1、高性能低密度轻量化聚丙烯复合材料研究进展
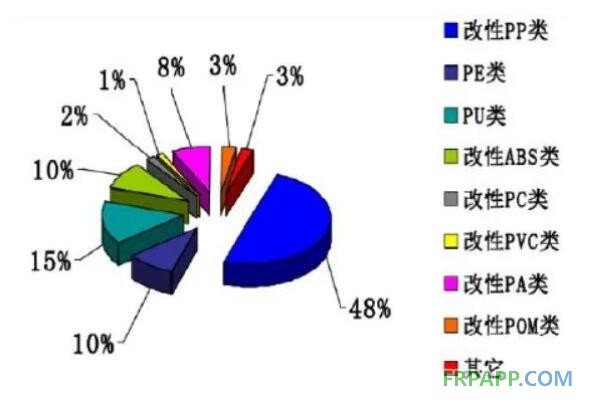
整车非金属材料使用品类较多,PP类材料占比最大,因此做好PP类材料的轻量化工作特别重要。
聚丙烯常用的改性方法为物理改性、化学改性两类。在聚丙烯的改性中,人们通常会添加无机粉体,这些添加的无机粉体由于其密度远高于聚丙烯密度,导致改性聚丙烯材料的密度增加,从而使得塑料制品重量增大。为零件的轻量化计,可通过不添加、少量添加或添加低密度物质,来改善聚丙烯材料这些缺陷,从而满足使用要求。为此,在汽车内外饰上采用低密度聚丙烯材料的设想自2012 年开始兴起,随着整车轻量化的要求和低碳经济的发展,目前低密度聚丙烯在整车上的应用越来越广,采用高性能低密度的聚丙烯复合材料可使相关零件实现一定程度的轻量化,从而提升车辆的能耗节约效果。
近几年,国外相当一部分的车型内外饰零件已在使用低密度型的改性聚丙烯材料。如 basell 为某车型开发的 HCTKC2007N、HC TKC 420N、HX TKS 428P等牌号的材料目前已在大众、通用、奥迪等整车厂的相关车型上使用,这类材料的填充量通常为 1%~12%,密度0.90 g/cm3~0.98g/cm3,可代替 10%~20%滑石粉填充的改性聚丙烯材料在仪表板本体、中央通道、门板、立柱等零件上应用,可使零件密度平均降低 6%~10%并满足零件的使用要求,近几年,国内某些整车厂和材料厂也在研究并验证该方案的可行性。
相关资料显示:低密度聚丙烯材料的开有两种途径:一是合成性能更优异的树脂材料,这方面技术和资源主要掌握在大的石化厂家手里,这里不多加叙述;二是复合改性技术方面的创新,使填充体系更细,或是强度更高,与树脂的结合更好,在体系里形成双网络或三网络结构,使用性能更优异的增强材料或复配使用,先进的表面处理技术或加工技术,以及纤维骨架结构、多层结构等结构上的创新材料的应用以及晶须材料、纤维材料、碳纤维材料的产业化应用等。
2、轻量化聚丙烯复合材料的发泡技术研究
采用合适性能的聚丙烯进行微孔发泡,发泡后的材料具有密度小、比强度高、韧性好、隔热隔音性能佳等优势。目前,发泡聚丙烯广泛应用于汽车及飞机零部件、体育器械、电器、各类家电产品,某种程度上来说,发泡聚丙烯材料国内外研究热度较大。但由于聚丙烯树脂是柔软长链大分子结构,它的分子链结晶度高,柔顺的线性分子链使聚丙烯在温度达到熔融温度后黏度迅速下降,从而使得 PP 的发泡过程难以控制。所以目前可直接独立批量工业化生产微孔发泡聚丙烯的国家相对较少。
发泡剂是使对象物质成孔的物质,其应用源自橡胶工业早期。1846 年Hancock 等人发表了发泡剂专利,他们采用碳酸铵和挥发性液体作为天然橡胶的发泡剂制得了开孔海绵制品。1940 年杜邦公司发明了工业用有机化学发泡剂二偶氮氨基苯,尽管该物质存在一定毒性及污染性,但受限于当时的条件,仍得到了广泛地应用。之后,偶氮二异丁腈作为非污染性发泡剂被大量用于制造 PVC泡沫制品;二亚硝基五次甲基四胺替代碳酸铵和挥发性液体作为橡胶发泡剂;50年代,偶氮二甲酰胺因其无毒、无臭、不污染、不助燃等优点使其成为发泡剂的主力产品;70 年代,日本推出酰肼类发泡剂 4,4’-二磺酰肼,由于该发泡剂本身和分解产物都具有良好的电性能,因此在高频和超高频电线电缆领域受到青睐;近年来,发泡剂的生产工艺不断得以改进,发泡剂种类越来越多并运用于各行各业,相关资料显示,目前全球与发泡剂有关的橡塑发泡制品消耗量已超过1000 万吨,后续仍可能继续增加。选择合适的发泡剂是使聚丙烯材料发泡完美的重要措施。
针对聚丙烯在发泡过程中的气泡逃逸问题,HE.Naguib 等认为可采用以下三种方法进行处理:(1)在体系中引入支化程度或交联程度较高的成分以提升体系熔体强度来避免发泡材料在发泡时出现的泡孔快速合并现象;(2)采用惰性长链发泡剂;(3)优化设备结构,改变模口形态及制作工艺条件以避免材料的快速结晶。体系中引入 HMSPP 是体系发泡获得优质发泡材料的重要方法,HMSPP 具有较高的熔体粘度和熔体强度,可大幅提升 PP 的发泡性能。当然,也可采用PP 部分交联、PP 与其他聚合物共混改性、PP 与无机粒子共混改性来增加体系的熔体粘度及熔体强度。
3、轻量化聚丙烯复合材料的表面性能研究
轻量化聚丙烯复合材料的表面性能,是呈现的表面效果,主要表现有材料的光泽度、耐刮擦性能、表面硬度、外观均匀度方面。零件表面的光泽度,一方面可以通过调整模具的表面来调整,另一方面可以通过材料本身的光泽度来调整,只有结合两者,才能更好地满足要求。在材料方面有研究者做了许多影响材料光泽的研究。
汽车内外饰件的会与物体发生摩擦或微碰撞,在零件表面留下痕迹影响其外观装饰效果,这与材料的耐刮擦性、表面硬度有着直接的关系,可以通过改善材料的耐刮擦性来避免,在轻量化聚丙烯材料的应用有着重要的作用。表面硬度与耐刮擦性能是相关的,提高耐刮擦性能一般是通过二个方面来,一是提高材料的表面硬度,让材料表面的承受力增加,不易产生较深的划痕或不产生划痕,二则是通过增加材料表面的自润滑性,让材料的内部组织不宜产生内聚破坏,发生发白的现象,在视觉上降低外观缺陷。
在材料外观缺陷种,零件表面的光泽差,产生的虎皮纹现象,也是外观性能表现的一种,有研究表面,这种缺陷是由于流动不畅所导致,一般可以通过提高材料的流动性、模温、改善润滑体系等方式解决。
4、轻量化聚丙烯复合材料的散发性能研究
近年来,随着汽车市场的不断的更新迭代发展,人们不仅追求汽车的款式、性能,也更加关注汽车内饰物品对人体所产生的影响。目前,汽车空气质量越来越受到关注,尤其是新车的散发性,进入 21 世纪以来,由车内空气污染严重超标所引发的诉讼案件在我国时有曝光,引起了人们对于车用材料挥发性有机物污染的高度重视。2004 年 7 月 14 日,国家环保总局正式启动车内空气的国家环保标准制定;2008 年 3 月,由国家环保总局牵头制定的的行业标准实施。2009 年底,环境保护部公布了《车内空气挥发性有机物浓度要求》(征求意见稿),该要求规定了车内空气中挥发性有机物的浓度限制,并确定了以乙苯、苯、二甲苯、甲醛、苯乙烯、乙醛、丙烯醛等作为主要控制物质。2011 年我国颁布了《GB/T27630-2011 乘用车内空气质量评价指南》,规定了车内空气中苯、二甲苯、乙苯、丙烯醛、苯乙烯、甲醛、乙醛的浓度限值标准。2017 年 1 月 1 日,国家汽车内饰件气味新规开始实施,汽车内装饰有机物挥发引起的污染问题引起了世界汽车制造业厂商们的高度的关注。
挥发性有机物,常用 VOCs 表示,VOCs(volatile organic compounds)指的是指在常温状态下容易挥发的有机化合物,常见的是五苯(苯、乙苯、甲苯、苯乙烯、二甲苯);三醛(甲醛、丙烯醛、乙醛),是表征室内污染程度的一个重要指标。这些气体对人身体健康的危害不容小觑,当车中的 VOCs 到达一定浓度时候,短时间内人们会感觉到恶心、头痛、头晕等,严重时候会出现抽搐症状,并且会伤害到人体的肾脏、肝脏、神经系统和大脑,长期处在这种有害气体超标准的环境中还会导致血液、肌体皮肤及免疫等系统的损害。其中的甲醛已经被世界卫生组织确定为可致癌的物质,对免疫系统、神经系统、肝脏均有毒害,而短时间吸入过量苯物质会导致急性中毒,对人体造成的伤害不可逆。
塑料制品产生气味和 VOC 的主要原因是聚合物受到光照、氧气、高温、潮湿等条件影响,助剂或挤出过程中降解的小分子发生迁移。汽车散发 VOC 及气味的来源主要是汽车的车顶毡、仪表板塑料零件、座椅、地毯和其它装饰时候使用胶水等。所以应尽量采用环保级别高的添加剂与助剂,从原料上入手控制有害物质的产生,改善生产工艺,提高检测力度,提高安全意识,有效地控制汽车环境质量,保证消费者的安全。探索和使用散发性能较低的环保材料,将是未来前景以及相关主机厂和零部件企业的应对之道。
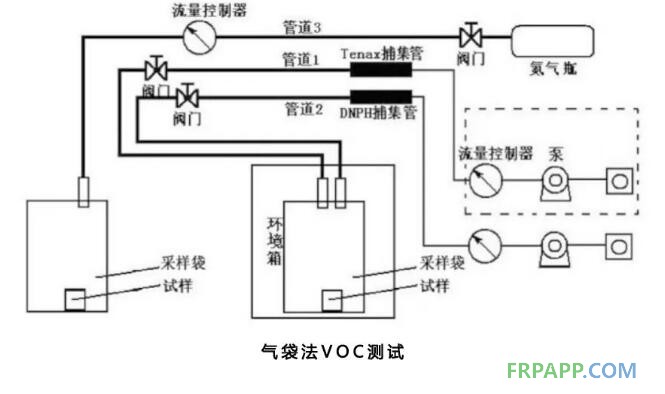
国内各主机厂对 VOC 的要求和测试方法不尽相同。国内整车厂(长安、吉利、长城)主要采用气袋法(TD-GC/MS)进行气味、VOC 测试。气袋法流程如下图所示。采用气袋法收集气体,用 TENAX 管收集、TD-GCMS 分析烃类物质,用 DNPH 管收集、HPLC 分析醛类物质;而大众、通用等欧美车系主要采用顶空进样法,借鉴 VDA277 方法进行测试,总之各大主机厂均有属于自己的标准。