1 ·引言
高压玻璃钢管道固化成型工艺自传统固化工艺改进而来,目前已经在玻璃钢管道生产中得到了广泛应用[1]。与传统固化工艺相比,该工艺由于采用内部加热方式,因此更加适合于高压管道的制造[2,3]。玻璃钢管道主要靠纤维承压,采用树脂充当粘合剂,因此对于高压壳体的生产,要严格控制树脂的含量[4]。如图1 所示,根据树脂的黏度特性,控制树脂含量即为控制管道固化过程中内部温度[5],根据本文所选用树脂的黏度特性,期望的温度范围为70 ~ 90℃。
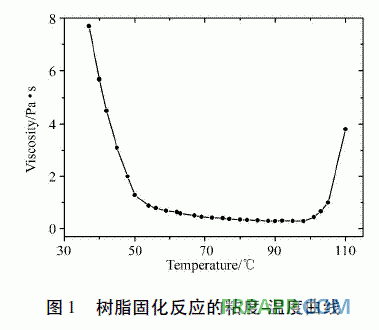
影响正在缠绕的玻璃钢管道外表面温度的因素众多,其中芯模的加温历程对其影响最大。本文利用有限元软件ANSYS 和APDL 语言开发了数值模拟程序,对采用传统恒温加热的热芯缠绕工艺缠绕过程( 以下简称缠绕过程) 进行了数值模拟,分析了外表面温度受加温历程影响规律,继而优化缠绕过程的加温历程使复合材料外表面温度在期望的范围内。
2· 数值模拟
以缠绕20 层、厚度为6. 6mm、纤维体积含量为60%的DN65 高压玻璃钢管道为例,按照60s /层的缠绕速率进行缠绕。对该固化成型工艺进行数值模拟仿真及分析。材料的热学性质和固化动力学参数分别如表1、表2 所示。
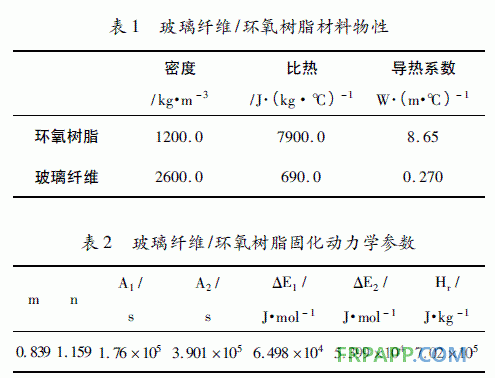
玻璃钢管道含胶量的控制实质上就是缠绕过程中外表面温度的控制,而缠绕过程的加温历程是影响外表面温度的重要因素。因此本文根据传统的恒温加热对缠绕过程进行数值模拟,分析了缠绕过程中温度、放热反应强度的分布和外表面温度的变化规律。传统的恒温加热在缠绕第1 层时芯模以65℃ /min 的升温速率从室温35℃升高到100℃,在缠绕接下来的19 层时芯模温度恒定在100℃,仿真所得第1 层、2 层、5 层、7 层、10 层、15 层和20 层外表面中心节点的温度随时间变化曲线如图2 所示。
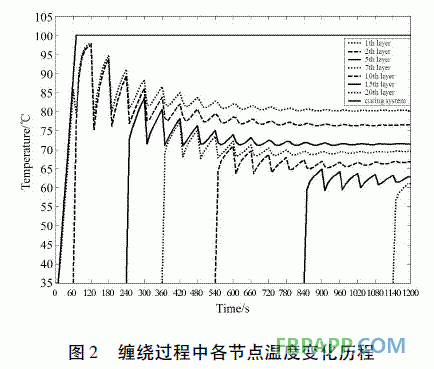
3 ·缠绕过程加温历程的优化
为了清楚地分析缠绕过程中管道外表面温度变化规律,本文将缠绕下一层时,壳体前一层外表面中心节点的温度( 以下简称缠绕过程中管道的外表面温度) 列为表3。
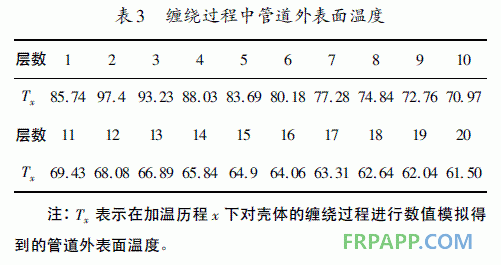
由表3 可见,第2、3 层外表面的温度超出了工艺要求的最高温度90℃。随着缠绕的继续,外表面的温度逐渐降低,第11 层外表面温度已经低于工艺要求的最低温度70℃,此时外表面的黏度增大,不利于树脂更好地浸渍纤维,也不利于多余树脂的排出。由此可见,实际生产中所使用的缠绕过程中的加温历程是不合理的。基于上述问题,本文通过优化缠绕过程的加温历程( 分为a、b、c 三个阶段) 来控制管道的外表面温度,使其始终维持在工艺要求的温度范围内。优化后和优化前的温度对比如图3 所示,由图可见优化后的温度始终控制在期望的范围内。
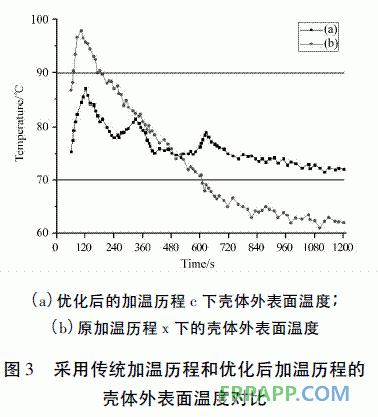
4 ·结论
本文利用有限元软件ANSYS 和APDL 语言开发了数值模拟程序,对高压玻璃钢管道的固化成型过程进行了数值模拟,分析了缠绕过程中管道外表面温度的变化规律,对采用传统恒温加热的缠绕过程进行了优化,保证了在缠绕过程中管道外表面温度始终在工艺要求的范围内,从而提高高压玻璃钢管道的耐压能力。