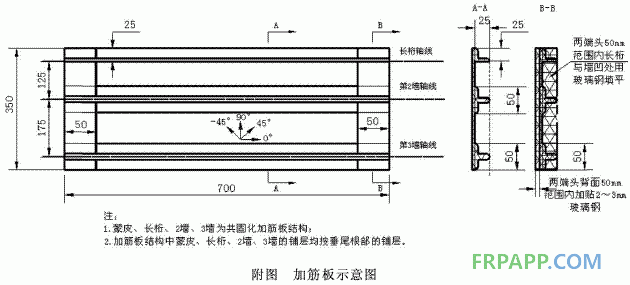
3 结果及讨论
3. 1 NY9200GES/T300增韧复合材料的韧性性能
复合材料的韧性一般采用开孔拉伸强度、开孔压缩强度、冲击后压缩强度、边缘分层层间断裂韧性、Ⅰ型层间断裂韧性和Ⅱ型层间断裂韧性来表征,其中冲击后压缩强度CAI值是目前国际上通行评价韧性高低最常用的性能指标。
以NY9200G/T300复合材料性能数据为空白样作为对比基础,“离位”技术增韧的NY9200GES/T300复合材料韧性性能见表1。
“离位”技术增韧的复合材料开孔拉伸强度及开孔压缩强度与未增韧复合材料相当。而GⅠC,GⅡC性能值则有大幅度提高。
“离位”技术增韧的复合材料冲击后压缩强度CAI值260MPa较未增韧复合材料173MPa有极大地提高,为未增韧复合材料的150. 3%。
3. 2 NY9200GES/T300增韧复合材料的常规力学性能
常规力学性能可以全面反映复合材料的基本性能,是复合材料结构设计的依据。复合材料的常规力学性能主要包括: 0°拉伸强度、0°拉伸模量、泊松比、90°拉伸强度、90°拉伸模量、断裂伸长率、0°压缩强度、0°压缩模量、90°压缩强度、90°压缩模量、层间剪切强度、弯曲强度、弯曲模量、纵横剪切强度和模量等。
“离位”技术增韧的复合材料常规力学性能见表2,此表以NY9200G/T300复合材料性能数据为空白样作为对比基础。
0°拉伸性能试验结果表明:采用“离位”技术增韧的NY9200GES/T300复合材料0°拉伸性能与NY9200G/T300复合材料基本相当,并且高于其指标值。
90°拉伸性能主要反映复合材料的树脂基体内聚强度和树脂与纤维间的界面粘接强度。从表2数据可以看出:“离位”技术增韧的NY9200GES/T300复合材料90°拉伸强度和模量均高于NY9200G/T300复合材料指标值。
0°压缩性能试验结果表明:“离位”技术增韧的NY9200GES /T300复合材料的0°压缩强度和模量与NY9200G/T300复合材料指标值相当。
90°压缩性能试验结果表明:“离位”技术增韧的NY9200GES/T300复合材料的90°压缩强度和模量均与NY9200G/T300复合材料相当,并且远高于其指标值。
0°弯曲性能在表观上显示:“离位”增韧复合材料的弯曲强度及模量均有一定程度的下降。实际上,正常断口情况下弯曲性能主要由纤维控制,当纤维体积含量较低时,弯曲强度和模量均有不同程度下降。考虑到“离位”增韧复合材料试样纤维体积含量较低,可以认为:当“离位”增韧复合材料与未增韧复合材料的纤维体积含量相当时,两者弯曲性能应基本相当。
层间剪切强度是反映树脂基复合材料基体内聚强度及其与纤维之间粘接强度的一个重要指标,层间剪切强度的高低直接影响到树脂基复合材料的承载能力。从表2数据来看:“离位”技术增韧的NY9200GES/T300复合材料层间剪切强度高于NY9200G/T300复合材料,并且远高于其指标值。
纵横剪切性能试验结果表明:“离位”技术增韧的NY9200GES /T300复合材料的纵横剪切性能与NY9200G/T300复合材料相当。
综上所述,我们可以得出:“离位”技术增韧的NY9200GES/T300复合材料基本保持了NY9200G/T300复合材料的常温常规力学性能。
3. 3 复合材料螺接挤压强度
从表3的数据来看,经过“离位”技术增韧的复合材料螺接结构,其挤压强度比未增韧的复合材料略高:对于φ5双钉单剪试件,无论是平头连接形式还是沉头连接形式,“离位”增韧复合材料的极限挤压强度均高于未增韧复合材料,但拐点挤压强度则基本相当。对于平头连接形式,“离位”增韧复合材料的拐点挤压强度和极限挤压强度分别为547MPa和674MPa,而未增韧复合材料则分别为547MPa和606MPa,其极限挤压强度的提高幅度为11. 2%;对于沉头连接形式,“离位”增韧复合材料的拐点挤压强度和极限挤压强度分别为526MPa和664MPa,而未增韧复合材料则分别为518MPa和632MPa,其极限挤压强度的提高幅度为5. 1%。对于φ6单钉双剪试件,“离位”增韧复合材料的拐点挤压强度和极限挤压强度分别为883MPa和1004MPa,而未增韧复合材料的拐点挤压强度和极限挤压强度则分别为855MPa和993MPa,“离位”增韧复合材料的挤压强度比未增韧复合材料略有提高。
实际上,“离位”增韧技术本身并没有提高复合材料螺接挤压强度的任务,该试验的主要目的是为了考核“离位”增韧技术对NY9200G/T300复合材料螺接挤压强度的影响。试验结果表明:“离位”增韧技术不但不会降低NY9200G/T300复合材料螺接挤压强度,而且还使之略有提高。
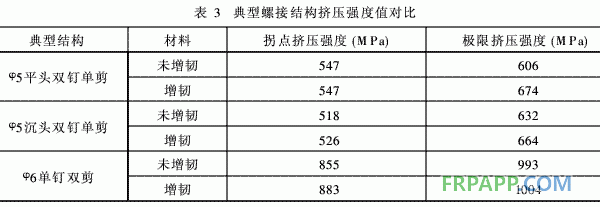
3. 4 加筋板的研制及其性能
3. 4. 1 加筋板的研制
“离位”增韧加筋板的成型步骤为:NY9200GES/T300“离位”增韧预浸料的制备→铺贴蒙皮→预吸胶→铺贴蒙皮→预固化→无损检测→蒙皮与墙及长桁组装→总固化→无损检测→“离位”增韧加筋板。同时制备1件同种未增韧的加筋板,成型步骤同上。2件加筋板经无损检测均符合要求。
3. 4. 2 加筋板的性能
3. 4. 2. 1 “离位”增韧加筋板与未增韧加筋板的损伤阻抗性能
对于相同支持条件下且凹坑深度相近的情况下,“离位”增韧加筋板的损伤阻抗性能高于未增韧加筋板,具体结果如下:
a)在中跨蒙皮产生1. 2mm深凹坑时,增韧加筋板承受的压缩载荷为5. 52kN,而未增韧加筋板所承受的压缩载荷仅为4. 73kN,“离位”增韧后的加筋板承载能力提高了16. 7%,而损伤面积却减小了38. 8%;
b)在筋条凸缘边缘处的蒙皮产生1. 2mm深凹坑时,增韧加筋板承受的压缩载荷为7. 92kN,而未增韧加筋板所承受的压缩载荷仅为5.69kN,“离位”增韧后的加筋板承载能力提高了39.2%。
3. 4. 2. 2 疲劳试验中的损伤扩展状况
疲劳试验前后,“离位”增韧加筋板与未增韧加筋板内部损伤的无损检测结果表明: 2倍疲劳寿命后,损伤都没有发生扩展。
3. 4. 2. 3 “离位”增韧加筋板与未增韧加筋板对压缩强度的影响 从表4可以看到:对于包含中跨蒙皮损伤(相同凹坑深度)的加筋板,增韧加筋板的承载能力大于未增韧加筋板的承载能力,即加筋板B1比A1的初始屈曲载荷和极限承载能力分别提高了37. 5%和25%。
对于包含筋条凸缘处蒙皮损伤的加筋板,即使增韧加筋板的凹坑深度明显大于未增韧加筋板,其承载能力也大于未增韧加筋板的承载能力,即加筋板B2比A2的初始屈曲载荷和极限承载能力分别提高了7. 2%和18. 6%。
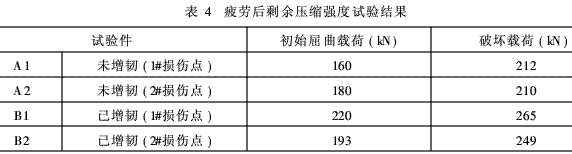
考虑到增韧加筋板与未增韧加筋板几何尺寸的差异:增韧加筋板的蒙皮及L型筋条腹板的厚度均大于未增韧加筋板(蒙皮厚度增加了25. 9%,筋条腹板厚度增加了48. 2% ),在试件几何尺寸存在较大差异的情况下,虽然已增韧加筋板表现出较高的承载能力,但不能由此判断增韧对结构承载能力的影响程度。然而,加筋板的破坏应变(包括屈曲应变和极限应变)却是一个与结构厚度无关的无量纲参数,同时也是结构设计时应考虑的重要指标。因此,应该以破坏应变来考核复合材料的增韧效果,表5给出了增韧与未增韧加筋板破坏时蒙皮的应变值。
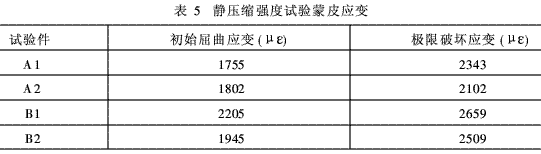
试验结果表明:
a)对于包含中跨蒙皮损伤(相同凹坑深度)的加筋板,增韧加筋板的破坏应变大于未增韧加筋板,即加筋板B1比A1的初始屈曲应变和极限应变分别提高了25. 6%和13. 5%。
b)对于包含筋条凸缘处蒙皮损伤的加筋板,即使增韧加筋板的凹坑深度明显大于未增韧加筋板,其承载能力也大于未增韧加筋板的承载能力,即加筋板B2比A2的初始屈曲载荷和极限承载能力分别提高了7. 9%和19. 4%。
综上所述,可以得出:“离位”增韧加筋板的损伤阻抗高于未增韧加筋板;对于增韧与未增韧加筋板,损伤在2倍疲劳寿命期间均未扩展;“离位”增韧提高了加筋板的承载能力(破坏应变)。
4 结 论
1)“离位”技术增韧的NY9200GES/T300复合材料在基本不降低NY9200G/T300复合材料常温常规力学性能的同时,能显著提高原体系复合材料的抗冲击损伤能力、大幅度提高冲击后压缩强度CAI值,增韧效果显著。
2)经过“离位”技术增韧,NY9200G/T300复合材料螺接结构的挤压强度没有降低,而且还略有提高。
3)“离位”技术增韧加筋板的损伤阻抗高于未增韧加筋板;对于增韧和未增韧加筋板,损伤在2倍疲劳寿命期间均未扩展;“离位”增韧技术提高了加筋板的承载能力(破坏应变)。