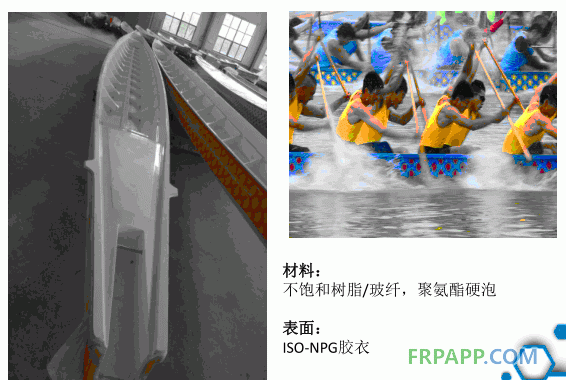
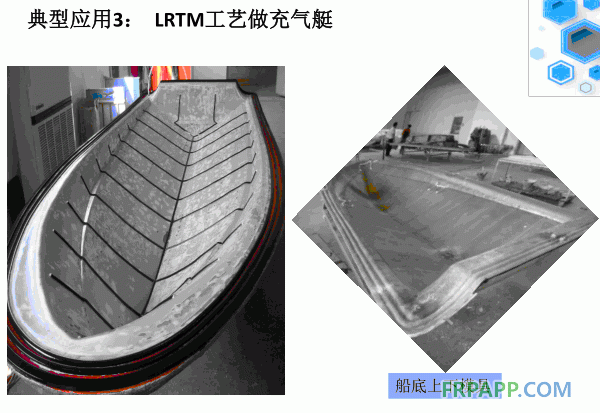
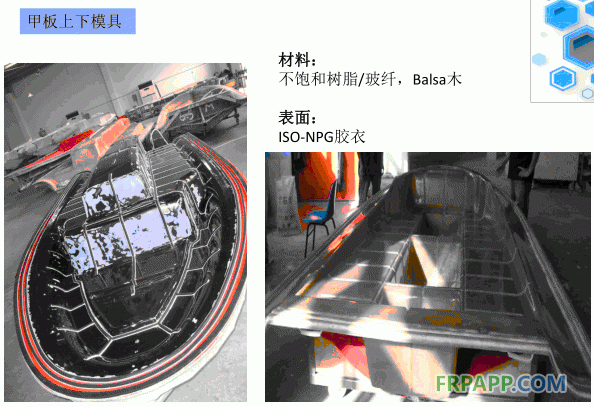
四、常见问题探讨FAQ
Q1. 我们从手糊工艺转到真空导入工艺,铺层需要什么变化?怎么变?
建议是咨询专业的设计公司。铺层既要满足工艺施工,又要达到结构强度、
刚性要求,同时兼顾成本。
在船舶行业,有多家可以提供复合材料结构设计的单位。通过有限元分析
和模拟软件,可以少走很多弯路。同时他们对于材料参数与性能也比较了
解,可以给出最优化的方案。
大致的变化有:
传统手糊的单板结构,会从毡布结合铺层转变成为轴向织物铺层,减少纤
维的强度损失并且提高树脂导入的工艺性。
主龙骨往往会使用泡沫,跟船壳整体真空导入成型。
单板加筋的船体结构将被三明治结构所取代,便于整体成型。
Q2. 如何选择一种合适的工艺来做一条船?
跟材料和结构有关系。比如预浸料/蜂窝结构只能用湿法真空工艺。
(以5M 玻璃钢快艇为例)
具体还要看项目情况,不同工艺都有一些优缺点。哪方面的要求是最主要的,才是决定因素。
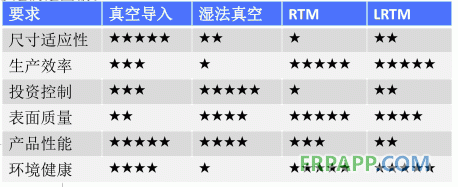
Q3. 真空导入做的船壳脱模出来,产品胶衣表面布纹印和芯材印明显怎么办?
一方面可能是树脂和固化剂的问题,收缩率太大,反应太快,放热高。主要是不饱和树脂这方面的问题多,需要联系树脂厂家或者固化剂厂家,找到更合适的原料。另一方面可以通过手糊过渡层、喷涂屏障胶衣来减少印痕。还可以通过调整真空导入铺层结构和芯材,使用特殊强芯毡TF放在第一层,± 45°轴向织物放在0/90°织物之前,还有让芯材厂家调整开槽打孔的方式和孔径、槽宽等。最后如果是模具耐热冲击差或者还在熟化过程中,模具表面已经形成了印痕了的话,需要处理模具表面。
Q4. 为什么眼睁睁看着树脂真空导入过程非常完美,固化前没一点瑕疵。但船体固化脱模完后,内表面存在一些颜色发花、纤维发白的问题?
为什么眼睁睁看着树脂真空导入过程非常完美,固化前没一点瑕疵。但船体固化脱模完后,内表面存在一些颜色发花、纤维发白的问题?
一种原因是局部缺胶引起发白,虽然树脂浸润透了,但是提前停掉了树脂,最终固化过程中抽气管路抽走了不少铺层里的树脂。树脂含胶量太低,露出纤维发白发花颜色。另一种是真空关早了,铺层间出现了纤维回弹分层的问题,导致层间局部发白。
还有喷胶用多了,导入过程中看不到,脱模后可以看到喷胶的白雾、白斑。最后,可能为了好撕,在移除脱模布和导流网的时候树脂固化度不完全,损伤到表层的玻纤,使之脱层发白。
Q5. 真空导入做船,树脂导流管压得内舱有很明显的压痕,影响内装。如何避免?
真空导入做船,树脂导流管压得内舱有很明显的压痕,影响内装。如何避免?建议使用欧米茄管,或者导流带ENKA CHANNEL。还有一种土办法就是用导流网包裹住导流管,留出一些导流网的重叠距离,抽真空的时候,用真空袋膜把导流网中的导流管“提”起来。
Q6. LRTM 工艺做船为什么经常容易超重?
由于LRTM工艺的上模是半刚性模,当铺层材料铺放不到位时,上模无法在1个大气压力下,完全帖服,往往影响到上下模的合模间隙,使得多出来的间隙厚度中充满树脂,从而超重。同时随着橡胶密封圈的老化,也会影响到上下模合模间隙,从而超重。
五、闭模造船发展畅想
1、 向更多船型的发展,替代木质、钢制结构渔船。
日本的渔船技术遥遥领先,特别是远洋渔船。中国渔船改革能够带动复合材料船舶行业发展,需要使用闭模工艺后来居上。减轻船重,减少油料消耗,与冷藏保温用的泡沫一体成型三明治结构。
军船。
越来越多的结构部件及配件会使用闭模工艺制作,同时整船使用闭模工艺制作,替代钢材也非常有必要。发挥轻质高强、隐身性能以及高透波率的性能。国外的大型扫雷艇,大型登陆气垫船已经技术成熟。
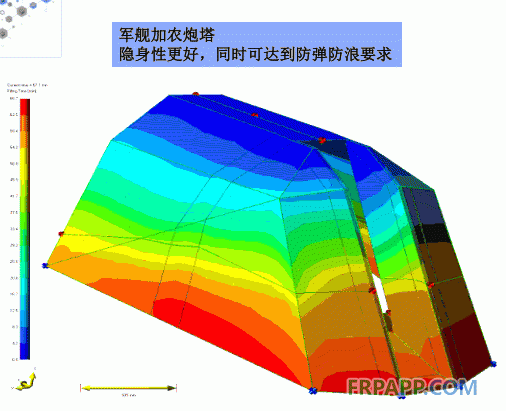
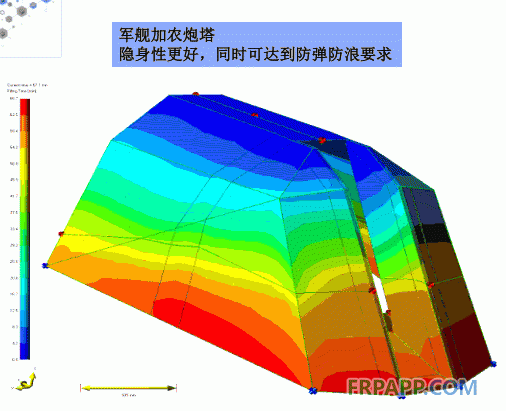
2模块化应用
使用闭模成型的模块化零件,来做加法,减少资源的浪费。例如,澳大利亚ATLCOMPOSITE公司的DUFLEX板材提供了一种思路,在一些特殊的项目上,有比较好的应用效果。同时模块化的零件以后应该可以提高材料的可塑性、易加工性。通过特殊材料的半固化状态性能、或者热变形性能,使得闭模成型的模块化零件有希望可以在3D打印出来的模胚上直接成型。
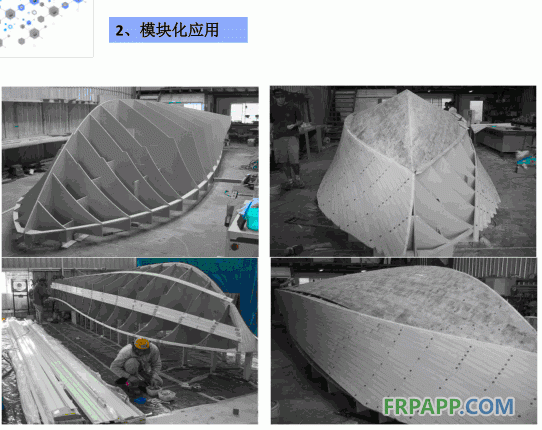
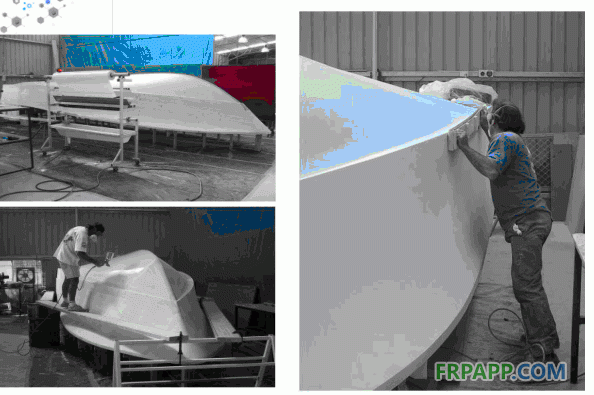
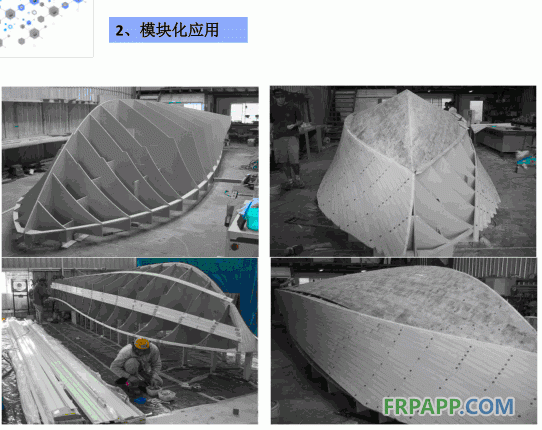
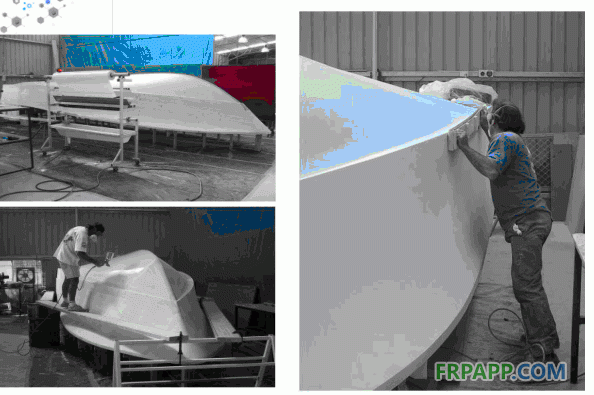