碳纤维复合材料(CFRP)由于具有高强度、高模量、低密度、耐高温、耐腐蚀、耐摩擦、抗疲劳等优异的性能,广泛应用于航空航天、国防军事、汽车飞机构件等领域。以空客A380为例,碳纤维复合材料的用量已经达到32t左右,占机构总量的15%,再加上其他种类的复合材料,估计其总用量可达结构总重的25%左右。钻削加工是碳纤维复合材料最常见的二次加工方式之一,制孔主要用于铆接或者紧固结构件。然而,碳纤维复合材料因其具有各向异性和非均匀性、层间结合强度低、受温度影响大等特点,在钻削制孔过程中极易产生分层、毛刺和撕裂等缺陷,属于典型的难加工材料。
研究表明,在上述几种碳纤维复合材料常见的制孔缺陷中,分层缺陷对复合材料结构件的承载能力和疲劳强度影响最大。本文主要从碳纤维复合材料钻削加工过程中分层缺陷的产生机理、影响因素和检测等方面对国内外目前的研究现状进行综述。
CFRP的机理分析
由于CFRP力学性能的特殊性和内部结构的多样性,在切削过程中,材料的变形过程远比金属材料复杂得多,这不仅与刀具形状及工艺参数等传统因素有关,还受纤维和基体属性以及纤维铺层方向的直接影响。因此,CFRP的切削加工机理与传统的金属切削加工机理有很大区别。
1.CFRP的切削机理
在1983年,Koplev等较早对碳纤维切削过程进行试验研究,指出CFRP切屑主要是由材料的脆性断裂形成的。D.H.Wang等对单向和多向碳纤维复合材料进行正交切削试验,研究了不同的纤维方向对切屑形成机制的影响。由于碳纤维复合材料由脆性的碳纤维和韧性的树脂基体组成,两者强度极限相差很大,前者是后者的若干倍,因此学者张厚江等认为在切削过程中可以将其简化地看成只是对碳纤维的切削,而将对树脂基体的切削忽略。

图1 不同纤维方向角θ下的切削过程
文献对一些典型的纤维铺层方向进行研究,总结碳纤维复合材料在不同的纤维方向角θ下切屑的形成形式(见图1)。
当θ=0°时,切屑的形成是刀具通过不断地将切削层材料与基体材料分离开而实现的。这种切削变形形式称为层间分离型。
当0°<θ≤90°时,以图1中θ=45°和θ=90°为代表,刀具切削刃对碳纤维复合材料的推挤作用在纤维内部形成垂直于纤维自身轴线的剪切应力。当剪切应力超过纤维剪切强度极限时,纤维被切断。切断后的纤维在刀具前刀面的推挤作用下,沿纤维方向产生滑移。当滑移引起的纤维界面间的剪切应力超过基体树脂材料的剪切强度极限时,被切断纤维与其他纤维分离,形成切屑。这种切削变形形式称为纤维切断型。
当90°<θ<180°时,以图1中θ=45°为代表,刀具对前端材料的推挤作用导致复合材料间的层间分离。刀具前端材料在刀具作用下发生弯曲,当弯曲应力超过碳纤维复合材料的弯曲强度极限时,底部发生断裂。刀具继续前进,刀具对其前端材料推挤作用加强,当前端材料底部断裂点处的剪切应力超过材料剪切强度极限时,发生剪切断裂,形成切屑。这种切削变形形式称为弯曲剪切型。
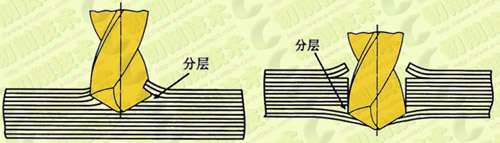
图2 钻削CFRP时孔出入口的分层机制示意图
2.分层产生机理分析
分层是指由层间应力或制造缺陷等引起的复合材料铺层之间的脱胶分离破坏现象。研究表明,钻削碳纤维复合材料过程中的分层缺陷可以分为两种损伤机制:入口剥离分层和出口顶出分层(见图2)。
在钻削过程中,一方面,当钻头横刃开始接触材料而主切削刃未完全切入材料时,切削力会将被切除的材料推入螺旋槽。这些材料在切断之前会沿着螺旋槽表面上升,产生向上的剥离力。剥离力会使上层未切除的区域产生分离,即为剥离分层。另一方面,当钻头的横刃即将钻出材料时,由于材料剩余的未切除的材料层数越来越少,在轴向力超过材料的层间结合强度时,出口周边的铺层之间发生脱粘现象而造成顶出分层缺陷。顶出分层发生在层间区域,因此它不仅取决于纤维的性质,而且和树脂的性质有关。
对于分层的产生机理,张厚江等通过声学显微镜分析指出,CFRP板材钻削孔入口侧和出口侧都有分层,入口侧分层为圆形,出口侧表层分层为椭圆形,深层分层为圆环型;同一孔出口侧的分层远远大于入口侧的分层。
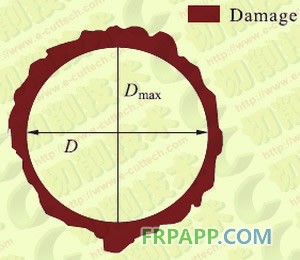
图3 分层因子表征示意图
分层的影响因素
影响钻削分层缺陷的因素有很多,包括切削参数、刀具、材料性质、制造工艺等。这些影响因素之间存在相互耦合的关系,而且在钻削过程中还受到很多不可控因素的影响。目前,国内外学者研究较多的是切削参数与刀具对分层缺陷的影响。研究表明,钻削过程中的轴向力是导致分层缺陷的最主要原因。在钻削加工过程中,当轴向力超过一个阀值时,分层缺陷就会发生。其中,横刃对轴向力的贡献约占60%左右。
1.切削参数影响
切削参数变量主要包括切削速度、进给量f(每齿进给量fz)等因素。切削速度和进给量是钻削加工过程中的两个主要参数变量。研究表明,进给量对分层缺陷的影响大于切削速度。António T.Marques等采用4种不同的钻头研究了其在不同切削参数下的切削加工性能。试验表明,合理选择切削参数可以减小轴向力,进而减小分层缺陷影响。试验研究指出以0.025mm/r的进给速度和53m/min的切削速度切削材料可以使轴向力和分层因子达到最小,分层因子下降大概4%-5%左右。
V.N.Gaitonde等用硬质合金钻头(K20)对碳纤维复合材料进行钻削加工试验研究,结果表明分层趋势随着切削速度的增加而减小,并且采用低进给量和顶角可以减小分层因子。
张厚江等采用YG6X整体硬质合金四面钻头钻削CFRP时,发现进给量对各层间分层的影响呈上凹曲线。在进给量很小时,进给量增大分层尺寸降低;当进给量超过时,进给量增大,各层间分层尺寸上升。因此是产生最小分层的进给量,是一个临界值。
Vijayan Krishnaraj等采用K20硬质合金钻头在不同主轴转速和进给量的情况下研究碳纤维复合材料的切削加工性能。试验表明,入口侧剥离分层因子与进给速率之间并没有明显的规律,但是从总体上看,低进给速率的分层因子小于高进给速率的分层因子。出口侧顶出分层因子随着进给速率和主轴速率的增加而增大。进给速率是出口侧顶出分层因子的主要影响因素。进给速率的贡献率是51.4%,而主轴转速的贡献率是35.42%。试验还给出了最优的进给速率和主轴转速,分别为0.137mm/r和12000r/min。
2.刀具的影响
由于碳纤维复合材料属于典型的难加工材料,并且钻孔加工属于半封闭加工,切削加工过程中产生的大量热不易被切屑和刀具带走。因此,钻削加工容易导致刀具的磨损。刀具的磨损不仅影响制孔质量而且也会影响制孔效率和增加加工成本。刀具的影响因素主要包括刀具几何形状、刀具涂层、刀具参数等。
由于导致分层缺陷的临界轴向力受切削刃的影响,因此刀具几何结构对于减小分层缺陷有着重要的作用。Luís Miguel P.Dur?o等研究了五种刀具:120°顶角麻花钻、85°顶角麻花钻、锯齿钻、匕首钻、阶梯钻。研究表明,120°顶角麻花钻的分层因子最小,阶梯钻的分层因子次之,且与120°顶角麻花钻的分层因子相差不大。分层因子最大的为锯齿钻,达到了1.23左右。因此,根据该试验条件最佳的刀具为120°顶角麻花钻,阶梯钻次之。
对于硬质合金涂层刀具,目前常用的主要有普通涂层(如AlTiN)和金刚石涂层等类型。Xin Wang等对比试验研究了三种不同的刀具:未涂层硬质合金钻头、金刚石涂层硬质合金钻头和AlTiN涂层硬质合金钻头。试验结果表明,金刚石涂层可以显着减少刀具的磨损,然而AlTiN涂层硬质合金钻头由于在钻削过程中出现氧化现象而未能有效降低刀具磨损速率。Redouane Zitoune等用纳米涂层硬质合金钻头对碳纤维和铝合金叠层材料进行钻削加工。他们指出,在钻削CFRP过程中,采用纳米涂层硬质合金钻头可以显着降低粗糙度和轴向力。轴向力的降低可以有效预防钻削过程中的分层缺陷。
3.其他影响因素
影响分层缺陷的因素很多,除了上述广泛研究的切削参数和刀具外还有其他重要的影响因素,比如材料的预浸渍方式、导孔的影响、垫板的影响、新工艺等。Islam Shyha等对比分析了3种类型预浸渍材料(977-2/HTS AC、8552/AS4 AC、MTM44-1/HTS OC)对钻削过程的影响。研究表明在入口侧分层缺陷,预浸渍方式的贡献率为12%;然而,在出口侧分层缺陷,预浸渍方式的贡献率已经高达38.5%。另外,8552/AS4 AC预浸材料的分层因子较大,特别是在高进给速度(0.4mm/r)的情况下,该现象更为明显。C.C.Tsao和H.Hocheng研究了导孔对分层缺陷的影响,其中导孔的直径与套料钻的内径相等。试验结果表明,虽然分层临界轴向力由于导孔而降低,但是钻削过程中的轴向力也由于切屑的去除而大大降低。控制预制导孔直径与钻孔直径的比值,可以在较大进给量情况下钻削加工碳纤维复合材料而不出现分层缺陷。C.C.Tsao和H.Hocheng通过在被加工材料底部安装垫板,研究其对分层缺陷的影响。他们首先推导出锯齿钻和套料钻带垫板钻削的分层临界轴向力模型公式,随后进行了试验验证。研究表明,安装垫板可以较未安装垫板获得更好的钻孔质量。
近年来,科研人员在对钻削制孔机理进行大量的研究基础上,试验了一些新的制孔方法和材料处理工艺,并取得了一定的成果。本文以螺旋铣削制孔技术和缝合技术为例。螺旋铣削制孔技术是利用铣削原理进行制孔的新型切削加工方法。在螺旋铣削过程中,通过改变刀具与孔轴线之问的偏心距而得到不同的孔径,因此可以实现同一刀具针对不同孔径的制孔及锪窝加工,从而降低了加工成本,提高了加工效率。王奔等以传统钻削加工为参照,分别利用螺旋铣削及传统钻削两种方法对C/E复合材料进行制孔试验,并对螺旋铣削与传统钻削刀具的运动轨迹进行分析。结果表明,切削温度是影响C/E复合材料制孔质量的重要因素。因为,螺旋铣削制孔时的切削温度较传统钻削时降低69℃以上,降幅大于36%,因此有效避免了制孔出口处的撕裂及分层现象。
缝合技术作为一种复合材料液体成型预制体的有效连接增强的方法,其原理是通过缝合手段,使复合材料在垂直于铺层平面的方向得到增强,从而提高材料层间损伤容限。穿过增强织物厚度方向的缝线可以大大改善复合材料的层间性能。Yosra Turki等试验研究了缝合与未缝合复合材料的钻削加工性能。结果表明,缝合材料在表面质量和缺陷减少方面比未缝合材料有很大的改进。缝合线使层间产生压缩效应并且在钻头的推进过程中,阻碍其分离。因此,缝合技术可以减少由轴向力导致的分层缺陷和基质破裂。K.T.Tan等还研究了缝合密度和缝合线厚度对碳纤维复合材料的破坏形式和失效特性的影响。
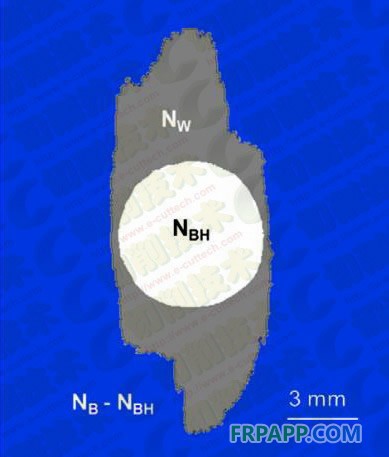
图4 面积法分层因子表征示意图
分层缺陷的检测
为了检测分层缺陷的程度,国内外科研人员研究试验了许多种方法。张厚江等采用氯化金渗透液检测法较早对碳纤维复合材料钻削制孔分层缺陷进行检测。检测试验中发现,分层缺陷的形状主要有近似椭圆形和近似圆形两种,两者的中心都与孔中心重合。随后,他们又采用声学显微镜对碳纤维复合材料钻孔分层缺陷进行检测,根据检测试验结果及分析,总结出了立体分层模型,并对分层形成机理进行了探讨。
为避免对材料产生人为损伤,无损检测技术在分层缺陷检测方面得到了广泛运用。目前采用的无损检测技术主要包括声学显微镜、超声C扫描、X射线电脑断层摄影技术、增强射线照相法等。周正干等基于激光超声技术,对复合材料紧固孔分层进行量化表征试验;基于穿透法和脉冲反射法进行激光超声C扫描检测,得到紧固孔区域分层缺陷的形状、尺寸和位置特征。研究结果表明,利用激光超声技术的非接触式激发、接收和高分辨力特点,可以准确测得紧固孔区域分层缺陷导致的波反射和衰减,有效表征飞机复合材料结构的紧固孔分层缺陷。
C.C.Tsao和H.Hocheng采用X射线电脑断层摄影技术和超声C扫描技术这两种无损检测技术对分层缺陷进行检测。试验结果表明X射线电脑断层摄影技术和超声C扫描技术测得的结果很接近,这两项技术都可以揭示不同刀具分层发生的临界轴向力。然而X射线电脑断层摄影技术对于检测分层缺陷更加灵活和有效。
结语
随着对碳纤维复合材料性能要求越来越高、工作条件越来越苛刻,对碳纤维复合材料制孔质量要求也越来越高。分层作为钻削制孔过程中的主要缺陷之一,国内外学者已经对其产生机理和影响因素进行了深入研究。通过优化合理选择切削参数和采用不同几何形状和涂层的刀具是目前减少分层缺陷的有效途径。通过对国内外对碳纤维复合材料分层缺陷的研究现状进行综述,今后可从以下方面加大对碳纤维复合材料制孔分层缺陷的研究:继续研究新的刀具及优化刀具几何结构参数以提高其切削性能;对复合材料进行深入研究,改善制造工艺,提高材料性能;建立完善、合理的仿真模型,以期达到对分层缺陷更准确的预测。