RTM是在模腔中铺放设计好的增强材料预成型体,在压力或真空或两者共同的作用下将低粘度的树脂注入模腔,树脂在流动充模的过程中完成对增强材料预成型体的浸润,并固化成型而得到复合材料构件的工艺方法,是一种先进复合材料低成本制备技术,广受瞩目。日本强化塑料协会将RTM工艺和拉挤工艺一起,推荐为两大最有发展前途的工艺,欧美很多公司投入巨资用于研究开发RTM工艺,其中仅欧共体投资的“开发RTM工艺技术和应用”项目就耗资290万欧元,美国设置了专科学校,用于培训RTM专业人才。
二、 RTM工艺衍化
RTM工艺在发展的过程中,从传统RTM的衍化出多种型式的RTM工艺,如轻质RTM、硅胶模RTM、冷压、多嵌入面模RTM、及真空灌注工艺等。
我们可以根据实际的需要来选择合适的工艺,如果制造大型的产品时,如游艇,大型叶片,高铁车头、及飞机上的大型部件等我们可以采用真空灌注工艺,因为该工艺的树脂含量很低,能获很好的力学性能,相对于手糊,能节省一半的作业时间,另外还可以在纤维中加放夹芯材,并且可制作一次成型极厚的制品,如叶片的叶根,一次灌注130多层的产品大约有30公分厚度。
小型的制品则更合适用传统的RTM工艺和其它的RTM衍化工艺,因为做小型产品时,耗材的的成本会提高产品的制造成本;而体型中等的产品则适合用轻质RTM或硅胶模工艺,在真空吸附的状态下,模具不用承载很大的压力,上半模可以做得很轻,因为这时用传统的RTM模具来制作这些产品时,模具要有很大的刚性来防止注射时产生的压力,而传统的RTM工艺则因为模具的耐用性适合做一些中小型而批量大的产品,对产品表面质量不太高的而批量特别的大的适合用冷压工艺,(如我在马来亚见一家小厂,用该工艺制作产品时,可达十几分钟一个水箱板,一个十几个人的小厂,一天能生产160多片水箱板,)而多多嵌入面模RTM 工艺则把工艺中最费时的的铺毡工艺和胶衣喷涂工艺放在主模的嵌入面模上进行,主模承担的只是灌注和加热固化的部份,因此能极大的提高生产的效率,因些也适合大批量的产品制作。
1、传统RTM
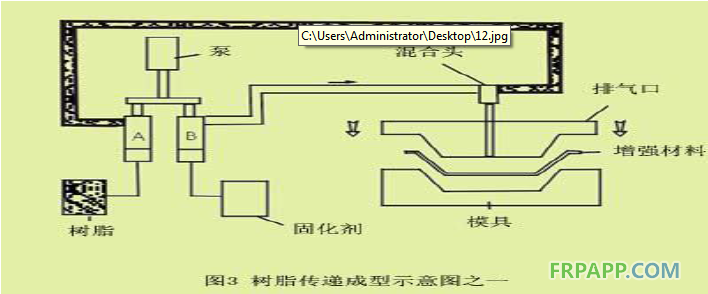
1、传统RTM
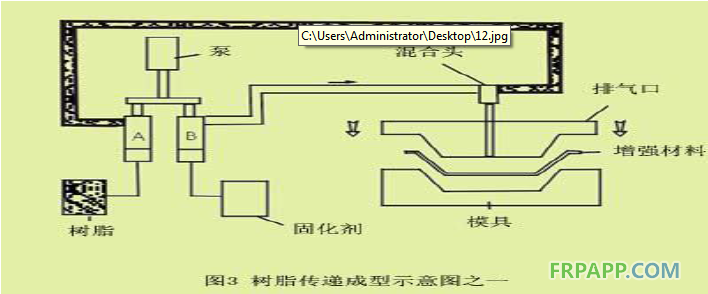
树脂传递模塑成型简称RTM,起始于50、60年代,是手糊成型工艺改进的一种闭模成型技术,可以生产出两面光的制品。
RTM的基本原理是将玻璃纤维增强材料铺放到闭模的模腔内,用专用压力设备将树脂胶液注入模腔,浸透玻纤增强材料,然后固化,脱模成型制品。
RTM成型技术的特点:
1、可以制造两面光的制品;
2、成型效率高,适合于中等规模的玻璃钢产品生产(20000件/年);
3、RTM为闭模操作,不污染环境,不损害工人健康;
4、增强材料可以任意方向铺放,容易实现按制品受力状况例题铺放增强材料;
5、原材料及能源消耗少;
6、建厂投资相对少,项目容易上马。
RTM技术适用范围很广,目前已广泛用于建筑、交通、电讯、卫浴、航空航天等工业领域。已开发的产品有:汽车壳体及部件、娱乐车构件、天线罩、机器罩、浴盆、沐浴间、游泳池板、座椅、水箱、电话亭、小型游艇等。
(RTM模具有制作时,,除了采用低收缩,耐高温树脂及胶衣外,还应采用下列方法来改进模具的质量1\毡布结合的方法,能降低树脂含量2\ 铺布时,采用45度的角度,得到最佳的力学性能, 3\间歇法以此来减少产品的收缩4/ 热处理在80度的温度下进行3到4个小时的热处理,使产品得到充分的固化,让玻璃钢模具在结构造型上不同角度收缩变形的应力得以缓冲释放,能有效减少模具的变形,当然,采用真空导流工艺来制作模具,也是一个值得探讨的方法,在大型风电叶片模具制作时,大多采用该种工艺来进行制作,)
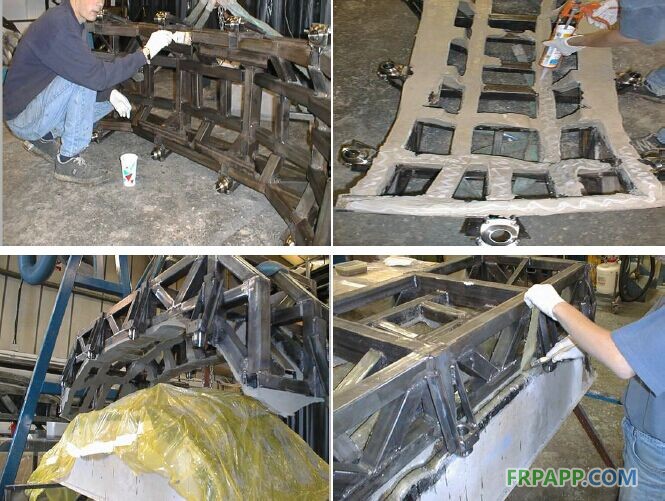
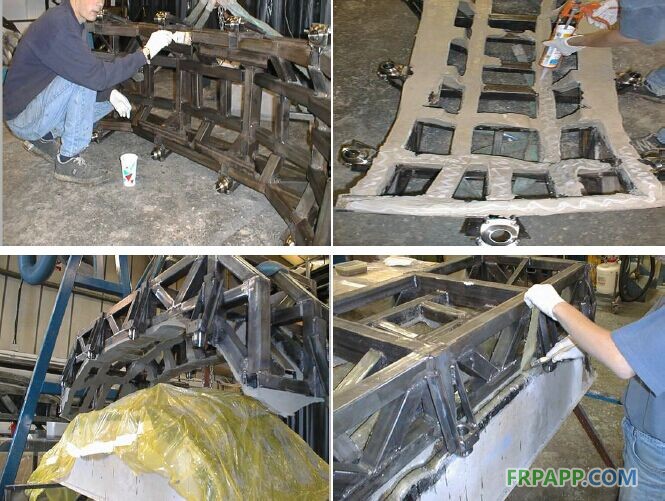
以上的图例是说明RTM模具在制作加强筋时,由于钢骨加和腻子固化的成型体,更能增加同模具帖服性同时,中间采用硅胶过渡层能有效的减少钢骨架的焊接应力,以此来减少模具的变形,同时也能避免钢骨加同玻璃钢模具壳直接接触,在模具表面产生的钢骨架应力痕
RTM成型工艺过程中,注射设备是必须的,要求设备的固化剂的比例可调,一般从0.5% 到3.5%之间不等比例的产品,每分钟流量5-10升左右,注射压力从0.1到8个大气压。可以预设置注射树脂量,带自循环的通过循环泵的简易通道,能够实现简单的设备维护。一般RTM模具模腔内是3-6公斤正压,因此对于模具的刚度有一定要求,如若模具刚度不够的话,不能够保证产品的尺寸精确性也很容易出现爆模意外。RTM工艺用的树脂主要是不饱和聚酯树脂,要求粘度适中。RTM的玻璃纤维含量为45%~55%;常用的增强材料有玻璃纤维连续毡、复合毡、方格布及闭模毡。填料对RTM工艺很重要,它不仅能降低成本,改善性能,而且能在树脂固化放热阶段吸收热量。常用填料有氢氧化铝、玻璃微珠、碳酸钙、云母等。其用量为20%~40%。RTM全部生产过程各工序的操作人员及工具、设备位置固定,模具由小车运送,依次经过每一道工序,实现流水作业。模具在流水线上的循环时间,基本上反映了制品的生产周期,小型制品一般只需十几分钟,大型制品的生产周期可以控制在1小时以内完成。一般RTM工艺的流道设计都从中心注入,从周边排出RTM汽泡产生的原理。
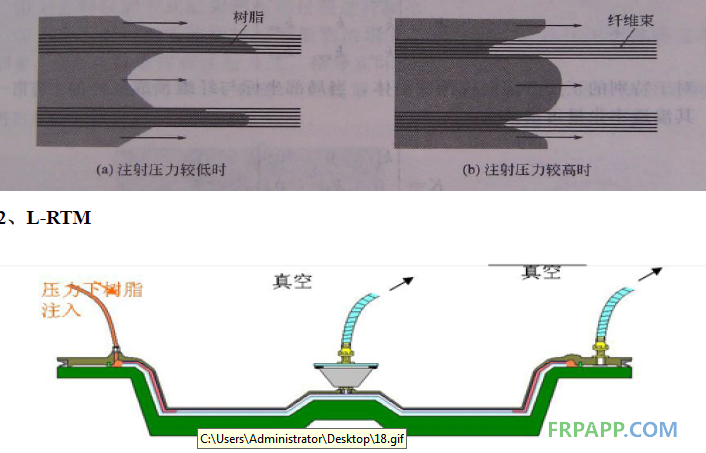
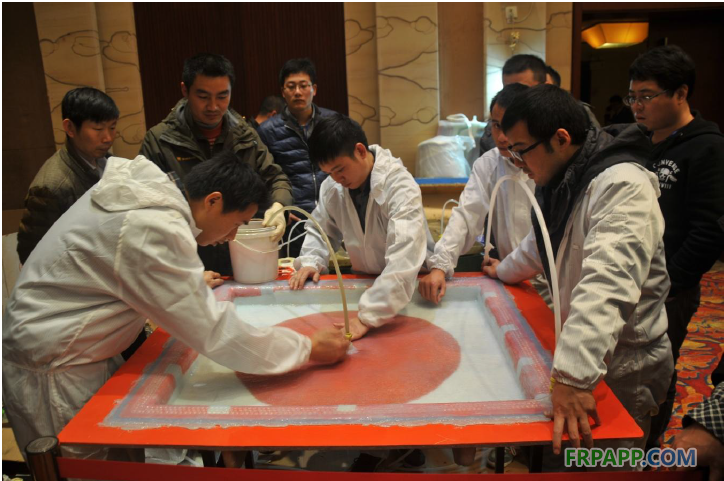
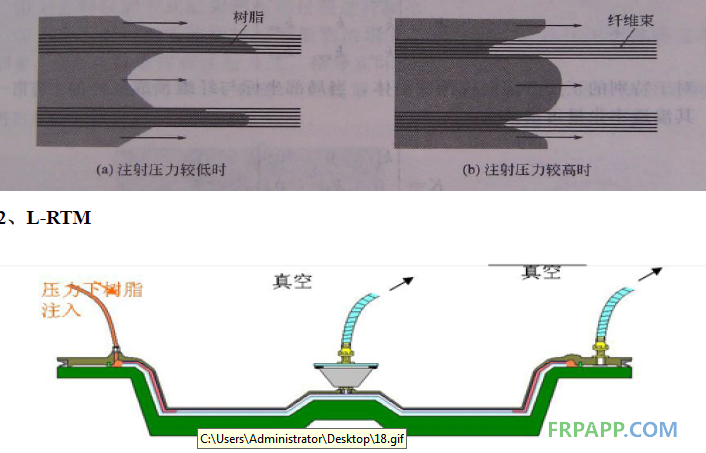
在液体闭模工艺发展过程中,轻质RTM工艺(L-RTM)的开发成功可谓具有里程碑意义,真空辅助成型L-RTM技术是一种新型的低成本的复合材料大型制件的成型技术,它主要原理为首先在模腔中铺放好按性能和结构要求设计好的增强材料预成型体,采用注射设备将专用低粘度注射树脂体系注入闭合模腔,模具具有周边密封和紧固以及注射从排气系统以保证树脂流动顺畅并排出模腔中的全部气体和彻底浸润纤维,是在真空状态下排除纤维增强体中的气体,通过树脂的流动,渗透,实现对纤维及织物的浸渍,并在室温下进行固化,形成一定的树脂及纤维比例的工艺方法。其技术路线上与传统RTM的不同之处,在于有一半模具是半刚性的,模具的厚度可以做到很薄。
L-RTM工艺的特点:
1、可以制造两面光的制品;
2、成型效率高,适合于中等规模的玻璃钢产品生产(3000件/年);
3、L-RTM为闭模操作,不污染环境,不损害工人健康;
4、增强材料可以任意方向铺放,容易实现按制品受力状况例题铺放增强材料;
5、原材料及能源消耗少。
对于尺寸、大面积的复合材料制件,L-RTM是一种十分有效的成型方法,采用以往的复合材料成型工艺,大型模具的选材困难,而且成本昂贵,制造十分困难,尤其是对于大厚度的船舶、汽车、飞机等结构件。L-RTM工艺制造的复合材料制件具有成本低、空隙率含量小、成型过程中产生的VOC挥发气体少、环境污染小(有机挥发份小于50ppm,是唯一符合国际环保要求的复合材料成型工艺)。产品的性能好等优点,并且工艺具有很大的灵活性。被广泛应用于中小型游艇、风电机舱罩、汽车大包围、工程车覆盖件等等领域。
L-RTM成型工艺过程中,除了真空泵是必须的以外,注射设备是可选的,设备要求同RTM所用设备基本一样。如果不采用树脂注射设备也可以达到相同的目的,只是效率上稍有差异。L-RTM模具模腔内是0.2-0.8公斤正压,因此对于产品内表面模具的刚度要求不高,主要是为了体现一个“轻”字。L-RTM用的原材料有基体树脂、增强玻纤材料。L-RTM工艺用的树脂可以是不饱和聚酯树脂,也可以是乙烯基或者环氧树脂,主要要求:
(1) 低粘度,仅借助真空即可在增强剂堆积的高密度预成型体中流动、浸润、浸透。(粘度指标180—300厘泊)
(2) 适用周期长,较长的凝胶时间,较快的固化速度,这样有利于浸透、排气。
(3) 可在室温下固化,树脂工作寿命满足结构要求。
(4) 固化时无需额外压力,只需真空负压。
(5) 具有良好的韧性与高于一般树脂的弹性模量,以及抗腐蚀性。
一般L-RTM的增强材料主要是玻璃纤维,其含量为45%~55%;常用的增强材料也是玻璃纤维连续毡、复合毡及方格布、闭模毡。
3、软模RTM
3、软模RTM
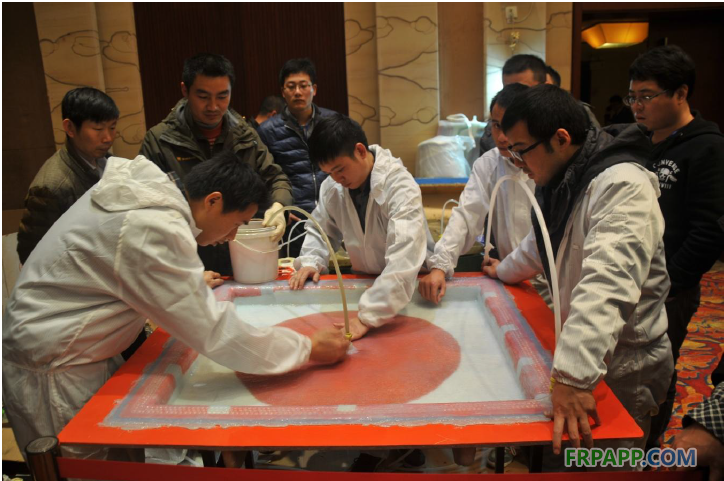
软模RTM工艺兼顾了RTM和真空导流工艺的优点,将RTM的刚性上模改成硅胶或者橡胶的软模,其作用相当于一层真空袋膜,制品处于软模和模具之间,密封周边,抽真空(0.1MPa左右),在抽真空的同时将树脂从模具的另一端由管路导入到模具中,将增强玻纤浸润。固化后脱模。软模RTM成型技术的特点:
1、可以制造两面光的形状结构复杂的制品;
2、成型效率一般,适合于中等规模的玻璃钢产品生产(1000件/年以内);
3、为闭模操作,不污染环境,不损害工人健康;
4、增强材料可以任意方向铺放,容易实现按制品受力状况例题铺放增强材料;
5、软模的使用寿命在10—50次左右,成本介于RTM和真空导流工艺之间目前用于船艇、汽车零部件、工程车覆盖件等等。
4、真空导流工艺(VARIM)
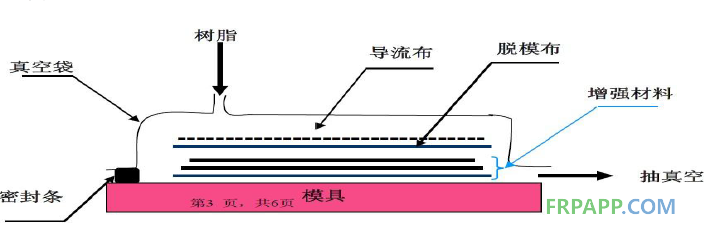
4、真空导流工艺(VARIM)
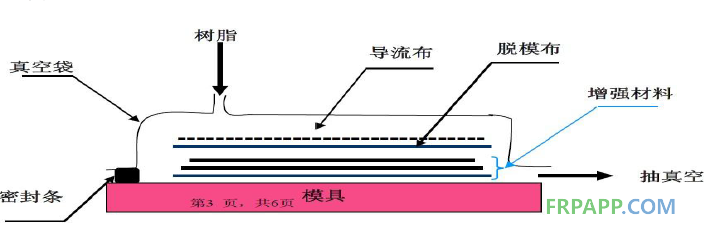
真空导流工艺分为干法和湿法2种。
湿法是将手糊或者喷射成型未固化的制品,加盖一层真空袋膜,制品处于薄膜和模具之间,密封周边,抽真空(0.07MPa),使制品中的气泡和挥发物排除。
干法是将增强玻纤铺放到模具上,将真空袋膜与模具周边密封,在抽真空的同时将树脂从模具的另一端由管路导入到模具中,将增强玻纤浸润。2种工艺的区别在于干法的玻纤含量可以做的更高。
真空导流成型技术的特点:
1、可以制造单面光的制品;
2、成型效率一般,适合于中等规模的玻璃钢产品生产(1000件/年);
3、为闭模操作,不污染环境,不损害工人健康;
4、增强材料可以任意方向铺放,容易实现按制品受力状况例题铺放增强材料;
5、一次性耗材较多、垃圾回收是个问题,成本相对高;目前用于船艇、风能等大型制品;如豪华游艇,风电叶片、机舱罩等等。工艺过程根据制品的形状复杂程度以及面积的大小而有所差异,一般从几分钟到4、5小时不等。
真空导入的四种基本方式为: 中心导入外围导入多边导入线型导入
真空导流成型工艺过程中,不需要注射设备,只需要一台真空泵就可以了;模具只需要单模一般模腔内是负压0.1Mpa ,真空导流工艺所用的原材料有树脂体系、增强材料,不添加填料。该工艺用的树脂主要是要求粘度要低,在180—300厘泊左右。增强材料主要是玻璃纤维,其含量为50%~65%;常用的增强材料有玻璃纤维短切毡、复合毡及方格布等。
5、多嵌入面模RTM (MIT RTM)
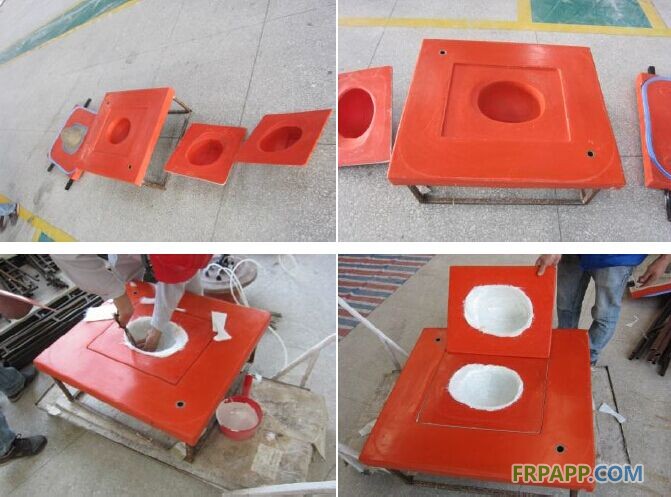
多嵌入面工艺是指在传统的RTM工艺中,原本两个主体模中进行的工序,改变为,在主体模中,制备几个衬模,然后把胶衣喷涂,铺层等工序,在主模外进行,避免了由于以上的工序造成的占模占用时间,这样,有效的提升了产品的成型速度,在使用该工艺时,只有注射和中固化是在主模中进行,所以产品成的型时间就能得到大幅度的提升,单件产品的成型时间大约在10分名钟左右.
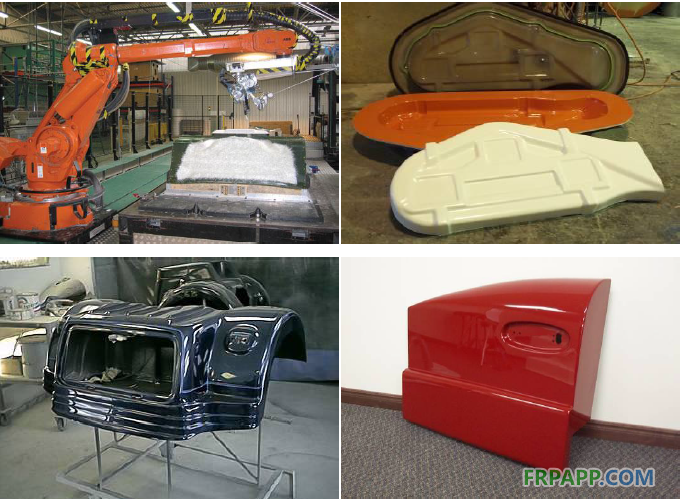
5、多嵌入面模RTM (MIT RTM)
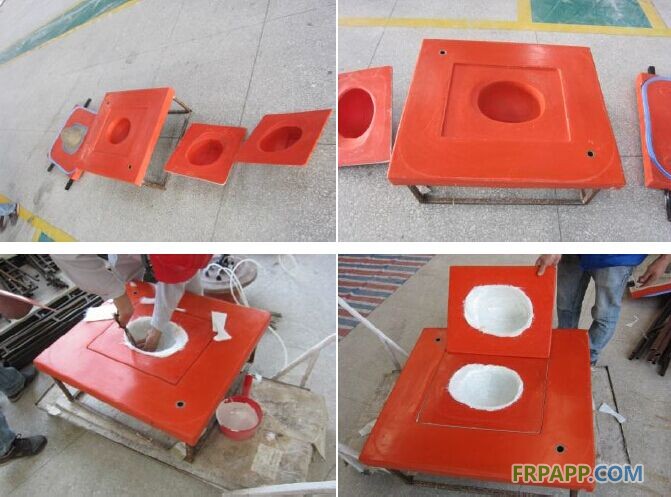
多嵌入面工艺是指在传统的RTM工艺中,原本两个主体模中进行的工序,改变为,在主体模中,制备几个衬模,然后把胶衣喷涂,铺层等工序,在主模外进行,避免了由于以上的工序造成的占模占用时间,这样,有效的提升了产品的成型速度,在使用该工艺时,只有注射和中固化是在主模中进行,所以产品成的型时间就能得到大幅度的提升,单件产品的成型时间大约在10分名钟左右.
冷压成型是指先把纤维或预型体放放模腔内,然后把加入固化剂的树脂倒入维纤上面,然后用压机把模具合模压紧,然后树脂在模腔内流动并充满模腔,然后固化后脱模的一种工艺,该工艺成型的速度快,且质量好,大约10分钟左右,可生产一个产品。
三、 RTM工艺发展的机遇
RTM从上世纪九十年代引入我国以来,由于多种条件的限制,一直未能得到大规模的推广应用,直到近几年,由于风电行业,游艇行业,汽车零配行业的带动,RTM工艺特别是L-RTM得到了迅速的发展,基下以下几个原因,可以预见,该工艺将取代手糊工艺成为主流工艺。
1、用工荒,由于人口红利时代已经结束,加之玻璃钢行业目前还是由主流工艺是由手糊工艺的构成,而该工艺在制作过中环境比较差的特性,使得现在的玻璃钢厂招人成了一大难,即使招到了,人的流动性也很大,工资涨幅也大,因此,过度依于手工工艺成为了玻璃钢行业发展的瓶颈,所以,相对于手糊工艺更容易掌握且环境更能改观的RTM将成为玻璃钢行业发展的首选工艺。(例如,我们在珠海的工厂,以前做日本高铁的隔音墙手糊工艺来做,差不多要20人,后来改用RTM工艺后,只要6人就要能完成相同的工作量,所以制造成本也大幅下降,同时一个合格的手糊工,没有2年以上的实践,很难制作出合格的产品,)
2、越来越严格的环境保护政策的限制,玻璃钢的手糊工艺的特性,显然,也跟不上时代发展的步伐,由于对环境保护和对人的身体健康保护,开模制作的手糊工艺显然是要让位于闭模制作RTM工艺。
3、复合材料市场不断提高的品质要求,由于RTM工艺产品的性能的优越性,也成为风电,游艇,高铁行业,飞机制造、汽车配件主要的制造工艺。
由以上几个原因,我们可以预见,在未来的发展过程中,只要我们不断的推广及加大该工艺制造的应用,RTM工艺一定会迎来发展的高潮期。
四、 RTM工艺提高生产效率的一些思路
RTM工艺要得到大力的发展,除了该工艺本身具有高质量,对环境污染小等特点外,还必须能有比手糊更高的生产效率,这样才能使生产厂家在使用该工艺时,获取更高的利润,这样,就能有效的推动该工艺的快速发展,借鉴国内外一此工厂在使用该工艺时的一些经验,我就如何提高RTM生产效率方面,作一总结。
1、RTM模具增加加热系统,用于玻璃钢工业的大多数树脂都有一与温度直接相在的固化曲线,所以寻找生产模具能够控制温度的方法具有相当的现实意义,这样有助于优化生产效率。事实上模具温度每提高10℃,凝胶时间将减半,因此在环境温度(20℃)下,模塑一个部件也许固化脱模时间需要60分钟,而在50℃,同样的树脂体系,模塑同一部件,在7.5分钟内就能脱模。
2、增强纤维铺放,采用预成型工艺,在RTM工艺中,纤维铺层是在模具内比较占用时间的工序之一,如果事先把铺层要用的纤维放先预制好,在铺放时,直接放入模具内,合模后,注入树脂即可,这样就能大大提高生产效率,
3、多嵌入面模RTM,前面我也介绍过了该工艺,该工艺最明显的优势就是,通过多个廉价的内模,然后把胶衣喷涂及铺层的工艺在这些内模上完成,最后,把完成上述工序的内模放入主模中,然后合模注入树脂即可,该工艺能产品在模具内的成型时间有效的缩短,大大的产品的生产效率。
4、采用气缸或用压机、气袋等设备来进行合模,在传统的RTM工艺中,大部份合模机构才采用螺丝来锁紧合模,这样合模效率低下,最好能采用气缸或用压机、气袋合模平台来进行合模,这样,就能有效的加快产品的成型时间。
5、在进行RTM工艺进行产品生产时,最好采用流水线的思路来进行,明确各岗位的分工,如铺层,注入,脱模及原材料配送中心,这样,使各生产岗位分工时,各工序更单一,所以更能熟悉掌握,在作业时,更能有效的加快产品的制作时间。同时,科学的制定好产品的作业指导书及材料用量表,使员工在生产时,做到有“法”可依,同时加大员工的RTM技能的培训,使员工理论联系实际,更能在实际操作,有效的提升作业的质量和效率;RTM操作工,只要培训得合理,在二到三个月内,即可基本掌握RTM工艺的操作技能,而一个好的手糊操作工,没有一到两年的实际操作,是掌握不好手糊的的技能,这也是RTM工艺的优势之一。
6、采用国外通用的第三代RTM工艺布局
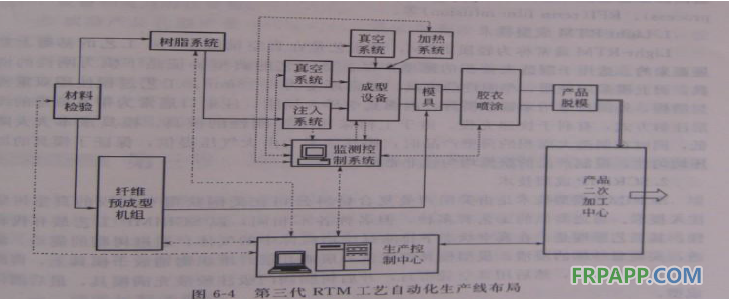
五、RTM工艺应用案例
6、采用国外通用的第三代RTM工艺布局
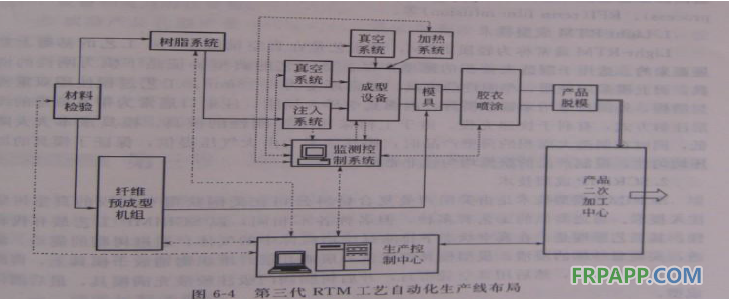
五、RTM工艺应用案例
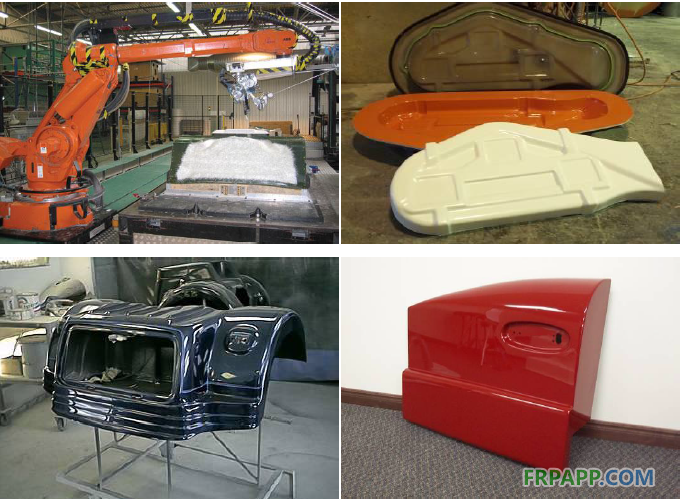
六、总结
RTM工艺以它友善的工作环境,优异的力学性能使得它在未来的中国玻璃钢发展中,逐渐取代手糊等落后的工艺,成为一种主流的玻璃钢生产工艺,但是也应该注意,只有努力改善应用和对相应的员工进行培训,才能真正让这项先进的工艺为之所用。
我们可以利用该工艺的诸多优点来作为基础,多开发一些高附加值的产品,如汽车轻量方面的,新能源方面的,碳纤制品等等,提升公司的产品的竞争力,努力去开拓市场,进而给公司带来新的经济增长点,同时也健康良性带动RTM工艺的发展,